Information injection-pump assembly
ZEXEL
106671-6270
1066716270
ISUZU
1156032151
1156032151
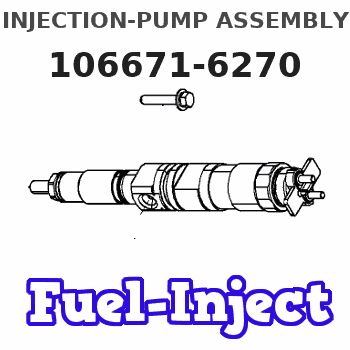
Rating:
Service parts 106671-6270 INJECTION-PUMP ASSEMBLY:
1.
_
7.
COUPLING PLATE
8.
_
9.
_
11.
Nozzle and Holder
1-15300-332-0
12.
Open Pre:MPa(Kqf/cm2)
17.7{180}/22.1{225}
15.
NOZZLE SET
Include in #1:
106671-6270
as INJECTION-PUMP ASSEMBLY
Cross reference number
ZEXEL
106671-6270
1066716270
ISUZU
1156032151
1156032151
Zexel num
Bosch num
Firm num
Name
Calibration Data:
Adjustment conditions
Test oil
1404 Test oil ISO4113 or {SAEJ967d}
1404 Test oil ISO4113 or {SAEJ967d}
Test oil temperature
degC
40
40
45
Nozzle and nozzle holder
105780-8140
Bosch type code
EF8511/9A
Nozzle
105780-0000
Bosch type code
DN12SD12T
Nozzle holder
105780-2080
Bosch type code
EF8511/9
Opening pressure
MPa
17.2
Opening pressure
kgf/cm2
175
Injection pipe
Outer diameter - inner diameter - length (mm) mm 8-3-600
Outer diameter - inner diameter - length (mm) mm 8-3-600
Overflow valve
131424-8620
Overflow valve opening pressure
kPa
206
172
240
Overflow valve opening pressure
kgf/cm2
2.1
1.75
2.45
Tester oil delivery pressure
kPa
157
157
157
Tester oil delivery pressure
kgf/cm2
1.6
1.6
1.6
Direction of rotation (viewed from drive side)
Left L
Left L
Injection timing adjustment
Direction of rotation (viewed from drive side)
Left L
Left L
Injection order
1-5-3-6-
2-4
Pre-stroke
mm
4.5
4.47
4.53
Beginning of injection position
Governor side NO.1
Governor side NO.1
Difference between angles 1
Cal 1-5 deg. 60 59.75 60.25
Cal 1-5 deg. 60 59.75 60.25
Difference between angles 2
Cal 1-3 deg. 120 119.75 120.25
Cal 1-3 deg. 120 119.75 120.25
Difference between angles 3
Cal 1-6 deg. 180 179.75 180.25
Cal 1-6 deg. 180 179.75 180.25
Difference between angles 4
Cyl.1-2 deg. 240 239.75 240.25
Cyl.1-2 deg. 240 239.75 240.25
Difference between angles 5
Cal 1-4 deg. 300 299.75 300.25
Cal 1-4 deg. 300 299.75 300.25
Injection quantity adjustment
Adjusting point
-
Rack position
11.3
Pump speed
r/min
700
700
700
Average injection quantity
mm3/st.
149
147
151
Max. variation between cylinders
%
0
-3
3
Basic
*
Fixing the rack
*
Standard for adjustment of the maximum variation between cylinders
*
Injection quantity adjustment_02
Adjusting point
H
Rack position
6.4+-0.5
Pump speed
r/min
290
290
290
Average injection quantity
mm3/st.
10
6.8
13.2
Max. variation between cylinders
%
0
-13
13
Fixing the rack
*
Standard for adjustment of the maximum variation between cylinders
*
Injection quantity adjustment_03
Adjusting point
A
Rack position
R1(11.3)
Pump speed
r/min
700
700
700
Average injection quantity
mm3/st.
149
147
151
Basic
*
Fixing the lever
*
Boost pressure
kPa
60
60
Boost pressure
mmHg
450
450
Injection quantity adjustment_04
Adjusting point
B
Rack position
R1+0.65
Pump speed
r/min
1100
1100
1100
Average injection quantity
mm3/st.
161
155
167
Fixing the lever
*
Boost pressure
kPa
60
60
Boost pressure
mmHg
450
450
Injection quantity adjustment_05
Adjusting point
E
Rack position
R1+0.2
Pump speed
r/min
800
800
800
Average injection quantity
mm3/st.
149
143
155
Fixing the lever
*
Boost pressure
kPa
60
60
Boost pressure
mmHg
450
450
Boost compensator adjustment
Pump speed
r/min
500
500
500
Rack position
R2-1.75
Boost pressure
kPa
4
4
6.7
Boost pressure
mmHg
30
30
50
Boost compensator adjustment_02
Pump speed
r/min
500
500
500
Rack position
R2(R1-0.
45)
Boost pressure
kPa
46.7
46.7
46.7
Boost pressure
mmHg
350
350
350
Timer adjustment
Pump speed
r/min
850--
Advance angle
deg.
0
0
0
Remarks
Start
Start
Timer adjustment_02
Pump speed
r/min
800
Advance angle
deg.
0.5
Timer adjustment_03
Pump speed
r/min
875
Advance angle
deg.
1.5
1
2
Remarks
Finish
Finish
Test data Ex:
Governor adjustment
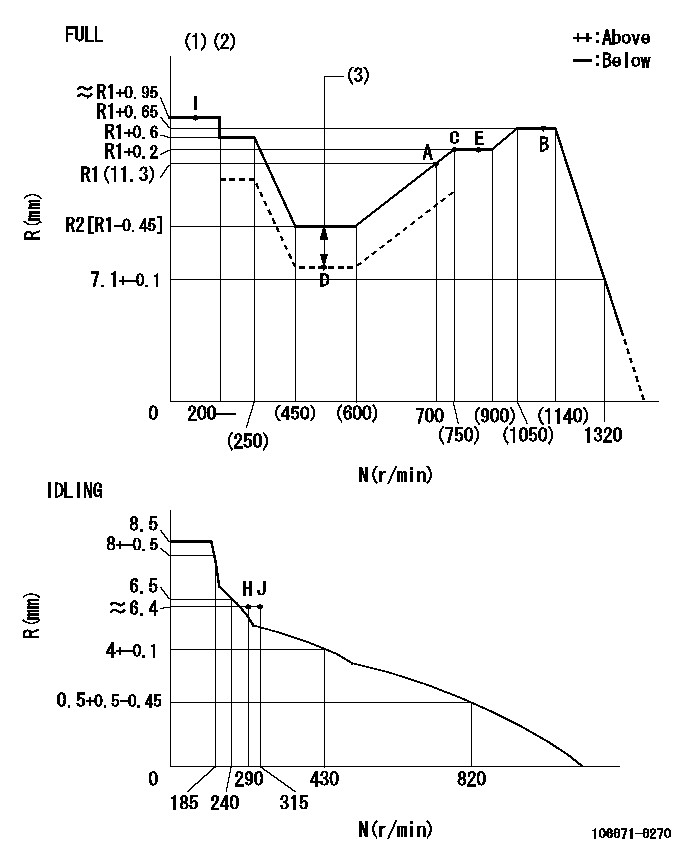
N:Pump speed
R:Rack position (mm)
(1)Torque cam stamping: T1
(2)Tolerance for racks not indicated: +-0.05mm.
(3)Boost compensator stroke: BCL
----------
T1=AE45 BCL=1.75+-0.1mm
----------
----------
T1=AE45 BCL=1.75+-0.1mm
----------
Speed control lever angle
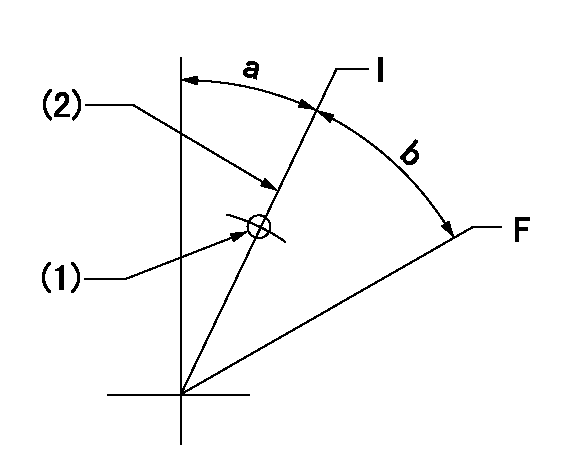
F:Full speed
I:Idle
(1)Use the pin at R = aa
(2)Stopper bolt set position 'H'
----------
aa=35mm
----------
a=27deg+-5deg b=32.5deg+-3deg
----------
aa=35mm
----------
a=27deg+-5deg b=32.5deg+-3deg
Stop lever angle
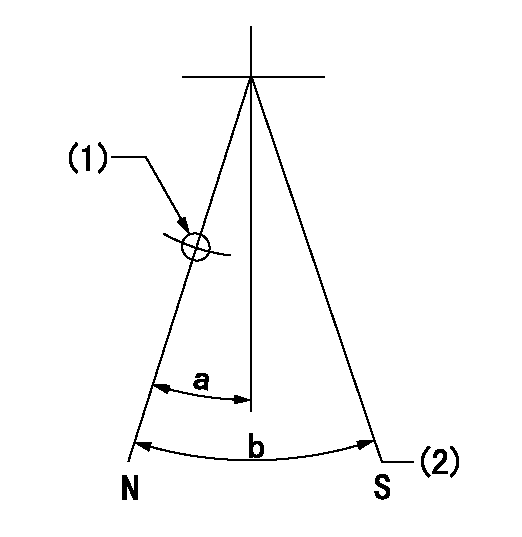
N:Pump normal
S:Stop the pump.
(1)Use the pin at R = aa
(2)Set the stopper bolt so that speed = bb and rack position = cc. (Confirm non-injection.)
----------
aa=40mm bb=0r/min cc=1.5+-0.3mm
----------
a=22deg+-5deg b=41deg+-5deg
----------
aa=40mm bb=0r/min cc=1.5+-0.3mm
----------
a=22deg+-5deg b=41deg+-5deg
0000001501 ACS

(A) Set screw
(B) Push rod 1
(C) Push rod 2
(D) Lever
1. Aneroid compensator unit adjustment
(1)Screw in (A) to obtain L1.
(2)Select C so that dimension L2 can be obtained.
2. Adjustment when mounting the governor.
(1)Set the speed of the pump to N1 r/min and fix the control lever at the full set position.
(2)Set to full boost.
(3)Screw in the aneroid compensator body to obtain the performance shown in the graph above.
(4)As there is hysterisis, measure when the absolute pressure drops.
(5)Hysterisis must not exceed rack position = h1.
----------
N1=800r/min L1=1.5+-0.5mm L2=37.5+-0.5mm h1=0.15mm
----------
Ra=R3(R1+0.2)mm Rb=(R3-0.4)mm Rc=R3-0.75mm P1=(89.8)+-2.7kPa((674)+-20mmHg) P2=79.4+-2.7kPa(596+-20mmHg) P3=70.1+-0.7kPa(526+-5mmHg) Q1=(149)+-3cm3/1000st Q2=(138.5)cm3/1000st Q3=(129)+-3cm3/1000st
----------
N1=800r/min L1=1.5+-0.5mm L2=37.5+-0.5mm h1=0.15mm
----------
Ra=R3(R1+0.2)mm Rb=(R3-0.4)mm Rc=R3-0.75mm P1=(89.8)+-2.7kPa((674)+-20mmHg) P2=79.4+-2.7kPa(596+-20mmHg) P3=70.1+-0.7kPa(526+-5mmHg) Q1=(149)+-3cm3/1000st Q2=(138.5)cm3/1000st Q3=(129)+-3cm3/1000st
Timing setting
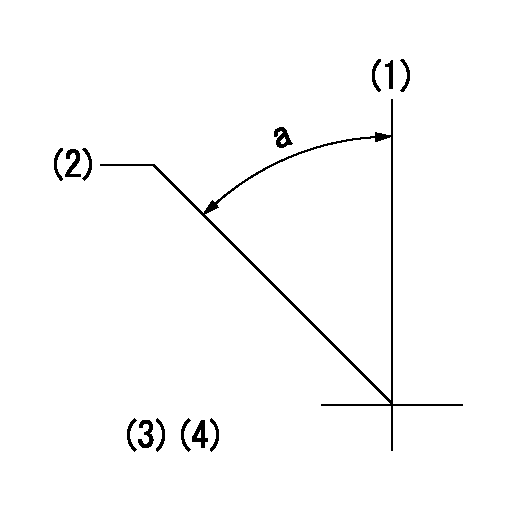
(1)Pump vertical direction
(2)Position of timer's threaded hole at No 1 cylinder's beginning of injection
(3)B.T.D.C.: aa
(4)-
----------
aa=10deg
----------
a=(50deg)
----------
aa=10deg
----------
a=(50deg)
Information:
CONFIDENTIAL
TECHNICAL INFORMATION BULLETIN March 27, 2002
Engines 3516 (25Z, 5SJ, 7KM, CMD, 4XF)
3516B (1HZ, 7RN, 5AN, FDN, BDP,
6HN)
Component Code: 1404SUBJECT: Generator Stator Adapter Cracking on 3516 Diesel Generator Set
PROBLEM:
Certain SR4B single bearing generators may develop cracks in the adapter assembly. The generator adapter is the welded assembly, part of the generator stator, consisting of the front adapter ring that bolts to the flywheel housing and the individual support bars welded to this adapter ring. Several different weld failure modes exist for the generator adapter. First, there may be cracks along the top weld leg between the adapter supports and the front adapter ring. Second, there may be cracks at the toe of the welds joining the adapter support bars to the front ring. These cracks appear in the heat-affected zone of the welds and propagate into the front adapter ring of the generator. The third failure mode is radial cracks between the end ring of the generator adapter and the stator housing. This type of crack most likely occurs after the support welds have failed. After the support welds have failed, the cracks at the toe of the support bars propagate into the ring and create a stress riser.
SOLUTION:
Caterpillar is redesigning the current product and is also working on a solution that will address the existing units in the field. At this time, it is NOT recommended to immediately replace cracked generator stators, nor is it recommended to re-weld the cracked adapters as a field repair. Rather, a crack observation and evaluation process should be established for each individual case. It is anticipated that the first recognizable cracks on suspect generators (cracks size of 0.25" and larger) may appear as early as 300 hours. If any of the above-described cracks are found, the servicing dealer should contact Caterpillar Service. The servicing dealer should also assist in periodic inspection of the cracks in an effort to determine the next action.
Contact (if different from sender): Miro Halicek (770) 233-5877 or Marc Sylvester (770) 233-5630.
COPYRIGHT 2002 CATERPILLAR
ALL RIGHTS RESERVED
TECHNICAL INFORMATION BULLETIN March 27, 2002
Engines 3516 (25Z, 5SJ, 7KM, CMD, 4XF)
3516B (1HZ, 7RN, 5AN, FDN, BDP,
6HN)
Component Code: 1404SUBJECT: Generator Stator Adapter Cracking on 3516 Diesel Generator Set
PROBLEM:
Certain SR4B single bearing generators may develop cracks in the adapter assembly. The generator adapter is the welded assembly, part of the generator stator, consisting of the front adapter ring that bolts to the flywheel housing and the individual support bars welded to this adapter ring. Several different weld failure modes exist for the generator adapter. First, there may be cracks along the top weld leg between the adapter supports and the front adapter ring. Second, there may be cracks at the toe of the welds joining the adapter support bars to the front ring. These cracks appear in the heat-affected zone of the welds and propagate into the front adapter ring of the generator. The third failure mode is radial cracks between the end ring of the generator adapter and the stator housing. This type of crack most likely occurs after the support welds have failed. After the support welds have failed, the cracks at the toe of the support bars propagate into the ring and create a stress riser.
SOLUTION:
Caterpillar is redesigning the current product and is also working on a solution that will address the existing units in the field. At this time, it is NOT recommended to immediately replace cracked generator stators, nor is it recommended to re-weld the cracked adapters as a field repair. Rather, a crack observation and evaluation process should be established for each individual case. It is anticipated that the first recognizable cracks on suspect generators (cracks size of 0.25" and larger) may appear as early as 300 hours. If any of the above-described cracks are found, the servicing dealer should contact Caterpillar Service. The servicing dealer should also assist in periodic inspection of the cracks in an effort to determine the next action.
Contact (if different from sender): Miro Halicek (770) 233-5877 or Marc Sylvester (770) 233-5630.
COPYRIGHT 2002 CATERPILLAR
ALL RIGHTS RESERVED