Information injection-pump assembly
ZEXEL
106671-6070
1066716070
ISUZU
1156029751
1156029751
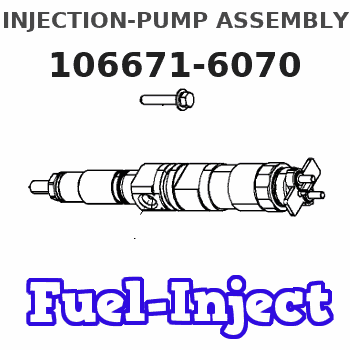
Rating:
Service parts 106671-6070 INJECTION-PUMP ASSEMBLY:
1.
_
7.
COUPLING PLATE
8.
_
9.
_
11.
Nozzle and Holder
1-15300-289-2
12.
Open Pre:MPa(Kqf/cm2)
19.6{200}
15.
NOZZLE SET
Include in #1:
106671-6070
as INJECTION-PUMP ASSEMBLY
Cross reference number
ZEXEL
106671-6070
1066716070
ISUZU
1156029751
1156029751
Zexel num
Bosch num
Firm num
Name
Calibration Data:
Adjustment conditions
Test oil
1404 Test oil ISO4113 or {SAEJ967d}
1404 Test oil ISO4113 or {SAEJ967d}
Test oil temperature
degC
40
40
45
Nozzle and nozzle holder
105780-8140
Bosch type code
EF8511/9A
Nozzle
105780-0000
Bosch type code
DN12SD12T
Nozzle holder
105780-2080
Bosch type code
EF8511/9
Opening pressure
MPa
17.2
Opening pressure
kgf/cm2
175
Injection pipe
Outer diameter - inner diameter - length (mm) mm 8-3-600
Outer diameter - inner diameter - length (mm) mm 8-3-600
Overflow valve
134424-1920
Overflow valve opening pressure
kPa
127
107
147
Overflow valve opening pressure
kgf/cm2
1.3
1.1
1.5
Tester oil delivery pressure
kPa
157
157
157
Tester oil delivery pressure
kgf/cm2
1.6
1.6
1.6
Direction of rotation (viewed from drive side)
Left L
Left L
Injection timing adjustment
Direction of rotation (viewed from drive side)
Left L
Left L
Injection order
1-5-3-6-
2-4
Pre-stroke
mm
3.7
3.67
3.73
Beginning of injection position
Governor side NO.1
Governor side NO.1
Difference between angles 1
Cal 1-5 deg. 60 59.75 60.25
Cal 1-5 deg. 60 59.75 60.25
Difference between angles 2
Cal 1-3 deg. 120 119.75 120.25
Cal 1-3 deg. 120 119.75 120.25
Difference between angles 3
Cal 1-6 deg. 180 179.75 180.25
Cal 1-6 deg. 180 179.75 180.25
Difference between angles 4
Cyl.1-2 deg. 240 239.75 240.25
Cyl.1-2 deg. 240 239.75 240.25
Difference between angles 5
Cal 1-4 deg. 300 299.75 300.25
Cal 1-4 deg. 300 299.75 300.25
Injection quantity adjustment
Adjusting point
A
Rack position
11.3
Pump speed
r/min
1000
1000
1000
Average injection quantity
mm3/st.
135
133
137
Max. variation between cylinders
%
0
-3
3
Basic
*
Fixing the lever
*
Boost pressure
kPa
73.3
73.3
Boost pressure
mmHg
550
550
Injection quantity adjustment_02
Adjusting point
-
Rack position
8.4+-0.5
Pump speed
r/min
400
400
400
Average injection quantity
mm3/st.
14.5
11.3
17.7
Max. variation between cylinders
%
0
-13
13
Fixing the rack
*
Boost pressure
kPa
0
0
0
Boost pressure
mmHg
0
0
0
Remarks
Adjust only variation between cylinders; adjust governor according to governor specifications.
Adjust only variation between cylinders; adjust governor according to governor specifications.
Boost compensator adjustment
Pump speed
r/min
500
500
500
Rack position
R1-0.9
Boost pressure
kPa
32
29.3
34.7
Boost pressure
mmHg
240
220
260
Boost compensator adjustment_02
Pump speed
r/min
500
500
500
Rack position
R1-0.65
Boost pressure
kPa
40
38.7
41.3
Boost pressure
mmHg
300
290
310
Boost compensator adjustment_03
Pump speed
r/min
500
500
500
Rack position
R1(11.3)
Boost pressure
kPa
60
60
60
Boost pressure
mmHg
450
450
450
Timer adjustment
Pump speed
r/min
1000++
Advance angle
deg.
0
0
0
Remarks
Do not advance until starting N = 1000.
Do not advance until starting N = 1000.
Timer adjustment_02
Pump speed
r/min
1100
Advance angle
deg.
0.5
Timer adjustment_03
Pump speed
r/min
-
Advance angle
deg.
1
1
1
Remarks
Measure the actual speed, stop
Measure the actual speed, stop
Test data Ex:
Governor adjustment
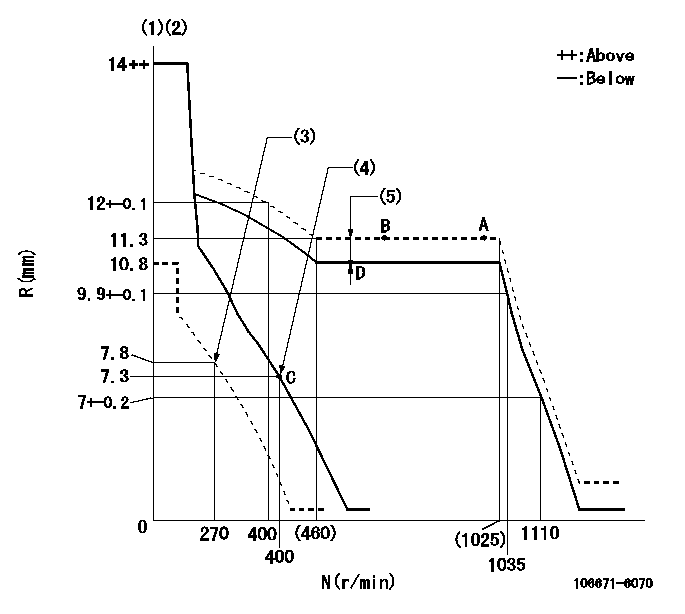
N:Pump speed
R:Rack position (mm)
(1)Target notch: K
(2)Tolerance for racks not indicated: +-0.05mm.
(3)Set idle sub-spring
(4)Main spring setting
(5)Boost compensator stroke: BCL
----------
K=14 BCL=0.9+-0.1mm
----------
----------
K=14 BCL=0.9+-0.1mm
----------
Speed control lever angle
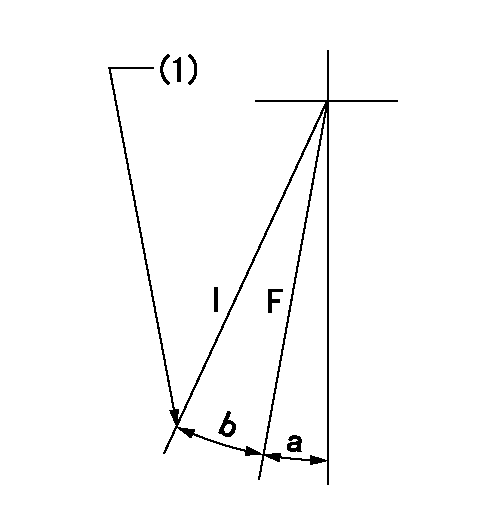
F:Full speed
I:Idle
(1)Stopper bolt setting
----------
----------
a=6deg+-5deg b=17deg+-5deg
----------
----------
a=6deg+-5deg b=17deg+-5deg
Stop lever angle
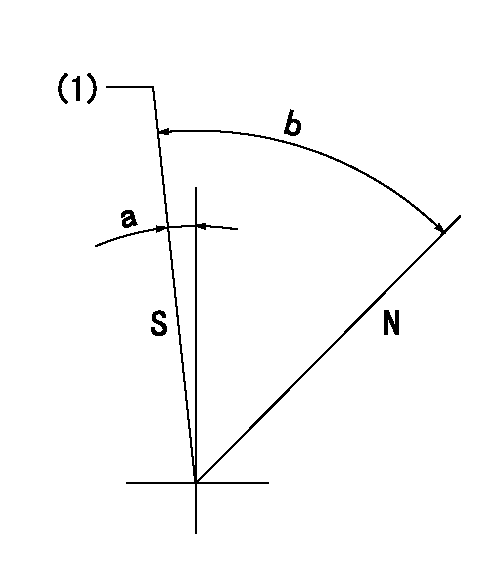
N:Pump normal
S:Stop the pump.
(1)Rack position = aa, speed = bb (stamp at delivery)
----------
aa=1-0.5mm bb=0r/min
----------
a=15deg+-5deg b=70deg+-5deg
----------
aa=1-0.5mm bb=0r/min
----------
a=15deg+-5deg b=70deg+-5deg
Timing setting
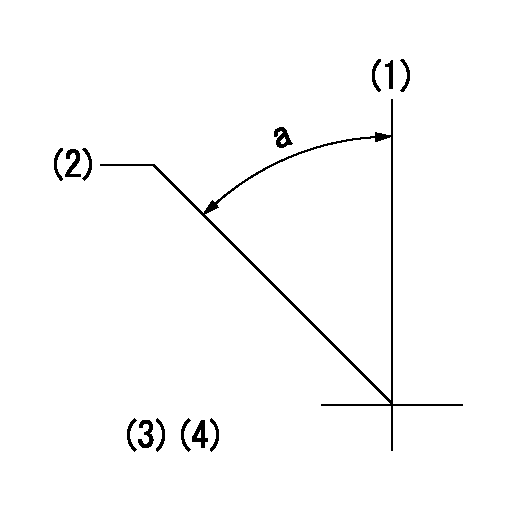
(1)Pump vertical direction
(2)Position of timer's threaded hole at No 1 cylinder's beginning of injection
(3)B.T.D.C.: aa
(4)-
----------
aa=14deg
----------
a=(50deg)
----------
aa=14deg
----------
a=(50deg)
Information:
Image1.2.1
Image1.2.2
Image1.2.3
3 - Using long straps and a crane, tilt the DOC on end so the outlet with the perforated plate end is facing up. With the DOC rotated on end, locate and center the drilling template and use C-Clamps to clamp the template in place so it does not shift.
With the DOC in this position ensure that all of the inside insulation pieces and the perforated plate are still in the correct position and in place.
Reference Image 1.3.1 and 1.3.2
Image1.3.1
Image1.3.2
4 - Position a mag base drill on the drilling template. While holding the inside perforated plate in position with a piece of 2" x 4" x 8' piece of lumber or other suitable size, drill the (4) 1.25" (31.75 mm) holes using a carbide tip cutter bit. Drill through the DOC end plate and insulation making sure the carbide tip cutter bit does NOT go through the perforated plate on the inside.
Note: A Hougen magnetic base drill works best for the drilling process and use a Hougen Copperhead Carbide Tip Annular Cutter bit. Hougen p/n 18240
Once the holes are drilled through clean out the drilled material.
Change out the carbide tip hole saw bit with a 3/8" drill bit. Ensure that the mag base drill stays in the same position so the 3/8" bit is drilling in the center of the 1.25" hole.
Note: The spacer can also be inserted in the 1.25" hole to use as a template to drill the 3/8" hole.
Drill a 3/8" hole through the inside perforated plate being careful not to drill too deep. From the outside end plate, the minimum drilling depth is 45 mm and the maximum drilling depth is 150 mm.
Note: This is a two person process with one person holding the inside perforated plate in place while the other person is drilling the holes. Additionally, the drilling through DOC should be done slowly as to not bend or drill through the perforated plate.
Reference Image 1.4.1 and 1.4.2
Image1.4.1
Image1.4.2
5 - Install the 1.25" spacer and slotted washer (Pacman washer) into each of the (4) drilled holes. The slotted washer will have to be angled in with needle nosed pliers and then moved in place in order to get it in the correct location. As an alternative to using needle nosed pliers, a thin wire tie can be tied around the slotted washer and lowered into the hole out of the way until it is re-positioned on top of the spacer.
Reference Images 1.5.1 and 1.5.2
Image1.5.1
Image1.5.2
6 - Once the spacer and slotted washer (Pacman washer) are installed in the DOC, install the 1.25" washer on top of the slotted washer. The 1.25" washer needs to be coated on both sides with Loctite 2620 sealant prior to installation.
From the outside of the DOC, install (2) each of the 3/8" bolt, small bolt washer, 2" washers and Graphite gasket through the holes in the slotted washers and spacers. On the inside of the DOC install an L Angle piece onto the lower 3/8" bolt threads and then