Information injection-pump assembly
ZEXEL
106671-5380
1066715380
NISSAN-DIESEL
1680095502
1680095502
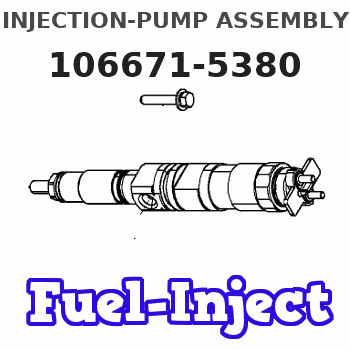
Rating:
Service parts 106671-5380 INJECTION-PUMP ASSEMBLY:
1.
_
7.
COUPLING PLATE
8.
_
9.
_
11.
Nozzle and Holder
16600-95505
12.
Open Pre:MPa(Kqf/cm2)
18.6{190}/22.6{230}
14.
NOZZLE
Include in #1:
106671-5380
as INJECTION-PUMP ASSEMBLY
Cross reference number
ZEXEL
106671-5380
1066715380
NISSAN-DIESEL
1680095502
1680095502
Zexel num
Bosch num
Firm num
Name
Calibration Data:
Adjustment conditions
Test oil
1404 Test oil ISO4113 or {SAEJ967d}
1404 Test oil ISO4113 or {SAEJ967d}
Test oil temperature
degC
40
40
45
Nozzle and nozzle holder
105780-8140
Bosch type code
EF8511/9A
Nozzle
105780-0000
Bosch type code
DN12SD12T
Nozzle holder
105780-2080
Bosch type code
EF8511/9
Opening pressure
MPa
17.2
Opening pressure
kgf/cm2
175
Injection pipe
Outer diameter - inner diameter - length (mm) mm 8-3-600
Outer diameter - inner diameter - length (mm) mm 8-3-600
Overflow valve
134424-4120
Overflow valve opening pressure
kPa
255
221
289
Overflow valve opening pressure
kgf/cm2
2.6
2.25
2.95
Tester oil delivery pressure
kPa
157
157
157
Tester oil delivery pressure
kgf/cm2
1.6
1.6
1.6
Direction of rotation (viewed from drive side)
Right R
Right R
Injection timing adjustment
Direction of rotation (viewed from drive side)
Right R
Right R
Injection order
1-4-2-6-
3-5
Pre-stroke
mm
4.4
4.37
4.43
Beginning of injection position
Drive side NO.1
Drive side NO.1
Difference between angles 1
Cal 1-4 deg. 60 59.75 60.25
Cal 1-4 deg. 60 59.75 60.25
Difference between angles 2
Cyl.1-2 deg. 120 119.75 120.25
Cyl.1-2 deg. 120 119.75 120.25
Difference between angles 3
Cal 1-6 deg. 180 179.75 180.25
Cal 1-6 deg. 180 179.75 180.25
Difference between angles 4
Cal 1-3 deg. 240 239.75 240.25
Cal 1-3 deg. 240 239.75 240.25
Difference between angles 5
Cal 1-5 deg. 300 299.75 300.25
Cal 1-5 deg. 300 299.75 300.25
Injection quantity adjustment
Adjusting point
-
Rack position
13
Pump speed
r/min
650
650
650
Average injection quantity
mm3/st.
156.5
153.5
159.5
Max. variation between cylinders
%
0
-4
4
Basic
*
Fixing the rack
*
Standard for adjustment of the maximum variation between cylinders
*
Injection quantity adjustment_02
Adjusting point
Z
Rack position
8+-0.5
Pump speed
r/min
530
530
530
Average injection quantity
mm3/st.
10
9
11
Max. variation between cylinders
%
0
-10
10
Fixing the rack
*
Standard for adjustment of the maximum variation between cylinders
*
Injection quantity adjustment_03
Adjusting point
A
Rack position
R1(13)
Pump speed
r/min
650
650
650
Average injection quantity
mm3/st.
156.5
154.5
158.5
Basic
*
Fixing the lever
*
Boost pressure
kPa
46.7
46.7
Boost pressure
mmHg
350
350
Injection quantity adjustment_04
Adjusting point
B
Rack position
(R1+0.2)
Pump speed
r/min
1250
1250
1250
Average injection quantity
mm3/st.
127.5
121.5
133.5
Fixing the lever
*
Boost pressure
kPa
46.7
46.7
Boost pressure
mmHg
350
350
Injection quantity adjustment_05
Adjusting point
C
Rack position
R2(R1-1)
Pump speed
r/min
300
300
300
Average injection quantity
mm3/st.
149.5
143.5
155.5
Fixing the lever
*
Boost pressure
kPa
46.7
46.7
Boost pressure
mmHg
350
350
Injection quantity adjustment_06
Adjusting point
D
Rack position
R2-1.35
Pump speed
r/min
300
300
300
Average injection quantity
mm3/st.
81.5
75.5
87.5
Fixing the lever
*
Boost pressure
kPa
0
0
0
Boost pressure
mmHg
0
0
0
Boost compensator adjustment
Pump speed
r/min
300
300
300
Rack position
R2-1.35
Boost pressure
kPa
10.7
9.4
12
Boost pressure
mmHg
80
70
90
Boost compensator adjustment_02
Pump speed
r/min
300
300
300
Rack position
R2(R1-1)
Boost pressure
kPa
33.3
33.3
33.3
Boost pressure
mmHg
250
250
250
Test data Ex:
Governor adjustment

N:Pump speed
R:Rack position (mm)
(1)Torque cam stamping: T1
(2)Tolerance for racks not indicated: +-0.05mm.
(3)Boost compensator stroke: BCL
(4)Damper spring setting
----------
T1=AC50 BCL=1.35+-0.1mm
----------
----------
T1=AC50 BCL=1.35+-0.1mm
----------
Timer adjustment

(1)Adjusting range
(2)Step response time
(N): Speed of the pump
(L): Load
(theta) Advance angle
(Srd1) Step response time 1
(Srd2) Step response time 2
1. Adjusting conditions for the variable timer
(1)Adjust the clearance between the pickup and the protrusion to L.
----------
L=1-0.2mm N4=800r/min C4=(8deg) t1=2--sec. t2=2--sec.
----------
N1=400r/min N2=1000++r/min N3=1250r/min C1=8+-0.3deg C2=4++deg C3=4--deg P1=0kPa(0kgf/cm2) P2=147kPa(1.5kgf/cm2) P3=392kPa(4kgf/cm2) R01=0/4load R02=4/4load R03=4/4load
----------
L=1-0.2mm N4=800r/min C4=(8deg) t1=2--sec. t2=2--sec.
----------
N1=400r/min N2=1000++r/min N3=1250r/min C1=8+-0.3deg C2=4++deg C3=4--deg P1=0kPa(0kgf/cm2) P2=147kPa(1.5kgf/cm2) P3=392kPa(4kgf/cm2) R01=0/4load R02=4/4load R03=4/4load
Speed control lever angle

F:Full speed
I:Idle
(1)Use the hole at R = aa
(2)Stopper bolt set position 'H'
----------
aa=39mm
----------
a=34deg+-5deg b=41deg+-3deg
----------
aa=39mm
----------
a=34deg+-5deg b=41deg+-3deg
Stop lever angle

N:Pump normal
S:Stop the pump.
(1)Use the pin at R = aa
(2)Set the stopper screw so that speed = bb and the rack position = cc (after setting apply red paint).
----------
aa=40mm bb=0r/min cc=1.5+-0.3mm
----------
a=20deg+-5deg b=44deg+-5deg
----------
aa=40mm bb=0r/min cc=1.5+-0.3mm
----------
a=20deg+-5deg b=44deg+-5deg
0000001501 RACK SENSOR
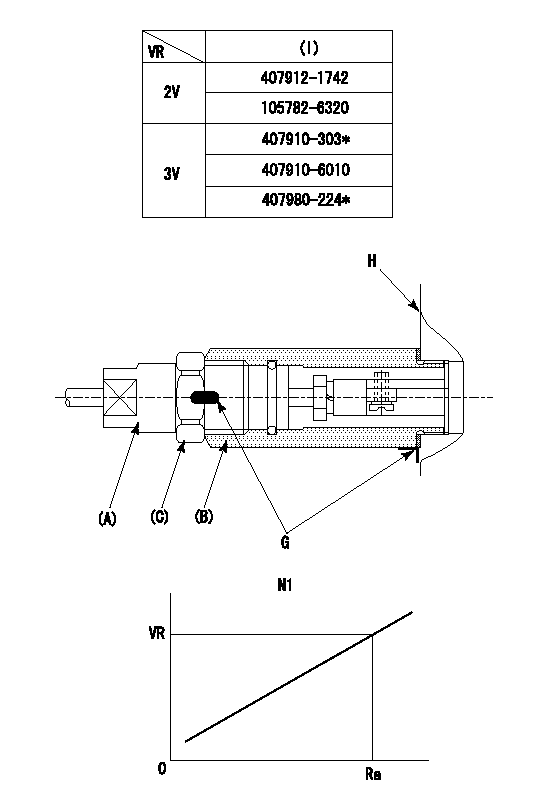
(VR) measurement voltage
(I) Part number of the control unit
(G) Apply red paint.
(H): End surface of the pump
1. Rack sensor adjustment (-0620)
(1)Fix the speed control lever at the full position
(2)Set the speed to N1 r/min.
(If the boost compensator is provided, apply boost pressure.)
(3)Adjust the bobbin (A) so that the rack sensor's output voltage is VR+-0.01.
(4)At that time, rack position must be Ra.
(5)Apply G at two places.
Connecting part between the joint (B) and the nut (F)
Connecting part between the joint (B) and the end surface of the pump (H)
----------
N1=650r/min Ra=R1(13)mm
----------
----------
N1=650r/min Ra=R1(13)mm
----------
Timing setting

(1)Pump vertical direction
(2)Coupling's key groove position at No 1 cylinder's beginning of injection
(3)-
(4)-
----------
----------
a=(30deg)
----------
----------
a=(30deg)
Information:
The diagnostic lamp, on the truck dashboard, can be used to communicate status or operation problems of the electronic control system.Trucks With Cruise
The dash mounted cruise switches are used to interrogate the ECM for system status. With the cruise switch in the "off" position, hold the set/resume switch in the resume position until "check engine" light begins to flash. The sequence of flashes represents the system diagnostic message. The first sequence of flashes adds up to the first digit of the fault code. After a one second pause, a second sequence of flashes will occur which represents the second digit of the fault code. Any additional fault codes will follow, after a pause, and will be displayed in the same manner.Trucks Without Cruise
If cruise control switches are not installed or if their configuration (such as a GM type switch) does not permit their usage for checking diagnostic codes, then a push button momentary ON switch should be installed between Pin 3 of the vehicle connector P7 and engine ground.Faults With Throttle Response
The vehicle should be driven to a dealer for service ONLY if the engine oil pressure gauge indicates normal engine oil pressure and engine fuel pressure is within the normal range.Faults Without Throttle Response
If the check engine light is on and the engine does not respond to changes in throttle position, the vehicle should be driven to a dealer ONLY if the oil pressure gauge indicates normal engine oil pressure and engine fuel pressure is within the normal range.If equipped, turn on the cruise on/off switch and operate the vehicle using the set/resume cruise control switch to raise and lower the engine rpm.The cruise control mode is operational from 0 km/h (mph) up to the vehicle speed limit (VSL) when the 3406B (PEEC III) control unit does not respond to changes in throttle position. Maximum engine rpm will be the programmed engine rpm at the vehicle speed limit (VSL). Cruise control must be reselected after each gear change.
The dash mounted cruise switches are used to interrogate the ECM for system status. With the cruise switch in the "off" position, hold the set/resume switch in the resume position until "check engine" light begins to flash. The sequence of flashes represents the system diagnostic message. The first sequence of flashes adds up to the first digit of the fault code. After a one second pause, a second sequence of flashes will occur which represents the second digit of the fault code. Any additional fault codes will follow, after a pause, and will be displayed in the same manner.Trucks Without Cruise
If cruise control switches are not installed or if their configuration (such as a GM type switch) does not permit their usage for checking diagnostic codes, then a push button momentary ON switch should be installed between Pin 3 of the vehicle connector P7 and engine ground.Faults With Throttle Response
The vehicle should be driven to a dealer for service ONLY if the engine oil pressure gauge indicates normal engine oil pressure and engine fuel pressure is within the normal range.Faults Without Throttle Response
If the check engine light is on and the engine does not respond to changes in throttle position, the vehicle should be driven to a dealer ONLY if the oil pressure gauge indicates normal engine oil pressure and engine fuel pressure is within the normal range.If equipped, turn on the cruise on/off switch and operate the vehicle using the set/resume cruise control switch to raise and lower the engine rpm.The cruise control mode is operational from 0 km/h (mph) up to the vehicle speed limit (VSL) when the 3406B (PEEC III) control unit does not respond to changes in throttle position. Maximum engine rpm will be the programmed engine rpm at the vehicle speed limit (VSL). Cruise control must be reselected after each gear change.