Information injection-pump assembly
BOSCH
9 400 610 850
9400610850
ZEXEL
106671-5241
1066715241
NISSAN-DIESEL
1671396913
1671396913
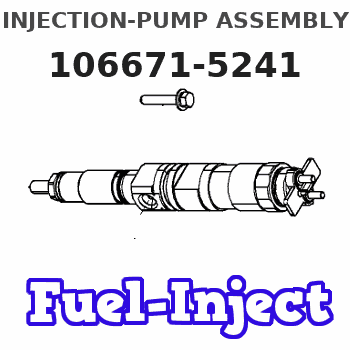
Rating:
Service parts 106671-5241 INJECTION-PUMP ASSEMBLY:
1.
_
7.
COUPLING PLATE
8.
_
9.
_
11.
Nozzle and Holder
16600-96603
12.
Open Pre:MPa(Kqf/cm2)
22.6{230}
15.
NOZZLE SET
Include in #1:
106671-5241
as INJECTION-PUMP ASSEMBLY
Cross reference number
BOSCH
9 400 610 850
9400610850
ZEXEL
106671-5241
1066715241
NISSAN-DIESEL
1671396913
1671396913
Zexel num
Bosch num
Firm num
Name
Calibration Data:
Adjustment conditions
Test oil
1404 Test oil ISO4113 or {SAEJ967d}
1404 Test oil ISO4113 or {SAEJ967d}
Test oil temperature
degC
40
40
45
Nozzle and nozzle holder
105780-8140
Bosch type code
EF8511/9A
Nozzle
105780-0000
Bosch type code
DN12SD12T
Nozzle holder
105780-2080
Bosch type code
EF8511/9
Opening pressure
MPa
17.2
Opening pressure
kgf/cm2
175
Injection pipe
Outer diameter - inner diameter - length (mm) mm 8-3-600
Outer diameter - inner diameter - length (mm) mm 8-3-600
Overflow valve
132424-0620
Overflow valve opening pressure
kPa
157
123
191
Overflow valve opening pressure
kgf/cm2
1.6
1.25
1.95
Tester oil delivery pressure
kPa
157
157
157
Tester oil delivery pressure
kgf/cm2
1.6
1.6
1.6
Direction of rotation (viewed from drive side)
Right R
Right R
Injection timing adjustment
Direction of rotation (viewed from drive side)
Right R
Right R
Injection order
1-4-2-6-
3-5
Pre-stroke
mm
3.9
3.85
3.95
Beginning of injection position
Drive side NO.1
Drive side NO.1
Difference between angles 1
Cal 1-4 deg. 60 59.5 60.5
Cal 1-4 deg. 60 59.5 60.5
Difference between angles 2
Cyl.1-2 deg. 120 119.5 120.5
Cyl.1-2 deg. 120 119.5 120.5
Difference between angles 3
Cal 1-6 deg. 180 179.5 180.5
Cal 1-6 deg. 180 179.5 180.5
Difference between angles 4
Cal 1-3 deg. 240 239.5 240.5
Cal 1-3 deg. 240 239.5 240.5
Difference between angles 5
Cal 1-5 deg. 300 299.5 300.5
Cal 1-5 deg. 300 299.5 300.5
Injection quantity adjustment
Adjusting point
A
Rack position
11.6
Pump speed
r/min
1050
1050
1050
Average injection quantity
mm3/st.
176.5
174.5
178.5
Max. variation between cylinders
%
0
-4
4
Basic
*
Fixing the lever
*
Boost pressure
kPa
66.7
66.7
Boost pressure
mmHg
500
500
Injection quantity adjustment_02
Adjusting point
C
Rack position
6.4+-0.5
Pump speed
r/min
260
260
260
Average injection quantity
mm3/st.
13.5
12.2
14.8
Max. variation between cylinders
%
0
-10
10
Fixing the rack
*
Boost pressure
kPa
0
0
0
Boost pressure
mmHg
0
0
0
Injection quantity adjustment_03
Adjusting point
D
Rack position
8.8
Pump speed
r/min
400
400
400
Average injection quantity
mm3/st.
91.5
85.5
97.5
Fixing the lever
*
Boost pressure
kPa
0
0
0
Boost pressure
mmHg
0
0
0
Boost compensator adjustment
Pump speed
r/min
400
400
400
Rack position
8.8
Boost pressure
kPa
13.3
12
14.6
Boost pressure
mmHg
100
90
110
Boost compensator adjustment_02
Pump speed
r/min
400
400
400
Rack position
11.05
Boost pressure
kPa
42
35.3
48.7
Boost pressure
mmHg
315
265
365
Boost compensator adjustment_03
Pump speed
r/min
400
400
400
Rack position
11.8+0.2
Boost pressure
kPa
53.3
53.3
53.3
Boost pressure
mmHg
400
400
400
Timer adjustment
Pump speed
r/min
750--
Advance angle
deg.
0
0
0
Remarks
Start
Start
Timer adjustment_02
Pump speed
r/min
700
Advance angle
deg.
0.5
Timer adjustment_03
Pump speed
r/min
1050
Advance angle
deg.
1
0.5
1.5
Remarks
Finish
Finish
Test data Ex:
Governor adjustment
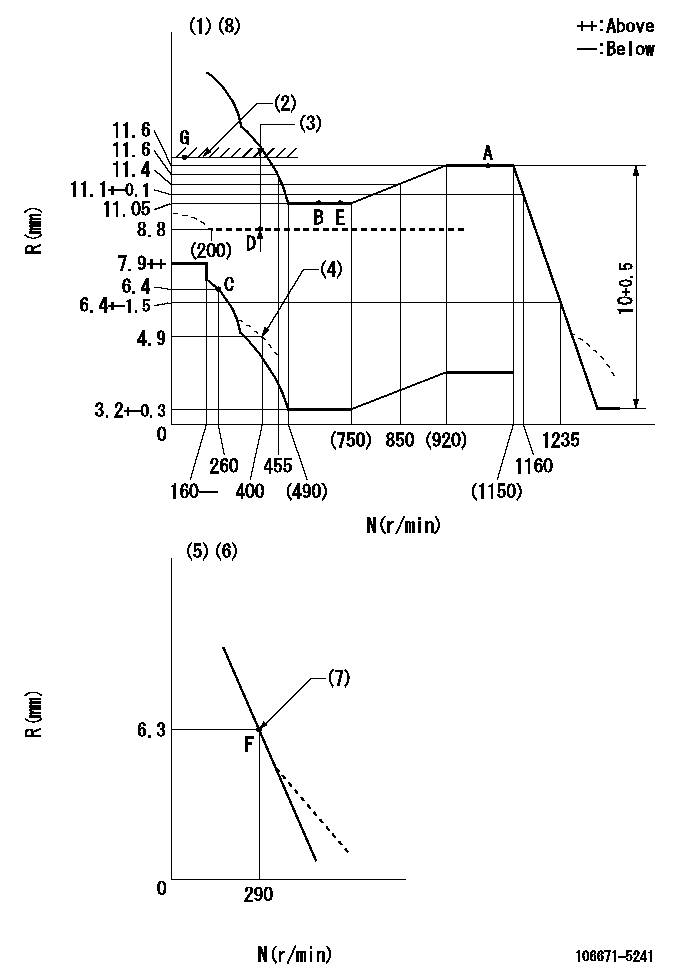
N:Pump speed
R:Rack position (mm)
(1)Tolerance for racks not indicated: +-0.05mm.
(2)Rack limit using the stop lever: R1
(3)Boost compensator stroke: BCL
(4)Damper spring setting
(5)Variable speed specification: idling adjustment
(6)Fix the lever at the full-load position at delivery.
(7)Main spring setting
(8)Perform governor adjustment at an ambient temperature of at least 15 deg C (boost compensator start spring is shape memory alloy).
----------
R1=11.8+0.2mm BCL=(3.1)mm
----------
----------
R1=11.8+0.2mm BCL=(3.1)mm
----------
Speed control lever angle

F:Full speed
I:Idle
(1)Pump speed = aa
(2)Set the stopper bolt (fixed at full-load position at delivery.)
----------
aa=290r/min
----------
a=16deg+-5deg b=6deg+-5deg
----------
aa=290r/min
----------
a=16deg+-5deg b=6deg+-5deg
0000000901

F:Full load
I:Idle
(1)Stopper bolt setting
(2)Use the hole at R = aa
----------
aa=42mm
----------
a=29deg+-3deg b=45deg+-5deg
----------
aa=42mm
----------
a=29deg+-3deg b=45deg+-5deg
Stop lever angle

N:Pump normal
S:Stop the pump.
(1)Rack position = aa
----------
aa=11.8+0.2mm
----------
a=39deg+-5deg b=37deg+-5deg
----------
aa=11.8+0.2mm
----------
a=39deg+-5deg b=37deg+-5deg
Timing setting

(1)Pump vertical direction
(2)Coupling's key groove position at No 1 cylinder's beginning of injection
(3)-
(4)-
----------
----------
a=(20deg)
----------
----------
a=(20deg)
Information:
Typical Example3. Loosen the clamps on breather tube (1), and pull it back for clearance. 4. Remove bolt (2) from the cover on the side of the cylinder block. 5. Remove the three bolts that hold cover (3) to the water pump. Remove cover (3) from the water pump. 6. Remove the two bolts, and remove elbow (4) from bonnet (5). Remove the two bolts, and remove bonnet (5) from the water pump. It is not necessary to remove bolts (6). These bolts only hold the cover to the timing gear cover.7. Remove six long bolts (7) that hold the water pump to the timing gear cover. Remove water pump (8).Install Water Pump
1. Check the O-ring seals and gaskets, and make replacements if needed. 2. Make sure O-ring seal (9) is in position on the water pump. Put water pump (8) into position in the timing gear cover. Install the bolts that hold the water pump in place. 3. Make sure the gaskets are in place. Connect bonnet (5) to the water pump. Connect elbow (4) to the bonnet. 4. Make sure O-ring seal (10) is in position, and install cover (3) on the water pump. 5. Install bolt (2) on the cover on the side of the engine. 6. Put breather tube (1) in position, and install the clamps that hold it.7. Install the altenator mounting group and alternator on the engine.8. Install the water temperature regulator and manifold. See the topic Install Water Temperature Regulator and Manifold.9. Fill the cooling system to the correct level. See the Maintenance Manual.Disassemble & Assemble Water Pump
Start By:a. remove water pump The water pump seal can be replaced without removing the water pump from the engine.An intermittent leakage of a small amount of coolant from the hole in the water pump housing is not an indication of a water pump seal failure. This is required to provide lubrication for the seal. Replace the water pump seal only if a large amount of leakage or a constant flow of coolant is observed draining from the water pump housing. 1. Remove O-ring seal (3) from adapter (4). Remove the adapter from housing (7). Remove the O-ring seal from the outside of the adapter.2. Remove bolt (1) and washer (2). Use tooling (A) to remove impeller (6) from shaft (13).3. Remove spring and seal (5) from the shaft.4. Remove four bolts (16) from retainer (12) that hold the shaft assembly to the pump housing. Remove O-ring seal (18) from housing (7).5. Remove gear and shaft assembly (17) from the housing. Remove bolt (15), retainer (14), and retainer (12) from the shaft assembly.6. Use a press to remove shaft (13) from the gear. Remove bearing (9), spacer (10), and bearing (11) from the shaft.7. Remove lip-type seal (8) from the housing.8. Turn the housing over, and remove ceramic ring (20) and seal (19) from the housing. The following steps are for the assembly of the water pump.9. Use 6V1541 Quick Cure Primer and clean