Information injection-pump assembly
BOSCH
F 019 Z10 529
f019z10529
ZEXEL
106671-5170
1066715170
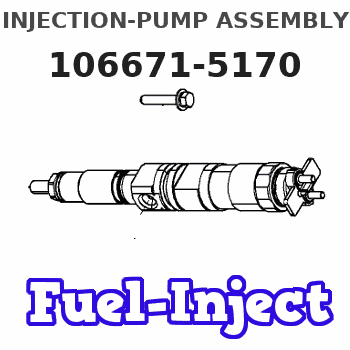
Rating:
Service parts 106671-5170 INJECTION-PUMP ASSEMBLY:
1.
_
7.
COUPLING PLATE
8.
_
9.
_
11.
Nozzle and Holder
1660096573
12.
Open Pre:MPa(Kqf/cm2)
17.7(180)/22.6(230)
15.
NOZZLE SET
Include in #1:
106671-5170
as INJECTION-PUMP ASSEMBLY
Cross reference number
BOSCH
F 019 Z10 529
f019z10529
ZEXEL
106671-5170
1066715170
Zexel num
Bosch num
Firm num
Name
Calibration Data:
Adjustment conditions
Test oil
1404 Test oil ISO4113 or {SAEJ967d}
1404 Test oil ISO4113 or {SAEJ967d}
Test oil temperature
degC
40
40
45
Nozzle and nozzle holder
105780-8140
Bosch type code
EF8511/9A
Nozzle
105780-0000
Bosch type code
DN12SD12T
Nozzle holder
105780-2080
Bosch type code
EF8511/9
Opening pressure
MPa
17.2
Opening pressure
kgf/cm2
175
Injection pipe
Outer diameter - inner diameter - length (mm) mm 8-3-600
Outer diameter - inner diameter - length (mm) mm 8-3-600
Overflow valve
132424-0620
Overflow valve opening pressure
kPa
157
123
191
Overflow valve opening pressure
kgf/cm2
1.6
1.25
1.95
Tester oil delivery pressure
kPa
157
157
157
Tester oil delivery pressure
kgf/cm2
1.6
1.6
1.6
Direction of rotation (viewed from drive side)
Right R
Right R
Injection timing adjustment
Direction of rotation (viewed from drive side)
Right R
Right R
Injection order
1-4-2-6-
3-5
Pre-stroke
mm
3.9
3.85
3.95
Beginning of injection position
Drive side NO.1
Drive side NO.1
Difference between angles 1
Cal 1-4 deg. 60 59.5 60.5
Cal 1-4 deg. 60 59.5 60.5
Difference between angles 2
Cyl.1-2 deg. 120 119.5 120.5
Cyl.1-2 deg. 120 119.5 120.5
Difference between angles 3
Cal 1-6 deg. 180 179.5 180.5
Cal 1-6 deg. 180 179.5 180.5
Difference between angles 4
Cal 1-3 deg. 240 239.5 240.5
Cal 1-3 deg. 240 239.5 240.5
Difference between angles 5
Cal 1-5 deg. 300 299.5 300.5
Cal 1-5 deg. 300 299.5 300.5
Injection quantity adjustment
Adjusting point
A
Rack position
10.8
Pump speed
r/min
600
600
600
Average injection quantity
mm3/st.
174.4
172.4
176.4
Max. variation between cylinders
%
0
-4
4
Basic
*
Fixing the lever
*
Solenoid boost comp. OFF
*
Injection quantity adjustment_02
Adjusting point
C
Rack position
5.3+-0.5
Pump speed
r/min
225
225
225
Average injection quantity
mm3/st.
9
8
10
Max. variation between cylinders
%
0
-10
10
Fixing the rack
*
Solenoid boost comp. OFF
*
Injection quantity adjustment_03
Adjusting point
D
Rack position
8.4
Pump speed
r/min
300
300
300
Average injection quantity
mm3/st.
107.4
105.4
109.4
Fixing the lever
*
Solenoid boost comp. ON
*
Test data Ex:
Governor adjustment

N:Pump speed
R:Rack position (mm)
(1)Tolerance for racks not indicated: +-0.05mm.
(2)Rack limit using the stop lever: R1
(3)Damper spring setting
(4)Variable speed specification: idling adjustment
(5)Fix the lever at the full-load position at delivery.
(6)Main spring setting
----------
R1=11.1+-0.1mm
----------
----------
R1=11.1+-0.1mm
----------
Timer adjustment

(1)Adjusting range
(2)Step response time
(N): Speed of the pump
(L): Load
(theta) Advance angle
(Srd1) Step response time 1
(Srd2) Step response time 2
1. Adjusting conditions for the variable timer
(1)Adjust the clearance between the pickup and the protrusion to L.
----------
L=1-0.2mm N4=800r/min C4=(6.5deg) t1=2--sec. t2=2--sec.
----------
N1=300r/min N2=900++r/min N3=1100r/min C1=6.5+-0.3deg C2=3++deg C3=4--deg P1=0kPa(0kgf/cm2) P2=196kPa(2kgf/cm2) P3=392kPa(4kgf/cm2) R01=0/4load R02=4/4load R03=4/4load
----------
L=1-0.2mm N4=800r/min C4=(6.5deg) t1=2--sec. t2=2--sec.
----------
N1=300r/min N2=900++r/min N3=1100r/min C1=6.5+-0.3deg C2=3++deg C3=4--deg P1=0kPa(0kgf/cm2) P2=196kPa(2kgf/cm2) P3=392kPa(4kgf/cm2) R01=0/4load R02=4/4load R03=4/4load
Speed control lever angle

F:Full speed
I:Idle
(1)Pump speed = aa
(2)Set the stopper bolt (fixed at full-load position at delivery.)
----------
aa=290r/min
----------
a=(13deg)+-5deg b=5.5deg+-5deg
----------
aa=290r/min
----------
a=(13deg)+-5deg b=5.5deg+-5deg
0000000901

F:Full load
I:Idle
(1)Stopper bolt setting
(2)Use the hole at R = aa
----------
aa=42mm
----------
a=34.5deg+-3deg b=45deg+-5deg
----------
aa=42mm
----------
a=34.5deg+-3deg b=45deg+-5deg
Stop lever angle

N:Pump normal
S:Stop the pump.
(1)Rack position = aa
----------
aa=11.1+-0.1mm
----------
a=33deg+-5deg b=33deg+-5deg
----------
aa=11.1+-0.1mm
----------
a=33deg+-5deg b=33deg+-5deg
0000001501 RACK SENSOR
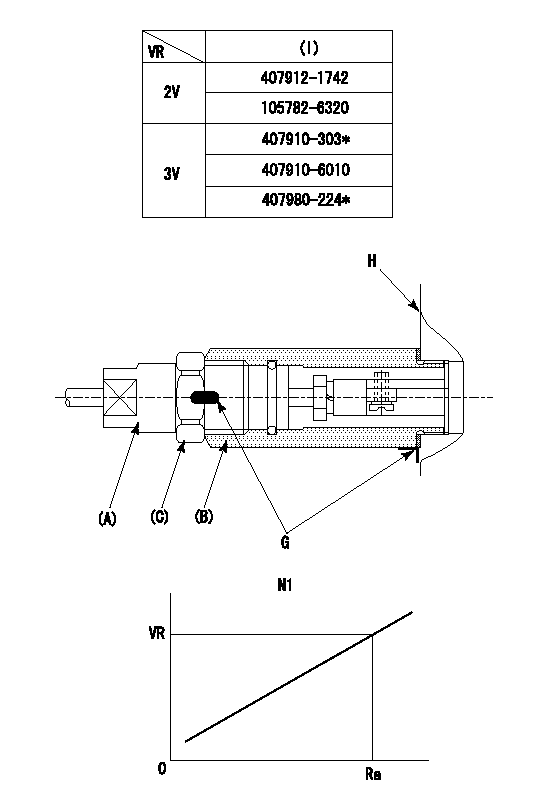
(VR) measurement voltage
(I) Part number of the control unit
(G) Apply red paint.
(H): End surface of the pump
1. Rack sensor adjustment (-0620)
(1)Fix the speed control lever at the full position
(2)Set the speed to N1 r/min.
(If the boost compensator is provided, apply boost pressure.)
(3)Adjust the bobbin (A) so that the rack sensor's output voltage is VR+-0.01.
(4)At that time, rack position must be Ra.
(5)Apply G at two places.
Connecting part between the joint (B) and the nut (F)
Connecting part between the joint (B) and the end surface of the pump (H)
----------
N1=600r/min Ra=10.8mm
----------
----------
N1=600r/min Ra=10.8mm
----------
0000001601 BCS

(A) Screw for precise adjustment
(B) Pre-adjustment screw
(C) Control rack, rack decrease direction
(D) Rack limit
1. Solenoid boost compensator adjustment
(1)Supply DC: V1 to the solenoid terminals and confirm solenoid operation.
(2)With the solenoid ON, calculate L1 from the value of R1. [L1 = La - (10.5 - R1) +-0.2]
(3)Adjust (B) to obtain L1.
(4)Assemble the solenoid to the governor.
(5)With the solenoid ON, readjust (B) so that R1 is within the allowance a.
(6)With the solenoid OFF, perform all governor adjustments except rack limit adjustment.
(7)Set the pump speed at N1 and turn the solenoid ON.
(8)Adjust (A) so that R1 is within the allowance range a.
(9)Set the pump speed at N1 and fix the load lever in the full position
(10)Turn the solenoid switch ON and OFF several times and confirm that the difference in rack positions is within L2.
(11)Set the rack limit.
(12)Stamp the solenoid valve.
----------
V1=24V N1=300r/min N2=0r/min R1=8.4mm a=+-0.5mm La=28mm L1=25.9+-0.2mm L2=3.5~5mm
----------
----------
V1=24V N1=300r/min N2=0r/min R1=8.4mm a=+-0.5mm La=28mm L1=25.9+-0.2mm L2=3.5~5mm
----------
0000001701 SPEED SENSOR

(A) Flyweight projection
(B) Pickup sensor
(c) Lock nut
Speed sensor installation
(1)Install the speed sensor so that the clearance between the sensor and the flyweight projection is L.
(This gap is the gap when the pickup sensor is returned 1 turn from where it contacts the flyweight tooth.)
----------
L=0.8~1mm
----------
----------
L=0.8~1mm
----------
Timing setting

(1)Pump vertical direction
(2)Coupling's key groove position at No 1 cylinder's beginning of injection
(3)-
(4)-
----------
----------
a=(30deg)
----------
----------
a=(30deg)
Information:
Low Gears #1 RPM Limit:
Engine rpm limited below "Low Gear #1 Turn Off Speed". PEEC III will pause at this rpm, then allow slow acceleration up to Top Engine Limit. This is to encourage the driver to shift to the next highest gear. Maximum 3000 rpmMinimum 1100 rpmDefault 3000 rpmLow Gears #1 Turn Off:
Vehicle Speed where "Low Gears #1 RPM Limit" turns off. This must be matched with "Low Gear #1 RPM Limit" to the specific drive train for best performance. Maximum 30 mphMinimum 0 mphDefault 30 mphLow Gears #2 RPM Limit:
Similar to "Low Gears #1 RPM Limit". Typically programmed to slightly higher rpm. Maximum 3000 rpmMinimum 1100 rpmDefault 3000 rpmLow Gears #2 Turn Off:
Similar to "Low Gears #1 Turn Off". Typically programmed to a slightly higher vehicle speed. Maximum 50 mphMinimum 0 mphDefault 50 mphHigh Gear RPM Limit:
Engine RPM Limit when vehicle speed is above "High Gear Turn On Speed". This is a "hard" limit: PEEC III will not power the engine above this limit. This is to encourage the driver to shift up into overdrive or top gear. Maximum 3000 rpmMinimum 1300 rpmDefault 3000 rpmHigh Gear Turn On Speed:
Vehicle Speed where "High Gear RPM Limit" turns on. This must be matched to the specific drive train for best performance. Maximum 127 mphMinimum 30 mphDefault 127 mphEngine Parameters
Rating Number:
Number of rating within horsepower family. The personality module defines the horsepower family (such as 350 hp) and may contain several ratings within that family. The rating number defines which rating is used (such as 350 hp @ 1900 rpm or 330 hp @ 1700 rpm) within the family.Top Engine Limit:
Maximum engine RPM when the engine is under load. The engine will still achieve Rated RPM under no load conditions. Maximum Rated rpm + 20 rpmMinimum Rated rpm - 79 rpmDefault Rated rpm + 20 rpmLow Idle RPM:
Minimum engine RPM which may be programmed to any value between 600 RPM to 750 RPM range.Idle Shutdown Time:
Time (in minutes) that engine will idle before shutting down (between 3 and 60 minutes). Engine will only shutdown if PEEC III sees no engine load, no vehicle speed, and the park brake is set. If this parameter is programmed to zero, this feature is disabled and the engine will idle until the key switch is turned OFF.Passwords
Factory Passwords
Factory passwords are required to perform each of the following four functions:1. Program a New ECM When an ECM is replaced, the System Configuration Parameters must be programmed into the new ECM. These parameters are protected by factory passwords.2. Rerate Engine to another Engine Family This requires changing the personality Module Code, which is protected by factory passwords.3. Read Customer Passwords If the owner loses his customer passwords, he will not be able to program customer parameters. Using factory passwords, one can read customer passwords, then use those customer passwords to program customer parameters.4. Clear Certain Diagnostic Codes Only Diagnostic Code 23-02 (Excessive Engine Power) requires factory passwords to clear once it is logged. Certain other
Engine rpm limited below "Low Gear #1 Turn Off Speed". PEEC III will pause at this rpm, then allow slow acceleration up to Top Engine Limit. This is to encourage the driver to shift to the next highest gear. Maximum 3000 rpmMinimum 1100 rpmDefault 3000 rpmLow Gears #1 Turn Off:
Vehicle Speed where "Low Gears #1 RPM Limit" turns off. This must be matched with "Low Gear #1 RPM Limit" to the specific drive train for best performance. Maximum 30 mphMinimum 0 mphDefault 30 mphLow Gears #2 RPM Limit:
Similar to "Low Gears #1 RPM Limit". Typically programmed to slightly higher rpm. Maximum 3000 rpmMinimum 1100 rpmDefault 3000 rpmLow Gears #2 Turn Off:
Similar to "Low Gears #1 Turn Off". Typically programmed to a slightly higher vehicle speed. Maximum 50 mphMinimum 0 mphDefault 50 mphHigh Gear RPM Limit:
Engine RPM Limit when vehicle speed is above "High Gear Turn On Speed". This is a "hard" limit: PEEC III will not power the engine above this limit. This is to encourage the driver to shift up into overdrive or top gear. Maximum 3000 rpmMinimum 1300 rpmDefault 3000 rpmHigh Gear Turn On Speed:
Vehicle Speed where "High Gear RPM Limit" turns on. This must be matched to the specific drive train for best performance. Maximum 127 mphMinimum 30 mphDefault 127 mphEngine Parameters
Rating Number:
Number of rating within horsepower family. The personality module defines the horsepower family (such as 350 hp) and may contain several ratings within that family. The rating number defines which rating is used (such as 350 hp @ 1900 rpm or 330 hp @ 1700 rpm) within the family.Top Engine Limit:
Maximum engine RPM when the engine is under load. The engine will still achieve Rated RPM under no load conditions. Maximum Rated rpm + 20 rpmMinimum Rated rpm - 79 rpmDefault Rated rpm + 20 rpmLow Idle RPM:
Minimum engine RPM which may be programmed to any value between 600 RPM to 750 RPM range.Idle Shutdown Time:
Time (in minutes) that engine will idle before shutting down (between 3 and 60 minutes). Engine will only shutdown if PEEC III sees no engine load, no vehicle speed, and the park brake is set. If this parameter is programmed to zero, this feature is disabled and the engine will idle until the key switch is turned OFF.Passwords
Factory Passwords
Factory passwords are required to perform each of the following four functions:1. Program a New ECM When an ECM is replaced, the System Configuration Parameters must be programmed into the new ECM. These parameters are protected by factory passwords.2. Rerate Engine to another Engine Family This requires changing the personality Module Code, which is protected by factory passwords.3. Read Customer Passwords If the owner loses his customer passwords, he will not be able to program customer parameters. Using factory passwords, one can read customer passwords, then use those customer passwords to program customer parameters.4. Clear Certain Diagnostic Codes Only Diagnostic Code 23-02 (Excessive Engine Power) requires factory passwords to clear once it is logged. Certain other