Information injection-pump assembly
ZEXEL
106671-5150
1066715150
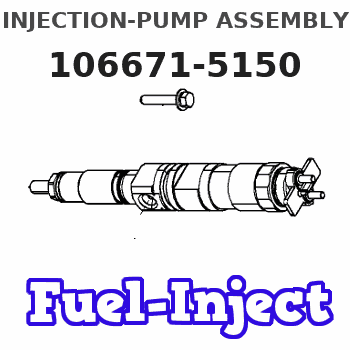
Rating:
Service parts 106671-5150 INJECTION-PUMP ASSEMBLY:
1.
_
7.
COUPLING PLATE
8.
_
9.
_
11.
Nozzle and Holder
16600-96575
12.
Open Pre:MPa(Kqf/cm2)
22.6{230}
15.
NOZZLE SET
Include in #1:
106671-5150
as INJECTION-PUMP ASSEMBLY
Cross reference number
ZEXEL
106671-5150
1066715150
Zexel num
Bosch num
Firm num
Name
106671-5150
INJECTION-PUMP ASSEMBLY
Calibration Data:
Adjustment conditions
Test oil
1404 Test oil ISO4113 or {SAEJ967d}
1404 Test oil ISO4113 or {SAEJ967d}
Test oil temperature
degC
40
40
45
Nozzle and nozzle holder
105780-8140
Bosch type code
EF8511/9A
Nozzle
105780-0000
Bosch type code
DN12SD12T
Nozzle holder
105780-2080
Bosch type code
EF8511/9
Opening pressure
MPa
17.2
Opening pressure
kgf/cm2
175
Injection pipe
Outer diameter - inner diameter - length (mm) mm 8-3-600
Outer diameter - inner diameter - length (mm) mm 8-3-600
Overflow valve
132424-0620
Overflow valve opening pressure
kPa
157
123
191
Overflow valve opening pressure
kgf/cm2
1.6
1.25
1.95
Tester oil delivery pressure
kPa
157
157
157
Tester oil delivery pressure
kgf/cm2
1.6
1.6
1.6
Direction of rotation (viewed from drive side)
Right R
Right R
Injection timing adjustment
Direction of rotation (viewed from drive side)
Right R
Right R
Injection order
1-4-2-6-
3-5
Pre-stroke
mm
3.9
3.85
3.95
Beginning of injection position
Drive side NO.1
Drive side NO.1
Difference between angles 1
Cal 1-4 deg. 60 59.5 60.5
Cal 1-4 deg. 60 59.5 60.5
Difference between angles 2
Cyl.1-2 deg. 120 119.5 120.5
Cyl.1-2 deg. 120 119.5 120.5
Difference between angles 3
Cal 1-6 deg. 180 179.5 180.5
Cal 1-6 deg. 180 179.5 180.5
Difference between angles 4
Cal 1-3 deg. 240 239.5 240.5
Cal 1-3 deg. 240 239.5 240.5
Difference between angles 5
Cal 1-5 deg. 300 299.5 300.5
Cal 1-5 deg. 300 299.5 300.5
Injection quantity adjustment
Adjusting point
A
Rack position
10.8
Pump speed
r/min
600
600
600
Average injection quantity
mm3/st.
159.5
157.5
161.5
Max. variation between cylinders
%
0
-4
4
Basic
*
Fixing the lever
*
Boost pressure
kPa
34.7
34.7
Boost pressure
mmHg
260
260
Injection quantity adjustment_02
Adjusting point
C
Rack position
6.2+-0.5
Pump speed
r/min
260
260
260
Average injection quantity
mm3/st.
14
12.7
15.3
Max. variation between cylinders
%
0
-10
10
Fixing the rack
*
Boost pressure
kPa
0
0
0
Boost pressure
mmHg
0
0
0
Injection quantity adjustment_03
Adjusting point
D
Rack position
9.5
Pump speed
r/min
400
400
400
Average injection quantity
mm3/st.
125
122
128
Fixing the lever
*
Boost pressure
kPa
0
0
0
Boost pressure
mmHg
0
0
0
Boost compensator adjustment
Pump speed
r/min
400
400
400
Rack position
9.5
Boost pressure
kPa
5.3
5.3
Boost pressure
mmHg
40
40
Boost compensator adjustment_02
Pump speed
r/min
400
400
400
Rack position
10.3
Boost pressure
kPa
16
14.7
17.3
Boost pressure
mmHg
120
110
130
Boost compensator adjustment_03
Pump speed
r/min
400
400
400
Rack position
10.8
Boost pressure
kPa
21.3
21.3
21.3
Boost pressure
mmHg
160
160
160
Timer adjustment
Pump speed
r/min
750--
Advance angle
deg.
0
0
0
Remarks
Start
Start
Timer adjustment_02
Pump speed
r/min
700
Advance angle
deg.
0.5
Timer adjustment_03
Pump speed
r/min
1050
Advance angle
deg.
1
0.5
1.5
Remarks
Finish
Finish
Test data Ex:
Governor adjustment
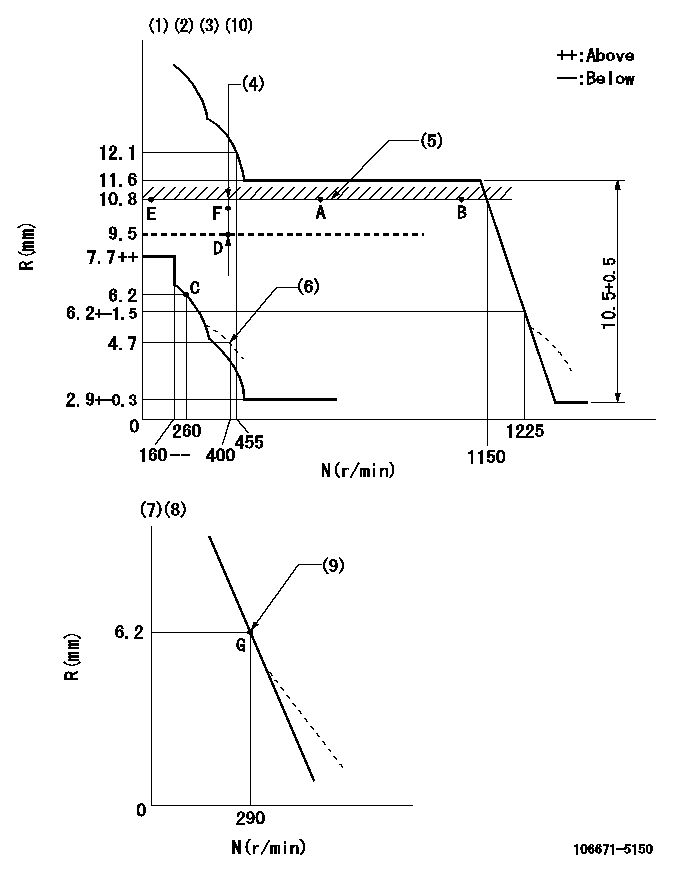
N:Pump speed
R:Rack position (mm)
(1)Lever ratio: RT
(2)Target shim dimension: TH
(3)Tolerance for racks not indicated: +-0.05mm.
(4)Boost compensator stroke: BCL
(5)Rack limit using stop lever
(6)Damper spring setting
(7)Variable speed specification: idling adjustment
(8)Fix the lever at the full-load position at delivery.
(9)Main spring setting
(10)Perform governor adjustment at an ambient temperature of at least 15 deg C (boost compensator start spring is shape memory alloy).
----------
RT=1 TH=2.2mm BCL=1.3+-0.1mm
----------
----------
RT=1 TH=2.2mm BCL=1.3+-0.1mm
----------
Speed control lever angle

F:Full speed
I:Idle
(1)Pump speed = aa
(2)Set the stopper bolt (fixed at full-load position at delivery.)
----------
aa=290r/min
----------
a=16deg+-5deg b=6deg+-5deg
----------
aa=290r/min
----------
a=16deg+-5deg b=6deg+-5deg
0000000901

F:Full load
I:Idle
(1)Stopper bolt setting
(2)Use the hole at R = aa
----------
aa=42mm
----------
a=32deg+-3deg b=45deg+-5deg
----------
aa=42mm
----------
a=32deg+-3deg b=45deg+-5deg
Stop lever angle

N:Pump normal
S:Stop the pump.
(1)Rack position = aa
----------
aa=10.8mm
----------
a=32deg+-5deg b=32deg+-5deg
----------
aa=10.8mm
----------
a=32deg+-5deg b=32deg+-5deg
0000001501 ACS

(A) Set screw
1. Aneroid compensator unit adjustment
Screw in (A) to obtain L1.
2. Adjustment following governor installation
(1)Set the speed of the pump to N1 r/min and fix the control lever at the full set position.
(2)Screw in the aneroid compensator to obtain the performance shown in the graph above.
----------
N1=1050r/min L1=(0.1~0.5)mm
----------
R1=10.8mm R2=(9.5)mm P1=(74.5)+-2.7kPa((559)+-20mmHg) P2=57.5+-0.7 kPa(431+-5mmHg) Q1=(158.5)+-3cm3/1000st Q2=124+-3cm3/1000st
----------
N1=1050r/min L1=(0.1~0.5)mm
----------
R1=10.8mm R2=(9.5)mm P1=(74.5)+-2.7kPa((559)+-20mmHg) P2=57.5+-0.7 kPa(431+-5mmHg) Q1=(158.5)+-3cm3/1000st Q2=124+-3cm3/1000st
Timing setting

(1)Pump vertical direction
(2)Coupling's key groove position at No 1 cylinder's beginning of injection
(3)-
(4)-
----------
----------
a=(20deg)
----------
----------
a=(20deg)
Information:
Example of Pulse Width Modulation SignalsRated Fuel Position("Rated Fuel Pos" on ECAP) - this indicates the maximum allowable fuel position (longest injection pulse). It will produce rated power for this engine configuration.Reference VoltageA regulated voltage supplied by the ECM to a sensor. The reference voltage is used by the sensor to generate a signal voltage.Remote Mounted Throttle Position SensorThis sensor measures pedal position and sends a signal to the ECM. The sensor is mounted off of the throttle pedal assembly, usually near the fire wall in the engine compartment (not the cab). The throttle pedal is connected through an adjustable linkage to this pedal. See Pedal Mounted Throttle Position Sensor.Retarder Enable SignalThe retarder enable signal interfaces the ECM to the engine retarder. This will prohibit operation of the engine brake during undesirable engine operating conditions (such as while the engine is being fueled).SensorA device used to detect and convert a change in pressure, temperature, or mechanical movement into an electrical signal.Service Program ModuleA software program on a factory programmable computer chip, designed to adapt an ECAP or DDT to a specific application.Short CircuitA condition where an electrical circuit is unintentionally connected to an undesirable point. Example: a wire which rubs against a vehicle frame until it wears off its insulation and makes electrical contact with the frame.SignalA voltage or waveform used to transmit information typically from a sensor to the ECM.Speed "burp"A sudden brief change in engine speed.SubsystemAs used here, it is a part of the 3176 System that relates to a particular function, for instance: throttle subsystem, etc.Supply VoltageA constant voltage supplied to a component to provide electrical power for its operation. It may be generated by the ECM, or it may be vehicle battery voltage supplied by the vehicle wiring. "T" HarnessA test harness designed to permit normal circuit operation while measuring voltages, typically inserted between the two ends of a connector.Throttle PositionThe ECM's interpretation of the signal from the Throttle Position Sensor.Throttle Position SensorAn electronic sensor which is connected to the accelerator pedal and sends a Pulse Width Modulated signal to the ECM.Total TattletaleTotal number of changes to all Customer Specified Parameters.TransducerA device which converts a mechanical signal to an electrical signalTransducer ModuleA sealed unit mounted mounted on one end of the ECM, which contains the Boost Pressure Sensor and Atmospheric Pressure Sensor (if equipped), and protective signal conditioning circuitry.Vehicle Speed BufferA device used to condition and amplify the output of the vehicle speed sensor.Vehicle Speed SensorAn electromagnetic pickup that measures vehicle speed from the rotation of gear teeth in the drive train of the vehicle.Warning LampUsed to warn the operator of the presence of a Caterpillar Engine Protection detected problem.
Have questions with 106671-5150?
Group cross 106671-5150 ZEXEL
Nissan-Diesel
Nissan-Diesel
Nissan-Diesel
Nissan-Diesel
Nissan-Diesel
106671-5150
INJECTION-PUMP ASSEMBLY