Information injection-pump assembly
ZEXEL
106671-3980
1066713980
HINO
220005250A
220005250a
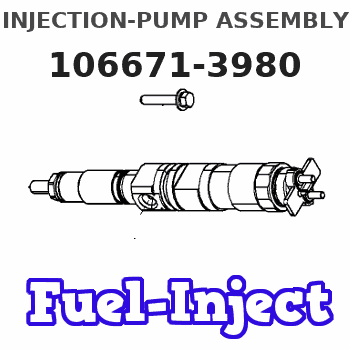
Rating:
Service parts 106671-3980 INJECTION-PUMP ASSEMBLY:
1.
_
7.
COUPLING PLATE
8.
_
9.
_
11.
Nozzle and Holder
23600-1221A
12.
Open Pre:MPa(Kqf/cm2)
21.6{220}
15.
NOZZLE SET
Include in #1:
106671-3980
as INJECTION-PUMP ASSEMBLY
Cross reference number
ZEXEL
106671-3980
1066713980
HINO
220005250A
220005250a
Zexel num
Bosch num
Firm num
Name
Calibration Data:
Adjustment conditions
Test oil
1404 Test oil ISO4113 or {SAEJ967d}
1404 Test oil ISO4113 or {SAEJ967d}
Test oil temperature
degC
40
40
45
Nozzle and nozzle holder
105780-8140
Bosch type code
EF8511/9A
Nozzle
105780-0000
Bosch type code
DN12SD12T
Nozzle holder
105780-2080
Bosch type code
EF8511/9
Opening pressure
MPa
17.2
Opening pressure
kgf/cm2
175
Injection pipe
Outer diameter - inner diameter - length (mm) mm 8-3-600
Outer diameter - inner diameter - length (mm) mm 8-3-600
Overflow valve
134424-0920
Overflow valve opening pressure
kPa
162
147
177
Overflow valve opening pressure
kgf/cm2
1.65
1.5
1.8
Tester oil delivery pressure
kPa
157
157
157
Tester oil delivery pressure
kgf/cm2
1.6
1.6
1.6
Direction of rotation (viewed from drive side)
Left L
Left L
Injection timing adjustment
Direction of rotation (viewed from drive side)
Left L
Left L
Injection order
1-4-2-6-
3-5
Pre-stroke
mm
3.3
3.24
3.3
Beginning of injection position
Drive side NO.1
Drive side NO.1
Difference between angles 1
Cal 1-4 deg. 60 59.75 60.25
Cal 1-4 deg. 60 59.75 60.25
Difference between angles 2
Cyl.1-2 deg. 120 119.75 120.25
Cyl.1-2 deg. 120 119.75 120.25
Difference between angles 3
Cal 1-6 deg. 180 179.75 180.25
Cal 1-6 deg. 180 179.75 180.25
Difference between angles 4
Cal 1-3 deg. 240 239.75 240.25
Cal 1-3 deg. 240 239.75 240.25
Difference between angles 5
Cal 1-5 deg. 300 299.75 300.25
Cal 1-5 deg. 300 299.75 300.25
Injection quantity adjustment
Adjusting point
A
Rack position
10.6
Pump speed
r/min
500
500
500
Average injection quantity
mm3/st.
129
126
132
Max. variation between cylinders
%
0
-4
4
Fixing the lever
*
Injection quantity adjustment_02
Adjusting point
B
Rack position
10.9
Pump speed
r/min
700
700
700
Average injection quantity
mm3/st.
139.5
137.5
141.5
Max. variation between cylinders
%
0
-2
2
Basic
*
Fixing the lever
*
Injection quantity adjustment_03
Adjusting point
C
Rack position
11.4
Pump speed
r/min
1150
1150
1150
Average injection quantity
mm3/st.
148
145
151
Max. variation between cylinders
%
0
-4
4
Fixing the lever
*
Injection quantity adjustment_04
Adjusting point
D
Rack position
7+-0.5
Pump speed
r/min
225
225
225
Average injection quantity
mm3/st.
15
12
18
Max. variation between cylinders
%
0
-15
15
Fixing the rack
*
Injection quantity adjustment_05
Adjusting point
E
Rack position
-
Pump speed
r/min
100
100
100
Average injection quantity
mm3/st.
126.3
119.3
133.3
Fixing the lever
*
Timer adjustment
Pump speed
r/min
950
Advance angle
deg.
0.5
Timer adjustment_02
Pump speed
r/min
1000
Advance angle
deg.
1.5
Timer adjustment_03
Pump speed
r/min
1050
Advance angle
deg.
1.9
1.4
2.4
Timer adjustment_04
Pump speed
r/min
1150
Advance angle
deg.
4.5
4.2
4.8
Remarks
Finish
Finish
Test data Ex:
Governor adjustment
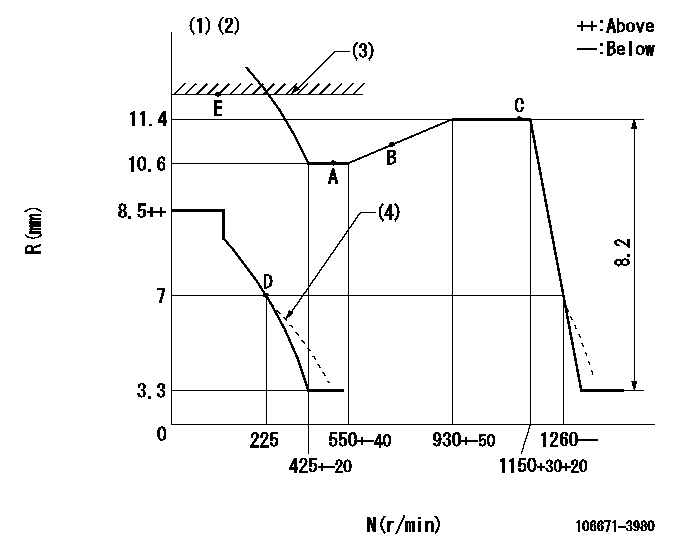
N:Pump speed
R:Rack position (mm)
(1)Lever ratio: RT
(2)Target shim dimension: TH
(3)RACK LIMIT
(4)Damper spring setting: DL
----------
RT=1 TH=2.2mm DL=6.2-0.2mm
----------
----------
RT=1 TH=2.2mm DL=6.2-0.2mm
----------
Speed control lever angle

F:Full speed
----------
----------
a=3deg+-5deg
----------
----------
a=3deg+-5deg
0000000901

F:Full load
I:Idle
(1)Stopper bolt setting
----------
----------
a=10deg+-5deg b=27.5deg+-3deg
----------
----------
a=10deg+-5deg b=27.5deg+-3deg
Stop lever angle

N:Pump normal
S:Stop the pump.
----------
----------
a=15deg+-5deg b=64deg+-5deg
----------
----------
a=15deg+-5deg b=64deg+-5deg
0000001501 GOVERNOR TORQUE CONTROL

Dr:Torque control stroke
(A): Without torque control spring capsule
1. Adjustment procedures
(1)Procedure is the same as that for the RFD (former type), except that the positive torque control stroke must be determined at the full lever setting.
2. Procedures for adjustment
(1)Remove the torque control spring capsule.
(2)Operate the pump at approximately N1. (End of idling spring operation < N1.)
(3)Tilt the lever to the full side.
(4)Set so that R = RF.
(5)Increase the speed by pushing in the screw (attached to the bracket on the rear of the tension lever) through the adjusting window.
(6)Adjust so that the torque control stroke Dr1 can be obtained.
(7)Align N2 and N3 with the torque control spring capsule.
3. Final confirmation
(1)After final confirmation, temporarily set the load lever to N = N1, R = idling position.
(2)From this condition, increase speed to N = N4.
(3)Confirm that positive torque control stroke is Dr2.
----------
N1=500r/min N2=550+-40r/min N3=930+-50r/min N4=1000r/min RF=10.6mm Dr1=0.8mm Dr2=0+0.3mm
----------
----------
N1=500r/min N2=550+-40r/min N3=930+-50r/min N4=1000r/min RF=10.6mm Dr1=0.8mm Dr2=0+0.3mm
----------
Timing setting

(1)Pump vertical direction
(2)Coupling's key groove position at No 1 cylinder's beginning of injection
(3)-
(4)-
----------
----------
a=(0deg)
----------
----------
a=(0deg)
Information:
Fuel and the Effect from Cold Weather
The two types of diesel fuel available for your truck engine are typically grades No. 1 and No. 2. Although No. 2 diesel fuel is the most commonly used fuel, No. 1 diesel fuel or a blend of No. 1 and No. 2, is the fuel that is best suited for cold weather operation.During cold weather operation, it may be necessary for you to use No. 2 diesel fuel since quantities of No. 1 diesel fuel are limited and generally are only available during the winter months and in the colder climates.There are three major differences between No. 1 and No. 2 diesel fuel. No. 1 diesel fuel has a lower cloud point, a lower pour point and has a lower BTU (kJ) (heat content) rating per unit volume of fuel than the average No. 2 diesel fuel.When using No. 1 diesel fuel, you may notice a drop in power and fuel efficiency, but should not experience any other operating effects.The cloud point is the temperature at which a cloud or haze of wax crystals will begin to form in the fuel and cause fuel filters to plug. The pour point is the temperature which diesel fuel will begin to thicken and be more resistant to flow through fuel pumps and lines.Be aware of these fuel values when purchasing your diesel fuel and anticipate the average outside (ambient) temperature for the area your engine will be operating. Engines fueled in one climate may not operate satisfactorily if moved to another because of problems that result from cold weather.Before troubleshooting for low power or poor performance in winter months, check the type of fuel being used.The use of starting aids, engine oil pan heaters, engine coolant heaters, fuel heaters and fuel line insulation also provide a means of minimizing starting and fuel problems in cold weather when No. 2 diesel fuel is used.Fuel Related Components in Cold Weather
ECM Fuel Cooling
Fuel Cooled Electronic ECMThe electronic control module (ECM) is fuel cooled. Fuel is routed from the tank, to a primary fuel filter, through the transfer pump, then through cored passages in the electronic control module housing, on to the secondary fuel filter, and finally to the injection pump.Inlet fuel temperature to the transfer pump must never exceed 149°F (65°C). Fuel temperatures in excess of this temperature reduce the life of the electronics, reduce the life of the transfer pump check valves, and reduce engine power availability.Fuel Tanks
Fuel tanks should contain some provision for draining water and sediment from the bottom of the tanks.Some fuel tanks use supply pipes that allow water and sediment to settle below the end of the fuel supply pipe. This water and sediment should be drained at each oil change.Some fuel tanks use supply lines that take fuel directly from the bottom of the tank. If equipped with this system, regular maintenance of the fuel system filter(s) is important.Fuel Heaters
Fuel heaters prevent plugging of the fuel filters in cold weather
The two types of diesel fuel available for your truck engine are typically grades No. 1 and No. 2. Although No. 2 diesel fuel is the most commonly used fuel, No. 1 diesel fuel or a blend of No. 1 and No. 2, is the fuel that is best suited for cold weather operation.During cold weather operation, it may be necessary for you to use No. 2 diesel fuel since quantities of No. 1 diesel fuel are limited and generally are only available during the winter months and in the colder climates.There are three major differences between No. 1 and No. 2 diesel fuel. No. 1 diesel fuel has a lower cloud point, a lower pour point and has a lower BTU (kJ) (heat content) rating per unit volume of fuel than the average No. 2 diesel fuel.When using No. 1 diesel fuel, you may notice a drop in power and fuel efficiency, but should not experience any other operating effects.The cloud point is the temperature at which a cloud or haze of wax crystals will begin to form in the fuel and cause fuel filters to plug. The pour point is the temperature which diesel fuel will begin to thicken and be more resistant to flow through fuel pumps and lines.Be aware of these fuel values when purchasing your diesel fuel and anticipate the average outside (ambient) temperature for the area your engine will be operating. Engines fueled in one climate may not operate satisfactorily if moved to another because of problems that result from cold weather.Before troubleshooting for low power or poor performance in winter months, check the type of fuel being used.The use of starting aids, engine oil pan heaters, engine coolant heaters, fuel heaters and fuel line insulation also provide a means of minimizing starting and fuel problems in cold weather when No. 2 diesel fuel is used.Fuel Related Components in Cold Weather
ECM Fuel Cooling
Fuel Cooled Electronic ECMThe electronic control module (ECM) is fuel cooled. Fuel is routed from the tank, to a primary fuel filter, through the transfer pump, then through cored passages in the electronic control module housing, on to the secondary fuel filter, and finally to the injection pump.Inlet fuel temperature to the transfer pump must never exceed 149°F (65°C). Fuel temperatures in excess of this temperature reduce the life of the electronics, reduce the life of the transfer pump check valves, and reduce engine power availability.Fuel Tanks
Fuel tanks should contain some provision for draining water and sediment from the bottom of the tanks.Some fuel tanks use supply pipes that allow water and sediment to settle below the end of the fuel supply pipe. This water and sediment should be drained at each oil change.Some fuel tanks use supply lines that take fuel directly from the bottom of the tank. If equipped with this system, regular maintenance of the fuel system filter(s) is important.Fuel Heaters
Fuel heaters prevent plugging of the fuel filters in cold weather