Information injection-pump assembly
BOSCH
9 400 610 838
9400610838
ZEXEL
106671-3387
1066713387
HINO
220004081A
220004081a
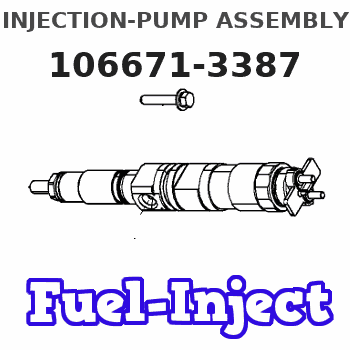
Rating:
Service parts 106671-3387 INJECTION-PUMP ASSEMBLY:
1.
_
7.
COUPLING PLATE
8.
_
9.
_
11.
Nozzle and Holder
23600-1221A
12.
Open Pre:MPa(Kqf/cm2)
21.6{220}
15.
NOZZLE SET
Include in #1:
106671-3387
as INJECTION-PUMP ASSEMBLY
Cross reference number
BOSCH
9 400 610 838
9400610838
ZEXEL
106671-3387
1066713387
HINO
220004081A
220004081a
Zexel num
Bosch num
Firm num
Name
106671-3387
9 400 610 838
220004081A HINO
INJECTION-PUMP ASSEMBLY
EK100 K 14CA INJECTION PUMP ASSY PE6P,6PD PE
EK100 K 14CA INJECTION PUMP ASSY PE6P,6PD PE
Calibration Data:
Adjustment conditions
Test oil
1404 Test oil ISO4113 or {SAEJ967d]
1404 Test oil ISO4113 or {SAEJ967d]
Test oil temperature
degC
40
40
45
Nozzle and nozzle holder
105780-8140
Bosch type code
EF8511/9A
Nozzle
105780-0000
Bosch type code
DN12SD12T
Nozzle holder
105780-2080
Bosch type code
EF8511/9
Opening pressure
MPa
17.2
Opening pressure
kgf/cm2
175
Injection pipe
Outer diameter - inner diameter - length (mm) mm 8-3-600
Outer diameter - inner diameter - length (mm) mm 8-3-600
Overflow valve
134424-0920
Overflow valve opening pressure
kPa
162
147
177
Overflow valve opening pressure
kgf/cm2
1.65
1.5
1.8
Tester oil delivery pressure
kPa
157
157
157
Tester oil delivery pressure
kgf/cm2
1.6
1.6
1.6
Direction of rotation (viewed from drive side)
Left L
Left L
Injection timing adjustment
Direction of rotation (viewed from drive side)
Left L
Left L
Injection order
1-4-2-6-
3-5
Pre-stroke
mm
3.3
3.24
3.3
Beginning of injection position
Drive side NO.1
Drive side NO.1
Difference between angles 1
Cal 1-4 deg. 60 59.75 60.25
Cal 1-4 deg. 60 59.75 60.25
Difference between angles 2
Cyl.1-2 deg. 120 119.75 120.25
Cyl.1-2 deg. 120 119.75 120.25
Difference between angles 3
Cal 1-6 deg. 180 179.75 180.25
Cal 1-6 deg. 180 179.75 180.25
Difference between angles 4
Cal 1-3 deg. 240 239.75 240.25
Cal 1-3 deg. 240 239.75 240.25
Difference between angles 5
Cal 1-5 deg. 300 299.75 300.25
Cal 1-5 deg. 300 299.75 300.25
Injection quantity adjustment
Adjusting point
A
Rack position
10.6
Pump speed
r/min
500
500
500
Average injection quantity
mm3/st.
129
126
132
Max. variation between cylinders
%
0
-4
4
Fixing the lever
*
Injection quantity adjustment_02
Adjusting point
B
Rack position
10.9
Pump speed
r/min
700
700
700
Average injection quantity
mm3/st.
139.5
137.5
141.5
Max. variation between cylinders
%
0
-2
2
Basic
*
Fixing the lever
*
Injection quantity adjustment_03
Adjusting point
C
Rack position
11.4
Pump speed
r/min
1150
1150
1150
Average injection quantity
mm3/st.
148
145
151
Max. variation between cylinders
%
0
-4
4
Fixing the lever
*
Injection quantity adjustment_04
Adjusting point
D
Rack position
7+-0.5
Pump speed
r/min
225
225
225
Average injection quantity
mm3/st.
15
12
18
Max. variation between cylinders
%
0
-15
15
Fixing the rack
*
Injection quantity adjustment_05
Adjusting point
E
Rack position
-
Pump speed
r/min
100
100
100
Average injection quantity
mm3/st.
126.3
119.3
133.3
Fixing the lever
*
Rack limit
*
Timer adjustment
Pump speed
r/min
950
Advance angle
deg.
0.5
Timer adjustment_02
Pump speed
r/min
1000
Advance angle
deg.
1.5
Timer adjustment_03
Pump speed
r/min
1050
Advance angle
deg.
1.9
1.4
2.4
Timer adjustment_04
Pump speed
r/min
1150
Advance angle
deg.
4.5
4.2
4.8
Remarks
Finish
Finish
Test data Ex:
Governor adjustment
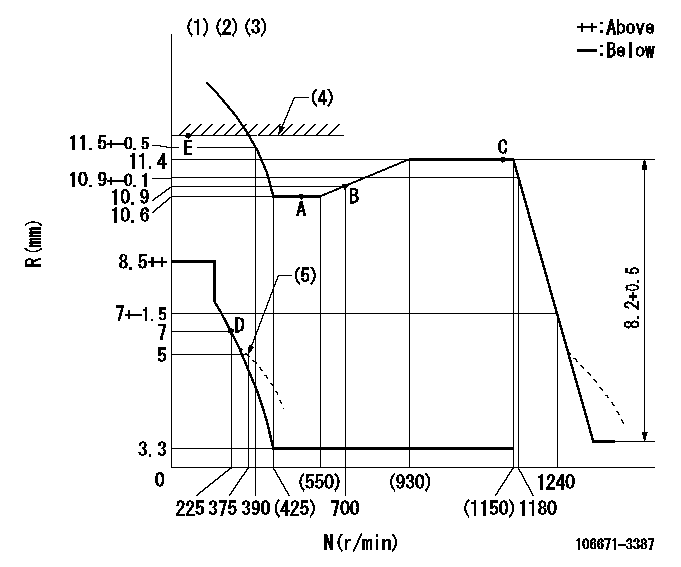
N:Pump speed
R:Rack position (mm)
(1)Lever ratio: RT
(2)Target shim dimension: TH
(3)Tolerance for racks not indicated: +-0.05mm.
(4)RACK LIMIT
(5)Damper spring setting
----------
RT=1 TH=2.2mm
----------
----------
RT=1 TH=2.2mm
----------
Speed control lever angle

F:Full speed
----------
----------
a=3deg+-5deg
----------
----------
a=3deg+-5deg
0000000901

F:Full load
I:Idle
(1)Stopper bolt setting
----------
----------
a=10deg+-5deg b=27deg+-3deg
----------
----------
a=10deg+-5deg b=27deg+-3deg
Stop lever angle
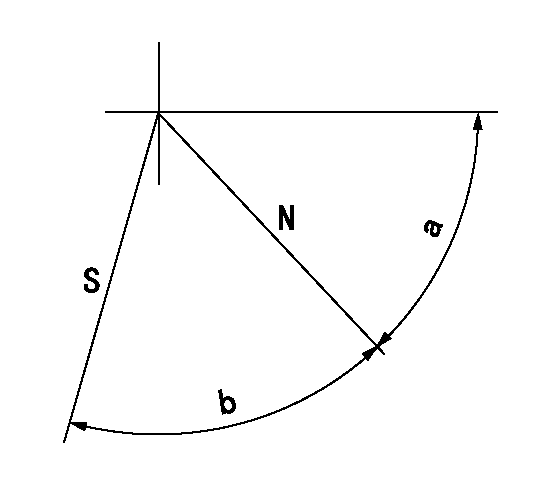
N:Pump normal
S:Stop the pump.
----------
----------
a=40deg+-5deg b=64deg+-5deg
----------
----------
a=40deg+-5deg b=64deg+-5deg
0000001501 GOVERNOR TORQUE CONTROL

Dr:Torque control stroke
(A): Without torque control spring capsule
1. Adjustment procedures
(1)Procedure is the same as that for the RFD (former type), except that the positive torque control stroke must be determined at the full lever setting.
2. Procedures for adjustment
(1)Remove the torque control spring capsule.
(2)Operate the pump at approximately N1. (End of idling spring operation < N1.)
(3)Tilt the lever to the full side.
(4)Set so that R = RF.
(5)Increase the speed by pushing in the screw (attached to the bracket on the rear of the tension lever) through the adjusting window.
(6)Adjust so that the torque control stroke Dr1 can be obtained.
(7)Align N2 and N3 with the torque control spring capsule.
3. Final confirmation
(1)After final confirmation, temporarily set the load lever to N = N1, R = idling position.
(2)From this condition, increase speed to N = N4.
(3)Confirm that positive torque control stroke is Dr2.
----------
N1=500r/min N2=(550)r/min N3=(930)r/min N4=1000r/min RF=10.6mm Dr1=0.8mm Dr2=0+0.3mm
----------
----------
N1=500r/min N2=(550)r/min N3=(930)r/min N4=1000r/min RF=10.6mm Dr1=0.8mm Dr2=0+0.3mm
----------
Timing setting

(1)Pump vertical direction
(2)Coupling's key groove position at No 1 cylinder's beginning of injection
(3)-
(4)-
----------
----------
a=(0deg)
----------
----------
a=(0deg)
Information:
2. Maintain the oil level to the FULL mark (between the ADD and FULL RANGE zone) on the ENGINE STOPPED WITH OIL COLD side of the dipstick. Do not fill the crankcase above the FULL RANGE zone.3. Remove oil fill cap and add oil if necessary. DO NOT fill the crankcase above the FULL mark on the dipstick.
Do NOT overfill to reach above or to the top of the FULL mark on the dipstick.
Operating your engine when the oil level is above the FULL Range zone could cause your crankshaft to dip into the oil. If this occurs during engine operation, it could result in a loss of power and a possible alarm from high crankcase pressure. Remote mounted or auxiliary filters require additional oil. For all information pertaining to auxiliary filters, refer to the OEM or filter manufacturer's recommendations and instructions for all information regarding auxiliary oil filters.Estimating Oil Consumption
Oil consumption, along with fuel consumption and maintenance information, can be used to estimate total operating cost for your Caterpillar engine. It can also be used to estimate the capacity of a makeup oil system required to accommodate your maintenance intervals.Oil consumption is somewhat proportional to the percent load at which the engine is operating. The higher the percent load, the higher the amount of oil consumed per hour.The oil consumption rate, or BSOC (brake specific oil consumption), measure is grams/brake kW-hour (lb/bhp-hour). The BSOC varies depending on the load on your engine. The established typical mid-life BSOC values for your engine can be determined by contacting your Caterpillar dealer for assistance in determining typical oil consumption for your engine.Oil Consumption as an Overhaul Indicator
When an engine's oil consumption has risen to three times the initial (new) consumption rate due to normal wear, then the engine should be scheduled for overhaul. There may be a corresponding increase in blowby and also a slight increase in fuel consumption. Contact your Caterpillar dealer for assistance in determining typical oil consumption for your engine.Cooling System
Make sure you read and understand the information in the Safety and Cooling System Specifications sections of this manual before you proceed with maintenance of the cooling system.
Check Coolant Level
If Coolant is Low
Refer to the Cooling System Specifications section in this publication for all information pertaining to water, antifreeze and supplemental coolant additive requirements before performing this maintenance procedure.1. Stop the engine and allow the engine to cool before performing this maintenance procedure.2. Release vent valve (if equipped) slowly to relieve pressure. Remove filler cap and inspect condition of cap gasket. Replace cap if gaskets are damaged.3. Maintain the coolant level within 13 mm (1/2 inch) below the bottom of the fill pipe or to the proper level (upper half) on the sight glass (if equipped) by adding make-up coolant (antifreeze and water). Install the filler cap.4. Inspect for leaks or damaged piping. Make repairs if necessary.Air Cleaner Indicator
Typical air cleaner indicator shown.Check the service indicator (if equipped) mounted on the air cleaner. A colored piston showing
Do NOT overfill to reach above or to the top of the FULL mark on the dipstick.
Operating your engine when the oil level is above the FULL Range zone could cause your crankshaft to dip into the oil. If this occurs during engine operation, it could result in a loss of power and a possible alarm from high crankcase pressure. Remote mounted or auxiliary filters require additional oil. For all information pertaining to auxiliary filters, refer to the OEM or filter manufacturer's recommendations and instructions for all information regarding auxiliary oil filters.Estimating Oil Consumption
Oil consumption, along with fuel consumption and maintenance information, can be used to estimate total operating cost for your Caterpillar engine. It can also be used to estimate the capacity of a makeup oil system required to accommodate your maintenance intervals.Oil consumption is somewhat proportional to the percent load at which the engine is operating. The higher the percent load, the higher the amount of oil consumed per hour.The oil consumption rate, or BSOC (brake specific oil consumption), measure is grams/brake kW-hour (lb/bhp-hour). The BSOC varies depending on the load on your engine. The established typical mid-life BSOC values for your engine can be determined by contacting your Caterpillar dealer for assistance in determining typical oil consumption for your engine.Oil Consumption as an Overhaul Indicator
When an engine's oil consumption has risen to three times the initial (new) consumption rate due to normal wear, then the engine should be scheduled for overhaul. There may be a corresponding increase in blowby and also a slight increase in fuel consumption. Contact your Caterpillar dealer for assistance in determining typical oil consumption for your engine.Cooling System
Make sure you read and understand the information in the Safety and Cooling System Specifications sections of this manual before you proceed with maintenance of the cooling system.
Check Coolant Level
If Coolant is Low
Refer to the Cooling System Specifications section in this publication for all information pertaining to water, antifreeze and supplemental coolant additive requirements before performing this maintenance procedure.1. Stop the engine and allow the engine to cool before performing this maintenance procedure.2. Release vent valve (if equipped) slowly to relieve pressure. Remove filler cap and inspect condition of cap gasket. Replace cap if gaskets are damaged.3. Maintain the coolant level within 13 mm (1/2 inch) below the bottom of the fill pipe or to the proper level (upper half) on the sight glass (if equipped) by adding make-up coolant (antifreeze and water). Install the filler cap.4. Inspect for leaks or damaged piping. Make repairs if necessary.Air Cleaner Indicator
Typical air cleaner indicator shown.Check the service indicator (if equipped) mounted on the air cleaner. A colored piston showing
Have questions with 106671-3387?
Group cross 106671-3387 ZEXEL
Hino
106671-3387
9 400 610 838
220004081A
INJECTION-PUMP ASSEMBLY
EK100
EK100