Information injection-pump assembly
ZEXEL
106671-3180
1066713180
HINO
220001490C
220001490c
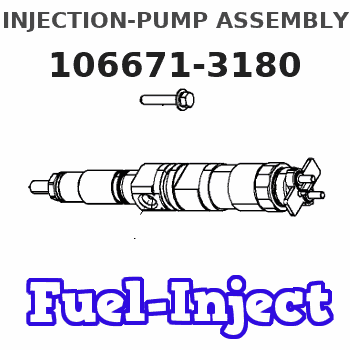
Rating:
Service parts 106671-3180 INJECTION-PUMP ASSEMBLY:
1.
_
7.
COUPLING PLATE
8.
_
9.
_
11.
Nozzle and Holder
23600-1024
12.
Open Pre:MPa(Kqf/cm2)
21.6{220}
15.
NOZZLE SET
Include in #1:
106671-3180
as INJECTION-PUMP ASSEMBLY
Cross reference number
ZEXEL
106671-3180
1066713180
HINO
220001490C
220001490c
Zexel num
Bosch num
Firm num
Name
106671-3180
220001490C HINO
INJECTION-PUMP ASSEMBLY
EK100 *
EK100 *
Calibration Data:
Adjustment conditions
Test oil
1404 Test oil ISO4113 or {SAEJ967d}
1404 Test oil ISO4113 or {SAEJ967d}
Test oil temperature
degC
40
40
45
Nozzle and nozzle holder
105780-8140
Bosch type code
EF8511/9A
Nozzle
105780-0000
Bosch type code
DN12SD12T
Nozzle holder
105780-2080
Bosch type code
EF8511/9
Opening pressure
MPa
17.2
Opening pressure
kgf/cm2
175
Injection pipe
Outer diameter - inner diameter - length (mm) mm 8-3-600
Outer diameter - inner diameter - length (mm) mm 8-3-600
Overflow valve
134424-0620
Overflow valve opening pressure
kPa
162
147
177
Overflow valve opening pressure
kgf/cm2
1.65
1.5
1.8
Tester oil delivery pressure
kPa
157
157
157
Tester oil delivery pressure
kgf/cm2
1.6
1.6
1.6
Direction of rotation (viewed from drive side)
Left L
Left L
Injection timing adjustment
Direction of rotation (viewed from drive side)
Left L
Left L
Injection order
1-4-2-6-
3-5
Pre-stroke
mm
3.3
3.2
3.3
Beginning of injection position
Drive side NO.1
Drive side NO.1
Difference between angles 1
Cal 1-4 deg. 60 59.5 60.5
Cal 1-4 deg. 60 59.5 60.5
Difference between angles 2
Cyl.1-2 deg. 120 119.5 120.5
Cyl.1-2 deg. 120 119.5 120.5
Difference between angles 3
Cal 1-6 deg. 180 179.5 180.5
Cal 1-6 deg. 180 179.5 180.5
Difference between angles 4
Cal 1-3 deg. 240 239.5 240.5
Cal 1-3 deg. 240 239.5 240.5
Difference between angles 5
Cal 1-5 deg. 300 299.5 300.5
Cal 1-5 deg. 300 299.5 300.5
Injection quantity adjustment
Adjusting point
A
Rack position
9.7
Pump speed
r/min
500
500
500
Average injection quantity
mm3/st.
126
123
129
Max. variation between cylinders
%
0
-4
4
Fixing the lever
*
Injection quantity adjustment_02
Adjusting point
B
Rack position
10.3
Pump speed
r/min
700
700
700
Average injection quantity
mm3/st.
142.5
140.5
144.5
Max. variation between cylinders
%
0
-2
2
Basic
*
Fixing the lever
*
Injection quantity adjustment_03
Adjusting point
C
Rack position
10.8
Pump speed
r/min
1150
1150
1150
Average injection quantity
mm3/st.
155
152
158
Max. variation between cylinders
%
0
-4
4
Fixing the lever
*
Injection quantity adjustment_04
Adjusting point
D
Rack position
5.1+-0.5
Pump speed
r/min
225
225
225
Average injection quantity
mm3/st.
16
13
19
Max. variation between cylinders
%
0
-15
15
Fixing the rack
*
Injection quantity adjustment_05
Adjusting point
E
Rack position
11+-0.5
Pump speed
r/min
100
100
100
Average injection quantity
mm3/st.
125
125
145
Fixing the lever
*
Timer adjustment
Pump speed
r/min
700+-50
Advance angle
deg.
0
0
0
Remarks
Start
Start
Timer adjustment_02
Pump speed
r/min
900
Advance angle
deg.
1.4
0.9
1.9
Timer adjustment_03
Pump speed
r/min
1150
Advance angle
deg.
4
3.5
4.5
Remarks
Finish
Finish
Test data Ex:
Governor adjustment
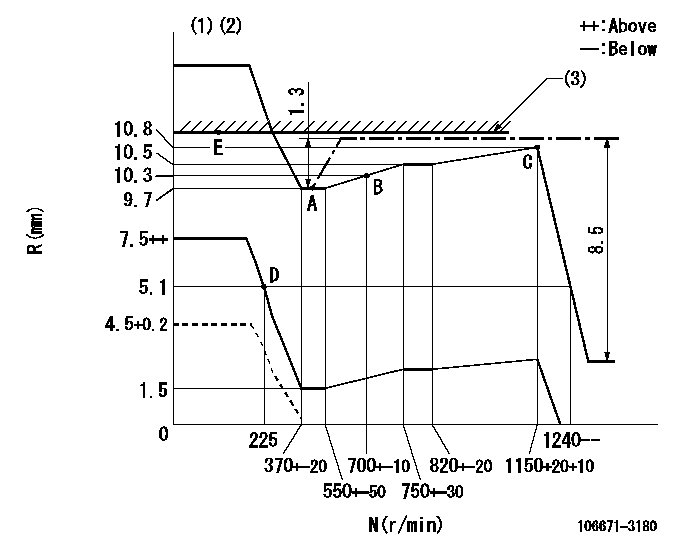
N:Pump speed
R:Rack position (mm)
(1)Set the load lever's stop position so that R = aa (N = 0).
(2)Beginning of damper spring operation: DL
(3)RACK LIMIT
----------
aa=4.5+0.2mm DL=4.8-0.2mm
----------
----------
aa=4.5+0.2mm DL=4.8-0.2mm
----------
Speed control lever angle

F:Full speed
----------
----------
a=15deg+-5deg
----------
----------
a=15deg+-5deg
0000000901

F:Full load
I:Idle
S:Stop
----------
----------
a=10deg+-5deg b=29deg+-3deg c=14deg+-3deg
----------
----------
a=10deg+-5deg b=29deg+-3deg c=14deg+-3deg
0000001501 MICRO SWITCH
Switch adjustment
Adjust the bolt so that the lower lever position is obtained when the switch is turned ON.
(1)Speed N1
(2)Rack position Ra
----------
N1=325-25r/min Ra=5.1mm
----------
----------
N1=325-25r/min Ra=5.1mm
----------
Information:
Startability will be improved at temperatures below +32°F (0°C) by the use of a starting aid and/or use of a cylinder block coolant heater or other means to heat the crankcase oil.Start the engine using the following procedure:1. Place the transmission in NEUTRAL and disengage the flywheel clutch (if equipped) to remove the transmission drag and prevent movement of the truck. Depressing the clutch in cold weather can mean the difference between starting and not starting. Depressing the clutch in warm weather produces faster starts and reduces battery drain.2. Turn the ignition switch to the ON position and push the crank button or turn the ignition switch to the START position. Crank the engine. (At temperatures below +32°F (0°C), it may be necessary to spray starting fluid into the air cleaner inlet.) DO NOT PUSH DOWN OR HOLD THE THROTTLE DOWN while cranking the engine. The 3176 system will automatically provide the correct amount of fuel to start the engine. The engine may need to crank slightly longer than a mechanically governed engine, because some oil pressure is required for the electronic actuator to move the rack. The "CHECK ENGINE" light should beON while the engine is cranking, but should go OFF after the engine starts and operating oil pressure is achieved.If the engine fails to start in 30 seconds, release the starter switch and wait two minutes to allow the starter motor to cool before using it again.
When using starting fluid, follow the manufacturer's instructions carefully, use it sparingly and spray it only while cranking the engine. Also, do not store starting fluid containers in the cab. Failure todo so, could result in an explosion and/or fire and possible personal injury.
Excessive ether can cause piston and ring damage. Use ether for cold starting purposes only.
3. As soon as the engine starts, allow the engine to idle for two or three minutes, or until the water temperature gauge indicator has begun to rise.4. Do not apply load to the engine or increase engine speed until the oil pressure gauge indicates normal. Oil pressure should rise within 15 seconds after the engine starts.5. Operate the engine at low load until all systems reach operating temperature. Check all gauges during the warm-up period.Starting With Jumper Cables
Batteries give off flammable fumes that can explode.Improper jumper cable connections can cause an explosion resulting in personal injury.Prevent sparks near the batteries. Sparks could cause vapors to explode. Do not allow jumper cable ends to contact each other or the engine.Do not smoke when observing the battery electrolyte levels.Always wear protective glasses when working with batteries.Electrolyte is an acid and can cause personal injury if it contacts skin or eyes.
Engines installed without engine-to-frame ground straps can be damaged by electrical discharge.To prevent electrical discharge damage, check to make sure the engine's electrical system has an engine-to-frame ground strap. For engines which have the alternator connected to an engine component, the ground strap must connect that component to thframe.Some engines have starter-to-frame ground straps.
When using starting fluid, follow the manufacturer's instructions carefully, use it sparingly and spray it only while cranking the engine. Also, do not store starting fluid containers in the cab. Failure todo so, could result in an explosion and/or fire and possible personal injury.
Excessive ether can cause piston and ring damage. Use ether for cold starting purposes only.
3. As soon as the engine starts, allow the engine to idle for two or three minutes, or until the water temperature gauge indicator has begun to rise.4. Do not apply load to the engine or increase engine speed until the oil pressure gauge indicates normal. Oil pressure should rise within 15 seconds after the engine starts.5. Operate the engine at low load until all systems reach operating temperature. Check all gauges during the warm-up period.Starting With Jumper Cables
Batteries give off flammable fumes that can explode.Improper jumper cable connections can cause an explosion resulting in personal injury.Prevent sparks near the batteries. Sparks could cause vapors to explode. Do not allow jumper cable ends to contact each other or the engine.Do not smoke when observing the battery electrolyte levels.Always wear protective glasses when working with batteries.Electrolyte is an acid and can cause personal injury if it contacts skin or eyes.
Engines installed without engine-to-frame ground straps can be damaged by electrical discharge.To prevent electrical discharge damage, check to make sure the engine's electrical system has an engine-to-frame ground strap. For engines which have the alternator connected to an engine component, the ground strap must connect that component to thframe.Some engines have starter-to-frame ground straps.
Have questions with 106671-3180?
Group cross 106671-3180 ZEXEL
Hino
106671-3180
220001490C
INJECTION-PUMP ASSEMBLY
EK100
EK100