Information injection-pump assembly
BOSCH
9 400 610 071
9400610071
ZEXEL
106671-2941
1066712941
MITSUBISHI
ME059626
me059626
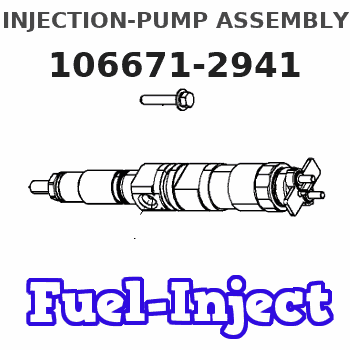
Rating:
Service parts 106671-2941 INJECTION-PUMP ASSEMBLY:
1.
_
7.
COUPLING PLATE
8.
_
9.
_
11.
Nozzle and Holder
ME059621
12.
Open Pre:MPa(Kqf/cm2)
21.6{220}
15.
NOZZLE SET
Include in #1:
106671-2941
as INJECTION-PUMP ASSEMBLY
Cross reference number
BOSCH
9 400 610 071
9400610071
ZEXEL
106671-2941
1066712941
MITSUBISHI
ME059626
me059626
Zexel num
Bosch num
Firm num
Name
106671-2941
9 400 610 071
ME059626 MITSUBISHI
INJECTION-PUMP ASSEMBLY
6D22T K 14CA INJECTION PUMP ASSY PE6P,6PD PE
6D22T K 14CA INJECTION PUMP ASSY PE6P,6PD PE
Calibration Data:
Adjustment conditions
Test oil
1404 Test oil ISO4113 or {SAEJ967d}
1404 Test oil ISO4113 or {SAEJ967d}
Test oil temperature
degC
40
40
45
Nozzle and nozzle holder
105780-8140
Bosch type code
EF8511/9A
Nozzle
105780-0000
Bosch type code
DN12SD12T
Nozzle holder
105780-2080
Bosch type code
EF8511/9
Opening pressure
MPa
17.2
Opening pressure
kgf/cm2
175
Injection pipe
Outer diameter - inner diameter - length (mm) mm 8-3-600
Outer diameter - inner diameter - length (mm) mm 8-3-600
Overflow valve
131424-4620
Overflow valve opening pressure
kPa
255
221
289
Overflow valve opening pressure
kgf/cm2
2.6
2.25
2.95
Tester oil delivery pressure
kPa
157
157
157
Tester oil delivery pressure
kgf/cm2
1.6
1.6
1.6
Direction of rotation (viewed from drive side)
Right R
Right R
Injection timing adjustment
Direction of rotation (viewed from drive side)
Right R
Right R
Injection order
1-5-3-6-
2-4
Pre-stroke
mm
4.8
4.75
4.85
Beginning of injection position
Governor side NO.1
Governor side NO.1
Difference between angles 1
Cal 1-5 deg. 60 59.5 60.5
Cal 1-5 deg. 60 59.5 60.5
Difference between angles 2
Cal 1-3 deg. 120 119.5 120.5
Cal 1-3 deg. 120 119.5 120.5
Difference between angles 3
Cal 1-6 deg. 180 179.5 180.5
Cal 1-6 deg. 180 179.5 180.5
Difference between angles 4
Cyl.1-2 deg. 240 239.5 240.5
Cyl.1-2 deg. 240 239.5 240.5
Difference between angles 5
Cal 1-4 deg. 300 299.5 300.5
Cal 1-4 deg. 300 299.5 300.5
Injection quantity adjustment
Adjusting point
A
Rack position
9.7
Pump speed
r/min
700
700
700
Average injection quantity
mm3/st.
75
72
78
Max. variation between cylinders
%
0
-3
3
Basic
*
Fixing the lever
*
Injection quantity adjustment_02
Adjusting point
B
Rack position
5.8+-0.5
Pump speed
r/min
500
500
500
Average injection quantity
mm3/st.
15
12.4
17.6
Max. variation between cylinders
%
0
-15
15
Fixing the rack
*
Injection quantity adjustment_03
Adjusting point
C
Rack position
13.9+-0.
5
Pump speed
r/min
100
100
100
Average injection quantity
mm3/st.
133
113
153
Fixing the lever
*
Rack limit
*
Injection quantity adjustment_04
Adjusting point
D
Rack position
6.9+-0.5
Pump speed
r/min
225
225
225
Average injection quantity
mm3/st.
15
12.4
17.6
Fixing the rack
*
Remarks
(check)
(check)
Timer adjustment
Pump speed
r/min
650--
Advance angle
deg.
0
0
0
Remarks
Start
Start
Timer adjustment_02
Pump speed
r/min
600
Advance angle
deg.
0.5
Timer adjustment_03
Pump speed
r/min
900
Advance angle
deg.
1.6
1.1
2.1
Timer adjustment_04
Pump speed
r/min
1000
Advance angle
deg.
2.2
1.7
2.7
Timer adjustment_05
Pump speed
r/min
-
Advance angle
deg.
3
2.5
3.5
Remarks
Measure the actual speed, stop
Measure the actual speed, stop
Test data Ex:
Governor adjustment
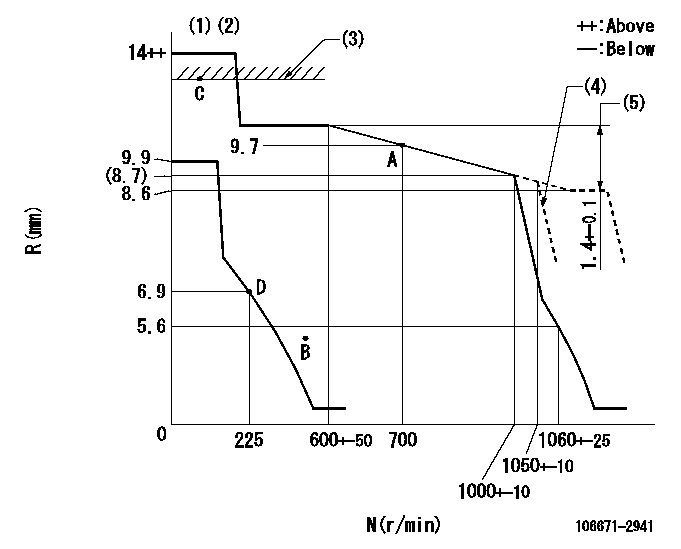
N:Pump speed
R:Rack position (mm)
(1)Target notch: K
(2)Torque spring does not operate.
(3)RACK LIMIT
(4)At shipping
(5)Rack difference between N = N1 and N = N2
----------
K=13 N1=1100r/min N2=500r/min
----------
----------
K=13 N1=1100r/min N2=500r/min
----------
Speed control lever angle

F:Full speed
I:Idle
(1)Stopper bolt setting
(2)At shipping
----------
----------
a=26deg+-5deg b=(2deg) c=5deg+-5deg
----------
----------
a=26deg+-5deg b=(2deg) c=5deg+-5deg
Stop lever angle

N:Pump normal
S:Stop the pump.
----------
----------
a=19deg+-5deg b=53deg+-5deg
----------
----------
a=19deg+-5deg b=53deg+-5deg
Timing setting

(1)Pump vertical direction
(2)Coupling's key groove position at No 1 cylinder's beginning of injection
(3)-
(4)-
----------
----------
a=(7deg)
----------
----------
a=(7deg)
Information:
You must read and understand the warnings and instructions contained in the Safety section of this manual before performing any operation or maintenance procedures.This maintenance is to be performed at the interval specified in the Maintenance Schedule for the engine being maintained.Before proceeding with 125 Service Hour maintenance, first perform previous maintenance requirements.Clutch (If Equipped)
Refer to the Instruction Plate on your clutch for the correct lubrication information.Lubricate Shift Collar Bearings
Instruction PlateLubricate the shift collar fittings with one or two grease gun shots each with MPGL or 2S3230 grease. Do not over grease.Lubricate Shift Lever Bearings
Refer to the Instruction Plate on the clutch for lubrication information.Some earlier clutches have pilot bearing fittings that need lubrication, whereas the later clutches have pilot bearings that are sealed for life.Lubricate the clutch shift lever bearings, pilot bearing and main shaft bearing (if equipped). Lubricate one fitting on top-rear of housing. Lubricate one fitting at the end of shaft. Refer to Instruction Plate on your clutch for correct lubrication information.Check/Adjust
If the clutch is damaged to the point of burst failure, expelled pieces can cause personal injury to anyone in the immediate area. Proper safeguards must be followed to prevent accidents.Do NOT operate the engine with Instruction Plate cover removed from the clutch. Personal injury may result.
While engaging the clutch to pick up the load, check the clutch adjustment. The clutch should engage with a firm push of the lever and a distinct snap. If the engagement is "soft" or slow, adjust the clutch.When clutch lever is disengaged, the hand lever must fall behind the vertical position. If the clutch slips, overheats, or operating lever disengages, clutch adjustment is necessary.1. Stop the engine and remove the clutch inspection cover.2. Rotate the clutch manually until the lock pin (engaged in the locking ring) is visible.3. Pull the lock pin out and rotate the locking ring clockwise (CW) until the lock pin slips or pops into the next notch. Turn adjusting ring CW to increase engagement torque and CCW to decrease engagement torque.4. Test the clutch adjustment. To test the clutch adjustment, engage clutch with a torque wrench to turn adjusting ring so that 296 to 393 N m (218 to 289 lb ft)torque or 636 90 N (143 20 lb) force at 541 mm (21.3 inches) length on lever is required to engage the clutch. If torque is still low, rotate the locking ring (CW) until lock pin slips into next notch. If the adjustment is too tight, turn the locking ring back (CCW) one to the previous notch.5. Install cover plate after adjustment is completed.
Refer to the Instruction Plate on your clutch for the correct lubrication information.Lubricate Shift Collar Bearings
Instruction PlateLubricate the shift collar fittings with one or two grease gun shots each with MPGL or 2S3230 grease. Do not over grease.Lubricate Shift Lever Bearings
Refer to the Instruction Plate on the clutch for lubrication information.Some earlier clutches have pilot bearing fittings that need lubrication, whereas the later clutches have pilot bearings that are sealed for life.Lubricate the clutch shift lever bearings, pilot bearing and main shaft bearing (if equipped). Lubricate one fitting on top-rear of housing. Lubricate one fitting at the end of shaft. Refer to Instruction Plate on your clutch for correct lubrication information.Check/Adjust
If the clutch is damaged to the point of burst failure, expelled pieces can cause personal injury to anyone in the immediate area. Proper safeguards must be followed to prevent accidents.Do NOT operate the engine with Instruction Plate cover removed from the clutch. Personal injury may result.
While engaging the clutch to pick up the load, check the clutch adjustment. The clutch should engage with a firm push of the lever and a distinct snap. If the engagement is "soft" or slow, adjust the clutch.When clutch lever is disengaged, the hand lever must fall behind the vertical position. If the clutch slips, overheats, or operating lever disengages, clutch adjustment is necessary.1. Stop the engine and remove the clutch inspection cover.2. Rotate the clutch manually until the lock pin (engaged in the locking ring) is visible.3. Pull the lock pin out and rotate the locking ring clockwise (CW) until the lock pin slips or pops into the next notch. Turn adjusting ring CW to increase engagement torque and CCW to decrease engagement torque.4. Test the clutch adjustment. To test the clutch adjustment, engage clutch with a torque wrench to turn adjusting ring so that 296 to 393 N m (218 to 289 lb ft)torque or 636 90 N (143 20 lb) force at 541 mm (21.3 inches) length on lever is required to engage the clutch. If torque is still low, rotate the locking ring (CW) until lock pin slips into next notch. If the adjustment is too tight, turn the locking ring back (CCW) one to the previous notch.5. Install cover plate after adjustment is completed.
Have questions with 106671-2941?
Group cross 106671-2941 ZEXEL
Mitsubishi
Mitsubishi
106671-2941
9 400 610 071
ME059626
INJECTION-PUMP ASSEMBLY
6D22T
6D22T