Information injection-pump assembly
ZEXEL
106671-1480
1066711480
ISUZU
1156023200
1156023200
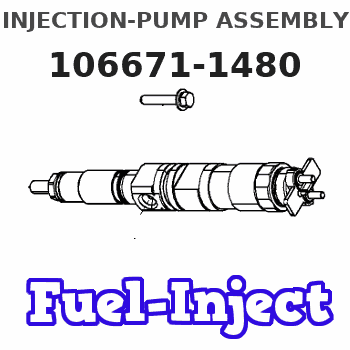
Rating:
Cross reference number
ZEXEL
106671-1480
1066711480
ISUZU
1156023200
1156023200
Zexel num
Bosch num
Firm num
Name
Calibration Data:
Adjustment conditions
Test oil
1404 Test oil ISO4113 or {SAEJ967d}
1404 Test oil ISO4113 or {SAEJ967d}
Test oil temperature
degC
40
40
45
Nozzle and nozzle holder
105780-8140
Bosch type code
EF8511/9A
Nozzle
105780-0000
Bosch type code
DN12SD12T
Nozzle holder
105780-2080
Bosch type code
EF8511/9
Opening pressure
MPa
17.2
Opening pressure
kgf/cm2
175
Injection pipe
Outer diameter - inner diameter - length (mm) mm 8-3-600
Outer diameter - inner diameter - length (mm) mm 8-3-600
Overflow valve
134424-1920
Overflow valve opening pressure
kPa
127
107
147
Overflow valve opening pressure
kgf/cm2
1.3
1.1
1.5
Tester oil delivery pressure
kPa
157
157
157
Tester oil delivery pressure
kgf/cm2
1.6
1.6
1.6
Direction of rotation (viewed from drive side)
Right R
Right R
Injection timing adjustment
Direction of rotation (viewed from drive side)
Right R
Right R
Injection order
1-4-2-6-
3-5
Pre-stroke
mm
3.8
3.77
3.83
Beginning of injection position
Drive side NO.1
Drive side NO.1
Difference between angles 1
Cal 1-4 deg. 60 59.75 60.25
Cal 1-4 deg. 60 59.75 60.25
Difference between angles 2
Cyl.1-2 deg. 120 119.75 120.25
Cyl.1-2 deg. 120 119.75 120.25
Difference between angles 3
Cal 1-6 deg. 180 179.75 180.25
Cal 1-6 deg. 180 179.75 180.25
Difference between angles 4
Cal 1-3 deg. 240 239.75 240.25
Cal 1-3 deg. 240 239.75 240.25
Difference between angles 5
Cal 1-5 deg. 300 299.75 300.25
Cal 1-5 deg. 300 299.75 300.25
Injection quantity adjustment
Adjusting point
A
Rack position
8.2
Pump speed
r/min
1000
1000
1000
Average injection quantity
mm3/st.
156.6
154.6
158.6
Max. variation between cylinders
%
0
-3
3
Basic
*
Fixing the lever
*
Injection quantity adjustment_02
Adjusting point
-
Rack position
5.4+-0.5
Pump speed
r/min
385
385
385
Average injection quantity
mm3/st.
13.2
10
16.4
Max. variation between cylinders
%
0
-13
13
Fixing the rack
*
Remarks
Adjust only variation between cylinders; adjust governor according to governor specifications.
Adjust only variation between cylinders; adjust governor according to governor specifications.
Injection quantity adjustment_03
Adjusting point
D
Rack position
-
Pump speed
r/min
150
150
150
Average injection quantity
mm3/st.
213
213
Fixing the lever
*
Rack limit
*
Timer adjustment
Pump speed
r/min
750--
Advance angle
deg.
0
0
0
Remarks
Start
Start
Timer adjustment_02
Pump speed
r/min
700
Advance angle
deg.
0.5
Timer adjustment_03
Pump speed
r/min
1000
Advance angle
deg.
1
0.5
1.5
Remarks
Finish
Finish
Test data Ex:
Governor adjustment
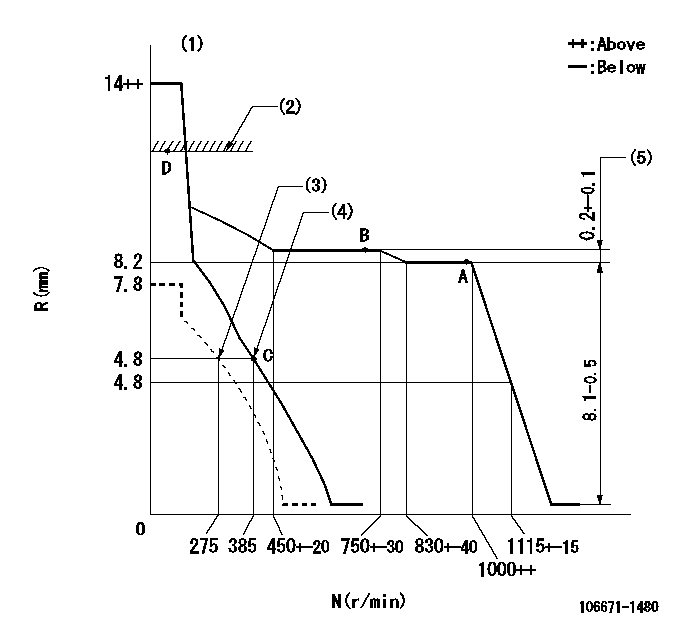
N:Pump speed
R:Rack position (mm)
(1)Notch fixed: K
(2)RACK LIMIT
(3)Set idle sub-spring
(4)Main spring setting
(5)Rack difference between N = N1 and N = N2
----------
K=15 N1=1000r/min N2=700r/min
----------
----------
K=15 N1=1000r/min N2=700r/min
----------
Speed control lever angle
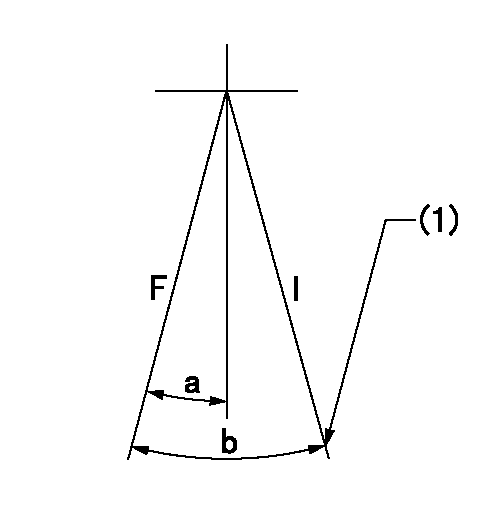
F:Full speed
I:Idle
(1)Stopper bolt setting
----------
----------
a=(6deg)+-5deg b=(19deg)+-5deg
----------
----------
a=(6deg)+-5deg b=(19deg)+-5deg
Stop lever angle

N:Pump normal
S:Stop the pump.
----------
----------
a=22deg+-5deg b=46deg+-5deg
----------
----------
a=22deg+-5deg b=46deg+-5deg
Timing setting
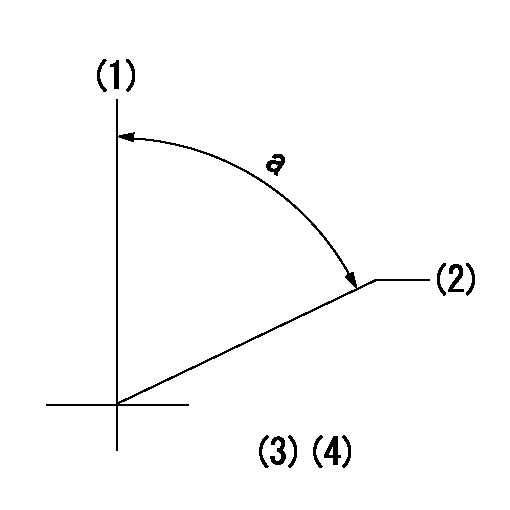
(1)Pump vertical direction
(2)Position of timer's threaded hole at No 1 cylinder's beginning of injection
(3)B.T.D.C.: aa
(4)-
----------
aa=17deg
----------
a=(70deg)
----------
aa=17deg
----------
a=(70deg)
Information:
Bearings
Anti-Friction Bearings
When an anti-friction bearing is removed, cover it to keep out dirt and abrasives. Wash the bearings in nonflammable cleaning solution and allow them to drain dry. The bearings may be dried with compressed air, but DO NOT SPIN THE BEARING. Discard the bearings if the races and balls or rollers are pitted, scored or burned. If the bearing is serviceable, coat it with oil and wrap it in clean paper. DO NOT unwrap new bearings until time of installation.The life of an anti-friction bearing will be shortened if not properly lubricated.Double Row, Tapered Roller
Double row, tapered roller bearings are precision fit during manufacture and the components are not interchangeable. The cups, cones and spacers are usually etched with the same serial number and letter designator. If no letter designators are found, wire the components together to assure correct installation. Reusable bearing components should be installed in their original positions.Heating Bearings
Bearings which require expansion for installation should be heated in oil not to exceed 121°C (250°F). When more than one part is heated to aid in assembly, they must be allowed to cool and then pressed together again. Parts often separate as they cool and shrink.Installation
Lubricate new or used bearings before installation. Bearings that are to be preloaded must have a film of oil over the entire assembly to obtain accurate preloading. When installing a bearing, spacer or washer against a shoulder on a shaft, be sure the chamfered side is toward the shoulder. When pressing bearings into a retainer or bore, apply pressure to the outer race. If the bearing is pressed on the shaft, apply pressure on the inner race.Preload
Preload is an initial force placed on the bearing at the time of assembly.Determine preload or end clearance form the Specifications Section of this Service Manual. Care should be exercised in applying preload. Misapplication of preload to bearings requiring end clearance can result in bearing failure.Sleeve Bearings
DO NOT INSTALL SLEEVE BEARINGS WITH A HAMMER. Use a press, if possible and apply the pressure directly in line with the bore. If it is necessary to drive on a bearing, use a driver or a bar with a smooth flat end. If a sleeve bearing has an oil hole, align it with the oil hole in the mating part.
Anti-Friction Bearings
When an anti-friction bearing is removed, cover it to keep out dirt and abrasives. Wash the bearings in nonflammable cleaning solution and allow them to drain dry. The bearings may be dried with compressed air, but DO NOT SPIN THE BEARING. Discard the bearings if the races and balls or rollers are pitted, scored or burned. If the bearing is serviceable, coat it with oil and wrap it in clean paper. DO NOT unwrap new bearings until time of installation.The life of an anti-friction bearing will be shortened if not properly lubricated.Double Row, Tapered Roller
Double row, tapered roller bearings are precision fit during manufacture and the components are not interchangeable. The cups, cones and spacers are usually etched with the same serial number and letter designator. If no letter designators are found, wire the components together to assure correct installation. Reusable bearing components should be installed in their original positions.Heating Bearings
Bearings which require expansion for installation should be heated in oil not to exceed 121°C (250°F). When more than one part is heated to aid in assembly, they must be allowed to cool and then pressed together again. Parts often separate as they cool and shrink.Installation
Lubricate new or used bearings before installation. Bearings that are to be preloaded must have a film of oil over the entire assembly to obtain accurate preloading. When installing a bearing, spacer or washer against a shoulder on a shaft, be sure the chamfered side is toward the shoulder. When pressing bearings into a retainer or bore, apply pressure to the outer race. If the bearing is pressed on the shaft, apply pressure on the inner race.Preload
Preload is an initial force placed on the bearing at the time of assembly.Determine preload or end clearance form the Specifications Section of this Service Manual. Care should be exercised in applying preload. Misapplication of preload to bearings requiring end clearance can result in bearing failure.Sleeve Bearings
DO NOT INSTALL SLEEVE BEARINGS WITH A HAMMER. Use a press, if possible and apply the pressure directly in line with the bore. If it is necessary to drive on a bearing, use a driver or a bar with a smooth flat end. If a sleeve bearing has an oil hole, align it with the oil hole in the mating part.