Information injection-pump assembly
ZEXEL
106671-0130
1066710130
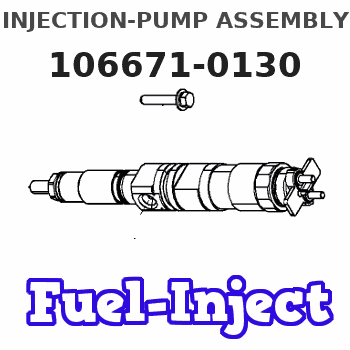
Rating:
Service parts 106671-0130 INJECTION-PUMP ASSEMBLY:
1.
_
3.
GOVERNOR
7.
COUPLING PLATE
8.
_
9.
_
11.
Nozzle and Holder
16600-96514
12.
Open Pre:MPa(Kqf/cm2)
17.7{180}/22.6{230}
15.
NOZZLE SET
Include in #1:
106671-0130
as INJECTION-PUMP ASSEMBLY
Cross reference number
ZEXEL
106671-0130
1066710130
Zexel num
Bosch num
Firm num
Name
Calibration Data:
Adjustment conditions
Test oil
1404 Test oil ISO4113 or {SAEJ967d}
1404 Test oil ISO4113 or {SAEJ967d}
Test oil temperature
degC
40
40
45
Nozzle and nozzle holder
105780-8140
Bosch type code
EF8511/9A
Nozzle
105780-0000
Bosch type code
DN12SD12T
Nozzle holder
105780-2080
Bosch type code
EF8511/9
Opening pressure
MPa
17.2
Opening pressure
kgf/cm2
175
Injection pipe
Outer diameter - inner diameter - length (mm) mm 8-3-600
Outer diameter - inner diameter - length (mm) mm 8-3-600
Overflow valve opening pressure
kPa
157
123
191
Overflow valve opening pressure
kgf/cm2
1.6
1.25
1.95
Tester oil delivery pressure
kPa
157
157
157
Tester oil delivery pressure
kgf/cm2
1.6
1.6
1.6
Direction of rotation (viewed from drive side)
Right R
Right R
Injection timing adjustment
Direction of rotation (viewed from drive side)
Right R
Right R
Injection order
1-4-2-6-
3-5
Pre-stroke
mm
3.65
3.6
3.7
Beginning of injection position
Drive side NO.1
Drive side NO.1
Difference between angles 1
Cal 1-4 deg. 60 59.5 60.5
Cal 1-4 deg. 60 59.5 60.5
Difference between angles 2
Cyl.1-2 deg. 120 119.5 120.5
Cyl.1-2 deg. 120 119.5 120.5
Difference between angles 3
Cal 1-6 deg. 180 179.5 180.5
Cal 1-6 deg. 180 179.5 180.5
Difference between angles 4
Cal 1-3 deg. 240 239.5 240.5
Cal 1-3 deg. 240 239.5 240.5
Difference between angles 5
Cal 1-5 deg. 300 299.5 300.5
Cal 1-5 deg. 300 299.5 300.5
Injection quantity adjustment
Adjusting point
A
Rack position
R2(11.5)
Pump speed
r/min
1100
1100
1100
Average injection quantity
mm3/st.
153.8
149.8
157.8
Max. variation between cylinders
%
0
-5
5
Fixing the lever
*
Boost pressure
kPa
30.7
30.7
Boost pressure
mmHg
230
230
Injection quantity adjustment_02
Adjusting point
B
Rack position
11.8
Pump speed
r/min
600
600
600
Average injection quantity
mm3/st.
161.7
159.7
163.7
Max. variation between cylinders
%
0
-4
4
Basic
*
Fixing the lever
*
Boost pressure
kPa
30.7
30.7
Boost pressure
mmHg
230
230
Injection quantity adjustment_03
Adjusting point
C
Rack position
7.4+-0.5
Pump speed
r/min
225
225
225
Average injection quantity
mm3/st.
10.1
9.1
11.1
Max. variation between cylinders
%
0
-10
10
Fixing the rack
*
Boost pressure
kPa
0
0
0
Boost pressure
mmHg
0
0
0
Injection quantity adjustment_04
Adjusting point
D
Rack position
R1(10.7)
Pump speed
r/min
300
300
300
Average injection quantity
mm3/st.
120.6
118.6
122.6
Fixing the lever
*
Boost pressure
kPa
0
0
0
Boost pressure
mmHg
0
0
0
Injection quantity adjustment_05
Adjusting point
E
Rack position
12.3
Pump speed
r/min
300
300
300
Average injection quantity
mm3/st.
171.1
166.1
176.1
Fixing the lever
*
Rack limit
*
Boost compensator adjustment
Pump speed
r/min
300
300
300
Rack position
R1(10.7)
Boost pressure
kPa
4
Boost pressure
mmHg
30
Boost compensator adjustment_02
Pump speed
r/min
300
300
300
Rack position
12.3
Boost pressure
kPa
17.3
17.3
17.3
Boost pressure
mmHg
130
130
130
Test data Ex:
Governor adjustment
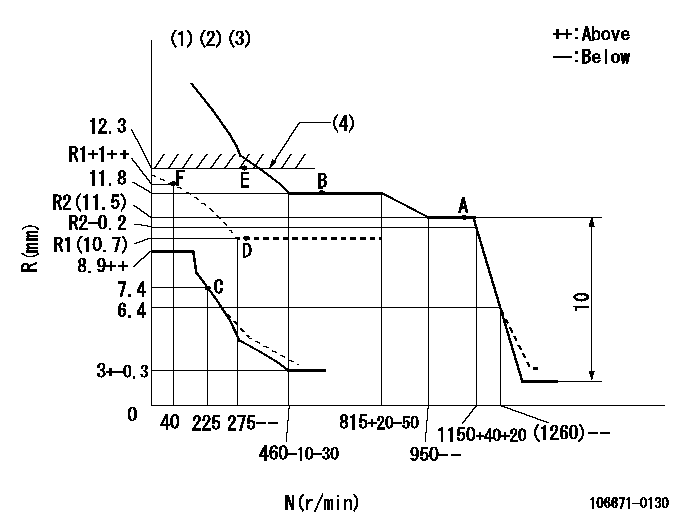
N:Pump speed
R:Rack position (mm)
(1)Lever ratio: RT
(2)Target shim dimension: TH
(3)Damper spring setting: DL
(4)Rack limit using stop lever
----------
RT=1 TH=2mm DL=6.4-0.2mm
----------
----------
RT=1 TH=2mm DL=6.4-0.2mm
----------
Timer adjustment

(1)Adjusting range
(2)Step response time
(N): Speed of the pump
(L): Load
(theta) Advance angle
(Srd1) Step response time 1
(Srd2) Step response time 2
1. Adjusting conditions for the variable timer
(1)Adjust the clearance between the pickup and the protrusion to L.
----------
L=1-0.2mm N2=800r/min C2=(6.5)deg t1=2--sec. t2=2--sec.
----------
N1=1250++r/min P1=0kPa(0kgf/cm2) P2=392kPa(4kgf/cm2) C1=6.5+-0.5deg R01=0/4load R02=4/4load
----------
L=1-0.2mm N2=800r/min C2=(6.5)deg t1=2--sec. t2=2--sec.
----------
N1=1250++r/min P1=0kPa(0kgf/cm2) P2=392kPa(4kgf/cm2) C1=6.5+-0.5deg R01=0/4load R02=4/4load
Speed control lever angle
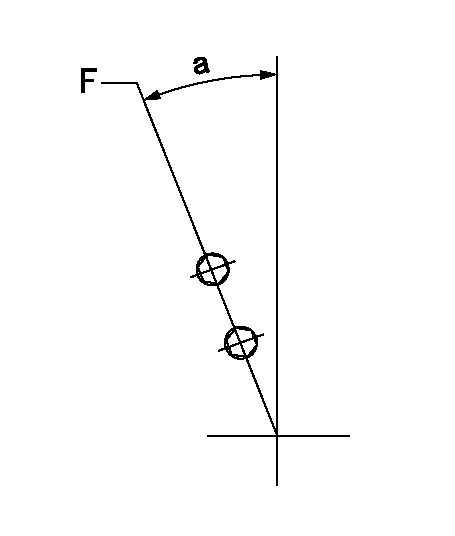
F:Full speed
----------
----------
a=31deg+-5deg
----------
----------
a=31deg+-5deg
0000000901
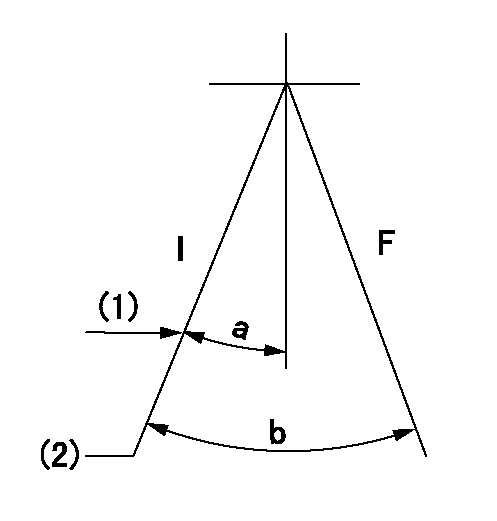
F:Full load
I:Idle
(1)Stopper bolt setting
(2)At center of threaded hole above R = aa
----------
aa=17mm
----------
a=22deg+-5deg b=32.5deg+-3deg
----------
aa=17mm
----------
a=22deg+-5deg b=32.5deg+-3deg
Stop lever angle
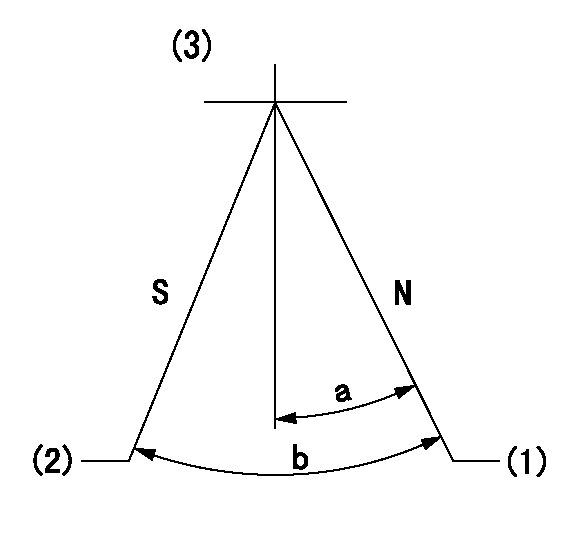
N:Pump normal
S:Stop the pump.
(1)Rack position = aa
(2)Rack position bb, pump speed cc
(3)Adjust after setting excess fuel lever.
----------
aa=12.3mm bb=1+0.5mm cc=0r/min
----------
a=19.5deg+-5deg b=32.5deg+-5deg
----------
aa=12.3mm bb=1+0.5mm cc=0r/min
----------
a=19.5deg+-5deg b=32.5deg+-5deg
0000001101
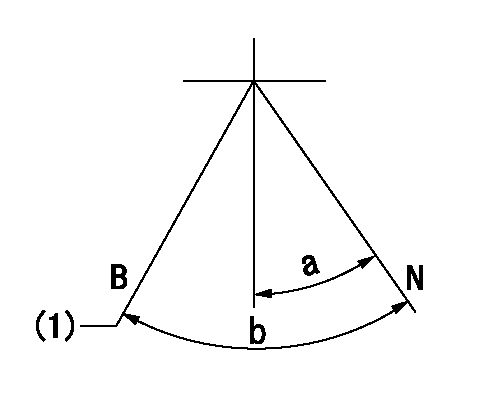
N:Normal
B:When boosted
(1)Rack position = aa
----------
aa=13mm
----------
a=(18deg) b=(32deg)
----------
aa=13mm
----------
a=(18deg) b=(32deg)
0000001501 RACK SENSOR

V1:Supply voltage
V2f:Full side output voltage
V2i:Idle side output voltage
(A) Black
(B) Yellow
(C) Red
(D) Trimmer
(E): Shaft
(F) Nut
(G) Load lever
1. Load sensor adjustment
(1)Connect as shown in the above diagram and apply supply voltage V1.
(2)Hold the load lever (G) against the full side.
(3)Turn the shaft so that the voltage between (A) and (B) is V2.
(4)Hold the load lever (G) against the idle side.
(5)Adjust (D) so that the voltage between (A) and (B) is V2i.
(6)Repeat the above adjustments.
(7)Tighten the nut (F) at the point satisfying the standards.
(8)Hold the load lever against the full side stopper and the idle side stopper.
(9)At this time, confirm that the full side output voltage is V2f and the idle side output voltage is V2i.
----------
V1= 5+-0.02V V2f=0.3+0.03V V2i=2.2-0.03V
----------
----------
V1= 5+-0.02V V2f=0.3+0.03V V2i=2.2-0.03V
----------
Timing setting

(1)Pump vertical direction
(2)Coupling's key groove position at No 1 cylinder's beginning of injection
(3)-
(4)-
----------
----------
a=(20deg)
----------
----------
a=(20deg)
Information:
This Program must be administered as soon as possible. When reporting the repair, use "PI3330" as the Part Number, "7751" as the Group Number, "56" as the Warranty Claim Description Code and "T" as the SIMS Description Code. Exception: If the repair is done after failure, use "PI3330" as the Part Number, "7751" as the Group Number, "96" as the Warranty Claim Description Code, and "Z" as the SIMS Description Code.
Completion Date
March 31, 2000Termination Date
September 30, 2000Problem
The torque of the injector electronic solenoid valves need to be checked. The valve has four Torx bolts that hold the stator to the housing. If these bolts are not properly tightened, fuel can leak into the oil.
Affected Product
Model & Identification Number
D11R (9TR441-442)
776D (5ER126, 5ER127)
785C (1HW122)
793C (4GZ165-167)
777D (3PR1058, 3PR1057, 3PR1061, 3PR1059, 3PR1060, 3PR1063)
3508B (3DM157-159 4GM426-439 6PN532-533 , 6PN535-536, 6PN539-540, 6PN542-543 5PS225-234 2HW125-126 1FZ366-370 )
3512 (6PM38-39 3MS186 3RS329 )
3512B (8EM317-318 8RM395-397 4TM215-217 3ZW131-134 6WN349-356 )
3516 (7KM50-51 3SS306-307 )
3516B (6HN384, 6HN390, 6HN392, 6HN394, 6HN398 7RN818-819 , 7RN821, 7RN824, 7RN826-827, 7RN833, 7RN836-840, 7RN850, 7RN852 8KN368-369 , 8KN372, 8KN373 7TR818 4BW333-334 )
Parts Needed
Dealers will not need to order parts for this Program.
Action Required
See the attached procedure.
Owner Notification
U.S. and Canadian owners will receive the attached Owner Notification.
Service Claim Allowances
This is a 3-hour job.
U.S. and Canadian Dealers Only - Eligible dealers may enter a Type 2 SIMS Report.
Parts Disposition
Handle the parts in accordance with your Warranty Bulletin on warranty parts handling.
MAKE EVERY EFFORT TO COMPLETE THIS PROGRAM AS SOON AS POSSIBLE.
Attach.(1-Owner Notification)(Torque Procedure)Copy Of Owner Notification For U.S. And Canadian Owners
Torque Procedure For Electronic 3500B Injector Bolts
THIS REWORK IS RESTRICTED TO ENGINES LISTED IN THE AFFECTED PRODUCT ONLY.
THIS PIP DOES NOT ALLOW FOR THE REMOVAL OF THE INJECTOR. DO NOT REMOVE ANY OF THE STATOR BOLTS. THIS WILL VOID INJECTOR WARRANTY.
PROCEDURE:
1. Remove the valve covers to reveal the injector assembly/ electronic valve.2. Remove electronic valve terminal connector (two retaining nuts) with a " universal socket. Take the terminal connectors off of the posts.3. The four stator retaining bolts you need to check are now accessible. To properly complete the torque check, the following tools are required.a) Click torque wrench, " drive (capable of accurately measuring 2.0 N m)b) 6" extension " drive.c) universal joint, "drived) T10 Torx bit, " drive4. Set the torque wrench value to (2.1 N m). Check all four bolts and tighten (if needed) until they reach the 2.1 specification.:
DO NOT OVER TORQUE THE STATOR RETAINING BOLTS (2.1 N m). THIS COULD CAUSE FURTHER DAMAGE.
5. Reassemble the engine in the reverse order.a) Torque value of the terminal connector nuts - 3.0 N m b) Torque value for the valve cover bolts - 47 9 N m.
Completion Date
March 31, 2000Termination Date
September 30, 2000Problem
The torque of the injector electronic solenoid valves need to be checked. The valve has four Torx bolts that hold the stator to the housing. If these bolts are not properly tightened, fuel can leak into the oil.
Affected Product
Model & Identification Number
D11R (9TR441-442)
776D (5ER126, 5ER127)
785C (1HW122)
793C (4GZ165-167)
777D (3PR1058, 3PR1057, 3PR1061, 3PR1059, 3PR1060, 3PR1063)
3508B (3DM157-159 4GM426-439 6PN532-533 , 6PN535-536, 6PN539-540, 6PN542-543 5PS225-234 2HW125-126 1FZ366-370 )
3512 (6PM38-39 3MS186 3RS329 )
3512B (8EM317-318 8RM395-397 4TM215-217 3ZW131-134 6WN349-356 )
3516 (7KM50-51 3SS306-307 )
3516B (6HN384, 6HN390, 6HN392, 6HN394, 6HN398 7RN818-819 , 7RN821, 7RN824, 7RN826-827, 7RN833, 7RN836-840, 7RN850, 7RN852 8KN368-369 , 8KN372, 8KN373 7TR818 4BW333-334 )
Parts Needed
Dealers will not need to order parts for this Program.
Action Required
See the attached procedure.
Owner Notification
U.S. and Canadian owners will receive the attached Owner Notification.
Service Claim Allowances
This is a 3-hour job.
U.S. and Canadian Dealers Only - Eligible dealers may enter a Type 2 SIMS Report.
Parts Disposition
Handle the parts in accordance with your Warranty Bulletin on warranty parts handling.
MAKE EVERY EFFORT TO COMPLETE THIS PROGRAM AS SOON AS POSSIBLE.
Attach.(1-Owner Notification)(Torque Procedure)Copy Of Owner Notification For U.S. And Canadian Owners
Torque Procedure For Electronic 3500B Injector Bolts
THIS REWORK IS RESTRICTED TO ENGINES LISTED IN THE AFFECTED PRODUCT ONLY.
THIS PIP DOES NOT ALLOW FOR THE REMOVAL OF THE INJECTOR. DO NOT REMOVE ANY OF THE STATOR BOLTS. THIS WILL VOID INJECTOR WARRANTY.
PROCEDURE:
1. Remove the valve covers to reveal the injector assembly/ electronic valve.2. Remove electronic valve terminal connector (two retaining nuts) with a " universal socket. Take the terminal connectors off of the posts.3. The four stator retaining bolts you need to check are now accessible. To properly complete the torque check, the following tools are required.a) Click torque wrench, " drive (capable of accurately measuring 2.0 N m)b) 6" extension " drive.c) universal joint, "drived) T10 Torx bit, " drive4. Set the torque wrench value to (2.1 N m). Check all four bolts and tighten (if needed) until they reach the 2.1 specification.:
DO NOT OVER TORQUE THE STATOR RETAINING BOLTS (2.1 N m). THIS COULD CAUSE FURTHER DAMAGE.
5. Reassemble the engine in the reverse order.a) Torque value of the terminal connector nuts - 3.0 N m b) Torque value for the valve cover bolts - 47 9 N m.