Information injection-pump assembly
BOSCH
9 400 610 833
9400610833
ZEXEL
106662-4281
1066624281
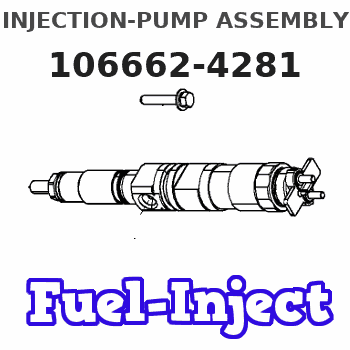
Rating:
Service parts 106662-4281 INJECTION-PUMP ASSEMBLY:
1.
_
5.
AUTOM. ADVANCE MECHANIS
6.
COUPLING PLATE
7.
COUPLING PLATE
8.
_
9.
_
11.
Nozzle and Holder
6221-13-3400
12.
Open Pre:MPa(Kqf/cm2)
24.0{245}
15.
NOZZLE SET
Include in #1:
106662-4281
as INJECTION-PUMP ASSEMBLY
Cross reference number
BOSCH
9 400 610 833
9400610833
ZEXEL
106662-4281
1066624281
Zexel num
Bosch num
Firm num
Name
Calibration Data:
Adjustment conditions
Test oil
1404 Test oil ISO4113 or {SAEJ967d}
1404 Test oil ISO4113 or {SAEJ967d}
Test oil temperature
degC
40
40
45
Nozzle and nozzle holder
105780-8140
Bosch type code
EF8511/9A
Nozzle
105780-0000
Bosch type code
DN12SD12T
Nozzle holder
105780-2080
Bosch type code
EF8511/9
Opening pressure
MPa
17.2
Opening pressure
kgf/cm2
175
Injection pipe
Outer diameter - inner diameter - length (mm) mm 8-3-600
Outer diameter - inner diameter - length (mm) mm 8-3-600
Overflow valve
131425-1520
Overflow valve opening pressure
kPa
255
221
289
Overflow valve opening pressure
kgf/cm2
2.6
2.25
2.95
Tester oil delivery pressure
kPa
157
157
157
Tester oil delivery pressure
kgf/cm2
1.6
1.6
1.6
RED3 control unit part number
407910-2
470
RED3 rack sensor specifications
mm
15
Direction of rotation (viewed from drive side)
Right R
Right R
Injection timing adjustment
Direction of rotation (viewed from drive side)
Right R
Right R
Injection order
1-5-3-6-
2-4
Pre-stroke
mm
3.9
3.85
3.95
Beginning of injection position
Drive side NO.1
Drive side NO.1
Difference between angles 1
Cal 1-5 deg. 60 59.5 60.5
Cal 1-5 deg. 60 59.5 60.5
Difference between angles 2
Cal 1-3 deg. 120 119.5 120.5
Cal 1-3 deg. 120 119.5 120.5
Difference between angles 3
Cal 1-6 deg. 180 179.5 180.5
Cal 1-6 deg. 180 179.5 180.5
Difference between angles 4
Cyl.1-2 deg. 240 239.5 240.5
Cyl.1-2 deg. 240 239.5 240.5
Difference between angles 5
Cal 1-4 deg. 300 299.5 300.5
Cal 1-4 deg. 300 299.5 300.5
Injection quantity adjustment
Rack position
(11)
Vist
V
1.8
1.8
1.8
Pump speed
r/min
1100
1100
1100
Average injection quantity
mm3/st.
96
94.5
97.5
Max. variation between cylinders
%
0
-3
3
Basic
*
Injection quantity adjustment_02
Rack position
(6.2)
Vist
V
2.8
2.7
2.9
Pump speed
r/min
390
390
390
Average injection quantity
mm3/st.
10
8.8
11.2
Max. variation between cylinders
%
0
-15
15
Injection quantity adjustment_03
Remarks
Rack limit setting V = 0.9-0.04
Rack limit setting V = 0.9-0.04
Test data Ex:
Speed control lever angle
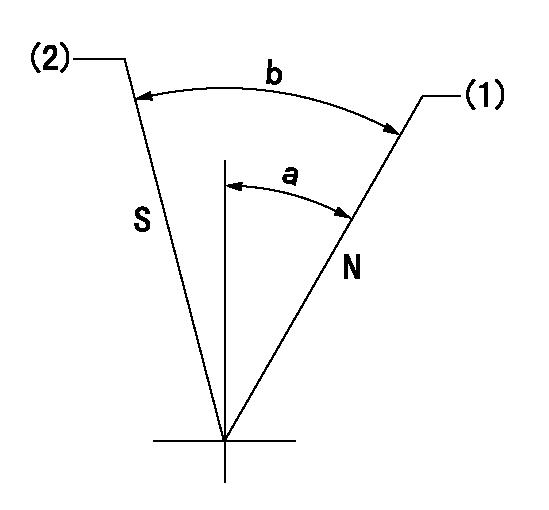
N:Pump normal
S:Stop the pump.
(1)Vist = aa, (rack position = bb)
(2)Rack position = cc
----------
aa=0.8V bb=16mm cc=1mm
----------
a=19deg+-5deg b=29deg+-5deg
----------
aa=0.8V bb=16mm cc=1mm
----------
a=19deg+-5deg b=29deg+-5deg
0000000901
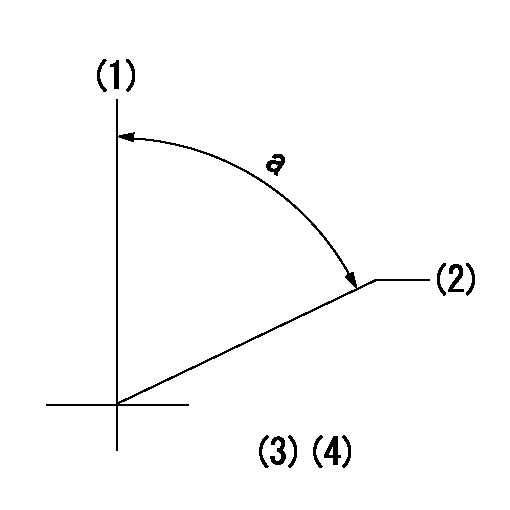
(1)Pump vertical direction
(2)Position of camshaft's key groove at No 1 cylinder's beginning of injection
(3)B.T.D.C.: aa
(4)-
----------
aa=15deg
----------
a=(50deg)
----------
aa=15deg
----------
a=(50deg)
Stop lever angle

(Rs) rack sensor specifications
(C/U) control unit part number
(V) Rack sensor output voltage
(R) Rack position (mm)
1. Confirming governor output characteristics (rack 15 mm, span 6 mm)
(1)When the output voltages of the rack sensor are V1 and V2, check that the rack positions R1 and R2 in the table above are satisfied.
----------
----------
----------
----------
Information:
Problem
Some fuel injectors may fail on certain Challenger 75 Tractors and 3176 Truck Engines.
Affected Product
Model & Identification Number
Challenger 75 (4CJ1-406)
3176 (2YG1-Up; 7LG1-4822)
Parts Needed
Use the following parts in quantities needed to perform repairs. The application of each injector listed is noted. Use remanufactured injectors, unless unavailable.
0R3397 Injector Grp. (4P9510 if reman unavailable for 7LG 250-300 HP)0R3398 Injector Grp. (4P9520 if reman unavailable for 7LG 325 HP and 4CJ)0R3399 Injector Grp. (4P9610 if reman unavailable for 2YG 250-275 HP)0R3400 Injector Grp. (4P9620 if reman unavailable for 2YG 300-325 HP)9X7557 Seal (injector upper O-ring)9X7722 Seal (injector lower O-ring)336044 Seal (injector thrust-pad-retaining O-ring)Action Required
1. Isolate the injector which is causing the problem. Some failure modes require duplication of the conditions where the customer say the problem occurs (i.e. at full load, idle, high speed, low speed, etc.)2. Replace injectors only after verifying a problem using the 1U6661 Unit Injector Tester, cutting out cylinders, etc. Replace any failed injectors according to the rework procedures attached.Service Claim Allowances
This is a 2.5-hour job. Add 0.2 hours for 1st injector diagnostic test and 0.1 hours for each additional injector test. Add 1.2 hours for first injector sleeve replaced and 0.7 hours for each additional sleeve replaced.
3176 Truck Engines
Parts Disposition
Handle the parts in accordance with your Warranty Bulletin on warranty parts handling.
Attach. (1-Rework Procedure)Rework Procedure
1. Drain fuel from the cylinder head and fuel manifold. Remove air inlet piping, valve covers and Jake Brake (if equipped) , rocker arm assemblies, and injector hold down bolts. Remove the suspect injector(s) for inspection and test. Mark each injector to denote the cylinder from which it was removed. It is important to install the injector(s) into the same cylinder to prevent combustion gas leaks.2. Test the injector(s) using the 1U6661 Unit Injector Tester. Check for leaks, VOP, and spray pattern. Replace all injectors which do not pass these test.Procedure For Installing The Following Injector Part Numbers:
4P1410, 4P1420, 4P2810, 4P2820, 0R3177, AND 0R3178
1. Inspect the raised edge on the injector cone for signs of damage. If any nicks or dings are present, do not reuse the injector.2. Ream the sleeves before installing the injectors. Ream only until the sleeve has been cut to provide a full length concentric taper past the injector/sleeve sealing interface. Full removal of the indentation created by the cone step edge is not necessary.3. Install new O-rings on the injector and apply STP ® to prevent cutting during installation.4. Install the injectors, apply 6V4876 Molykote to the hold-down bolt threads and tighten the bolts to 33 NM (24 ft. lb.). Make sure the longer 5P8347 Bolts and 4P8525 Spacers (or 8T0100 Bolts and 4P1711 Spacers) are used.5. Inspect bridge assemblies for wear.Procedures For Installing All Other Injectors:
1. Ream the sleeves before installing the injectors. Ream only until the sleeves have been cut to provide a full length concentric taper past the injector/sleeve sealing interface.2. After reaming, apply a thin coating of liquid machinist's blue (Dykem) to the bottom of the sleeves - allow to dry. Install injector without
Some fuel injectors may fail on certain Challenger 75 Tractors and 3176 Truck Engines.
Affected Product
Model & Identification Number
Challenger 75 (4CJ1-406)
3176 (2YG1-Up; 7LG1-4822)
Parts Needed
Use the following parts in quantities needed to perform repairs. The application of each injector listed is noted. Use remanufactured injectors, unless unavailable.
0R3397 Injector Grp. (4P9510 if reman unavailable for 7LG 250-300 HP)0R3398 Injector Grp. (4P9520 if reman unavailable for 7LG 325 HP and 4CJ)0R3399 Injector Grp. (4P9610 if reman unavailable for 2YG 250-275 HP)0R3400 Injector Grp. (4P9620 if reman unavailable for 2YG 300-325 HP)9X7557 Seal (injector upper O-ring)9X7722 Seal (injector lower O-ring)336044 Seal (injector thrust-pad-retaining O-ring)Action Required
1. Isolate the injector which is causing the problem. Some failure modes require duplication of the conditions where the customer say the problem occurs (i.e. at full load, idle, high speed, low speed, etc.)2. Replace injectors only after verifying a problem using the 1U6661 Unit Injector Tester, cutting out cylinders, etc. Replace any failed injectors according to the rework procedures attached.Service Claim Allowances
This is a 2.5-hour job. Add 0.2 hours for 1st injector diagnostic test and 0.1 hours for each additional injector test. Add 1.2 hours for first injector sleeve replaced and 0.7 hours for each additional sleeve replaced.
3176 Truck Engines
Parts Disposition
Handle the parts in accordance with your Warranty Bulletin on warranty parts handling.
Attach. (1-Rework Procedure)Rework Procedure
1. Drain fuel from the cylinder head and fuel manifold. Remove air inlet piping, valve covers and Jake Brake (if equipped) , rocker arm assemblies, and injector hold down bolts. Remove the suspect injector(s) for inspection and test. Mark each injector to denote the cylinder from which it was removed. It is important to install the injector(s) into the same cylinder to prevent combustion gas leaks.2. Test the injector(s) using the 1U6661 Unit Injector Tester. Check for leaks, VOP, and spray pattern. Replace all injectors which do not pass these test.Procedure For Installing The Following Injector Part Numbers:
4P1410, 4P1420, 4P2810, 4P2820, 0R3177, AND 0R3178
1. Inspect the raised edge on the injector cone for signs of damage. If any nicks or dings are present, do not reuse the injector.2. Ream the sleeves before installing the injectors. Ream only until the sleeve has been cut to provide a full length concentric taper past the injector/sleeve sealing interface. Full removal of the indentation created by the cone step edge is not necessary.3. Install new O-rings on the injector and apply STP ® to prevent cutting during installation.4. Install the injectors, apply 6V4876 Molykote to the hold-down bolt threads and tighten the bolts to 33 NM (24 ft. lb.). Make sure the longer 5P8347 Bolts and 4P8525 Spacers (or 8T0100 Bolts and 4P1711 Spacers) are used.5. Inspect bridge assemblies for wear.Procedures For Installing All Other Injectors:
1. Ream the sleeves before installing the injectors. Ream only until the sleeves have been cut to provide a full length concentric taper past the injector/sleeve sealing interface.2. After reaming, apply a thin coating of liquid machinist's blue (Dykem) to the bottom of the sleeves - allow to dry. Install injector without