Information injection-pump assembly
BOSCH
9 400 616 589
9400616589
ZEXEL
106661-2040
1066612040
MITSUBISHI
ME056800
me056800

Rating:
Service parts 106661-2040 INJECTION-PUMP ASSEMBLY:
1.
_
7.
COUPLING PLATE
8.
_
9.
_
11.
Nozzle and Holder
12.
Open Pre:MPa(Kqf/cm2)
17.7{180}/24.5{250}
15.
NOZZLE SET
Include in #1:
106661-2040
as INJECTION-PUMP ASSEMBLY
Cross reference number
BOSCH
9 400 616 589
9400616589
ZEXEL
106661-2040
1066612040
MITSUBISHI
ME056800
me056800
Zexel num
Bosch num
Firm num
Name
Calibration Data:
Adjustment conditions
Test oil
1404 Test oil ISO4113 or {SAEJ967d}
1404 Test oil ISO4113 or {SAEJ967d}
Test oil temperature
degC
40
40
45
Nozzle and nozzle holder
105780-8140
Bosch type code
EF8511/9A
Nozzle
105780-0000
Bosch type code
DN12SD12T
Nozzle holder
105780-2080
Bosch type code
EF8511/9
Opening pressure
MPa
17.2
Opening pressure
kgf/cm2
175
Injection pipe
Outer diameter - inner diameter - length (mm) mm 8-3-600
Outer diameter - inner diameter - length (mm) mm 8-3-600
Overflow valve
131424-6920
Overflow valve opening pressure
kPa
191
157
225
Overflow valve opening pressure
kgf/cm2
1.95
1.6
2.3
Tester oil delivery pressure
kPa
157
157
157
Tester oil delivery pressure
kgf/cm2
1.6
1.6
1.6
Direction of rotation (viewed from drive side)
Right R
Right R
Injection timing adjustment
Direction of rotation (viewed from drive side)
Right R
Right R
Injection order
1-5-3-6-
2-4
Pre-stroke
mm
4.8
4.75
4.85
Beginning of injection position
Governor side NO.1
Governor side NO.1
Difference between angles 1
Cal 1-5 deg. 60 59.5 60.5
Cal 1-5 deg. 60 59.5 60.5
Difference between angles 2
Cal 1-3 deg. 120 119.5 120.5
Cal 1-3 deg. 120 119.5 120.5
Difference between angles 3
Cal 1-6 deg. 180 179.5 180.5
Cal 1-6 deg. 180 179.5 180.5
Difference between angles 4
Cyl.1-2 deg. 240 239.5 240.5
Cyl.1-2 deg. 240 239.5 240.5
Difference between angles 5
Cal 1-4 deg. 300 299.5 300.5
Cal 1-4 deg. 300 299.5 300.5
Injection quantity adjustment
Adjusting point
-
Rack position
10.2
Pump speed
r/min
650
650
650
Each cylinder's injection qty
mm3/st.
138.5
135.1
141.9
Basic
*
Fixing the rack
*
Standard for adjustment of the maximum variation between cylinders
*
Injection quantity adjustment_02
Adjusting point
C
Rack position
6.5+-0.5
Pump speed
r/min
225
225
225
Each cylinder's injection qty
mm3/st.
17.5
14.9
20.1
Fixing the rack
*
Standard for adjustment of the maximum variation between cylinders
*
Injection quantity adjustment_03
Adjusting point
A
Rack position
R1(10.2)
Pump speed
r/min
650
650
650
Average injection quantity
mm3/st.
138.5
137.5
139.5
Basic
*
Fixing the lever
*
Boost pressure
kPa
27.3
27.3
Boost pressure
mmHg
205
205
Injection quantity adjustment_04
Adjusting point
D
Rack position
8.6
Pump speed
r/min
700
700
700
Average injection quantity
mm3/st.
101.5
98.5
104.5
Fixing the lever
*
Boost pressure
kPa
0
0
0
Boost pressure
mmHg
0
0
0
Injection quantity adjustment_05
Adjusting point
E
Rack position
-
Pump speed
r/min
100
100
100
Average injection quantity
mm3/st.
135
115
155
Fixing the lever
*
Boost pressure
kPa
0
0
0
Boost pressure
mmHg
0
0
0
Boost compensator adjustment
Pump speed
r/min
600
600
600
Rack position
8.6
Boost pressure
kPa
5.3
5.3
5.3
Boost pressure
mmHg
40
40
40
Boost compensator adjustment_02
Pump speed
r/min
600
600
600
Rack position
R1(10.2)
Boost pressure
kPa
14
14
14
Boost pressure
mmHg
105
105
105
Test data Ex:
Governor adjustment
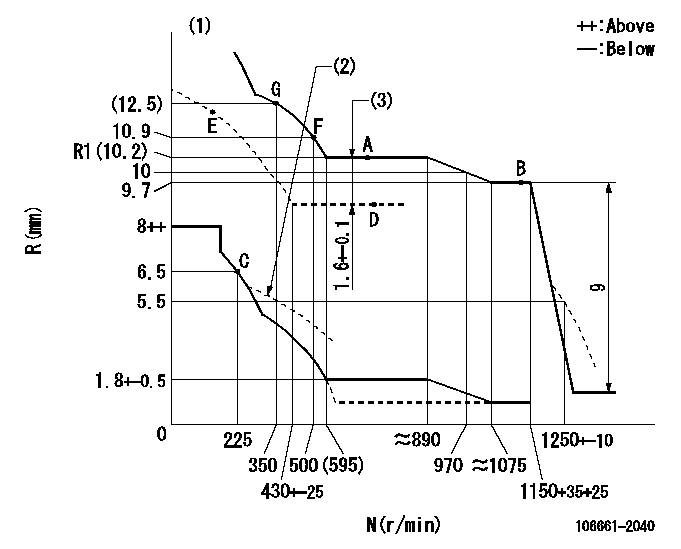
N:Pump speed
R:Rack position (mm)
(1)Boost compensator cancel stroke: BSL
(2)Damper spring setting: DL
(3)Boost compensator stroke
----------
BSL=1.6mm DL=6.2-0.2mm
----------
----------
BSL=1.6mm DL=6.2-0.2mm
----------
Timer adjustment

(1)Adjusting range
(2)Step response time
(N): Speed of the pump
(L): Load
(theta) Advance angle
(Srd1) Step response time 1
(Srd2) Step response time 2
1. Adjusting conditions for the variable timer
(1)Adjust the clearance between the pickup and the protrusion to L.
----------
L=1-0.2mm N2=800r/min C2=(8.8deg) t1=2.5--sec. t2=2.5--sec.
----------
N1=750++r/min P1=0kPa(0kgf/cm2) P2=392kPa(4kgf/cm2) C1=8.8+-0.3deg R01=0/4load R02=4/4load
----------
L=1-0.2mm N2=800r/min C2=(8.8deg) t1=2.5--sec. t2=2.5--sec.
----------
N1=750++r/min P1=0kPa(0kgf/cm2) P2=392kPa(4kgf/cm2) C1=8.8+-0.3deg R01=0/4load R02=4/4load
Speed control lever angle

F:Full speed
----------
----------
a=15.5deg+-5deg
----------
----------
a=15.5deg+-5deg
0000000901

F:Full load
I:Idle
(1)Stopper bolt setting
----------
----------
a=28deg+-5deg b=31deg+-3deg
----------
----------
a=28deg+-5deg b=31deg+-3deg
Stop lever angle
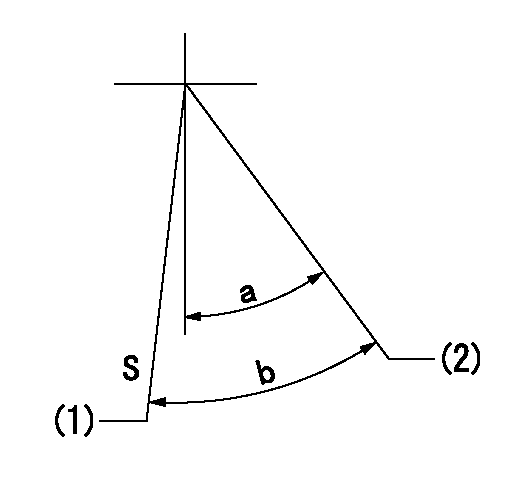
S:Stop the pump.
(1)Rack position = aa
(2)Free (at shipping)
----------
aa=3.4-0.5mm
----------
a=35.5deg+-5deg b=38.5deg+7deg-5deg
----------
aa=3.4-0.5mm
----------
a=35.5deg+-5deg b=38.5deg+7deg-5deg
0000001501 RACK SENSOR

V1:Supply voltage
V2f:Full side output voltage
V2i:Idle side output voltage
(A) Black
(B) Yellow
(C) Red
(D) Trimmer
(E): Shaft
(F) Nut
(G) Load lever
1. Load sensor adjustment
(1)Connect as shown in the above diagram and apply supply voltage V1.
(2)Hold the load lever (G) against the full side.
(3)Turn the shaft so that the voltage between (A) and (B) is V2.
(4)Hold the load lever (G) against the idle side.
(5)Adjust (D) so that the voltage between (A) and (B) is V2i.
(6)Repeat the above adjustments.
(7)Tighten the nut (F) at the point satisfying the standards.
(8)Hold the load lever against the full side stopper and the idle side stopper.
(9)At this time, confirm that the full side output voltage is V2f and the idle side output voltage is V2i.
----------
V1=5+-0.02V V2f=0.15+0.03V V2i=2.35-0.03V
----------
----------
V1=5+-0.02V V2f=0.15+0.03V V2i=2.35-0.03V
----------
0000001601 MICRO SWITCH
Adjustment of the micro-switch
Adjust the bolt to obtain the following lever position when the micro-switch is ON.
(1)Speed N1
(2)Rack position Ra
----------
N1=325+-5r/min Ra=6.2mm
----------
----------
N1=325+-5r/min Ra=6.2mm
----------
Timing setting

(1)Pump vertical direction
(2)Coupling's key groove position at No 1 cylinder's beginning of injection
(3)B.T.D.C.: aa
(4)-
----------
aa=11deg
----------
a=(7deg)
----------
aa=11deg
----------
a=(7deg)
Information:
The lubrication system consists of a sump (oil pan), oil pump, oil cooler and oil filter. The engine contains an oil manifold and oil passages to direct lubricant to the various components.The oil pump draws lubricant from the sump and forces it through the oil cooler, oil filter, and then into the oil manifold. Oil flows through connecting passages to lubricate the engine components. A regulating valve in the pump body controls the maximum pressure of the oil from the pump. When the engine is started, the lubricating oil in the oil pan is cool (thick). This cool viscous oil does not flow immediately through the oil cooler and oil filter. This cool oil forces bypass valves, in the oil cooler and oil filter base, to open allowing an unrestricted oil to flow through the engine.As oil temperature increases, oil viscosity and pressure decrease and the oil filter bypass valve closes. Now, only filtered oil is delivered to the engine components. Oil temperature continues to increase and the oil cooler bypass valve closes. Oil now flows through the oil cooler and oil filter before reaching the engine components.A contaminated or restricted oil filter element will not prevent lubricating oil from being delivered to the engine components. The oil filter bypass valve will open, allowing oil to bypass the element.An oil manifold, cast into the cylinder block, directs lubricant to the main bearings, valve rocker arm shafts, camshaft journals, and the camshaft idler (drive) gears.Oil spray orifices in the cylinder block spray oil on the underside of the pistons. This cools the pistons and provides lubricant for the piston pins, cylinder walls and piston rings.The connecting rod bearings receive oil through drilled passages in the crankshaft between the main bearing journals and connecting rod journals.When the engine is warm and running at rated speed, the oil pressure gauge should register in the "operating range". A lower pressure reading is normal at idling speeds.Many engines are equipped with an auxiliary or remote mounted bypass filter system. This system must be connected so part of the oil continuously circulates through the bypass filter, from the crankcase lubricating oil pump. An orifice on the outlet or clean side of the filter restricts the flow of oil through the bypass filter so full oil pressure is available to all parts of the engine. Filtered oil from the bypass filter is returned to the crankcase sump. Because of the additional oil capacity, extended change intervals can be established. See Lubrication Chart. The Bypass filter should never be used in place of the factory installed full flow filter.