Information injection-pump assembly
ZEXEL
106661-0660
1066610660
NISSAN-DIESEL
1670096108
1670096108
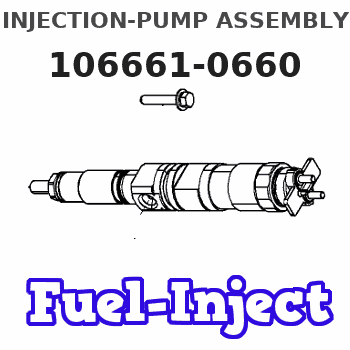
Rating:
Service parts 106661-0660 INJECTION-PUMP ASSEMBLY:
1.
_
3.
GOVERNOR
7.
COUPLING PLATE
8.
_
9.
_
11.
Nozzle and Holder
16600-96003
12.
Open Pre:MPa(Kqf/cm2)
22.6{230}
15.
NOZZLE SET
Include in #1:
106661-0660
as INJECTION-PUMP ASSEMBLY
Cross reference number
ZEXEL
106661-0660
1066610660
NISSAN-DIESEL
1670096108
1670096108
Zexel num
Bosch num
Firm num
Name
Calibration Data:
Adjustment conditions
Test oil
1404 Test oil ISO4113 or {SAEJ967d}
1404 Test oil ISO4113 or {SAEJ967d}
Test oil temperature
degC
40
40
45
Nozzle and nozzle holder
105780-8140
Bosch type code
EF8511/9A
Nozzle
105780-0000
Bosch type code
DN12SD12T
Nozzle holder
105780-2080
Bosch type code
EF8511/9
Opening pressure
MPa
17.2
Opening pressure
kgf/cm2
175
Injection pipe
Outer diameter - inner diameter - length (mm) mm 8-3-600
Outer diameter - inner diameter - length (mm) mm 8-3-600
Tester oil delivery pressure
kPa
157
157
157
Tester oil delivery pressure
kgf/cm2
1.6
1.6
1.6
Direction of rotation (viewed from drive side)
Right R
Right R
Injection timing adjustment
Direction of rotation (viewed from drive side)
Right R
Right R
Injection order
1-4-2-6-
3-5
Pre-stroke
mm
3.65
3.6
3.7
Beginning of injection position
Drive side NO.1
Drive side NO.1
Difference between angles 1
Cal 1-4 deg. 60 59.5 60.5
Cal 1-4 deg. 60 59.5 60.5
Difference between angles 2
Cyl.1-2 deg. 120 119.5 120.5
Cyl.1-2 deg. 120 119.5 120.5
Difference between angles 3
Cal 1-6 deg. 180 179.5 180.5
Cal 1-6 deg. 180 179.5 180.5
Difference between angles 4
Cal 1-3 deg. 240 239.5 240.5
Cal 1-3 deg. 240 239.5 240.5
Difference between angles 5
Cal 1-5 deg. 300 299.5 300.5
Cal 1-5 deg. 300 299.5 300.5
Injection quantity adjustment
Adjusting point
A
Rack position
11.7
Pump speed
r/min
750
750
750
Average injection quantity
mm3/st.
139.4
137.4
141.4
Max. variation between cylinders
%
0
-4
4
Basic
*
Fixing the rack
*
Injection quantity adjustment_02
Adjusting point
B
Rack position
10.9
Pump speed
r/min
400
400
400
Average injection quantity
mm3/st.
114.6
112.6
116.6
Max. variation between cylinders
%
0
-4
4
Fixing the lever
*
Injection quantity adjustment_03
Adjusting point
C
Rack position
11.7
Pump speed
r/min
1000
1000
1000
Average injection quantity
mm3/st.
139.7
137.7
141.7
Max. variation between cylinders
%
0
-4
4
Fixing the rack
*
Injection quantity adjustment_04
Adjusting point
D
Rack position
11.7
Pump speed
r/min
1150
1150
1150
Average injection quantity
mm3/st.
138.8
136.8
140.8
Max. variation between cylinders
%
0
-4
4
Fixing the rack
*
Injection quantity adjustment_05
Adjusting point
E
Rack position
7.2+-0.5
Pump speed
r/min
200
200
200
Average injection quantity
mm3/st.
10.1
9.1
11.1
Max. variation between cylinders
%
0
-10
10
Fixing the rack
*
Boost compensator adjustment
Pump speed
r/min
400
400
400
Rack position
10.9
Boost pressure
kPa
33.3
33.3
33.3
Boost pressure
mmHg
205
205
205
Boost compensator adjustment_02
Pump speed
r/min
400
400
400
Rack position
11.7
Boost pressure
kPa
42.7
41.4
44
Boost pressure
mmHg
320
310
330
Timer adjustment
Pump speed
r/min
500+-50
Advance angle
deg.
0
0
0
Remarks
Start
Start
Timer adjustment_02
Pump speed
r/min
700
Advance angle
deg.
0.2
0.1
0.6
Timer adjustment_03
Pump speed
r/min
900
Advance angle
deg.
0.7
0.3
1
Timer adjustment_04
Pump speed
r/min
1150+50
Advance angle
deg.
2.2
2
2.8
Remarks
Finish
Finish
Test data Ex:
Governor adjustment
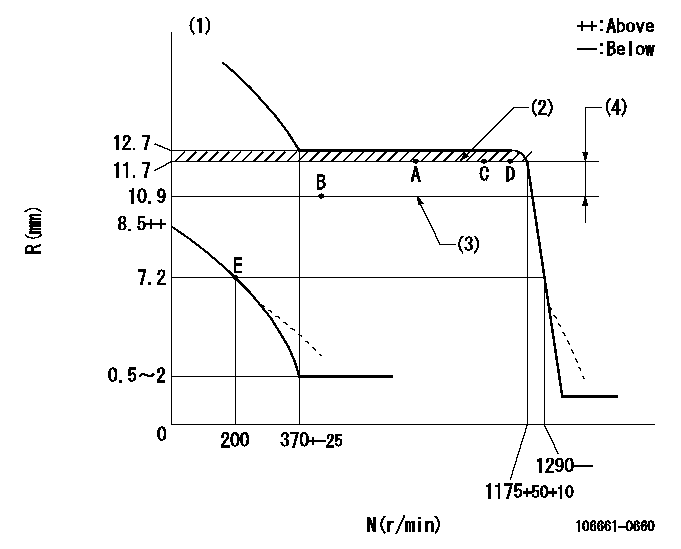
N:Pump speed
R:Rack position (mm)
(1)Beginning of damper spring operation: DL
(2)Boost pressure: not less than BP1
(3)Boost pressure: not exceeding BP2
(4)Boost compensator stroke
----------
DL=5.2+0.5mm BP1=50.7kPa(380mmHg) BP2=0kPa(0mmHg)
----------
----------
DL=5.2+0.5mm BP1=50.7kPa(380mmHg) BP2=0kPa(0mmHg)
----------
0000000901

F:Full load
I:Idle
(1)Set the idling position using the set screw.
----------
----------
a=13.5deg+-5deg b=23.5deg+-3deg
----------
----------
a=13.5deg+-5deg b=23.5deg+-3deg
Information:
Parts Location
Illustration 2 g01666016
Exploded view (1) 304-1120 Diesel Particulate Filter Gp (2) 308-4936 Bracket As (3) 308-4941 Clamp As (4) 277-4718 Clamp As (5) 3B-4508 Lockwasher (6) 5P-8245 Hard Washer (7) 6V-8149 Nut (8) 6V-3823 Bolt (9) 8T-4121 Hard Washer (10) 8T-4196 Bolt Installation Procedure
Diesel Particulate Filter Installation
Illustration 3 g01667275
(11) 241-9265 Muffler Clamp (16) Muffler Assembly (17) Bracket Assembly (18) Support Assembly (19) Exhaust Pipe Assembly (20) Clamp (21) Pipe Assembly (22) Bolt (23) Hard Washer (24) Bolt (25) Washer (26) Plate (27) Bolt (28) Hard Washer (29) Plate
Illustration 4 g01601993
(2) 308-4936 Bracket As (22) Bolt (23) Hard washer (24) Bolt (25) Washer (27) Bolt (28) Hard washer
Remove the existing muffler assembly (16) and bracket assembly (17). Set aside exhaust pipe assembly (19), clamp (20), three bolts (22), three hard washers (23), two bolts (24), two washers (25), three bolts (27), and three hard washers (28). These parts will be reused in later steps.
Reuse three bolts (22), and three hard washers (23) to secure the new 308-4936 Bracket As (2) to existing support assembly (18) .
Reuse two bolts (24), and two washers (25) to secure bracket assembly (2) to existing plate (26) .
Reuse three bolts (27), and three hard washers (28) to secure bracket assembly (2) to existing plate (29) .
Illustration 5 g01602054
(3) 308-4941 Clamp As (9) 8T-4121 Hard Washer (10) 8T-4196 Bolt
Install the two new 308-4941 Clamp As (3) by using four 8T-4196 Bolts (10), and 8T-4121 Hard Washers (9). Loosely secure the four bolts so that the clamp assemblies are adjustable. Refer to Illustration 5.
Illustration 6 g01602115
(1) 304-1120 Diesel Particulate Filter Gp (30) Inlet module tube
Install the new 304-1120 Diesel Particulate Filter Gp (1) on top of clamp assemblies (3). Make sure that inlet module tube (30) fits into existing pipe assembly (21). Use a new 241-9265 Muffler Clamp (11) to secure the joint. Refer to Illustration 6.
Illustration 7 g01601954
(4) 277-4718 Clamp As (5) 3B-4508 Lockwasher (6) 5P-8245 Hard Washer (7) 6V-8149 Nut (8) 6V-3823 Bolt (31) Outlet module tube
Once you have the pipe assembly installed properly, tighten the two bottom clamp assemblies (3). Install the new 277-4718 Clamp As (4) by using the four 5P-8245 Hard Washers (6), and four 6V-3823 Bolts (8). Use the four 3B-4508 Lockwashers (5), and four 6V-8149 Nuts (7) on the clamp assembly (3) side. Refer to Illustration 7.
Install the existing exhaust pipe assembly (19) to the outlet module tube of the diesel particulate filter. Secure the connection with existing clamp (20) .
Reconnect the drain lines.Exhaust Monitor Installation
Refer to Special Instruction, REHS5606, "Installation and Operation of the Caterpillar Diesel Particulate Filter (DPF) and the Diagnostic Module for Non-Road Machine Applications (Non-California Applications)" for information regarding the installation and the operation of the exhaust monitor.The exhaust
Illustration 2 g01666016
Exploded view (1) 304-1120 Diesel Particulate Filter Gp (2) 308-4936 Bracket As (3) 308-4941 Clamp As (4) 277-4718 Clamp As (5) 3B-4508 Lockwasher (6) 5P-8245 Hard Washer (7) 6V-8149 Nut (8) 6V-3823 Bolt (9) 8T-4121 Hard Washer (10) 8T-4196 Bolt Installation Procedure
Diesel Particulate Filter Installation
Illustration 3 g01667275
(11) 241-9265 Muffler Clamp (16) Muffler Assembly (17) Bracket Assembly (18) Support Assembly (19) Exhaust Pipe Assembly (20) Clamp (21) Pipe Assembly (22) Bolt (23) Hard Washer (24) Bolt (25) Washer (26) Plate (27) Bolt (28) Hard Washer (29) Plate
Illustration 4 g01601993
(2) 308-4936 Bracket As (22) Bolt (23) Hard washer (24) Bolt (25) Washer (27) Bolt (28) Hard washer
Remove the existing muffler assembly (16) and bracket assembly (17). Set aside exhaust pipe assembly (19), clamp (20), three bolts (22), three hard washers (23), two bolts (24), two washers (25), three bolts (27), and three hard washers (28). These parts will be reused in later steps.
Reuse three bolts (22), and three hard washers (23) to secure the new 308-4936 Bracket As (2) to existing support assembly (18) .
Reuse two bolts (24), and two washers (25) to secure bracket assembly (2) to existing plate (26) .
Reuse three bolts (27), and three hard washers (28) to secure bracket assembly (2) to existing plate (29) .
Illustration 5 g01602054
(3) 308-4941 Clamp As (9) 8T-4121 Hard Washer (10) 8T-4196 Bolt
Install the two new 308-4941 Clamp As (3) by using four 8T-4196 Bolts (10), and 8T-4121 Hard Washers (9). Loosely secure the four bolts so that the clamp assemblies are adjustable. Refer to Illustration 5.
Illustration 6 g01602115
(1) 304-1120 Diesel Particulate Filter Gp (30) Inlet module tube
Install the new 304-1120 Diesel Particulate Filter Gp (1) on top of clamp assemblies (3). Make sure that inlet module tube (30) fits into existing pipe assembly (21). Use a new 241-9265 Muffler Clamp (11) to secure the joint. Refer to Illustration 6.
Illustration 7 g01601954
(4) 277-4718 Clamp As (5) 3B-4508 Lockwasher (6) 5P-8245 Hard Washer (7) 6V-8149 Nut (8) 6V-3823 Bolt (31) Outlet module tube
Once you have the pipe assembly installed properly, tighten the two bottom clamp assemblies (3). Install the new 277-4718 Clamp As (4) by using the four 5P-8245 Hard Washers (6), and four 6V-3823 Bolts (8). Use the four 3B-4508 Lockwashers (5), and four 6V-8149 Nuts (7) on the clamp assembly (3) side. Refer to Illustration 7.
Install the existing exhaust pipe assembly (19) to the outlet module tube of the diesel particulate filter. Secure the connection with existing clamp (20) .
Reconnect the drain lines.Exhaust Monitor Installation
Refer to Special Instruction, REHS5606, "Installation and Operation of the Caterpillar Diesel Particulate Filter (DPF) and the Diagnostic Module for Non-Road Machine Applications (Non-California Applications)" for information regarding the installation and the operation of the exhaust monitor.The exhaust