Information injection-pump assembly
BOSCH
F 019 Z10 194
f019z10194
ZEXEL
106651-2530
1066512530

Rating:
Service parts 106651-2530 INJECTION-PUMP ASSEMBLY:
1.
_
7.
COUPLING PLATE
8.
_
9.
_
11.
Nozzle and Holder
12.
Open Pre:MPa(Kqf/cm2)
17.7{180}/21.6{220}
15.
NOZZLE SET
Include in #1:
106651-2530
as INJECTION-PUMP ASSEMBLY
Cross reference number
BOSCH
F 019 Z10 194
f019z10194
ZEXEL
106651-2530
1066512530
Zexel num
Bosch num
Firm num
Name
Calibration Data:
Adjustment conditions
Test oil
1404 Test oil ISO4113 or {SAEJ967d}
1404 Test oil ISO4113 or {SAEJ967d}
Test oil temperature
degC
40
40
45
Nozzle and nozzle holder
105780-8140
Bosch type code
EF8511/9A
Nozzle
105780-0000
Bosch type code
DN12SD12T
Nozzle holder
105780-2080
Bosch type code
EF8511/9
Opening pressure
MPa
17.2
Opening pressure
kgf/cm2
175
Injection pipe
Outer diameter - inner diameter - length (mm) mm 8-3-600
Outer diameter - inner diameter - length (mm) mm 8-3-600
Overflow valve
131424-4420
Overflow valve opening pressure
kPa
157
123
191
Overflow valve opening pressure
kgf/cm2
1.6
1.25
1.95
Tester oil delivery pressure
kPa
157
157
157
Tester oil delivery pressure
kgf/cm2
1.6
1.6
1.6
Direction of rotation (viewed from drive side)
Right R
Right R
Injection timing adjustment
Direction of rotation (viewed from drive side)
Right R
Right R
Injection order
1-5-3-6-
2-4
Pre-stroke
mm
5.1
5.05
5.15
Beginning of injection position
Governor side NO.1
Governor side NO.1
Difference between angles 1
Cal 1-5 deg. 60 59.5 60.5
Cal 1-5 deg. 60 59.5 60.5
Difference between angles 2
Cal 1-3 deg. 120 119.5 120.5
Cal 1-3 deg. 120 119.5 120.5
Difference between angles 3
Cal 1-6 deg. 180 179.5 180.5
Cal 1-6 deg. 180 179.5 180.5
Difference between angles 4
Cyl.1-2 deg. 240 239.5 240.5
Cyl.1-2 deg. 240 239.5 240.5
Difference between angles 5
Cal 1-4 deg. 300 299.5 300.5
Cal 1-4 deg. 300 299.5 300.5
Injection quantity adjustment
Adjusting point
-
Rack position
12
Pump speed
r/min
700
700
700
Each cylinder's injection qty
mm3/st.
137.4
134
140.8
Basic
*
Fixing the rack
*
Standard for adjustment of the maximum variation between cylinders
*
Injection quantity adjustment_02
Adjusting point
C
Rack position
6.3+-0.5
Pump speed
r/min
225
225
225
Each cylinder's injection qty
mm3/st.
18.6
15.9
21.3
Fixing the rack
*
Standard for adjustment of the maximum variation between cylinders
*
Injection quantity adjustment_03
Adjusting point
A
Rack position
R1(12)
Pump speed
r/min
700
700
700
Average injection quantity
mm3/st.
137.4
136.4
138.4
Basic
*
Fixing the lever
*
Boost pressure
kPa
52
52
Boost pressure
mmHg
390
390
Injection quantity adjustment_04
Adjusting point
B
Rack position
R1(12)
Pump speed
r/min
1100
1100
1100
Average injection quantity
mm3/st.
136.6
132.6
140.6
Difference in delivery
mm3/st.
8
8
8
Fixing the lever
*
Boost pressure
kPa
52
52
Boost pressure
mmHg
390
390
Injection quantity adjustment_05
Adjusting point
D
Rack position
11.5
Pump speed
r/min
500
500
500
Average injection quantity
mm3/st.
121
117.4
124.6
Fixing the lever
*
Boost pressure
kPa
29.3
28
30.6
Boost pressure
mmHg
220
210
230
Injection quantity adjustment_06
Adjusting point
E
Rack position
-
Pump speed
r/min
100
100
100
Average injection quantity
mm3/st.
110
90
130
Fixing the lever
*
Boost pressure
kPa
0
0
0
Boost pressure
mmHg
0
0
0
Boost compensator adjustment
Pump speed
r/min
600
600
600
Rack position
R2(R1-2)
Boost pressure
kPa
4
4
4
Boost pressure
mmHg
30
30
30
Boost compensator adjustment_02
Pump speed
r/min
600
600
600
Rack position
11.5
Boost pressure
kPa
29.3
28
30.6
Boost pressure
mmHg
220
210
230
Boost compensator adjustment_03
Pump speed
r/min
600
600
600
Rack position
R1(12)
Boost pressure
kPa
39.7
33
46.4
Boost pressure
mmHg
290
240
340
Timer adjustment
Pump speed
r/min
450--
Advance angle
deg.
0
0
0
Remarks
Start
Start
Timer adjustment_02
Pump speed
r/min
400
Advance angle
deg.
0.5
Timer adjustment_03
Pump speed
r/min
720
Advance angle
deg.
2.5
2
3
Remarks
Finish
Finish
Test data Ex:
Governor adjustment
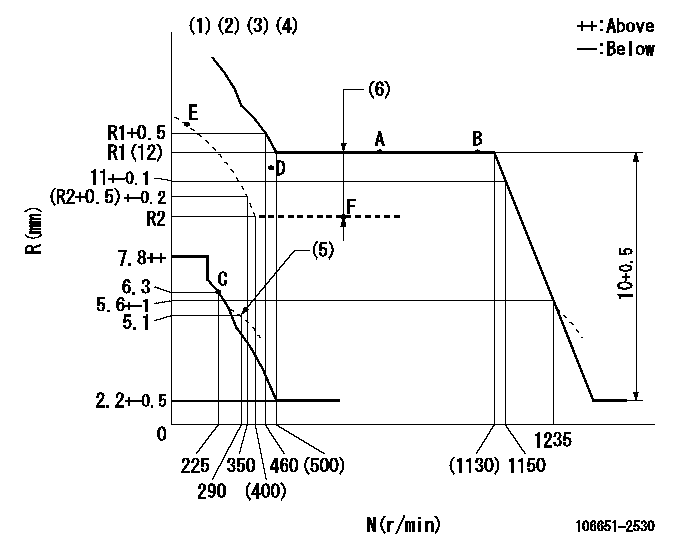
N:Pump speed
R:Rack position (mm)
(1)Lever ratio: RT
(2)Target shim dimension: TH
(3)Tolerance for racks not indicated: +-0.05mm.
(4)Boost compensator cancel stroke: BSL
(5)Damper spring setting
(6)Boost compensator stroke: BCL
----------
RT=1 TH=2.8mm BSL=2mm BCL=2+-0.1mm
----------
----------
RT=1 TH=2.8mm BSL=2mm BCL=2+-0.1mm
----------
Speed control lever angle

F:Full speed
----------
----------
a=8.5deg+-5deg
----------
----------
a=8.5deg+-5deg
0000000901

F:Full load
I:Idle
(1)Stopper bolt setting
----------
----------
a=21deg+-5deg b=36deg+-3deg
----------
----------
a=21deg+-5deg b=36deg+-3deg
Stop lever angle
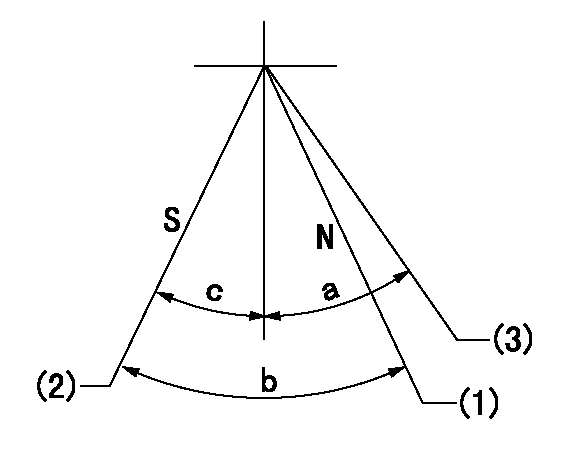
N:Engine manufacturer's normal use
S:Stop the pump.
(1)Rack position = aa
(2)Rack position = bb, set the stopper bolt.
(3)Free (at delivery)
----------
aa=14mm bb=4.9-0.5mm
----------
a=(35.5deg) b=25.5deg+-5deg c=0deg+7deg-5deg
----------
aa=14mm bb=4.9-0.5mm
----------
a=(35.5deg) b=25.5deg+-5deg c=0deg+7deg-5deg
0000001501 MICRO SWITCH
Adjustment of the micro-switch
Adjust the bolt to obtain the following lever position when the micro-switch is ON.
(1)Speed N1
(2)Rack position Ra
----------
N1=325r/min Ra=6+-0.1mm
----------
----------
N1=325r/min Ra=6+-0.1mm
----------
Timing setting

(1)Pump vertical direction
(2)Coupling's key groove position at No 1 cylinder's beginning of injection
(3)-
(4)-
----------
----------
a=(6deg)
----------
----------
a=(6deg)
Information:
ACTION REQUIRED
Refer to the attached Rework Procedure.
SERVICE CLAIM ALLOWANCES
Product smu/age whichever comes first Caterpillar Dealer Suggested Customer Suggested
Parts % Labor Hrs% Parts % Labor Hrs% Parts % Labor Hrs%
0-2000 hrs,
0-24 mo 100.0% 100.0% 0.0% 0.0% 0.0% 0.0%
This is a 2.0-hour job
PARTS DISPOSITION
Handle the parts in accordance with your Warranty Bulletin on warranty parts handling.
Rework Procedure
Use the procedures on the following pages in order to apply the updates to your machine.
- Park the machine on a firm, level surface.
- Fully retract and lower the boom.
- Place the travel select lever in the (N) NEUTRAL position.
- Apply Park Brake.
- Shut the engine off and remove the key from the MAIN switch located inside the engine compartment.
- Properly disconnect the battery.
- Place a Do Not Operate Tag on both the ignition key-switch and the steering wheel, stating that the machine should not be operated.
- Allow the engine area and antifreeze to cool down.
- Remove the cab rear cover.
- Use all applicable safety precautions while working on, around or under any machinery.
1. Locate DEF coolant supply hose (1) and DEF coolant return hose (2) on the engine. Refer to Image1.2.1.
Image1.2.1
2. Trace the routing of DEF coolant supply hose (1) on the engine to DEF coolant control valve (3) located in the middle of the frame. Refer to Image1.2.1 and 1.3.1.
Image1.3.1
3. Trace the routing of DEF coolant return hose (2) from the engine to DEF tank (4) located behind rear of the cab. Refer to Image1.2.1 and 1.4.1.
Image1.4.1
4. If the routing of DEF coolant supply hose (1) and DEF coolant return hose (2) are found to be correct, remount the cab rear cover and place the unit back in service.
5. If the routing of DEF coolant line (1) and DEF coolant return hose (2) are found to be incorrect, please continue the next steps to correct the DEF coolant line installation.
6. Remove all the cable straps that securing the two DEF coolant lines together or to other hoses. Refer to Image1.6.1. Some of the parts have been removed for clarity. Cut the 610cm of 5P-0767 Hose into two pieces: 330cm and 280cm.
Image1.6.1
7. Taking all precautions to minimize and contain any antifreeze spillage, disconnect DEF coolant supply hose (1) from DEF coolant control valve (3) and from the engine side DEF coolant supply port. The hose will not be reused. Retain the hose clamps for reuse. Refer to Image1.2.1 and 1.4.1.
8. Disconnect DEF coolant return hose (2) from DEF coolant tank (4) and from the engine side DEF coolant return port. The hose will not be reused. Retain the hose clamps for reuse. Refer to Image1.2.1 and 1.6.1.
9. Identify the new DEF coolant supply hose. It is the shorter