Information injection-pump assembly
BOSCH
9 460 614 787
9460614787
ZEXEL
104780-9350
1047809350
NISSAN-DIESEL
167003S302
167003s302
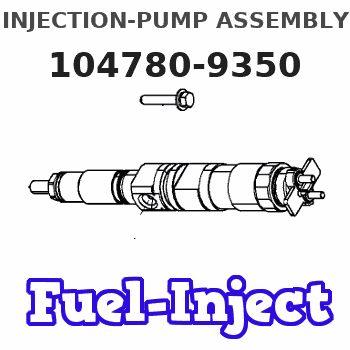
Rating:
Cross reference number
BOSCH
9 460 614 787
9460614787
ZEXEL
104780-9350
1047809350
NISSAN-DIESEL
167003S302
167003s302
Zexel num
Bosch num
Firm num
Name
104780-9350
9 460 614 787
167003S302 NISSAN-DIESEL
INJECTION-PUMP ASSEMBLY
TD25 K
TD25 K
Calibration Data:
Adjustment conditions
Test oil
1404 Test oil ISO4113orSAEJ967d
1404 Test oil ISO4113orSAEJ967d
Test oil temperature
degC
45
45
50
Nozzle
105780-0060
Bosch type code
NP-DN0SD1510
Nozzle holder
105780-2150
Opening pressure
MPa
13
13
13.3
Opening pressure
kgf/cm2
133
133
136
Injection pipe
157805-7320
Injection pipe
Inside diameter - outside diameter - length (mm) mm 2-6-450
Inside diameter - outside diameter - length (mm) mm 2-6-450
Joint assembly
157641-4720
Tube assembly
157641-4020
Transfer pump pressure
kPa
20
20
20
Transfer pump pressure
kgf/cm2
0.2
0.2
0.2
Direction of rotation (viewed from drive side)
Right R
Right R
Injection timing adjustment
Pump speed
r/min
1100
1100
1100
Average injection quantity
mm3/st.
44.4
43.9
44.9
Difference in delivery
mm3/st.
3.5
Basic
*
Oil temperature
degC
50
48
52
Injection timing adjustment_02
Pump speed
r/min
500
500
500
Average injection quantity
mm3/st.
41.3
38.3
44.3
Oil temperature
degC
48
46
50
Injection timing adjustment_03
Pump speed
r/min
1100
1100
1100
Average injection quantity
mm3/st.
44.4
43.4
45.4
Difference in delivery
mm3/st.
4
Basic
*
Oil temperature
degC
50
48
52
Injection timing adjustment_04
Pump speed
r/min
2150
2150
2150
Average injection quantity
mm3/st.
41.7
38.2
45.2
Oil temperature
degC
52
50
54
Injection quantity adjustment
Pump speed
r/min
2500
2500
2500
Average injection quantity
mm3/st.
14.9
12.9
16.9
Basic
*
Oil temperature
degC
55
52
58
Injection quantity adjustment_02
Pump speed
r/min
2700
2700
2700
Average injection quantity
mm3/st.
5
Oil temperature
degC
55
52
58
Injection quantity adjustment_03
Pump speed
r/min
2500
2500
2500
Average injection quantity
mm3/st.
14.9
11.9
17.9
Basic
*
Oil temperature
degC
55
52
58
Governor adjustment
Pump speed
r/min
375
375
375
Average injection quantity
mm3/st.
7.1
5.1
9.1
Difference in delivery
mm3/st.
2
Basic
*
Oil temperature
degC
48
46
50
Governor adjustment_02
Pump speed
r/min
375
375
375
Average injection quantity
mm3/st.
7.1
4.6
9.6
Difference in delivery
mm3/st.
2.5
Basic
*
Oil temperature
degC
48
46
50
Timer adjustment
Pump speed
r/min
100
100
100
Average injection quantity
mm3/st.
75
60
95
Basic
*
Oil temperature
degC
48
46
50
Remarks
Full
Full
Timer adjustment_02
Pump speed
r/min
100
100
100
Average injection quantity
mm3/st.
70
55
90
Oil temperature
degC
48
46
50
Remarks
Full
Full
Speed control lever angle
Pump speed
r/min
375
375
375
Average injection quantity
mm3/st.
0
0
0
Oil temperature
degC
48
46
50
Remarks
Magnet OFF at idling position
Magnet OFF at idling position
0000000901
Pump speed
r/min
1100
1100
1100
Overflow quantity with S/T ON
cm3/min
440
310
570
Oil temperature
degC
50
48
52
Stop lever angle
Pump speed
r/min
1100
1100
1100
Pressure with S/T ON
kPa
510
471
549
Pressure with S/T ON
kgf/cm2
5.2
4.8
5.6
Pressure with S/T OFF
kPa
432
403
461
Pressure with S/T OFF
kgf/cm2
4.4
4.1
4.7
Basic
*
Oil temperature
degC
50
48
52
Remarks
OFF
OFF
Stop lever angle_02
Pump speed
r/min
1100
1100
1100
Pressure with S/T OFF
kPa
432
393
471
Pressure with S/T OFF
kgf/cm2
4.4
4
4.8
Basic
*
Oil temperature
degC
50
48
52
Stop lever angle_03
Pump speed
r/min
2150
2150
2150
Pressure with S/T OFF
kPa
657
618
696
Pressure with S/T OFF
kgf/cm2
6.7
6.3
7.1
Oil temperature
degC
52
50
54
0000001101
Pump speed
r/min
1100
1100
1100
Timer stroke with S/T ON
mm
3.8
3.4
4.2
Timer stroke with S/T OFF
mm
2
1.8
2.2
Basic
*
Oil temperature
degC
50
48
52
Remarks
OFF
OFF
_02
Pump speed
r/min
700
700
700
Timer stroke with S/T OFF
mm
0.8
Oil temperature
degC
50
48
52
_03
Pump speed
r/min
1100
1100
1100
Timer stroke with S/T ON
mm
3.8
3.3
4.3
Timer stroke with S/T OFF
mm
2
1.7
2.3
Basic
*
Oil temperature
degC
50
48
52
_04
Pump speed
r/min
2150
2150
2150
Timer stroke with S/T ON
mm
7.8
7.3
8.2
Timer stroke with S/T OFF
mm
6.9
6.3
7.5
Oil temperature
degC
52
50
54
0000001201
Max. applied voltage
V
8
8
8
Test voltage
V
13
12
14
0000001401
Pump speed
r/min
1100
1100
1100
Average injection quantity
mm3/st.
30
29.5
30.5
Timer stroke TA
mm
1.7
1.7
1.7
Timer stroke variation dT
mm
0.3
0.1
0.5
Basic
*
Oil temperature
degC
50
48
52
Remarks
OFF
OFF
_02
Pump speed
r/min
1100
1100
1100
Average injection quantity
mm3/st.
30
29
31
Timer stroke TA
mm
1.7
1.7
1.7
Timer stroke variation dT
mm
0.3
0
0.6
Basic
*
Oil temperature
degC
50
48
52
_03
Pump speed
r/min
1100
1100
1100
Average injection quantity
mm3/st.
17
14.5
19.5
Timer stroke TA
mm
1.1
1.1
1.1
Timer stroke variation dT
mm
0.9
0.5
1.3
Oil temperature
degC
50
48
52
Timing setting
K dimension
mm
3.3
3.2
3.4
KF dimension
mm
5.8
5.7
5.9
MS dimension
mm
1.5
1.4
1.6
Pre-stroke
mm
0.1
0.08
0.12
Control lever angle alpha
deg.
55.5
51.5
59.5
Control lever angle beta
deg.
36
31
41
Test data Ex:
0000001801 POTENTIOMETER ADJUSTMENT
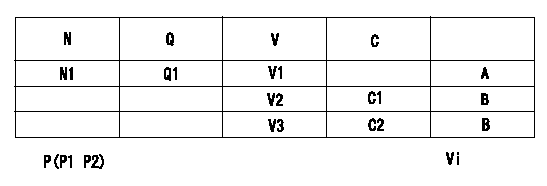
Adjusting method (dummy bolt method)
1. Determine the control lever position at N1 (r/min) and Q1 (mm3/st), hold the dummy bolt against the lever and then fix.
2. When adjusting the potentiometer, position the control lever so that it contacts the dummy bolt. Then assemble the potentiometer so that the output voltage is V1.
3. After completion, remove the dummy bolt and confirm that the potentiometer is within the specifications.
A:Adjusting point
B:Checking point
P:Boost pressure
Vi:Applied voltage
N:Pump speed
Q:Injection quantity
V:Output voltage
C:Angle of the control lever
C1:Idle
C2:Full-speed
----------
N1=1075r/min Q1=23.3+-1.0cm3/1,000st V1=5.64+-0.03V V2=(1.34)V V3=Above9.7V Vi=10V P1=0kPa P2=0mmHg
----------
V1=5.64+-0.03V V2=(1.34)V V3=Above 9.7V Vi=10V P1=0kPa P2=0mmHg N1=1075r/min Q1=23.3+-1.0cm3/1,000st
----------
N1=1075r/min Q1=23.3+-1.0cm3/1,000st V1=5.64+-0.03V V2=(1.34)V V3=Above9.7V Vi=10V P1=0kPa P2=0mmHg
----------
V1=5.64+-0.03V V2=(1.34)V V3=Above 9.7V Vi=10V P1=0kPa P2=0mmHg N1=1075r/min Q1=23.3+-1.0cm3/1,000st
Information:
Procedure
Note: Prior to performing the analysis with the APC, be sure to read and understand all the interferences listed in the "Interferences Inherent In the Fuel Sample" section of this document. Ensure that all precautions have been taken to minimize the affect of skewed results due to improper sampling, handling, or preparation.
Obtain the fuel sample to be analyzed in an appropriate sample bottle as described in the "Fuel Sample Preparation" section. Manually or mechanically shake the sample vigorously for 30 seconds. When manually shaking a sample, ensure thorough mixing of the sample by turning the bottle so that the lid is facing downward. Shake by moving the wrist and/or forearm up and down as rapidly as is comfortable for the 30 seconds.Note: Degassing samples can be accomplished with either the use of an ultrasonic bath or with the use of a vacuum pump.
Immediately degas the sample, by partially opening the lid to the bottle and placing the sample upright in the degassing unit. Perform only one of the degassing methods. An ultrasonic bath is the best method for degassing a sample. An ultrasonic bath takes the least amount of time minimizing the impact of particle settling.Note: The purpose of partially unscrewing or opening the lid is to promote quick degassing of the sample. Air bubbles to remaining near the surface of the sample following the degassing process are acceptable.
Illustration 5 g01741117
If an ultrasonic bath is unavailable, an alternative method of degassing the sample is with the use of a 1U-5718 Oil Sampling Vacuum Pump. Ensure the 1U-5718 Oil Sampling Vacuum Pump is clean before beginning the degas process.Note: Rubber is to be placed over the hole of the tubing for the pump to develop and hold the required vacuum.
With the sample to be analyzed in the sample bottle, thread the bottle into the bottom of the 1U-5718 Oil Sampling Vacuum Group. Operate the pump to create a vacuum. Maintain the vacuum until all air bubbles have risen to the surface of the sample and dissipated.
If an ultrasonic bath or a vacuum pump is not available, the sample can degas naturally. Degas the sample by setting the sample on a flat surface and leaving the sample undisturbed. If the APC performs a flushing cycle, let the sample sit for 15 seconds. If the APC does not perform a flushing cycle, such as the 293-8413 HYDAC Contamination Monitor Group or the 383-4255 HYDAC Contamination Monitor Group, let the sample sit for 30 seconds. Proceed to the "Sample Processing" section.Sample Processing
Remove the lid from the sample bottle. Immediately begin the processing of the sample on the APC that has been prepared according to the "Fuel Sample Preparation" section.Note: If more than 45 seconds elapse after the shaking of the sample, the procedure shall be restarted with shaking of the sample in "Fuel Sample Preparation" section. Shaking the sample ensures that suspended particles do not settle to the bottom of the sample, causing inaccurate particle count results.
Obtain the particle count results
Note: Prior to performing the analysis with the APC, be sure to read and understand all the interferences listed in the "Interferences Inherent In the Fuel Sample" section of this document. Ensure that all precautions have been taken to minimize the affect of skewed results due to improper sampling, handling, or preparation.
Obtain the fuel sample to be analyzed in an appropriate sample bottle as described in the "Fuel Sample Preparation" section. Manually or mechanically shake the sample vigorously for 30 seconds. When manually shaking a sample, ensure thorough mixing of the sample by turning the bottle so that the lid is facing downward. Shake by moving the wrist and/or forearm up and down as rapidly as is comfortable for the 30 seconds.Note: Degassing samples can be accomplished with either the use of an ultrasonic bath or with the use of a vacuum pump.
Immediately degas the sample, by partially opening the lid to the bottle and placing the sample upright in the degassing unit. Perform only one of the degassing methods. An ultrasonic bath is the best method for degassing a sample. An ultrasonic bath takes the least amount of time minimizing the impact of particle settling.Note: The purpose of partially unscrewing or opening the lid is to promote quick degassing of the sample. Air bubbles to remaining near the surface of the sample following the degassing process are acceptable.
Illustration 5 g01741117
If an ultrasonic bath is unavailable, an alternative method of degassing the sample is with the use of a 1U-5718 Oil Sampling Vacuum Pump. Ensure the 1U-5718 Oil Sampling Vacuum Pump is clean before beginning the degas process.Note: Rubber is to be placed over the hole of the tubing for the pump to develop and hold the required vacuum.
With the sample to be analyzed in the sample bottle, thread the bottle into the bottom of the 1U-5718 Oil Sampling Vacuum Group. Operate the pump to create a vacuum. Maintain the vacuum until all air bubbles have risen to the surface of the sample and dissipated.
If an ultrasonic bath or a vacuum pump is not available, the sample can degas naturally. Degas the sample by setting the sample on a flat surface and leaving the sample undisturbed. If the APC performs a flushing cycle, let the sample sit for 15 seconds. If the APC does not perform a flushing cycle, such as the 293-8413 HYDAC Contamination Monitor Group or the 383-4255 HYDAC Contamination Monitor Group, let the sample sit for 30 seconds. Proceed to the "Sample Processing" section.Sample Processing
Remove the lid from the sample bottle. Immediately begin the processing of the sample on the APC that has been prepared according to the "Fuel Sample Preparation" section.Note: If more than 45 seconds elapse after the shaking of the sample, the procedure shall be restarted with shaking of the sample in "Fuel Sample Preparation" section. Shaking the sample ensures that suspended particles do not settle to the bottom of the sample, causing inaccurate particle count results.
Obtain the particle count results
Have questions with 104780-9350?
Group cross 104780-9350 ZEXEL
Dpico
Nissan-Diesel
Dpico
Nissan-Diesel
104780-9350
9 460 614 787
167003S302
INJECTION-PUMP ASSEMBLY
TD25
TD25