Information injection-pump assembly
BOSCH
F 01G 09W 0C8
f01g09w0c8
ZEXEL
104760-7070
1047607070
NISSAN-DIESEL
16700GL00A
16700gl00a
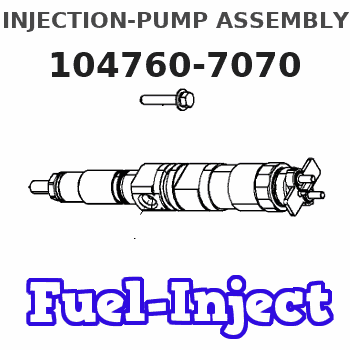
Rating:
Components :
0. | INJECTION-PUMP ASSEMBLY | 104760-7070 |
1. | _ | |
2. | FUEL INJECTION PUMP | |
3. | NUMBER PLATE | |
4. | _ | |
5. | CAPSULE | |
6. | ADJUSTING DEVICE | |
7. | NOZZLE AND HOLDER ASSY | 105148-1221 |
8. | Nozzle and Holder | |
9. | Open Pre:MPa(Kqf/cm2) | 9.8(100) |
10. | NOZZLE-HOLDER | 105078-0050 |
11. | NOZZLE | 105007-1210 |
Scheme ###:
1/6. | [1] | 146601-0900 | PACKING RING |
6. | [1] | 146100-0420 | SUPPLY PUMP |
9. | [1] | 146103-0100 | COVER |
10. | [2] | 139104-0000 | FLAT-HEAD SCREW |
12. | [1] | 146200-0020 | DRIVE SHAFT |
12/1. | [1] | 146200-0000 | DRIVE SHAFT |
12/2. | [1] | 146201-0000 | WOODRUFF KEY |
12/3. | [2] | 146202-0100 | DAMPER |
12/4. | [1] | 146203-0000 | TOOTHED GEAR |
17. | [1] | 146204-0000 | PLAIN WASHER |
20. | [1] | 146210-9520 | ROLLER SET |
24. | [1] | 146303-0100 | BEARING PIN |
25. | [1] | 146304-0000 | BEARING PIN |
26. | [1] | 146305-0000 | CLAMPING BAND |
27. | [1] | 146205-0000 | SLOTTED WASHER |
29. | [1] | 146221-1920 | CAM PLATE |
30. | [1] | 146600-0800 | O-RING |
31. | [1] | 146311-8920 | PUMP PLUNGER |
32. | [1] | 146301-0000 | SLIDING PIECE |
34. | [1] | 146312-2200 | COMPRESSION SPRING |
34B. | [1] | 146312-6600 | COMPRESSION SPRING |
34C. | [1] | 146312-3400 | COMPRESSION SPRING |
35/1. | [1] | 146690-3200 | SHIM D11.5&9.4T0.1 |
35/1. | [1] | 146690-3300 | SHIM D11.5&9.4T0.2 |
35/1. | [1] | 146690-3400 | SHIM D11.5&9.4T0.25 |
35/1. | [1] | 146690-3500 | SHIM D11.5&9.4T1.0 |
35/1. | [1] | 146690-4100 | SHIM D11.5&9.4T2 |
35/1. | [1] | 146690-4200 | SHIM D11.5&9.4T0.5 |
35/1. | [1] | 146690-4300 | SHIM D11.5&9.4T0.75 |
36. | [1] | 146600-0800 | O-RING |
37. | [1] | 146310-4020 | COVER |
38. | [2] | 146620-5000 | BLEEDER SCREW |
39. | [1] | 146310-0100 | COVER |
40. | [2] | 146620-5000 | BLEEDER SCREW |
41. | [1] | 146312-1900 | COMPRESSION SPRING |
43. | [1] | 146230-0000 | SHIM |
44. | [1] | 146230-0100 | PLAIN WASHER |
45. | [1] | 146231-0001 | SLOTTED WASHER |
47. | [2] | 146233-0000 | SLOTTED WASHER |
48/1. | [1] | 146603-0500 | SHIM D17.0&5.2T1.80 |
48/1. | [1] | 146603-0600 | SHIM D17.0&5.2T2.00 |
48/1. | [1] | 146690-1800 | SHIM D17&5.2T1.6 |
48/1. | [1] | 146690-1900 | SHIM D17&5.2T1.7 |
49. | [2] | 146234-0600 | GUIDE PIN |
50. | [1] | 146405-4020 | HYDRAULIC HEAD |
50. | [1] | 146405-4020 | HYDRAULIC HEAD |
50. | [1] | 146405-4020 | HYDRAULIC HEAD |
51. | [1] | 146600-0000 | O-RING |
52/1. | [1] | 146420-0200 | SHIM D9.5&3.0T1.94 |
52/1. | [1] | 146420-0700 | SHIM D9.5&3.0T2.04 |
52/1. | [1] | 146420-1200 | SHIM D9.5&3.0T2.14 |
52/1. | [1] | 146420-1700 | SHIM D9.5&3.0T2.24 |
52/1. | [1] | 146420-2200 | SHIM D9.5&3.0T2.34 |
52/1. | [1] | 146420-2700 | SHIM D9.5&3.0T2.44 |
52/1. | [1] | 146420-3200 | SHIM D9.5&3.0T2.54 |
52/1. | [1] | 146420-3700 | SHIM D9.5&3.0T2.64 |
52/1. | [1] | 146420-5600 | SHIM D9.5&3.0T1.84 |
54. | [6] | 146433-0100 | GASKET |
55. | [6] | 146430-2920 | DELIVERY-VALVE ASSEMBLY VE29 |
56. | [6] | 146432-0000 | COMPRESSION SPRING |
58. | [6] | 146440-0220 | FITTING |
60. | [4] | 139106-0100 | FLAT-HEAD SCREW |
67. | [1] | 146822-3920 | GOVERNOR COVER |
67/1. | [1] | 146805-2120 | GOVERNOR COVER |
67/2. | [1] | 146515-4820 | CONTROL SHAFT |
67/3. | [1] | 146600-0100 | O-RING |
67/4. | [2] | 139310-0200 | PLAIN WASHER |
67/4. | [2] | 139310-0200 | PLAIN WASHER |
67/5. | [1] | 146530-0000 | CONTROL LEVER |
67/5B. | [1] | 146530-0100 | CONTROL LEVER STAMP 001 |
67/5C. | [1] | 146832-1500 | CONTROL LEVER |
67/5D. | [1] | 146832-1600 | CONTROL LEVER |
67/6. | [2] | 014110-6440 | LOCKING WASHER D12.2&6.1T1.5 |
67/6. | [2] | 014110-6440 | LOCKING WASHER D12.2&6.1T1.5 |
67/7. | [1] | 013020-6040 | UNION NUT |
67/8. | [1] | 146515-0020 | LEVER SHAFT |
67/9. | [1] | 146592-0400 | COILED SPRING |
67/10. | [1] | 146600-0200 | O-RING |
67/11. | [1] | 146602-0100 | PLAIN WASHER |
67/12. | [1] | 146540-4000 | CONTROL LEVER |
67/12B. | [1] | 146540-4100 | CONTROL LEVER |
67/13. | [1] | 146621-1700 | UNION NUT |
67/14. | [1] | 146621-1700 | UNION NUT |
67/15. | [1] | 146526-2800 | BLEEDER SCREW |
67/16. | [1] | 146526-6400 | BLEEDER SCREW |
67/18. | [1] | 146594-0600 | COILED SPRING |
67/19. | [1] | 146541-0000 | ANGLE PIECE |
67/25. | [2] | 013020-6040 | UNION NUT |
67/25. | [2] | 013020-6040 | UNION NUT |
67/26. | [1] | 139006-0200 | BLEEDER SCREW |
67/78. | [1] | 146600-4400 | SEAL RING |
67/104. | [1] | 146936-1100 | BRACKET |
67/105. | [1] | 010206-1040 | HEX-SOCKET-HEAD CAP SCREW |
67/200. | [1] | 139308-0300 | PLAIN WASHER |
67/201. | [1] | 146545-3400 | THREADED PIN L53.00 |
67/201B. | [1] | 146545-3500 | THREADED PIN L55.00 |
67/201C. | [1] | 146545-3600 | THREADED PIN L57.00 |
67/202. | [1] | 139208-0900 | UNION NUT |
67/203. | [1] | 146600-1200 | O-RING |
95. | [1] | 146551-9920 | FULCRUM LEVER |
104. | [2] | 146568-0000 | SLOTTED SPRING PIN |
105. | [2] | 026508-1140 | GASKET D11.4&8.2T1.0 |
106. | [2] | 146588-0500 | COILED SPRING |
107. | [1] | 146569-0300 | UNION NUT |
108. | [1] | 146570-0100 | GOVERNOR SHAFT |
109. | [1] | 146600-0400 | O-RING |
110/1. | [1] | 146571-0000 | SHIM D20.2&8.3T1.05 |
110/1. | [1] | 146571-0100 | SHIM D20.2&8.3T1.25 |
110/1. | [1] | 146571-0200 | SHIM D20.2&8.3T1.45 |
110/1. | [1] | 146571-0300 | SHIM D20.2&8.3T1.65 |
110/1. | [1] | 146571-0400 | SHIM D20.2&8.3T1.85 |
111. | [1] | 146602-0600 | PLAIN WASHER |
112. | [1] | 146572-0020 | FLYWEIGHT ASSEMBLY |
114. | [1] | 146602-2600 | PLAIN WASHER |
115. | [1] | 146976-3800 | SLIDING SLEEVE |
116. | [1] | 146576-0400 | CAP |
117/1. | [1] | 146877-1620 | PLUG L=5.8 |
117/1. | [1] | 146877-1720 | PLUG L=5.9 |
117/1. | [1] | 146877-1820 | PLUG L=6.0 |
117/1. | [1] | 146877-1920 | PLUG L=6.1 |
117/1. | [1] | 146877-2020 | PLUG L=6.2 |
117/1. | [1] | 146877-2120 | PLUG L=6.3 |
117/1. | [1] | 146877-2220 | PLUG L=6.4 |
117/1. | [1] | 146877-2320 | PLUG L=6.5 |
117/1. | [1] | 146877-2420 | PLUG L=6.6 |
117/1. | [1] | 146877-2520 | PLUG L=6.7 |
117/1. | [1] | 146877-2620 | PLUG L=6.8 |
117/1. | [1] | 146877-2720 | PLUG L=6.9 |
117/1. | [1] | 146877-2820 | PLUG L=7.0 |
117/1. | [1] | 146877-2920 | PLUG L=7.1 |
117/1. | [1] | 146877-3020 | PLUG L=7.2 |
117/1. | [1] | 146877-3120 | PLUG L=7.3 |
117/1. | [1] | 146877-3220 | PLUG L=7.4 |
120. | [1] | 146579-1220 | RETAINING PIN |
122. | [1] | 146580-1300 | GOVERNOR SPRING |
123. | [4] | 139106-0200 | FLAT-HEAD SCREW |
130. | [1] | 146421-0020 | CAPSULE |
130/2. | [1] | 026508-1140 | GASKET D11.4&8.2T1.0 |
130/3. | [1] | 146422-0000 | BLEEDER SCREW |
130/4. | [1] | 146600-0500 | O-RING |
133. | [1] | 146600-0600 | O-RING |
134. | [1] | 146600-0700 | O-RING |
135. | [1] | 146110-0620 | CONTROL VALVE |
135/5. | [1] | 146114-0000 | SPRING WASHER |
136. | [1] | 146120-0120 | OVER FLOW VALVE |
200. | [1] | 146206-0100 | COILED SPRING |
240. | [1] | 146650-0720 | PULLING ELECTROMAGNET |
240/8. | [1] | 146600-1700 | O-RING |
242. | [1] | 146658-6120 | WIRE |
243. | [1] | 146621-4901 | UNION NUT |
245. | [1] | 139512-0500 | GASKET |
247. | [1] | 146669-1720 | INLET UNION |
351. | [1] | 146125-0101 | FILTER |
352. | [1] | 146125-0200 | COILED SPRING |
800S. | [1] | 146009-9220 | PUMP HOUSING |
800S/1/6. | [1] | 146601-0900 | PACKING RING |
804S. | [1] | 146232-1520 | COMPRESSION SPRING |
805S. | [1] | 146574-0920 | PARTS SET |
810S. | [1] | 146600-1120 | REPAIR SET |
821S. | [1] | 146210-9420 | ROLLER SET |
835S. | [1] | 146598-1000 | CAP |
836S/1. | [1] | 146598-0600 | CAP L18 |
836S/1. | [1] | 146598-0700 | CAP L21 |
836S/1. | [1] | 146598-0800 | CAP L24 |
836S/1. | [1] | 146598-0900 | CAP L27 |
906. | [1] | 146984-9300 | NAMEPLATE |
Include in #2:
104760-7070
as INJECTION-PUMP ASSEMBLY
Cross reference number
BOSCH
F 01G 09W 0C8
f01g09w0c8
ZEXEL
104760-7070
1047607070
NISSAN-DIESEL
16700GL00A
16700gl00a
Zexel num
Bosch num
Firm num
Name
104760-7070
F 01G 09W 0C8
16700GL00A NISSAN-DIESEL
INJECTION-PUMP ASSEMBLY
TD42
TD42
Calibration Data:
Adjustment conditions
Test oil
1404 Test oil ISO4113orSAEJ967d
1404 Test oil ISO4113orSAEJ967d
Test oil temperature
degC
45
45
50
Nozzle
105780-0060
Bosch type code
NP-DN0SD1510
Nozzle holder
105780-2150
Opening pressure
MPa
13
13
13.3
Opening pressure
kgf/cm2
133
133
136
Injection pipe
157805-7320
Injection pipe
Inside diameter - outside diameter - length (mm) mm 2-6-450
Inside diameter - outside diameter - length (mm) mm 2-6-450
Joint assembly
157641-4720
Tube assembly
157641-4020
Transfer pump pressure
kPa
20
20
20
Transfer pump pressure
kgf/cm2
0.2
0.2
0.2
Direction of rotation (viewed from drive side)
Right R
Right R
Injection timing adjustment
Pump speed
r/min
1000
1000
1000
Average injection quantity
mm3/st.
48.3
47.8
48.8
Difference in delivery
mm3/st.
3.5
Basic
*
Oil temperature
degC
50
48
52
Injection timing adjustment_02
Pump speed
r/min
300
300
300
Average injection quantity
mm3/st.
49.1
43.6
54.6
Oil temperature
degC
48
46
50
Injection timing adjustment_03
Pump speed
r/min
600
600
600
Average injection quantity
mm3/st.
51.5
48.5
54.5
Oil temperature
degC
50
48
52
Injection timing adjustment_04
Pump speed
r/min
1000
1000
1000
Average injection quantity
mm3/st.
48.3
47.3
49.3
Difference in delivery
mm3/st.
4
Basic
*
Oil temperature
degC
50
48
52
Injection timing adjustment_05
Pump speed
r/min
1200
1200
1200
Average injection quantity
mm3/st.
48.6
45.1
52.1
Oil temperature
degC
50
48
52
Injection quantity adjustment
Pump speed
r/min
1355
1355
1355
Average injection quantity
mm3/st.
9.2
7.2
11.2
Basic
*
Oil temperature
degC
50
48
52
Injection quantity adjustment_02
Pump speed
r/min
1355
1355
1355
Average injection quantity
mm3/st.
9.2
6.7
11.7
Basic
*
Oil temperature
degC
50
48
52
Injection quantity adjustment_03
Pump speed
r/min
1450
1450
1450
Average injection quantity
mm3/st.
3
Oil temperature
degC
52
50
54
Governor adjustment
Pump speed
r/min
385
385
385
Average injection quantity
mm3/st.
10.2
8.2
12.2
Difference in delivery
mm3/st.
2.5
Basic
*
Oil temperature
degC
48
46
50
Governor adjustment_02
Pump speed
r/min
385
385
385
Average injection quantity
mm3/st.
10.2
7.7
12.7
Difference in delivery
mm3/st.
3
Basic
*
Oil temperature
degC
48
46
50
Governor adjustment_03
Pump speed
r/min
350
350
350
Average injection quantity
mm3/st.
25
17
33
Oil temperature
degC
48
46
50
Timer adjustment
Pump speed
r/min
100
100
100
Average injection quantity
mm3/st.
57
52
62
Basic
*
Oil temperature
degC
48
46
50
Remarks
Full
Full
Timer adjustment_02
Pump speed
r/min
100
100
100
Average injection quantity
mm3/st.
57
52
62
Oil temperature
degC
48
46
50
Remarks
Full
Full
Speed control lever angle
Pump speed
r/min
385
385
385
Average injection quantity
mm3/st.
0
0
0
Oil temperature
degC
48
46
50
Remarks
Magnet OFF at idling position
Magnet OFF at idling position
0000000901
Pump speed
r/min
1000
1000
1000
Overflow quantity
cm3/min
400
270
530
Oil temperature
degC
50
48
52
Stop lever angle
Pump speed
r/min
1000
1000
1000
Pressure
kPa
441
421
461
Pressure
kgf/cm2
4.5
4.3
4.7
Basic
*
Oil temperature
degC
50
48
52
Stop lever angle_02
Pump speed
r/min
1000
1000
1000
Pressure
kPa
441
412
470
Pressure
kgf/cm2
4.5
4.2
4.8
Basic
*
Oil temperature
degC
50
48
52
Stop lever angle_03
Pump speed
r/min
1200
1200
1200
Pressure
kPa
510
471
549
Pressure
kgf/cm2
5.2
4.8
5.6
Oil temperature
degC
50
48
52
0000001101
Pump speed
r/min
1000
1000
1000
Timer stroke
mm
1.7
1.5
1.9
Basic
*
Oil temperature
degC
50
48
52
_02
Pump speed
r/min
1000
1000
1000
Timer stroke
mm
1.7
1.4
2
Basic
*
Oil temperature
degC
50
48
52
_03
Pump speed
r/min
1200
1200
1200
Timer stroke
mm
2.7
2.2
3.2
Oil temperature
degC
50
48
52
0000001201
Max. applied voltage
V
8
8
8
Test voltage
V
13
12
14
Timing setting
K dimension
mm
3.3
3.2
3.4
KF dimension
mm
6.76
6.66
6.86
MS dimension
mm
1.2
1.1
1.3
Control lever angle alpha
deg.
25
21
29
Control lever angle beta
deg.
32
27
37
Test data Ex:
0000001801 STOP LEVER ADJUSTMENT
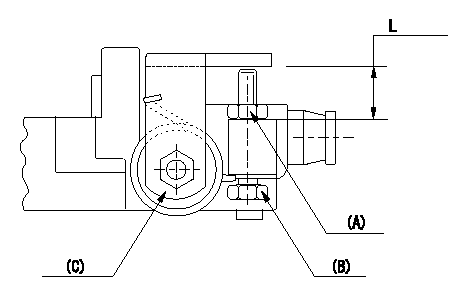
Adjustment of the stop lever
Adjust adjusting bolt (B) so that the starting injection quantity is within the standard.
Fix using nut.
(A) Adjusting nut
(C) Starting injection quantity adjusting lever
----------
----------
L=15.0~18.5mm
----------
----------
L=15.0~18.5mm
Information:
ELC Cooling System Contamination
Mixing ELC with other products reduces the effectiveness of the ELC and shortens the ELC service life. Use only Caterpillar products or commercial products that have passed the Caterpillar EC-1 specification for premixed or concentrate coolants. Use only Caterpillar Extender with Caterpillar ELC. Failure to follow these recommendations can result in shortened cooling system component life.
ELC cooling systems can withstand contamination of up to ten percent of conventional HD coolant/antifreeze. If the contamination exceeds ten percent of the total system capacity, perform either one of the following two procedures: * Drain the cooling system. Flush the system with clean water. Refill the system with ELC.* Maintain the cooling system as if the system is filled with conventional HD coolant/antifreeze.Commercial ELC
If Caterpillar extended life coolant is not used, select a commercial extended life coolant that meets the Caterpillar EC-1 specification. Do not use a product that is labeled as an extended life coolant but does not meet the Caterpillar EC-1 specification. Follow the coolant maintenance guidelines of the commercial ELC supplier. In all cases, use distilled or deionized water or use water that has the properties listed in the Caterpillar Water Quality Limits chart.Caterpillar Diesel Engine Antifreeze/Coolant (DEAC)
Caterpillar recommends the use of Caterpillar Diesel Engine Antifreeze/Coolant (DEAC) in conventional HD cooling systems. DEAC is an alkaline type, single-phase, ethylene glycol-based antifreeze/coolant. DEAC contains inorganic corrosion inhibitors and antifoaming agents.Contact your Caterpillar dealer for part numbers and available container sizes.Caterpillar DEAC is available premixed with distilled water in a 50/50 concentration. If DEAC concentrate is used, Caterpillar recommends mixing the concentrate with distilled or deionized water. If distilled or deionized water is not available, use water that has the properties listed in the Caterpillar Water Quality Limits chart.Caterpillar Supplemental Coolant Additive (SCA)
Caterpillar Supplemental Coolant Additive (SCA) is effective in preventing corrosion on all metals. Caterpillar SCA also prevents the formation of mineral deposits, prevents liner cavitation, and eliminates coolant foaming.Caterpillar DEAC is formulated with the correct level of Caterpillar SCA. Additional SCA is NOT needed when the cooling system is initially filled with DEAC.Contact your Caterpillar dealer for part numbers and available container sizes.Commercial Heavy Duty (HD) Coolant/Antifreeze and SCA
If Caterpillar DEAC is not used, select a low silicate commercial HD coolant/antifreeze that meets ASTM D5345 or D4985 specifications.When a commercial HD coolant/antifreeze is used, the cooling system should be treated with three to six percent Caterpillar SCA by volume. Refer to the Caterpillar SCA Requirements for Heavy Duty Coolant/Antifreeze chart. If Caterpillar SCA is not used, select a commercial SCA. The commercial SCA must provide a minimum of 1200 mg/L or 1200 ppm (70 grains/US gal) nitrites in the final coolant mixture. Follow the coolant maintenance guidelines of the commercial SCA supplier.HD coolant/antifreezes that meet ASTM D5345 or D4985 specifications DO require SCA treatment at initial fill, and on a maintenance basis.When mixing concentrated coolants, use distilled or deionized water or use water that has the properties listed in the Caterpillar Water Quality Limits chart.Heavy Duty
Mixing ELC with other products reduces the effectiveness of the ELC and shortens the ELC service life. Use only Caterpillar products or commercial products that have passed the Caterpillar EC-1 specification for premixed or concentrate coolants. Use only Caterpillar Extender with Caterpillar ELC. Failure to follow these recommendations can result in shortened cooling system component life.
ELC cooling systems can withstand contamination of up to ten percent of conventional HD coolant/antifreeze. If the contamination exceeds ten percent of the total system capacity, perform either one of the following two procedures: * Drain the cooling system. Flush the system with clean water. Refill the system with ELC.* Maintain the cooling system as if the system is filled with conventional HD coolant/antifreeze.Commercial ELC
If Caterpillar extended life coolant is not used, select a commercial extended life coolant that meets the Caterpillar EC-1 specification. Do not use a product that is labeled as an extended life coolant but does not meet the Caterpillar EC-1 specification. Follow the coolant maintenance guidelines of the commercial ELC supplier. In all cases, use distilled or deionized water or use water that has the properties listed in the Caterpillar Water Quality Limits chart.Caterpillar Diesel Engine Antifreeze/Coolant (DEAC)
Caterpillar recommends the use of Caterpillar Diesel Engine Antifreeze/Coolant (DEAC) in conventional HD cooling systems. DEAC is an alkaline type, single-phase, ethylene glycol-based antifreeze/coolant. DEAC contains inorganic corrosion inhibitors and antifoaming agents.Contact your Caterpillar dealer for part numbers and available container sizes.Caterpillar DEAC is available premixed with distilled water in a 50/50 concentration. If DEAC concentrate is used, Caterpillar recommends mixing the concentrate with distilled or deionized water. If distilled or deionized water is not available, use water that has the properties listed in the Caterpillar Water Quality Limits chart.Caterpillar Supplemental Coolant Additive (SCA)
Caterpillar Supplemental Coolant Additive (SCA) is effective in preventing corrosion on all metals. Caterpillar SCA also prevents the formation of mineral deposits, prevents liner cavitation, and eliminates coolant foaming.Caterpillar DEAC is formulated with the correct level of Caterpillar SCA. Additional SCA is NOT needed when the cooling system is initially filled with DEAC.Contact your Caterpillar dealer for part numbers and available container sizes.Commercial Heavy Duty (HD) Coolant/Antifreeze and SCA
If Caterpillar DEAC is not used, select a low silicate commercial HD coolant/antifreeze that meets ASTM D5345 or D4985 specifications.When a commercial HD coolant/antifreeze is used, the cooling system should be treated with three to six percent Caterpillar SCA by volume. Refer to the Caterpillar SCA Requirements for Heavy Duty Coolant/Antifreeze chart. If Caterpillar SCA is not used, select a commercial SCA. The commercial SCA must provide a minimum of 1200 mg/L or 1200 ppm (70 grains/US gal) nitrites in the final coolant mixture. Follow the coolant maintenance guidelines of the commercial SCA supplier.HD coolant/antifreezes that meet ASTM D5345 or D4985 specifications DO require SCA treatment at initial fill, and on a maintenance basis.When mixing concentrated coolants, use distilled or deionized water or use water that has the properties listed in the Caterpillar Water Quality Limits chart.Heavy Duty
Have questions with 104760-7070?
Group cross 104760-7070 ZEXEL
Nissan-Diesel
Nissan-Diesel
104760-7070
F 01G 09W 0C8
16700GL00A
INJECTION-PUMP ASSEMBLY
TD42
TD42