Information injection-pump assembly
BOSCH
9 460 615 094
9460615094
ZEXEL
104760-7050
1047607050
NISSAN-DIESEL
167001Y60A
167001y60a
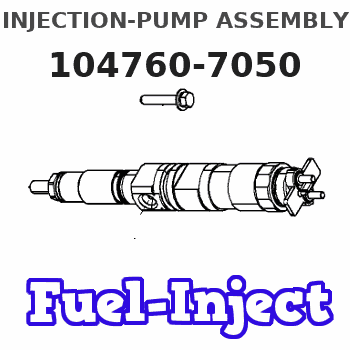
Rating:
Components :
0. | INJECTION-PUMP ASSEMBLY | 104760-7050 |
1. | _ | |
2. | FUEL INJECTION PUMP | 104660-7050 |
3. | NUMBER PLATE | |
4. | _ | |
5. | CAPSULE | |
6. | ADJUSTING DEVICE | |
7. | NOZZLE AND HOLDER ASSY | 105148-1121 |
8. | Nozzle and Holder | |
9. | Open Pre:MPa(Kqf/cm2) | 9.8(100) |
10. | NOZZLE-HOLDER | 105078-0050 |
11. | NOZZLE | 105007-1130 |
Scheme ###:
1/6. | [1] | 146601-0900 | PACKING RING |
6. | [1] | 146100-0420 | SUPPLY PUMP |
9. | [1] | 146103-0100 | COVER |
10. | [2] | 139104-0000 | FLAT-HEAD SCREW |
12. | [1] | 146200-0020 | DRIVE SHAFT |
12/1. | [1] | 146200-0000 | DRIVE SHAFT |
12/2. | [1] | 146201-0000 | WOODRUFF KEY |
12/3. | [2] | 146202-0100 | DAMPER |
12/4. | [1] | 146203-0000 | TOOTHED GEAR |
17. | [1] | 146204-0000 | PLAIN WASHER |
20. | [1] | 146210-2720 | ROLLER SET |
24. | [1] | 146303-0100 | BEARING PIN |
25. | [1] | 146304-0000 | BEARING PIN |
26. | [1] | 146305-0000 | CLAMPING BAND |
27. | [1] | 146205-0000 | SLOTTED WASHER |
29. | [1] | 146221-0920 | CAM PLATE |
30. | [1] | 146600-0800 | O-RING |
31. | [1] | 146311-6420 | PUMP PLUNGER |
32. | [1] | 146301-0000 | SLIDING PIECE |
34. | [1] | 146312-3700 | COMPRESSION SPRING |
34B. | [1] | 146312-1800 | COMPRESSION SPRING |
34C. | [1] | 146312-3400 | COMPRESSION SPRING |
35/1. | [1] | 146690-3200 | SHIM D11.5&9.4T0.1 |
35/1. | [1] | 146690-3300 | SHIM D11.5&9.4T0.2 |
35/1. | [1] | 146690-3400 | SHIM D11.5&9.4T0.25 |
35/1. | [1] | 146690-3500 | SHIM D11.5&9.4T1.0 |
35/1. | [1] | 146690-4100 | SHIM D11.5&9.4T2 |
35/1. | [1] | 146690-4200 | SHIM D11.5&9.4T0.5 |
35/1. | [1] | 146690-4300 | SHIM D11.5&9.4T0.75 |
36. | [1] | 146600-0800 | O-RING |
37. | [1] | 146310-4020 | COVER |
38. | [2] | 146620-5000 | BLEEDER SCREW |
39. | [1] | 146310-0100 | COVER |
40. | [2] | 146620-5000 | BLEEDER SCREW |
41. | [1] | 146312-1900 | COMPRESSION SPRING |
43. | [1] | 146230-0000 | SHIM |
44. | [1] | 146230-0100 | PLAIN WASHER |
45. | [1] | 146231-0001 | SLOTTED WASHER |
47. | [2] | 146233-0000 | SLOTTED WASHER |
48/1. | [1] | 146603-0400 | SHIM D17.0&5.2T1.50 |
48/1. | [1] | 146603-0500 | SHIM D17.0&5.2T1.80 |
48/1. | [1] | 146603-0600 | SHIM D17.0&5.2T2.00 |
48/1. | [1] | 146690-1800 | SHIM D17&5.2T1.6 |
48/1. | [1] | 146690-1900 | SHIM D17&5.2T1.7 |
49. | [2] | 146234-0500 | GUIDE PIN |
50. | [1] | 146405-1920 | HYDRAULIC HEAD |
50. | [1] | 146405-1920 | HYDRAULIC HEAD |
50. | [1] | 146405-1920 | HYDRAULIC HEAD |
51. | [1] | 146600-0000 | O-RING |
52/1. | [1] | 146420-0200 | SHIM D9.5&3.0T1.94 |
52/1. | [1] | 146420-0700 | SHIM D9.5&3.0T2.04 |
52/1. | [1] | 146420-1200 | SHIM D9.5&3.0T2.14 |
52/1. | [1] | 146420-1700 | SHIM D9.5&3.0T2.24 |
52/1. | [1] | 146420-2200 | SHIM D9.5&3.0T2.34 |
52/1. | [1] | 146420-2700 | SHIM D9.5&3.0T2.44 |
52/1. | [1] | 146420-3200 | SHIM D9.5&3.0T2.54 |
52/1. | [1] | 146420-3700 | SHIM D9.5&3.0T2.64 |
52/1. | [1] | 146420-5600 | SHIM D9.5&3.0T1.84 |
54. | [6] | 146433-0100 | GASKET |
55. | [6] | 146430-0320 | DELIVERY-VALVE ASSEMBLY VE4 |
56. | [6] | 146432-0000 | COMPRESSION SPRING |
58. | [6] | 146440-0220 | FITTING |
60. | [3] | 139106-0100 | FLAT-HEAD SCREW |
66. | [1] | 146600-0100 | O-RING |
67. | [1] | 146707-3620 | ANEROID CAPSULE |
67/1. | [1] | 146806-8620 | GOVERNOR COVER |
67/13. | [1] | 139206-0100 | UNION NUT |
67/14. | [1] | 146621-1700 | UNION NUT |
67/15. | [1] | 146526-4200 | BLEEDER SCREW |
67/16. | [1] | 146526-3000 | BLEEDER SCREW |
67/31. | [1] | 146710-0400 | BUSHING |
67/32. | [1] | 146602-1800 | PLAIN WASHER |
67/33. | [1] | 146716-0200 | UNION NUT |
67/34/1. | [1] | 146713-1000 | BEARING PIN L24.6 |
67/34/1. | [1] | 146713-1100 | BEARING PIN L24.8 |
67/34/1. | [1] | 146713-1200 | BEARING PIN L25.0 |
67/34/1. | [1] | 146713-1300 | BEARING PIN L25.2 |
67/34/1. | [1] | 146713-1400 | BEARING PIN L25.4 |
67/35. | [1] | 146621-0300 | UNION NUT |
67/36. | [1] | 146600-1400 | O-RING |
67/37. | [1] | 146710-0100 | BUSHING |
67/38. | [1] | 139506-0200 | GASKET |
67/39. | [1] | 146620-0300 | CAPSULE |
67/40. | [1] | 026512-1540 | GASKET |
67/41. | [1] | 146713-2400 | ADJUSTING PIN |
67/47. | [1] | 146717-0200 | COILED SPRING |
67/49. | [1] | 146721-0700 | COVER |
67/54. | [4] | 139006-4400 | BLEEDER SCREW |
67/56. | [1] | 146723-0200 | CONTROL LEVER |
67/57. | [1] | 146712-0100 | BEARING PIN |
67/58. | [2] | 146620-0600 | CAPSULE |
67/59. | [2] | 026506-1040 | GASKET |
67/60. | [1] | 146724-0300 | ELEMENT |
67/61. | [1] | 146724-0400 | CAPSULE |
67/70. | [1] | 016520-6010 | O-RING |
67/71. | [1] | 146714-0100 | SLOTTED WASHER |
67/72. | [1] | 016010-0920 | LOCKING WASHER |
67/73. | [1] | 146715-0120 | BELLOWS |
67/74/1. | [0] | 146603-3700 | SHIM T0.20 |
67/74/1. | [0] | 146603-3800 | SHIM T0.30 |
67/74/1. | [0] | 146603-3900 | SHIM T0.50 |
67/74/1. | [0] | 146603-4000 | SHIM T0.70 |
67/74/1. | [0] | 146603-4100 | SHIM T1.00 |
67/74/1. | [0] | 146603-4200 | SHIM T1.50 |
67/78. | [1] | 146600-4400 | SEAL RING |
67/200. | [1] | 139308-0300 | PLAIN WASHER |
67/201. | [1] | 146545-3400 | THREADED PIN L53.00 |
67/201B. | [1] | 146545-3500 | THREADED PIN L55.00 |
67/201C. | [1] | 146545-3600 | THREADED PIN L57.00 |
67/202. | [1] | 139208-0900 | UNION NUT |
67/203. | [1] | 146600-1200 | O-RING |
68. | [1] | 146810-7320 | CONTROL SHAFT |
69. | [1] | 139310-0200 | PLAIN WASHER |
72. | [1] | 146832-0520 | CONTROL LEVER STAMP 205 |
72B. | [1] | 146832-0620 | CONTROL LEVER STAMP 206 |
73. | [1] | 014110-6440 | LOCKING WASHER D12.2&6.1T1.5 |
75. | [1] | 013020-6040 | UNION NUT |
95. | [1] | 146851-3820 | FULCRUM LEVER |
104. | [2] | 146568-0000 | SLOTTED SPRING PIN |
105. | [2] | 026508-1140 | GASKET D11.4&8.2T1.0 |
106. | [2] | 146588-0500 | COILED SPRING |
107. | [1] | 146569-0300 | UNION NUT |
108. | [1] | 146570-0420 | GOVERNOR SHAFT |
109. | [1] | 146600-0400 | O-RING |
110/1. | [1] | 146571-0000 | SHIM D20.2&8.3T1.05 |
110/1. | [1] | 146571-0100 | SHIM D20.2&8.3T1.25 |
110/1. | [1] | 146571-0200 | SHIM D20.2&8.3T1.45 |
110/1. | [1] | 146571-0300 | SHIM D20.2&8.3T1.65 |
110/1. | [1] | 146571-0400 | SHIM D20.2&8.3T1.85 |
111. | [1] | 146602-0600 | PLAIN WASHER |
112. | [1] | 146572-0020 | FLYWEIGHT ASSEMBLY |
114. | [1] | 146602-0500 | PLAIN WASHER |
115. | [1] | 146975-5900 | SLIDING SLEEVE |
116. | [1] | 146576-0200 | CAP |
117/1. | [1] | 146577-2300 | PLUG L3.10 |
117/1. | [1] | 146577-2400 | PLUG L3.30 |
117/1. | [1] | 146577-2500 | PLUG L3.50 |
117/1. | [1] | 146577-2600 | PLUG L3.70 |
117/1. | [1] | 146577-2700 | PLUG L3.90 |
117/1. | [1] | 146577-2800 | PLUG L4.10 |
117/1. | [1] | 146577-2900 | PLUG L4.30 |
117/1. | [1] | 146577-3000 | PLUG L4.50 |
117/1. | [1] | 146577-3100 | PLUG L4.70 |
117/1. | [1] | 146577-7200 | PLUG L3.2 |
117/1. | [1] | 146577-7300 | PLUG L3.4 |
117/1. | [1] | 146577-7400 | PLUG L3.6 |
117/1. | [1] | 146577-7500 | PLUG L3.8 |
117/1. | [1] | 146577-7600 | PLUG L4.0 |
117/1. | [1] | 146577-7700 | PLUG L4.2 |
117/1. | [1] | 146577-7800 | PLUG L4.4 |
117/1. | [1] | 146577-7900 | PLUG L4.6 |
123. | [4] | 146620-0500 | HEX-SOCKET-HEAD CAP SCREW |
130. | [1] | 146421-0020 | CAPSULE |
130/2. | [1] | 026508-1140 | GASKET D11.4&8.2T1.0 |
130/3. | [1] | 146422-0000 | BLEEDER SCREW |
130/4. | [1] | 146600-0500 | O-RING |
133. | [1] | 146600-0600 | O-RING |
134. | [1] | 146600-0700 | O-RING |
135. | [1] | 146110-0620 | CONTROL VALVE |
135/5. | [1] | 146114-0000 | SPRING WASHER |
136. | [1] | 146650-5420 | PULLING ELECTROMAGNET |
137. | [2] | 139514-0200 | GASKET |
145. | [1] | 146621-4901 | UNION NUT |
147. | [1] | 146600-5000 | O-RING |
200. | [1] | 146206-0100 | COILED SPRING |
217. | [1] | 146541-3100 | SLOTTED WASHER |
218. | [1] | 146587-0800 | COILED SPRING |
219. | [1] | 146541-3000 | BUSHING |
220. | [1] | 146587-6900 | COILED SPRING |
230. | [1] | 146935-2721 | BRACKET |
231. | [1] | 139006-4600 | BLEEDER SCREW |
236. | [1] | 139006-4800 | BLEEDER SCREW |
237. | [1] | 146620-0200 | HEX-SOCKET-HEAD CAP SCREW |
240. | [1] | 146650-0720 | PULLING ELECTROMAGNET |
240/8. | [1] | 146600-1700 | O-RING |
242. | [1] | 146662-6620 | WIRE |
243. | [1] | 146621-4901 | UNION NUT |
244. | [1] | 020118-1440 | BLEEDER SCREW |
245. | [2] | 139512-0500 | GASKET |
246. | [1] | 027412-2440 | EYE BOLT |
247. | [1] | 146668-0120 | PIPE |
247. | [1] | 146668-0120 | PIPE |
251. | [1] | 014010-8140 | PLAIN WASHER |
321. | [1] | 146932-2600 | PLATE |
351. | [1] | 146125-0101 | FILTER |
352. | [1] | 146125-0200 | COILED SPRING |
800S. | [1] | 146018-0420 | PUMP HOUSING |
800S/1/6. | [1] | 146601-0900 | PACKING RING |
804S. | [1] | 146232-0320 | COMPRESSION SPRING |
805S. | [1] | 146574-0120 | PARTS SET |
810S. | [1] | 146600-1120 | REPAIR SET |
821S. | [1] | 146210-5720 | ROLLER SET |
835S. | [1] | 146598-1000 | CAP |
836S/1. | [1] | 146598-0600 | CAP L18 |
836S/1. | [1] | 146598-0700 | CAP L21 |
836S/1. | [1] | 146598-0800 | CAP L24 |
836S/1. | [1] | 146598-0900 | CAP L27 |
906. | [1] | 146984-6500 | NAMEPLATE |
907. | [1] | 025803-1640 | WOODRUFF KEY |
Include in #2:
104760-7050
as INJECTION-PUMP ASSEMBLY
Cross reference number
BOSCH
9 460 615 094
9460615094
ZEXEL
104760-7050
1047607050
NISSAN-DIESEL
167001Y60A
167001y60a
Zexel num
Bosch num
Firm num
Name
104760-7050
9 460 615 094
167001Y60A NISSAN-DIESEL
INJECTION-PUMP ASSEMBLY
TD42 K 11CK INJECTION PUMP ASSY VE6 VE
TD42 K 11CK INJECTION PUMP ASSY VE6 VE
Calibration Data:
Adjustment conditions
Test oil
1404 Test oil ISO4113orSAEJ967d
1404 Test oil ISO4113orSAEJ967d
Test oil temperature
degC
45
45
50
Nozzle
105780-0060
Bosch type code
NP-DN0SD1510
Nozzle holder
105780-2150
Opening pressure
MPa
13
13
13.3
Opening pressure
kgf/cm2
133
133
136
Injection pipe
157805-7320
Injection pipe
Inside diameter - outside diameter - length (mm) mm 2-6-450
Inside diameter - outside diameter - length (mm) mm 2-6-450
Joint assembly
157641-4720
Tube assembly
157641-4020
Transfer pump pressure
kPa
20
20
20
Transfer pump pressure
kgf/cm2
0.2
0.2
0.2
Direction of rotation (viewed from drive side)
Right R
Right R
(Solenoid timer adjustment condition)
With S/T O-ring; S/T OFF. OFF
With S/T O-ring; S/T OFF. OFF
Injection timing adjustment
Pump speed
r/min
1000
1000
1000
Average injection quantity
mm3/st.
46.9
46.4
47.4
Difference in delivery
mm3/st.
3.5
Basic
*
Oil temperature
degC
50
48
52
Injection timing adjustment_02
Pump speed
r/min
600
600
600
Average injection quantity
mm3/st.
45.4
42.9
47.9
Oil temperature
degC
50
48
52
Injection timing adjustment_03
Pump speed
r/min
1000
1000
1000
Average injection quantity
mm3/st.
46.9
45.9
47.9
Difference in delivery
mm3/st.
4
Basic
*
Oil temperature
degC
50
48
52
Injection timing adjustment_04
Pump speed
r/min
2000
2000
2000
Average injection quantity
mm3/st.
44.9
42.4
47.4
Oil temperature
degC
50
48
52
Injection quantity adjustment
Pump speed
r/min
2300
2300
2300
Average injection quantity
mm3/st.
17.8
15.8
19.8
Difference in delivery
mm3/st.
5
Basic
*
Oil temperature
degC
52
50
54
Injection quantity adjustment_02
Pump speed
r/min
2500
2500
2500
Average injection quantity
mm3/st.
5
Oil temperature
degC
55
52
58
Injection quantity adjustment_03
Pump speed
r/min
2100
2100
2100
Average injection quantity
mm3/st.
44.7
40.2
49.2
Oil temperature
degC
52
50
54
Injection quantity adjustment_04
Pump speed
r/min
2300
2300
2300
Average injection quantity
mm3/st.
17.8
15.3
20.3
Basic
*
Oil temperature
degC
52
50
54
Governor adjustment
Pump speed
r/min
350
350
350
Average injection quantity
mm3/st.
10.1
8.1
12.1
Difference in delivery
mm3/st.
2
Basic
*
Oil temperature
degC
48
46
50
Governor adjustment_02
Pump speed
r/min
350
350
350
Average injection quantity
mm3/st.
10.1
7.6
12.6
Difference in delivery
mm3/st.
2.5
Basic
*
Oil temperature
degC
48
46
50
Timer adjustment
Pump speed
r/min
100
100
100
Average injection quantity
mm3/st.
60
50
80
Basic
*
Oil temperature
degC
48
46
50
Remarks
Full
Full
Timer adjustment_02
Pump speed
r/min
100
100
100
Average injection quantity
mm3/st.
60
50
80
Oil temperature
degC
48
46
50
Remarks
Full
Full
Speed control lever angle
Pump speed
r/min
250
250
250
Average injection quantity
mm3/st.
5
Oil temperature
degC
48
46
50
Remarks
Magnet OFF at full-load position
Magnet OFF at full-load position
Speed control lever angle_02
Pump speed
r/min
350
350
350
Average injection quantity
mm3/st.
0
0
0
Oil temperature
degC
48
46
50
Remarks
Magnet OFF at idling position
Magnet OFF at idling position
0000000901
Pump speed
r/min
1000
1000
1000
Overflow quantity with S/T ON
cm3/min
450
320
580
Oil temperature
degC
50
48
52
Stop lever angle
Pump speed
r/min
1000
1000
1000
Pressure with S/T ON
kPa
539
500
578
Pressure with S/T ON
kgf/cm2
5.5
5.1
5.9
Pressure with S/T OFF
kPa
422
402
442
Pressure with S/T OFF
kgf/cm2
4.3
4.1
4.5
Basic
*
Oil temperature
degC
50
48
52
Remarks
OFF
OFF
Stop lever angle_02
Pump speed
r/min
1000
1000
1000
Pressure with S/T OFF
kPa
422
393
451
Pressure with S/T OFF
kgf/cm2
4.3
4
4.6
Basic
*
Oil temperature
degC
50
48
52
Remarks
OFF
OFF
Stop lever angle_03
Pump speed
r/min
1800
1800
1800
Pressure with S/T OFF
kPa
686
647
725
Pressure with S/T OFF
kgf/cm2
7
6.6
7.4
Oil temperature
degC
50
48
52
0000001101
Pump speed
r/min
1000
1000
1000
Timer stroke with S/T ON
mm
4.6
4.2
5
Timer stroke with S/T OFF
mm
2.9
2.7
3.1
Basic
*
Oil temperature
degC
50
48
52
Remarks
OFF
OFF
_02
Pump speed
r/min
650
650
650
Timer stroke with S/T OFF
mm
1.2
0.7
1.7
Oil temperature
degC
50
48
52
_03
Pump speed
r/min
1000
1000
1000
Timer stroke with S/T ON
mm
4.6
4.1
5.1
Timer stroke with S/T OFF
mm
2.9
2.6
3.2
Basic
*
Oil temperature
degC
50
48
52
Remarks
OFF
OFF
_04
Pump speed
r/min
1800
1800
1800
Timer stroke with S/T OFF
mm
6.6
6.1
7.1
Oil temperature
degC
50
48
52
_05
Pump speed
r/min
2200
2200
2200
Timer stroke with S/T OFF
mm
8.2
7.7
8.6
Oil temperature
degC
52
50
54
0000001201
Max. applied voltage
V
8
8
8
Test voltage
V
13
12
14
0000001401
Pump speed
r/min
1000
1000
1000
Average injection quantity
mm3/st.
25.1
24.6
25.6
Timer stroke TA
mm
2.1
1.9
2.3
Timer stroke variation dT
mm
0.8
0.8
0.8
Basic
*
Oil temperature
degC
50
48
52
_02
Pump speed
r/min
1000
1000
1000
Average injection quantity
mm3/st.
25.1
24.1
26.1
Timer stroke TA
mm
2.1
1.8
2.4
Timer stroke variation dT
mm
0.8
0.8
0.8
Basic
*
Oil temperature
degC
50
48
52
_03
Pump speed
r/min
1000
1000
1000
Average injection quantity
mm3/st.
15
12.5
17.5
Timer stroke TA
mm
1.2
0.6
1.8
Timer stroke variation dT
mm
1.7
1.7
1.7
Oil temperature
degC
50
48
52
0000001501
Pump speed
r/min
1000
1000
1000
Height
m
2000
2000
2000
Atmospheric pressure difference
kPa
-21.9
-23.2
-20.6
Atmospheric pressure difference
mmHg
-164
-174
-154
Average injection quantity
mm3/st.
38.4
36.9
39.9
Decrease qty
mm3/st.
8.5
8.5
8.5
Decrease rate
%
18.1
18.1
18.1
Basic
*
Oil temperature
degC
50
48
52
_02
Pump speed
r/min
1000
1000
1000
Height
m
0
0
0
Atmospheric pressure difference
kPa
0
0
0
Atmospheric pressure difference
mmHg
0
0
0
Average injection quantity
mm3/st.
46.9
45.9
47.9
Oil temperature
degC
50
48
52
_03
Pump speed
r/min
1000
1000
1000
Height
m
500
500
500
Atmospheric pressure difference
kPa
-5.9
-9.2
-2.6
Atmospheric pressure difference
mmHg
-44
-69
-19
Average injection quantity
mm3/st.
46.9
46.9
46.9
Oil temperature
degC
50
48
52
_04
Pump speed
r/min
1000
1000
1000
Height
m
2000
2000
2000
Atmospheric pressure difference
kPa
-21.9
-23.2
-20.6
Atmospheric pressure difference
mmHg
-164
-174
-154
Average injection quantity
mm3/st.
38.4
36.4
40.4
Basic
*
Oil temperature
degC
50
48
52
_05
Pump speed
r/min
1000
1000
1000
Height
m
4000
4000
4000
Atmospheric pressure difference
kPa
-39.7
-41
-38.4
Atmospheric pressure difference
mmHg
-298
-308
-288
Average injection quantity
mm3/st.
31.4
31.4
31.4
Oil temperature
degC
50
48
52
Timing setting
K dimension
mm
3.3
3.2
3.4
KF dimension
mm
6.64
6.54
6.74
MS dimension
mm
1
0.9
1.1
Control lever angle alpha
deg.
55.5
51.5
59.5
Control lever angle beta
deg.
40
35
45
Information:
Engine Lifting
When it is necessary to remove a component on an angle, remember that the capacity of an eyebolt is less as the angle between the supporting members and the object becomes less than 90 degrees. Eye Bolts and brackets should never be bent, and should only be loaded under tension.
Use a hoist to remove heavy components. Use an adjustable lifting beam to lift the engine. All supporting members (chains and cables) should be parallel to each other, and perpendicular as possible to the top of the object being lifted.Some removals require the use of lifting fixtures, to obtain proper balance and provide safe handling.To remove the engine ONLY, use the lifting eyes equipped with the engine.The lifting eyes are designed for the engine arrangement as sold. Modifying the lifting eyes and/or engine arrangement weight renders the lifting eyes and devices obsolete.If you modify the lifting eyes and/or engine arrangement weight, you are responsible for providing adequate lifting devices. Contact your Caterpillar dealer for information regarding fixtures for proper engine package lifting.Engine Lifting With Generator
Do not use the engine lifting eyes to remove the engine and generator together.Lifting the engine and generator together requires special equipment and procedures. Contact your Caterpillar dealer for information regarding fixtures for proper lifting of your engine package.Engine Lifting With Fuel Tank
Lifting the engine along with a mounted fuel tank requires special equipment and procedures. Do not lift the unit with fuel in the tank. Contact your Caterpillar dealer for information regarding proper engine and fuel tank lifting.Engine Storage
The following Engine Storage procedures and recommendations minimize the possibility of damage to engines stored for one year or less.When an engine is not started for several weeks, the lubricating oil drains from the cylinder walls and piston rings. Rust can then form on the cylinder liner surface, increasing engine wear and decreasing engine life.Special precautions should be used with engines remaining out of service for extended periods.After one year, a complete protection procedure must be followed if the engine is kept in storage longer. To prevent excessive engine wear: * Be sure all lubrication recommendations mentioned in the Maintenance Schedule intervals chart are completed.* If freezing temperatures are expected, check the cooling system for adequate protection against freezing. A 50/50 solution of Caterpillar (permanent-type) Antifreeze and approved water will give protection to -29°C (-20°F).If it will be impossible to start the engine periodically, consult your Caterpillar dealer for instructions to prepare your engine for longer storage periods.Refer to Storage Procedures For Caterpillar Products, SEHS9031, for more detailed information on engine storage.Generator Storage Procedure
When a generator is stored, moisture may condense in the windings. Use a dry storage space and space heaters to minimize condensation. Refer to: Service Manual for SR4 Generators, SENR3985, or Special Instruction, SEHS9124, Cleaning and Drying of Caterpillar Electric Set Generators, or contact your Caterpillar dealer.After Storage
Test the main stator windings with a megohmmeter: * Before the initial startup of the generator set.* Every 3 months* if the generator is operating
When it is necessary to remove a component on an angle, remember that the capacity of an eyebolt is less as the angle between the supporting members and the object becomes less than 90 degrees. Eye Bolts and brackets should never be bent, and should only be loaded under tension.
Use a hoist to remove heavy components. Use an adjustable lifting beam to lift the engine. All supporting members (chains and cables) should be parallel to each other, and perpendicular as possible to the top of the object being lifted.Some removals require the use of lifting fixtures, to obtain proper balance and provide safe handling.To remove the engine ONLY, use the lifting eyes equipped with the engine.The lifting eyes are designed for the engine arrangement as sold. Modifying the lifting eyes and/or engine arrangement weight renders the lifting eyes and devices obsolete.If you modify the lifting eyes and/or engine arrangement weight, you are responsible for providing adequate lifting devices. Contact your Caterpillar dealer for information regarding fixtures for proper engine package lifting.Engine Lifting With Generator
Do not use the engine lifting eyes to remove the engine and generator together.Lifting the engine and generator together requires special equipment and procedures. Contact your Caterpillar dealer for information regarding fixtures for proper lifting of your engine package.Engine Lifting With Fuel Tank
Lifting the engine along with a mounted fuel tank requires special equipment and procedures. Do not lift the unit with fuel in the tank. Contact your Caterpillar dealer for information regarding proper engine and fuel tank lifting.Engine Storage
The following Engine Storage procedures and recommendations minimize the possibility of damage to engines stored for one year or less.When an engine is not started for several weeks, the lubricating oil drains from the cylinder walls and piston rings. Rust can then form on the cylinder liner surface, increasing engine wear and decreasing engine life.Special precautions should be used with engines remaining out of service for extended periods.After one year, a complete protection procedure must be followed if the engine is kept in storage longer. To prevent excessive engine wear: * Be sure all lubrication recommendations mentioned in the Maintenance Schedule intervals chart are completed.* If freezing temperatures are expected, check the cooling system for adequate protection against freezing. A 50/50 solution of Caterpillar (permanent-type) Antifreeze and approved water will give protection to -29°C (-20°F).If it will be impossible to start the engine periodically, consult your Caterpillar dealer for instructions to prepare your engine for longer storage periods.Refer to Storage Procedures For Caterpillar Products, SEHS9031, for more detailed information on engine storage.Generator Storage Procedure
When a generator is stored, moisture may condense in the windings. Use a dry storage space and space heaters to minimize condensation. Refer to: Service Manual for SR4 Generators, SENR3985, or Special Instruction, SEHS9124, Cleaning and Drying of Caterpillar Electric Set Generators, or contact your Caterpillar dealer.After Storage
Test the main stator windings with a megohmmeter: * Before the initial startup of the generator set.* Every 3 months* if the generator is operating
Have questions with 104760-7050?
Group cross 104760-7050 ZEXEL
Nissan-Diesel
Nissan-Diesel
104760-7050
9 460 615 094
167001Y60A
INJECTION-PUMP ASSEMBLY
TD42
TD42