Information injection-pump assembly
ZEXEL
104760-4082
1047604082
NISSAN-DIESEL
1670006J04
1670006j04
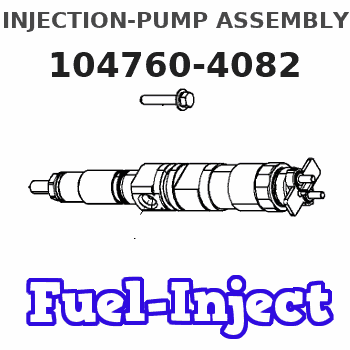
Rating:
Cross reference number
ZEXEL
104760-4082
1047604082
NISSAN-DIESEL
1670006J04
1670006j04
Zexel num
Bosch num
Firm num
Name
Calibration Data:
Adjustment conditions
Test oil
1404 Test oil ISO4113orSAEJ967d
1404 Test oil ISO4113orSAEJ967d
Test oil temperature
degC
45
45
50
Nozzle
105000-2010
Bosch type code
NP-DN12SD12TT
Nozzle holder
105780-2080
Opening pressure
MPa
14.7
14.7
15.19
Opening pressure
kgf/cm2
150
150
155
Injection pipe
Inside diameter - outside diameter - length (mm) mm 2-6-840
Inside diameter - outside diameter - length (mm) mm 2-6-840
Transfer pump pressure
kPa
20
20
20
Transfer pump pressure
kgf/cm2
0.2
0.2
0.2
Direction of rotation (viewed from drive side)
Right R
Right R
(Solenoid timer adjustment condition)
OFF
Injection timing adjustment
Pump speed
r/min
1000
1000
1000
Average injection quantity
mm3/st.
51.2
50.7
51.7
Difference in delivery
mm3/st.
3.5
Basic
*
Injection timing adjustment_02
Pump speed
r/min
2300
2300
2300
Average injection quantity
mm3/st.
16.7
14.2
19.2
Injection timing adjustment_03
Pump speed
r/min
2100
2100
2100
Average injection quantity
mm3/st.
43.8
39.3
48.3
Injection timing adjustment_04
Pump speed
r/min
2000
2000
2000
Average injection quantity
mm3/st.
45
42.9
47.1
Injection timing adjustment_05
Pump speed
r/min
1000
1000
1000
Average injection quantity
mm3/st.
51.2
50.2
52.2
Injection timing adjustment_06
Pump speed
r/min
600
600
600
Average injection quantity
mm3/st.
52.3
50.3
54.3
Injection quantity adjustment
Pump speed
r/min
2300
2300
2300
Average injection quantity
mm3/st.
16.7
14.7
18.7
Basic
*
Injection quantity adjustment_02
Pump speed
r/min
2500
2500
2500
Average injection quantity
mm3/st.
5
Governor adjustment
Pump speed
r/min
350
350
350
Average injection quantity
mm3/st.
8.8
6.8
10.8
Difference in delivery
mm3/st.
2
Basic
*
Governor adjustment_02
Pump speed
r/min
350
350
350
Average injection quantity
mm3/st.
8.8
6.8
10.8
Governor adjustment_03
Pump speed
r/min
450
450
450
Average injection quantity
mm3/st.
3
Timer adjustment
Pump speed
r/min
100
100
100
Average injection quantity
mm3/st.
65
50
80
Basic
*
Speed control lever angle
Pump speed
r/min
350
350
350
Average injection quantity
mm3/st.
0
0
0
Remarks
Magnet OFF
Magnet OFF
0000000901
Pump speed
r/min
1000
1000
1000
Overflow quantity with S/T ON
cm3/min
399
270
528
_02
Pump speed
r/min
1000
1000
1000
Remarks
Measure (solenoid timer without O-ring).
Measure (solenoid timer without O-ring).
Stop lever angle
Pump speed
r/min
1000
1000
1000
Pressure with S/T ON
kPa
451
412
490
Pressure with S/T ON
kgf/cm2
4.6
4.2
5
Pressure with S/T OFF
kPa
343.5
324
363
Pressure with S/T OFF
kgf/cm2
3.5
3.3
3.7
Basic
*
Stop lever angle_02
Pump speed
r/min
1000
1000
1000
Pressure with S/T ON
kPa
451
412
490
Pressure with S/T ON
kgf/cm2
4.6
4.2
5
Pressure with S/T OFF
kPa
343.5
324
363
Pressure with S/T OFF
kgf/cm2
3.5
3.3
3.7
Stop lever angle_03
Pump speed
r/min
1600
1600
1600
Pressure with S/T ON
kPa
588
539
637
Pressure with S/T ON
kgf/cm2
6
5.5
6.5
Pressure with S/T OFF
kPa
470.5
441
500
Pressure with S/T OFF
kgf/cm2
4.8
4.5
5.1
Stop lever angle_04
Pump speed
r/min
1800
1800
1800
Pressure with S/T OFF
kPa
519.5
490
549
Pressure with S/T OFF
kgf/cm2
5.3
5
5.6
0000001101
Pump speed
r/min
1000
1000
1000
Timer stroke with S/T ON
mm
3.8
3.4
4.2
Timer stroke with S/T OFF
mm
1.6
1.4
1.8
Basic
*
_02
Pump speed
r/min
1000
1000
1000
Timer stroke with S/T ON
mm
3.8
3.3
4.3
Timer stroke with S/T OFF
mm
1.6
1.3
1.9
_03
Pump speed
r/min
1800
1800
1800
Timer stroke with S/T OFF
mm
5.5
4.9
6.1
_04
Pump speed
r/min
2300
2300
2300
Timer stroke with S/T OFF
mm
7.3
6.8
7.8
0000001201
Max. applied voltage
V
16
16
16
Test voltage
V
25
24
26
Timing setting
K dimension
mm
3.3
3.2
3.4
KF dimension
mm
6.64
6.54
6.74
MS dimension
mm
1
0.9
1.1
Control lever angle alpha
deg.
55.5
51.5
59.5
Control lever angle beta
deg.
40
35
45
Test data Ex:
0000001801 CONTROL LEVER ANGLE
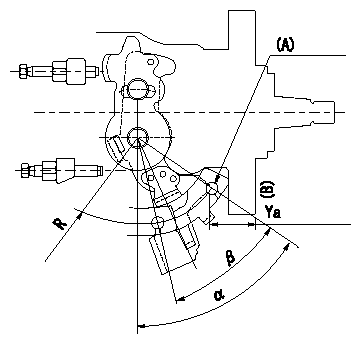
Control lever angle measurement
1. Measure dimension Ya between the end of the lever and the flange face.
2. Measure the lever angle from the pin hole R (plate).
(A) = lever angle and lever reaction force measuring position
----------
Ya=24.3~28.7mm R=53mm
----------
Ya=24.3~28.7mm R=53mm Alpha=51.5~59.5deg Beta=35~45deg
----------
Ya=24.3~28.7mm R=53mm
----------
Ya=24.3~28.7mm R=53mm Alpha=51.5~59.5deg Beta=35~45deg
0000001901 POTENTIOMETER ADJUSTMENT
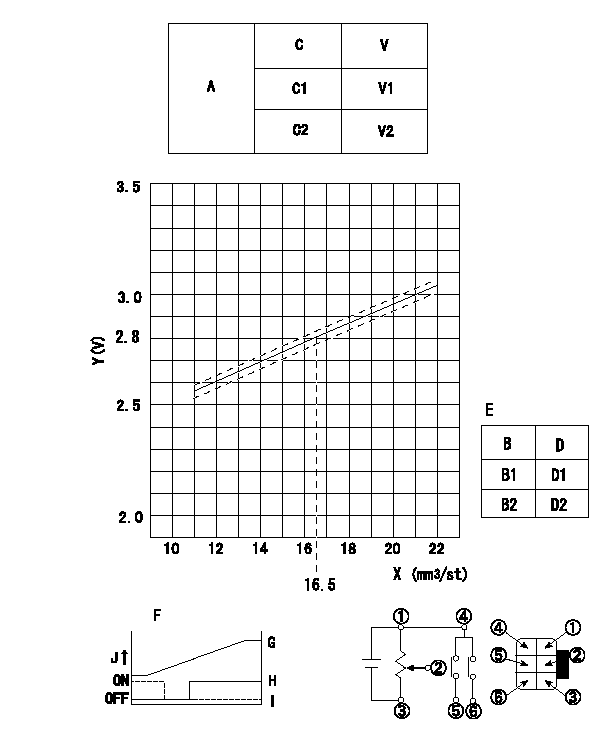
Adjustment of the potentiometer
Voltage conversion formula: V+-0.03 = xQ + y (V)
* Measure the injection quantity at N = N1r/min with the control lever position C3 (equivalent to L1 mm).
Determine the voltage with the conversion formula and adjust the potentiometer.
A:Performance standards for the potentiometer
B:Conversion point
C:Position of the control lever
D:Lever opening (from idle)
E:Standards for the potentiometer's ON/OFF switch
Vi:Applied voltage
V:Potentiometer voltage
X:Injection quantity: Q
Y:Voltage (V)
N1:Pump speed
C3:Position of the control lever
L1:Thickness of the shim
C1:Idle
C2:Full-speed
B1:ON-->OFF
B2:OFF-->ON
F:Connecting diagram for the potentiometer
G:Output when (2) and (3) connected.
H:When (4) or (6) connected: switch OFF to ON.
I:When (4) or (5) connected: switch ON to OFF.
J:Output
----------
x=0.044 y=2.07 N1=700r/min C3=7.5deg L1=4.9mm Vi=10V
----------
V1=1.6+-0.4V V2=8.0+-0.55V Vi=10V D1=6.0+-3.5deg D2=29.0+-3.5deg
----------
x=0.044 y=2.07 N1=700r/min C3=7.5deg L1=4.9mm Vi=10V
----------
V1=1.6+-0.4V V2=8.0+-0.55V Vi=10V D1=6.0+-3.5deg D2=29.0+-3.5deg
Information:
Problem
The retainer clips for the fuel injectors may crack or break on certain Challenger 75 Tractors. Also, the unit injector rocker arms may crack.
Affected Product
Mode & Identification Number
CH75 (4CJ1-308, 4CJ311-317, 4CJ320-331, 4CJ350, 4CJ356,4CJ375-378, 4CJ380, 4CJ382, 4CJ383, 4CJ386, 4CJ391, 4CJ394, 4CJ396, 4CJ406)
Parts Needed
6 - 7E8872 Rocker Arm Assembly (Use as needed)6 - 6I2538 Clip6 - 0R3398 Injector Group (Use as needed)Action Required
See attached rework procedure.
Service Claim Allowances
If required, add the following:
0.5 Hr R&I first fuel injector0.4 Hr R&I each additional fuel injectorParts Disposition
Handle the parts in accordance with your Warranty Bulletin on warranty parts handling.
Attach.
(1-Rework Procedure)Rework Procedure
1. Check for 3X stamped on the block next to the serial number plate. If the block has been stamped do not proceed with the rework unless suspect injectors have recently been installed in that engine. Check SIMS history to be sure.2. Remove hood from over engine, valve covers, and rocker arm stands.3. Inspect the injector rocker arms for the heat code and die code as shown in Illustration 1. Replace any injector rocker arms that have both heat code "1" and die code "1*C" (* Note symbol in Illustration.)
Illustration 1 - Injector Rocker Arm Identification Injector rocker arms must have BOTH heat code "1" and die code "1*C" to be eligible for replacement.
4. Inspect unit injectors for a paint strip across the top face of the spring retainer (either yellow or red). A paint stripe indicates the unit injector has been reworked previously.5. Remove the return to tank fuel line at the fuel manifold adapter (siphon break) and install a 0-100 psi gauge at the manifold.6. Use an O-ring pick to remove the O-ring from the spring retainer of each injector to be reworked. Remove the rocker arm thrust pad from each injector.7. Pressurize fuel system using the priming pump to 30 psi and maintain pressure from 15-30 psi during rework (fuel pressure keeps the injector plunger extended during clip replacement).8. Inspect the 9U5300 Unit Injector Spring Compressor Group. See Illustration 2. The 9U5320 Fixture is for off engine use only.
Illustration 2 - 9U5300 Unit Injector Spring Compressor GroupInstall the compressor group into a rocker arm support bolt hole with the arm aligned over a unit injector spring. Be sure the 5P0541 Nut is backed off to the top of the 9U5321 Tube before tightening the 7X0909 Bolt.
Install the compressor at hole locations closest to the inlet valves.Tighten the 5P0541 Nut to compress the injector spring only enough to allow removal of the clip (the clip is like a valve keeper).
9. Use a small magnet (pencil size works best) and a suitable clip removal tool to remove the old clip from the injector. Do not release tension on the spring until a new clip is installed. Releasing tension before a new clip is installed will cause the injector will come apart. See Illustration 3.
Illustration 3 - Use caution when handling injectors with missing clips. Loose springs and retainers will allow ball to come loose and fall into the engine.10. Inspect the clip
The retainer clips for the fuel injectors may crack or break on certain Challenger 75 Tractors. Also, the unit injector rocker arms may crack.
Affected Product
Mode & Identification Number
CH75 (4CJ1-308, 4CJ311-317, 4CJ320-331, 4CJ350, 4CJ356,4CJ375-378, 4CJ380, 4CJ382, 4CJ383, 4CJ386, 4CJ391, 4CJ394, 4CJ396, 4CJ406)
Parts Needed
6 - 7E8872 Rocker Arm Assembly (Use as needed)6 - 6I2538 Clip6 - 0R3398 Injector Group (Use as needed)Action Required
See attached rework procedure.
Service Claim Allowances
If required, add the following:
0.5 Hr R&I first fuel injector0.4 Hr R&I each additional fuel injectorParts Disposition
Handle the parts in accordance with your Warranty Bulletin on warranty parts handling.
Attach.
(1-Rework Procedure)Rework Procedure
1. Check for 3X stamped on the block next to the serial number plate. If the block has been stamped do not proceed with the rework unless suspect injectors have recently been installed in that engine. Check SIMS history to be sure.2. Remove hood from over engine, valve covers, and rocker arm stands.3. Inspect the injector rocker arms for the heat code and die code as shown in Illustration 1. Replace any injector rocker arms that have both heat code "1" and die code "1*C" (* Note symbol in Illustration.)
Illustration 1 - Injector Rocker Arm Identification Injector rocker arms must have BOTH heat code "1" and die code "1*C" to be eligible for replacement.
4. Inspect unit injectors for a paint strip across the top face of the spring retainer (either yellow or red). A paint stripe indicates the unit injector has been reworked previously.5. Remove the return to tank fuel line at the fuel manifold adapter (siphon break) and install a 0-100 psi gauge at the manifold.6. Use an O-ring pick to remove the O-ring from the spring retainer of each injector to be reworked. Remove the rocker arm thrust pad from each injector.7. Pressurize fuel system using the priming pump to 30 psi and maintain pressure from 15-30 psi during rework (fuel pressure keeps the injector plunger extended during clip replacement).8. Inspect the 9U5300 Unit Injector Spring Compressor Group. See Illustration 2. The 9U5320 Fixture is for off engine use only.
Illustration 2 - 9U5300 Unit Injector Spring Compressor GroupInstall the compressor group into a rocker arm support bolt hole with the arm aligned over a unit injector spring. Be sure the 5P0541 Nut is backed off to the top of the 9U5321 Tube before tightening the 7X0909 Bolt.
Install the compressor at hole locations closest to the inlet valves.Tighten the 5P0541 Nut to compress the injector spring only enough to allow removal of the clip (the clip is like a valve keeper).
9. Use a small magnet (pencil size works best) and a suitable clip removal tool to remove the old clip from the injector. Do not release tension on the spring until a new clip is installed. Releasing tension before a new clip is installed will cause the injector will come apart. See Illustration 3.
Illustration 3 - Use caution when handling injectors with missing clips. Loose springs and retainers will allow ball to come loose and fall into the engine.10. Inspect the clip