Information injection-pump assembly
ZEXEL
104749-1260
1047491260
ISUZU
8942499930
8942499930
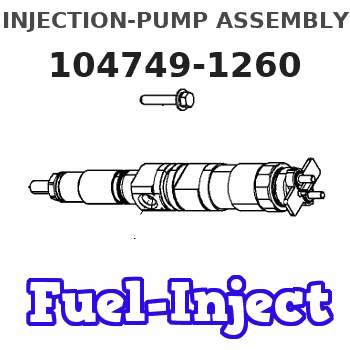
Rating:
Cross reference number
ZEXEL
104749-1260
1047491260
ISUZU
8942499930
8942499930
Zexel num
Bosch num
Firm num
Name
Calibration Data:
Adjustment conditions
Test oil
1404 Test oil ISO4113orSAEJ967d
1404 Test oil ISO4113orSAEJ967d
Test oil temperature
degC
45
45
50
Nozzle
105000-2010
Bosch type code
NP-DN12SD12TT
Nozzle holder
105780-2080
Opening pressure
MPa
14.7
14.7
15.19
Opening pressure
kgf/cm2
150
150
155
Injection pipe
Inside diameter - outside diameter - length (mm) mm 2-6-840
Inside diameter - outside diameter - length (mm) mm 2-6-840
Transfer pump pressure
kPa
20
20
20
Transfer pump pressure
kgf/cm2
0.2
0.2
0.2
Direction of rotation (viewed from drive side)
Right R
Right R
Injection timing adjustment
Pump speed
r/min
1250
1250
1250
Average injection quantity
mm3/st.
35.9
35.4
36.4
Difference in delivery
mm3/st.
2.5
Basic
*
Injection timing adjustment_02
Pump speed
r/min
2600
2600
2600
Average injection quantity
mm3/st.
15.6
13.6
17.6
Injection timing adjustment_03
Pump speed
r/min
2250
2250
2250
Average injection quantity
mm3/st.
34.6
32.6
36.6
Injection timing adjustment_04
Pump speed
r/min
1250
1250
1250
Average injection quantity
mm3/st.
35.9
34.9
36.9
Injection timing adjustment_05
Pump speed
r/min
600
600
600
Average injection quantity
mm3/st.
29.7
27.7
31.7
Injection timing adjustment_06
Pump speed
r/min
1250
1250
1250
Average injection quantity
mm3/st.
35
34.5
35.5
Difference in delivery
mm3/st.
2.5
Basic
*
Remarks
For Japan
For Japan
Injection timing adjustment_07
Pump speed
r/min
2600
2600
2600
Average injection quantity
mm3/st.
15.2
13.2
17.2
Remarks
For Japan
For Japan
Injection timing adjustment_08
Pump speed
r/min
2250
2250
2250
Average injection quantity
mm3/st.
33.8
31.8
35.8
Remarks
For Japan
For Japan
Injection timing adjustment_09
Pump speed
r/min
1250
1250
1250
Average injection quantity
mm3/st.
35
34
36
Remarks
For Japan
For Japan
Injection timing adjustment_10
Pump speed
r/min
600
600
600
Average injection quantity
mm3/st.
29
27
31
Remarks
For Japan
For Japan
Injection quantity adjustment
Pump speed
r/min
2600
2600
2600
Average injection quantity
mm3/st.
15.6
14.6
16.6
Basic
*
Injection quantity adjustment_02
Pump speed
r/min
2900
2900
2900
Average injection quantity
mm3/st.
5.1
Injection quantity adjustment_03
Pump speed
r/min
2600
2600
2600
Average injection quantity
mm3/st.
15.2
14.2
16.2
Basic
*
Remarks
For Japan
For Japan
Injection quantity adjustment_04
Pump speed
r/min
2900
2900
2900
Average injection quantity
mm3/st.
5
Remarks
For Japan
For Japan
Governor adjustment
Pump speed
r/min
315
315
315
Average injection quantity
mm3/st.
7.7
5.7
9.7
Difference in delivery
mm3/st.
2
Basic
*
Governor adjustment_02
Pump speed
r/min
315
315
315
Average injection quantity
mm3/st.
7.7
5.7
9.7
Governor adjustment_03
Pump speed
r/min
500
500
500
Average injection quantity
mm3/st.
0
0
0
Governor adjustment_04
Pump speed
r/min
315
315
315
Average injection quantity
mm3/st.
7.5
5.5
9.5
Difference in delivery
mm3/st.
2
Basic
*
Remarks
For Japan
For Japan
Governor adjustment_05
Pump speed
r/min
315
315
315
Average injection quantity
mm3/st.
7.5
5.5
9.5
Remarks
For Japan
For Japan
Governor adjustment_06
Pump speed
r/min
500
500
500
Average injection quantity
mm3/st.
0
0
0
Remarks
For Japan
For Japan
Timer adjustment
Pump speed
r/min
100
100
100
Average injection quantity
mm3/st.
64
54
74
Basic
*
Timer adjustment_02
Pump speed
r/min
100
100
100
Average injection quantity
mm3/st.
62
52
72
Basic
*
Remarks
For Japan
For Japan
Speed control lever angle
Pump speed
r/min
315
315
315
Average injection quantity
mm3/st.
0
0
0
Remarks
Magnet OFF
Magnet OFF
Speed control lever angle_02
Pump speed
r/min
315
315
315
Average injection quantity
mm3/st.
0
0
0
Remarks
For Japan: Magnet OFF
For Japan: Magnet OFF
0000000901
Pump speed
r/min
1250
1250
1250
Overflow quantity
cm3/min
456
324
588
_02
Pump speed
r/min
1250
1250
1250
Overflow quantity
cm3/min
480
348
612
Remarks
For Japan
For Japan
Stop lever angle
Pump speed
r/min
1250
1250
1250
Pressure
kPa
480.5
461
500
Pressure
kgf/cm2
4.9
4.7
5.1
Basic
*
Stop lever angle_02
Pump speed
r/min
1250
1250
1250
Pressure
kPa
480.5
461
500
Pressure
kgf/cm2
4.9
4.7
5.1
Stop lever angle_03
Pump speed
r/min
2000
2000
2000
Pressure
kPa
647.5
618
677
Pressure
kgf/cm2
6.6
6.3
6.9
Stop lever angle_04
Pump speed
r/min
1250
1250
1250
Pressure
kPa
470.5
451
490
Pressure
kgf/cm2
4.8
4.6
5
Basic
*
Remarks
For Japan
For Japan
Stop lever angle_05
Pump speed
r/min
1250
1250
1250
Pressure
kPa
470.5
451
490
Pressure
kgf/cm2
4.8
4.6
5
Remarks
For Japan
For Japan
Stop lever angle_06
Pump speed
r/min
2000
2000
2000
Pressure
kPa
637.5
608
667
Pressure
kgf/cm2
6.5
6.2
6.8
Remarks
For Japan
For Japan
0000001101
Pump speed
r/min
1250
1250
1250
Timer stroke
mm
2.7
2.5
2.9
Basic
*
_02
Pump speed
r/min
1250
1250
1250
Timer stroke
mm
2.7
2.4
3
_03
Pump speed
r/min
2000
2000
2000
Timer stroke
mm
5.6
5
6.2
_04
Pump speed
r/min
2500
2500
2500
Timer stroke
mm
7.4
7
7.8
_05
Pump speed
r/min
1250
1250
1250
Timer stroke
mm
2.6
2.4
2.8
Basic
*
Remarks
For Japan
For Japan
_06
Pump speed
r/min
1250
1250
1250
Timer stroke
mm
2.6
2.3
2.9
Remarks
For Japan
For Japan
_07
Pump speed
r/min
2000
2000
2000
Timer stroke
mm
5.5
4.9
6.1
Remarks
For Japan
For Japan
_08
Pump speed
r/min
2500
2500
2500
Timer stroke
mm
7.35
6.9
7.8
Remarks
For Japan
For Japan
0000001201
Max. applied voltage
V
8
8
8
Test voltage
V
13
12
14
0000001501
Pump speed
r/min
1250
1250
1250
Atmospheric pressure difference
kPa
-21.9
-22.6
-21.2
Atmospheric pressure difference
mmHg
-164
-169
-159
Decrease qty
mm3/st.
3.6
3.1
4.1
Basic
*
_02
Pump speed
r/min
1250
1250
1250
Atmospheric pressure difference
kPa
-21.9
-22.6
-21.2
Atmospheric pressure difference
mmHg
-164
-169
-159
Decrease qty
mm3/st.
3.6
2.6
4.6
_03
Pump speed
r/min
1250
1250
1250
Atmospheric pressure difference
kPa
-21.9
-22.6
-21.2
Atmospheric pressure difference
mmHg
-164
-169
-159
Decrease qty
mm3/st.
3.5
3
4
Basic
*
Remarks
For Japan
For Japan
_04
Pump speed
r/min
1250
1250
1250
Atmospheric pressure difference
kPa
-21.9
-22.6
-21.2
Atmospheric pressure difference
mmHg
-164
-169
-159
Decrease qty
mm3/st.
3.5
2.5
4.5
Remarks
For Japan
For Japan
Timing setting
K dimension
mm
3.3
3.2
3.4
KF dimension
mm
5.8
5.7
5.9
MS dimension
mm
1.6
1.5
1.7
Pre-stroke
mm
0.25
0.23
0.27
Control lever angle alpha
deg.
2
-2
6
Control lever angle beta
deg.
38
33
43
Test data Ex:
0000001501 ANEROID COMPENSATOR
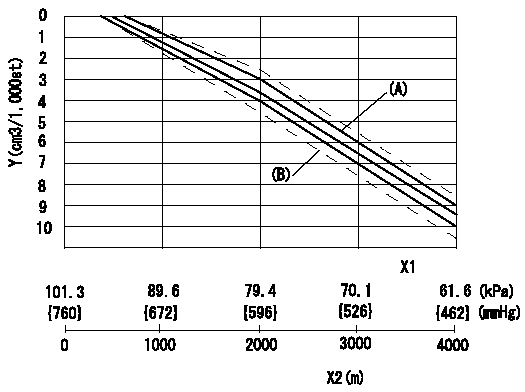
ACS adjustment
Full load injection quantity at high altitudes and ACS adjusting method
1. Full load injection quantity adjustment
(1)Remove the ACS cover and remove the bellows and adjusting shim.
(2)Perform all adjustments as per the adjustment standard except for ACS adjustment.
2. ACS adjustment
Adjust the ACS so that the reduction amount corresponds to the altitude in the table.
X1 = atmospheric pressure
X2 = altitude
Y = decrease quantity
(A) = adjustment value
(B) = test value
----------
N1=1250r/min
----------
----------
N1=1250r/min
----------
Information:
Introduction
The problem identified below does not have a permanent solution. Until a permanent solution is known, use the solution that is identified below.Problem
There have been instances of faults codes with the DEF Pump, which can lead to an engine derate condition. Affected part numbers for the DEF pumps are:
473-2749 Diesel Exhaust Fluid Pump Gp
473-2750 Diesel Exhaust Fluid Pump Gp
466-8285 Diesel Exhaust Fluid Pump Gp
466-8286 Diesel Exhaust Fluid Pump GpThe codes can be:
Table 1
Event Codes
J1939 Code CDL Code Description
4334-16 E930 (2) Aftertreatment #1 DEF #1 Pressure (absolute) : High - moderate severity (2)
4334-18 E931 (2) Aftertreatment #1 SCR Dosing Re-agent Absolute Pressure : Low - moderate severity (2)
4374-5 E3118 (6) Aftertreatment #1 Diesel Exhaust Fluid Pump Motor Speed : Current Below Normal
5392-31 E1370 (2) Aftertreatment Diesel Exhaust Fluid Dosing Unit Loss of Prime Caterpillar is investigating the root cause of these issues. To support the investigation, Caterpillar is requesting that the following steps are completed, documented, and recorded in SIMSi.Solution
Before starting any troubleshooting, download a Product Status Report (PSR) from the affected engine. Ensure that the PDF and the XML version of the PSR are downloaded, with the Histogram option selected in the Download List.Follow the appropriate troubleshooting steps for the displayed fault codes. Document the results of the troubleshooting tests in the relevant tables. Refer to Tables 2, 3, and 4.If Troubleshoot requests the Pump and Electronics Unit (PEU) to be replaced, conduct the following inspection before removal of the PEU.
Check the DEF for contamination, if the relevant troubleshooting procedure has not instructed you to do so. Refer to "System Operation Testing and Adjusting", Diesel Exhaust Fluid Quality - Test for the correct procedure.
Inspect the DEF tank cap, DEF header filter, DEF pump filter for any visible obstruction
Illustration 1 g06152768
(1) DEF line in
(2) DEF line out
(3) DEF line out let connection
(4) DEF line inlet connection
(5) Injector DEF line
Inspect and photograph both ends of the DEF fluid lines. If the ends of the lines are damaged or swollen, replace the DEF lines. Refer to "Disassembly and Assembly", Diesel Exhaust Fluid Lines - Remove and Install.At the end of the service take another PSR irrespective of outcome. Ensure that the PDF and the XML version of the PSR are downloaded, with the Histogram option selected in the Download List.If the troubleshooting steps have required a component to be changed, hold all replaced components for 30 days for a possible Parts Return Request (PRR). Make sure to include the closed work order paperwork.In every instance submit a SIMSi report, complete with TIB number M0079072, CPI number 359775 and submit through the CPI feedback tool within the SIMSi.
Detailed description of symptom experienced and under what conditions issue occurred
Product Status Report (PSR) before and after troubleshooting. Ensure that the PDF and the XML version of the PSR are downloaded, with the Histogram option selected in the Download List.
Completed Troubleshooting steps tables. Refer to Tables 2, 3, and 4.
Details of DEF tank cap, DEF header filter, DEF pump filter, visual inspection
Photos of DEF fluid lines
Details
The problem identified below does not have a permanent solution. Until a permanent solution is known, use the solution that is identified below.Problem
There have been instances of faults codes with the DEF Pump, which can lead to an engine derate condition. Affected part numbers for the DEF pumps are:
473-2749 Diesel Exhaust Fluid Pump Gp
473-2750 Diesel Exhaust Fluid Pump Gp
466-8285 Diesel Exhaust Fluid Pump Gp
466-8286 Diesel Exhaust Fluid Pump GpThe codes can be:
Table 1
Event Codes
J1939 Code CDL Code Description
4334-16 E930 (2) Aftertreatment #1 DEF #1 Pressure (absolute) : High - moderate severity (2)
4334-18 E931 (2) Aftertreatment #1 SCR Dosing Re-agent Absolute Pressure : Low - moderate severity (2)
4374-5 E3118 (6) Aftertreatment #1 Diesel Exhaust Fluid Pump Motor Speed : Current Below Normal
5392-31 E1370 (2) Aftertreatment Diesel Exhaust Fluid Dosing Unit Loss of Prime Caterpillar is investigating the root cause of these issues. To support the investigation, Caterpillar is requesting that the following steps are completed, documented, and recorded in SIMSi.Solution
Before starting any troubleshooting, download a Product Status Report (PSR) from the affected engine. Ensure that the PDF and the XML version of the PSR are downloaded, with the Histogram option selected in the Download List.Follow the appropriate troubleshooting steps for the displayed fault codes. Document the results of the troubleshooting tests in the relevant tables. Refer to Tables 2, 3, and 4.If Troubleshoot requests the Pump and Electronics Unit (PEU) to be replaced, conduct the following inspection before removal of the PEU.
Check the DEF for contamination, if the relevant troubleshooting procedure has not instructed you to do so. Refer to "System Operation Testing and Adjusting", Diesel Exhaust Fluid Quality - Test for the correct procedure.
Inspect the DEF tank cap, DEF header filter, DEF pump filter for any visible obstruction
Illustration 1 g06152768
(1) DEF line in
(2) DEF line out
(3) DEF line out let connection
(4) DEF line inlet connection
(5) Injector DEF line
Inspect and photograph both ends of the DEF fluid lines. If the ends of the lines are damaged or swollen, replace the DEF lines. Refer to "Disassembly and Assembly", Diesel Exhaust Fluid Lines - Remove and Install.At the end of the service take another PSR irrespective of outcome. Ensure that the PDF and the XML version of the PSR are downloaded, with the Histogram option selected in the Download List.If the troubleshooting steps have required a component to be changed, hold all replaced components for 30 days for a possible Parts Return Request (PRR). Make sure to include the closed work order paperwork.In every instance submit a SIMSi report, complete with TIB number M0079072, CPI number 359775 and submit through the CPI feedback tool within the SIMSi.
Detailed description of symptom experienced and under what conditions issue occurred
Product Status Report (PSR) before and after troubleshooting. Ensure that the PDF and the XML version of the PSR are downloaded, with the Histogram option selected in the Download List.
Completed Troubleshooting steps tables. Refer to Tables 2, 3, and 4.
Details of DEF tank cap, DEF header filter, DEF pump filter, visual inspection
Photos of DEF fluid lines
Details