Information injection-pump assembly
ZEXEL
104748-1642
1047481642
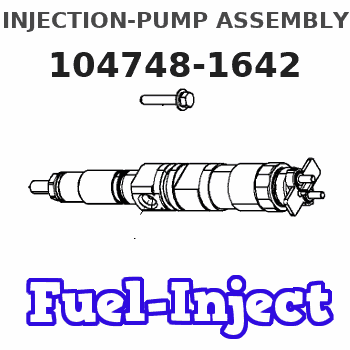
Rating:
Cross reference number
ZEXEL
104748-1642
1047481642
Zexel num
Bosch num
Firm num
Name
Calibration Data:
Adjustment conditions
Test oil
1404 Test oil ISO4113orSAEJ967d
1404 Test oil ISO4113orSAEJ967d
Test oil temperature
degC
45
45
50
Nozzle
105000-2010
Bosch type code
NP-DN12SD12TT
Nozzle holder
105780-2080
Opening pressure
MPa
14.7
14.7
15.19
Opening pressure
kgf/cm2
150
150
155
Injection pipe
Inside diameter - outside diameter - length (mm) mm 2-6-840
Inside diameter - outside diameter - length (mm) mm 2-6-840
Transfer pump pressure
kPa
20
20
20
Transfer pump pressure
kgf/cm2
0.2
0.2
0.2
Direction of rotation (viewed from drive side)
Right R
Right R
Injection timing adjustment
Pump speed
r/min
1250
1250
1250
Average injection quantity
mm3/st.
31.2
30.7
31.7
Difference in delivery
mm3/st.
2.5
Basic
*
Injection timing adjustment_02
Pump speed
r/min
2965
2965
2965
Average injection quantity
mm3/st.
11.1
7.6
14.6
Injection timing adjustment_03
Pump speed
r/min
2700
2700
2700
Average injection quantity
mm3/st.
25.3
21.8
28.8
Injection timing adjustment_04
Pump speed
r/min
2600
2600
2600
Average injection quantity
mm3/st.
26.9
24.8
29
Injection timing adjustment_05
Pump speed
r/min
2500
2500
2500
Average injection quantity
mm3/st.
27
25
29
Injection timing adjustment_06
Pump speed
r/min
1250
1250
1250
Average injection quantity
mm3/st.
31.2
30.2
32.2
Injection timing adjustment_07
Pump speed
r/min
600
600
600
Average injection quantity
mm3/st.
29.7
27.7
31.7
Injection quantity adjustment
Pump speed
r/min
2965
2965
2965
Average injection quantity
mm3/st.
11.1
8.1
14.1
Difference in delivery
mm3/st.
3.5
Basic
*
Injection quantity adjustment_02
Pump speed
r/min
2900
2900
2900
Average injection quantity
mm3/st.
3
Remarks
Insert a 4.5+-0.1 mm shim between the C/L and the full speed position and measure injection quantity.
Insert a 4.5+-0.1 mm shim between the C/L and the full speed position and measure injection quantity.
Governor adjustment
Pump speed
r/min
375
375
375
Average injection quantity
mm3/st.
6
4
8
Difference in delivery
mm3/st.
2
Basic
*
Governor adjustment_02
Pump speed
r/min
375
375
375
Average injection quantity
mm3/st.
6
4
8
Governor adjustment_03
Pump speed
r/min
450
450
450
Average injection quantity
mm3/st.
2
Timer adjustment
Pump speed
r/min
100
100
100
Average injection quantity
mm3/st.
50
50
Basic
*
Speed control lever angle
Pump speed
r/min
375
375
375
Average injection quantity
mm3/st.
0
0
0
Remarks
Magnet OFF
Magnet OFF
0000000901
Pump speed
r/min
1250
1250
1250
Overflow quantity
cm3/min
369
240
498
Stop lever angle
Pump speed
r/min
1250
1250
1250
Pressure
kPa
362.5
343
382
Pressure
kgf/cm2
3.7
3.5
3.9
Basic
*
Stop lever angle_02
Pump speed
r/min
500
500
500
Pressure
kPa
186.5
157
216
Pressure
kgf/cm2
1.9
1.6
2.2
Stop lever angle_03
Pump speed
r/min
1250
1250
1250
Pressure
kPa
362.5
343
382
Pressure
kgf/cm2
3.7
3.5
3.9
Stop lever angle_04
Pump speed
r/min
2000
2000
2000
Pressure
kPa
539.5
510
569
Pressure
kgf/cm2
5.5
5.2
5.8
Stop lever angle_05
Pump speed
r/min
2300
2300
2300
Pressure
kPa
617.5
588
647
Pressure
kgf/cm2
6.3
6
6.6
0000001101
Pump speed
r/min
1250
1250
1250
Timer stroke
mm
3.1
2.9
3.3
Basic
*
_02
Pump speed
r/min
620
520
720
Timer stroke
mm
0.5
0.5
0.5
_03
Pump speed
r/min
1250
1250
1250
Timer stroke
mm
3.1
2.8
3.4
_04
Pump speed
r/min
2000
2000
2000
Timer stroke
mm
6.1
5.5
6.7
_05
Pump speed
r/min
2300
2300
2300
Timer stroke
mm
7.4
7
7.8
0000001201
Max. applied voltage
V
8
8
8
Test voltage
V
13
12
14
0000001401
Pump speed
r/min
1250
1250
1250
Average injection quantity
mm3/st.
18.1
17.6
18.6
Timer stroke variation dT
mm
0.8
0.6
1
Basic
*
_02
Pump speed
r/min
1250
1250
1250
Average injection quantity
mm3/st.
18.1
17.1
19.1
Timer stroke variation dT
mm
0.8
0.4
1.2
_03
Pump speed
r/min
1250
1250
1250
Average injection quantity
mm3/st.
7
5.5
8.5
Timer stroke variation dT
mm
2.2
1.6
2.8
Timing setting
K dimension
mm
3.3
3.2
3.4
KF dimension
mm
5.8
5.7
5.9
MS dimension
mm
1.6
1.5
1.7
Control lever angle alpha
deg.
20
16
24
Control lever angle beta
deg.
45
40
50
Test data Ex:
0000001801 V-FICD ADJUSTMENT
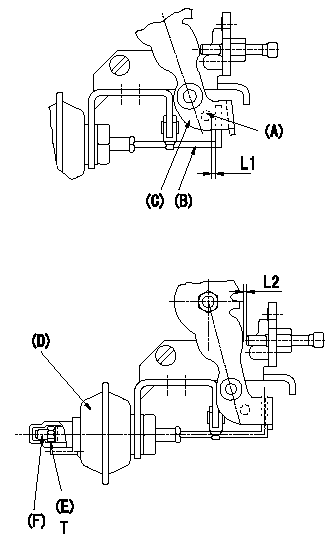
Adjustment of the V-FICD (perform with W-FICD released)
1. Adjust to obtain L1.
2. Confirm that L2 is obtained when negative pressure P1 (kPa) {P2 (mmHg)} is applied to the actuator.
Adjust the stroke using the actuator stroke adjusting screw (F).
(A): Pin
(B): Actuator shaft
(C): Control lever
(D): Actuator
(E): Lock nut (torque T)
----------
L1=1+1mm L2=1.6+-0.1mm P1=-46.7kPa P2=-350mmHg
----------
L1=1+1mm L2=1.6+-0.1mm T=1.2~1.5N-m{0.12~0.15kgf-m}
----------
L1=1+1mm L2=1.6+-0.1mm P1=-46.7kPa P2=-350mmHg
----------
L1=1+1mm L2=1.6+-0.1mm T=1.2~1.5N-m{0.12~0.15kgf-m}
0000001901 W-CSD ADJUSTMENT
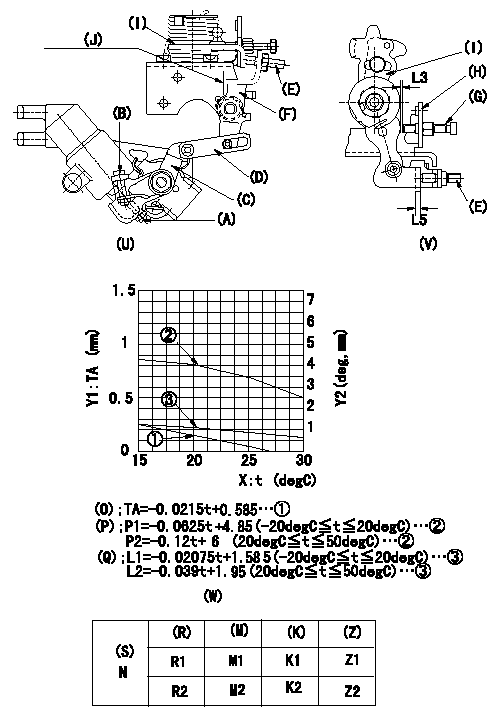
Adjustment of the W-CSD
1. Adjustment of the timer stroke
Adjust screw (A) so that the timer stroke is the value determined from the graph (W) [(V), (W)].
2. Adjustment of the position of the intermediate lever.
Insert a shim L3 between the control lever (I) and the idle screw (G).
Align the intermediate lever (F) with the aligning mark (J) and then fix the intermediate lever adjusting screw (E) so that (E) contacts the shim between (E) and (I). [(U), (V)]
3. Adjustment of the FICD
Insert a shim L4 between the control lever (I) and the idle set screw (G).
Use adjusting screw (B) to fix the CSD lever (C) in the position where it operates the intermediate lever (F) via the rod (D). [(U), (V), (W)]
(O) Timer stroke adjustment (mm)
(P): lever angle (deg)
(Q): lever angle (deg)
The (Q) indicates the clearance between the control lever and the idle set screw.
X:Temperature t (deg C)
Y1:Timer stroke TA (mm)
Y2:Control lever position at theta L (deg, mm)
(R): cooling water temperature (deg C)
(S): cooling water temperature: increase direction
N:Pump speed
(M): timer piston stroke (mm)
(K): colored ring
(Z): lever position (mm)
----------
L3=1.2+-0.05mm L4=L3+-0.05mm L5=-mm
----------
L3=1.2+-0.05mm L5=-mm R1=-degC R2=-degC M1=-mm M2=-mm K1=-deg K2=-deg Z1=-mm Z2=-mm
----------
L3=1.2+-0.05mm L4=L3+-0.05mm L5=-mm
----------
L3=1.2+-0.05mm L5=-mm R1=-degC R2=-degC M1=-mm M2=-mm K1=-deg K2=-deg Z1=-mm Z2=-mm
Information:
Electronic Controls
The electronic controller consists of two main components: the Electronic Control Module (ECM) and the Personality Module. The ECM is the computer which controls the PEEC engine. The Personality Module is the software which controls how the computer behaves. The two must be used together: neither can do anything by itself.Rack Controls
The rack mechanism on a PEEC III engine is very similar to a mechanical 3406 engine. The fuel injection pump is nearly identical; the rack is moved by a servo valve which receives oil pressure from the fuel injection pump. However, the PEEC III servo spool is moved by a solenoid (BTM) rather than by a linkage controlled by flyweights and springs.PEEC III determines a "desired rpm" based on the throttle position, vehicle speed, customer specified parameters, and certain diagnostic codes. The PEEC III governor tries to maintain the desired rpm by sensing actual engine speed using the engine speed sensor, then controlling the rack to achieve the desired rpm.PEEC III RPM Control Logic To move the rack, PEEC III adjusts the voltage to the rack solenoid (BTM) to increase rack. More voltage results in more rack. PEEC III knows how far the rack went by reading the rack position sensor. PEEC III increases the voltage to the rack solenoid until it senses the rack is in the desired position.PEEC III Electronic Governor PEEC III sets certain limits on rack motion. "FRC Rack" is a rack limit based on fuel-air ratio control, for emissions purposes. It works similar to a mechanical engine FARC; when PEEC III senses a higher boost pressure (more air into cylinder), it increases the FRC Rack limit, which allows more fuel into the cylinder. "Rated Rack" is a rack limit based on horsepower of the engine. It is similar to the rack stops and torque springs on a mechanical engine. It provides horsepower and torque curves for a specific engine family and rating. All of these limits are programmed by the factory into the personality module.Timing Advance Controls
The timing advance mechanism is the same as the 3406 mechanical engine, except the Timing solenoid (BTM), instead of the flyweights, controls timing advance. PEEC III adjusts voltage to the timing solenoid to change timing advance. More voltage results in more timing advance. PEEC III knows how much advance was achieved by reading the timing position sensor. PEEC III simply increases voltage to the timing solenoid until it senses that the timing advance is in the desired position.PEEC III Timing Advance Programmable Parameters
Certain parameters that affect PEEC III 3406 Diesel Engine operation may be changed with electronic service tools (either the ECAP or DDT). The parameters are stored in the ECM, and are protected from unauthorized changes by passwords.These parameters are either "System Configuration Parameters" or "Customer Parameters". System Configuration Parameters are those that effect horsepower family or emissions. Customer Parameters are those that affect cruise control, vehicle speed limits, progressive shifting, horsepower rating within a family, engine protection mode, and PTO operation.Some parameters may
The electronic controller consists of two main components: the Electronic Control Module (ECM) and the Personality Module. The ECM is the computer which controls the PEEC engine. The Personality Module is the software which controls how the computer behaves. The two must be used together: neither can do anything by itself.Rack Controls
The rack mechanism on a PEEC III engine is very similar to a mechanical 3406 engine. The fuel injection pump is nearly identical; the rack is moved by a servo valve which receives oil pressure from the fuel injection pump. However, the PEEC III servo spool is moved by a solenoid (BTM) rather than by a linkage controlled by flyweights and springs.PEEC III determines a "desired rpm" based on the throttle position, vehicle speed, customer specified parameters, and certain diagnostic codes. The PEEC III governor tries to maintain the desired rpm by sensing actual engine speed using the engine speed sensor, then controlling the rack to achieve the desired rpm.PEEC III RPM Control Logic To move the rack, PEEC III adjusts the voltage to the rack solenoid (BTM) to increase rack. More voltage results in more rack. PEEC III knows how far the rack went by reading the rack position sensor. PEEC III increases the voltage to the rack solenoid until it senses the rack is in the desired position.PEEC III Electronic Governor PEEC III sets certain limits on rack motion. "FRC Rack" is a rack limit based on fuel-air ratio control, for emissions purposes. It works similar to a mechanical engine FARC; when PEEC III senses a higher boost pressure (more air into cylinder), it increases the FRC Rack limit, which allows more fuel into the cylinder. "Rated Rack" is a rack limit based on horsepower of the engine. It is similar to the rack stops and torque springs on a mechanical engine. It provides horsepower and torque curves for a specific engine family and rating. All of these limits are programmed by the factory into the personality module.Timing Advance Controls
The timing advance mechanism is the same as the 3406 mechanical engine, except the Timing solenoid (BTM), instead of the flyweights, controls timing advance. PEEC III adjusts voltage to the timing solenoid to change timing advance. More voltage results in more timing advance. PEEC III knows how much advance was achieved by reading the timing position sensor. PEEC III simply increases voltage to the timing solenoid until it senses that the timing advance is in the desired position.PEEC III Timing Advance Programmable Parameters
Certain parameters that affect PEEC III 3406 Diesel Engine operation may be changed with electronic service tools (either the ECAP or DDT). The parameters are stored in the ECM, and are protected from unauthorized changes by passwords.These parameters are either "System Configuration Parameters" or "Customer Parameters". System Configuration Parameters are those that effect horsepower family or emissions. Customer Parameters are those that affect cruise control, vehicle speed limits, progressive shifting, horsepower rating within a family, engine protection mode, and PTO operation.Some parameters may