Information injection-pump assembly
BOSCH
9 460 613 252
9460613252
ZEXEL
104746-6500
1047466500
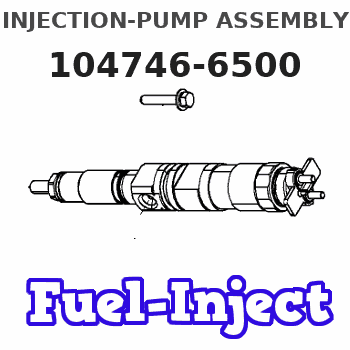
Rating:
Components :
0. | INJECTION-PUMP ASSEMBLY | 104746-6500 |
1. | _ | |
2. | FUEL INJECTION PUMP | 104646-6500 |
3. | NUMBER PLATE | 146968-7400 |
4. | _ | 146672-1720 |
5. | CAPSULE | |
6. | ADJUSTING DEVICE | 146679-4720 |
7. | NOZZLE AND HOLDER ASSY | 105118-6532 |
8. | Nozzle and Holder | 8-97188-521-0 |
9. | Open Pre:MPa(Kqf/cm2) | 18.1{185} |
10. | NOZZLE-HOLDER | 105048-3230 |
11. | NOZZLE | 105017-2280 |
Scheme ###:
1/6. | [1] | 146601-0700 | PACKING RING |
6. | [1] | 146100-0120 | SUPPLY PUMP |
9. | [1] | 146103-0000 | COVER |
10. | [2] | 139104-0000 | FLAT-HEAD SCREW |
12. | [1] | 146200-0820 | DRIVE SHAFT |
12/1. | [1] | 146200-0800 | DRIVE SHAFT |
12/2. | [1] | 146201-0000 | WOODRUFF KEY |
12/3. | [2] | 146202-0100 | DAMPER |
12/4. | [1] | 146203-0000 | TOOTHED GEAR |
17. | [1] | 146204-0000 | PLAIN WASHER |
20. | [1] | 146210-4120 | ROLLER SET |
24. | [1] | 146303-0000 | BEARING PIN |
25. | [1] | 146304-0000 | BEARING PIN |
26. | [1] | 146305-0000 | CLAMPING BAND |
27. | [1] | 146205-0100 | SLOTTED WASHER |
29. | [1] | 146220-0720 | CAM PLATE |
30. | [1] | 146600-0800 | O-RING |
31. | [1] | 146300-4000 | PUMP PLUNGER |
32. | [1] | 146301-0000 | SLIDING PIECE |
33. | [1] | 146603-0700 | SHIM D17.5&7.5T0.60 |
34. | [1] | 146302-3500 | COMPRESSION SPRING |
34B. | [1] | 146302-3600 | COMPRESSION SPRING |
34C. | [1] | 146302-3400 | COMPRESSION SPRING |
35/1. | [0] | 146603-0700 | SHIM D17.5&7.5T0.60 |
35/1. | [0] | 146603-0800 | SHIM D17.5&7.5T0.70 |
35/1. | [0] | 146603-0900 | SHIM D17.5&7.5T0.90 |
35/1. | [0] | 146603-1000 | SHIM D17.5&7.5T1.00 |
35/1. | [0] | 146603-1100 | SHIM D17.5&7.5T1.20 |
35/1. | [0] | 146603-3600 | SHIM D17.5&7.5T2.40 |
36. | [1] | 146600-0800 | O-RING |
37. | [1] | 146310-0700 | COVER |
38. | [2] | 146620-5000 | BLEEDER SCREW |
39. | [1] | 146310-5100 | COVER |
40. | [2] | 146620-5000 | BLEEDER SCREW |
43. | [1] | 146230-0000 | SHIM |
44. | [1] | 146230-0100 | PLAIN WASHER |
45. | [1] | 146231-0001 | SLOTTED WASHER |
47. | [2] | 146233-0000 | SLOTTED WASHER |
48/1. | [1] | 146603-0000 | SHIM D17.0&5.2T0.50 |
48/1. | [1] | 146603-0100 | SHIM D17.0&5.2T0.80 |
48/1. | [1] | 146603-0200 | SHIM D17.0&5.2T1.00 |
48/1. | [1] | 146603-0300 | SHIM D17.0&5.2T1.20 |
48/1. | [1] | 146603-0400 | SHIM D17.0&5.2T1.50 |
48/1. | [1] | 146603-0500 | SHIM D17.0&5.2T1.80 |
48/1. | [1] | 146603-0600 | SHIM D17.0&5.2T2.00 |
48/1. | [1] | 146690-1400 | SHIM D17&5.2T0.9 |
48/1. | [1] | 146690-1500 | SHIM D17&5.2T1.1 |
48/1. | [1] | 146690-1600 | SHIM D17&5.2T1.3 |
48/1. | [1] | 146690-1700 | SHIM D17&5.2T1.4 |
48/1. | [1] | 146690-1800 | SHIM D17&5.2T1.6 |
48/1. | [1] | 146690-1900 | SHIM D17&5.2T1.7 |
48/1. | [1] | 146690-5800 | SHIM D17&5.2T2.1 |
48/1. | [1] | 146690-5900 | SHIM D17&5.2T2.2 |
48/1. | [1] | 146690-6000 | SHIM D17&5.2T2.3 |
48/1. | [1] | 146690-6100 | SHIM D17&5.2T2.4 |
48/1. | [1] | 146690-6200 | SHIM D17&5.2T2.5 |
48/1. | [1] | 146690-6300 | SHIM D17&5.2T2.6 |
48/1. | [1] | 146690-6400 | SHIM D17&5.2T2.7 |
48/1. | [1] | 146690-6500 | SHIM D17&5.2T2.8 |
48/1. | [1] | 146690-6600 | SHIM D17&5.2T2.9 |
48/1. | [1] | 146690-6700 | SHIM D17&5.2T3.0 |
48/1. | [1] | 146690-6800 | SHIM D17&5.2T3.1 |
48/1. | [1] | 146690-6900 | SHIM D17&5.2T3.2 |
48/1. | [1] | 146690-7000 | SHIM D17&5.2T3.3 |
48/1. | [1] | 146690-7100 | SHIM D17&5.2T3.4 |
48/1. | [1] | 146690-7200 | SHIM D17&5.2T0.4 |
48/1. | [1] | 146690-7300 | SHIM D17&5.2T0.6 |
48/1. | [1] | 146690-7400 | SHIM D17&5.2T0.7 |
48/1. | [1] | 146690-7500 | SHIM D17&5.2T1.9 |
48/1. | [1] | 146690-7800 | SHIM D17&5.2T0.2 |
49. | [2] | 146234-0600 | GUIDE PIN |
50. | [1] | 146402-3420 | HYDRAULIC HEAD |
50. | [1] | 146402-3420 | HYDRAULIC HEAD |
50. | [1] | 146402-3420 | HYDRAULIC HEAD |
51. | [1] | 146600-0000 | O-RING |
52/1. | [1] | 146420-0000 | SHIM D9.5&3.0T1.90 |
52/1. | [1] | 146420-0100 | SHIM D9.5&3.0T1.92 |
52/1. | [1] | 146420-0200 | SHIM D9.5&3.0T1.94 |
52/1. | [1] | 146420-0300 | SHIM D9.5&3.0T1.96 |
52/1. | [1] | 146420-0400 | SHIM D9.5&3.0T1.98 |
52/1. | [1] | 146420-0500 | SHIM D9.5&3.0T2.00 |
52/1. | [1] | 146420-0600 | SHIM D9.5&3.0T2.02 |
52/1. | [1] | 146420-0700 | SHIM D9.5&3.0T2.04 |
52/1. | [1] | 146420-0800 | SHIM D9.5&3.0T2.06 |
52/1. | [1] | 146420-0900 | SHIM D9.5&3.0T2.08 |
52/1. | [1] | 146420-1000 | SHIM D9.5&3.0T2.10 |
52/1. | [1] | 146420-1100 | SHIM D9.5&3.0T2.12 |
52/1. | [1] | 146420-1200 | SHIM D9.5&3.0T2.14 |
52/1. | [1] | 146420-1300 | SHIM D9.5&3.0T2.16 |
52/1. | [1] | 146420-1400 | SHIM D9.5&3.0T2.18 |
52/1. | [1] | 146420-1500 | SHIM D9.5&3.0T2.20 |
52/1. | [1] | 146420-1600 | SHIM D9.5&3.0T2.22 |
52/1. | [1] | 146420-1700 | SHIM D9.5&3.0T2.24 |
52/1. | [1] | 146420-1800 | SHIM D9.5&3.0T2.26 |
52/1. | [1] | 146420-1900 | SHIM D9.5&3.0T2.28 |
52/1. | [1] | 146420-2000 | SHIM D9.5&3.0T2.30 |
52/1. | [1] | 146420-2100 | SHIM D9.5&3.0T2.32 |
52/1. | [1] | 146420-2200 | SHIM D9.5&3.0T2.34 |
52/1. | [1] | 146420-2300 | SHIM D9.5&3.0T2.36 |
52/1. | [1] | 146420-2400 | SHIM D9.5&3.0T2.38 |
52/1. | [1] | 146420-2500 | SHIM D9.5&3.0T2.40 |
52/1. | [1] | 146420-2600 | SHIM D9.5&3.0T2.42 |
52/1. | [1] | 146420-2700 | SHIM D9.5&3.0T2.44 |
52/1. | [1] | 146420-2800 | SHIM D9.5&3.0T2.46 |
52/1. | [1] | 146420-2900 | SHIM D9.5&3.0T2.48 |
52/1. | [1] | 146420-3000 | SHIM D9.5&3.0T2.50 |
52/1. | [1] | 146420-3100 | SHIM D9.5&3.0T2.52 |
52/1. | [1] | 146420-3200 | SHIM D9.5&3.0T2.54 |
52/1. | [1] | 146420-3300 | SHIM D9.5&3.0T2.56 |
52/1. | [1] | 146420-3400 | SHIM D9.5&3.0T2.58 |
52/1. | [1] | 146420-3500 | SHIM D9.5&3.0T2.60 |
52/1. | [1] | 146420-3600 | SHIM D9.5&3.0T2.62 |
52/1. | [1] | 146420-3700 | SHIM D9.5&3.0T2.64 |
52/1. | [1] | 146420-3800 | SHIM D9.5&3.0T2.66 |
52/1. | [1] | 146420-3900 | SHIM D9.5&3.0T2.68 |
52/1. | [1] | 146420-4000 | SHIM D9.5&3.0T2.70 |
52/1. | [1] | 146420-4100 | SHIM D9.5&3.0T2.72 |
52/1. | [1] | 146420-4200 | SHIM D9.5&3.0T2.74 |
52/1. | [1] | 146420-4300 | SHIM D9.5&3.0T2.76 |
52/1. | [1] | 146420-4400 | SHIM D9.5&3.0T2.78 |
52/1. | [1] | 146420-4500 | SHIM D9.5&3.0T2.80 |
52/1. | [1] | 146420-4600 | SHIM D9.5&3.0T2.82 |
52/1. | [1] | 146420-4700 | SHIM D9.5&3.0T2.84 |
52/1. | [1] | 146420-4800 | SHIM D9.5&3.0T2.86 |
52/1. | [1] | 146420-4900 | SHIM D9.5&3.0T2.88 |
52/1. | [1] | 146420-5000 | SHIM D9.5&3.0T2.90 |
52/1. | [1] | 146420-5100 | SHIM D9.5&3.0T1.74 |
52/1. | [1] | 146420-5200 | SHIM D9.5&3.0T1.76 |
52/1. | [1] | 146420-5300 | SHIM D9.5&3.0T1.78 |
52/1. | [1] | 146420-5400 | SHIM D9.5&3.0T1.80 |
52/1. | [1] | 146420-5500 | SHIM D9.5&3.0T1.82 |
52/1. | [1] | 146420-5600 | SHIM D9.5&3.0T1.84 |
52/1. | [1] | 146420-5700 | SHIM D9.5&3.0T1.86 |
52/1. | [1] | 146420-5800 | SHIM D9.5&3.0T1.88 |
54. | [4] | 146433-0100 | GASKET D12&6.4T1.00 |
55. | [4] | 146430-1420 | DELIVERY-VALVE ASSEMBLY |
56. | [4] | 146432-0200 | COMPRESSION SPRING |
58. | [4] | 146440-1520 | FITTING |
60. | [4] | 139106-0100 | FLAT-HEAD SCREW |
66. | [1] | 146600-0100 | O-RING |
67. | [1] | 146504-0920 | GOVERNOR COVER |
67/1. | [1] | 146508-1221 | GOVERNOR COVER |
67/13. | [1] | 013020-6040 | UNION NUT M6P1H5 |
67/14. | [1] | 146621-1700 | UNION NUT |
67/15. | [1] | 146526-2800 | BLEEDER SCREW |
67/16. | [1] | 146526-2800 | BLEEDER SCREW |
67/23. | [1] | 146932-0701 | BRACKET |
67/24. | [2] | 139006-4500 | BLEEDER SCREW |
67/64. | [1] | 146932-0800 | BRACKET |
67/69. | [1] | 010206-1040 | HEX-SOCKET-HEAD CAP SCREW |
67/78. | [1] | 146600-4400 | SEAL RING |
67/102. | [1] | 146932-1100 | BRACKET |
67/103. | [1] | 139006-4800 | BLEEDER SCREW |
67/105. | [1] | 139006-4400 | BLEEDER SCREW |
67/200. | [1] | 139308-0300 | PLAIN WASHER |
67/201. | [1] | 146545-3400 | THREADED PIN L53.00 |
67/201B. | [1] | 146545-3500 | THREADED PIN L55.00 |
67/201C. | [1] | 146545-3600 | THREADED PIN L57.00 |
67/202. | [1] | 139208-0900 | UNION NUT |
67/203. | [1] | 146600-1200 | O-RING |
68. | [1] | 146810-1020 | CONTROL SHAFT |
69. | [1] | 139310-0200 | PLAIN WASHER |
72. | [1] | 146831-1800 | CONTROL LEVER |
72B. | [1] | 146831-1900 | CONTROL LEVER |
73. | [1] | 014110-6440 | LOCKING WASHER |
75. | [1] | 146621-4600 | UNION NUT |
95. | [1] | 146865-7020 | FULCRUM LEVER |
104. | [2] | 146568-0000 | SLOTTED SPRING PIN |
105. | [2] | 026508-1140 | GASKET D11.4&8.2T1 |
106. | [2] | 146588-0500 | COILED SPRING |
107. | [1] | 146569-0300 | UNION NUT |
108. | [1] | 146570-0100 | GOVERNOR SHAFT |
109. | [1] | 146600-0400 | O-RING |
110/1. | [1] | 146571-0000 | SHIM D20.2&8.3T1.05 |
110/1. | [1] | 146571-0100 | SHIM D20.2&8.3T1.25 |
110/1. | [1] | 146571-0200 | SHIM D20.2&8.3T1.45 |
110/1. | [1] | 146571-0300 | SHIM D20.2&8.3T1.65 |
110/1. | [1] | 146571-0400 | SHIM D20.2&8.3T1.85 |
110/1. | [1] | 146571-0500 | SHIM D20.2&8.3T1.15 |
110/1. | [1] | 146571-0600 | SHIM D20.2&8.3T1.35 |
110/1. | [1] | 146571-0700 | SHIM D20.2&8.3T1.55 |
110/1. | [1] | 146571-0800 | SHIM D20.2&8.3T1.75 |
111. | [1] | 146602-0600 | PLAIN WASHER D20&8.4T1.40 |
112. | [1] | 146572-0020 | FLYWEIGHT ASSEMBLY |
114. | [1] | 146602-0500 | PLAIN WASHER D17&6.4T1.60 |
115. | [1] | 146975-4200 | SLIDING SLEEVE |
116. | [1] | 146576-0200 | CAP |
117/1. | [1] | 146577-1800 | PLUG L2.10 |
117/1. | [1] | 146577-1900 | PLUG L2.30 |
117/1. | [1] | 146577-2000 | PLUG L2.50 |
117/1. | [1] | 146577-2100 | PLUG L2.70 |
117/1. | [1] | 146577-2200 | PLUG L2.90 |
117/1. | [1] | 146577-2300 | PLUG L3.10 |
117/1. | [1] | 146577-2400 | PLUG L3.30 |
117/1. | [1] | 146577-2500 | PLUG L3.50 |
117/1. | [1] | 146577-2600 | PLUG L3.70 |
117/1. | [1] | 146577-2700 | PLUG L3.90 |
117/1. | [1] | 146577-2800 | PLUG L4.10 |
117/1. | [1] | 146577-2900 | PLUG L4.30 |
117/1. | [1] | 146577-3000 | PLUG L4.50 |
117/1. | [1] | 146577-3100 | PLUG L4.70 |
117/1. | [1] | 146577-3200 | PLUG L4.90 |
117/1. | [1] | 146577-3300 | PLUG L5.10 |
117/1. | [1] | 146577-6700 | PLUG L2.2 |
117/1. | [1] | 146577-6800 | PLUG L2.4 |
117/1. | [1] | 146577-6900 | PLUG L2.6 |
117/1. | [1] | 146577-7000 | PLUG L2.8 |
117/1. | [1] | 146577-7100 | PLUG L3.0 |
117/1. | [1] | 146577-7200 | PLUG L3.2 |
117/1. | [1] | 146577-7300 | PLUG L3.4 |
117/1. | [1] | 146577-7400 | PLUG L3.6 |
117/1. | [1] | 146577-7500 | PLUG L3.8 |
117/1. | [1] | 146577-7600 | PLUG L4.0 |
117/1. | [1] | 146577-7700 | PLUG L4.2 |
117/1. | [1] | 146577-7800 | PLUG L4.4 |
117/1. | [1] | 146577-7900 | PLUG L4.6 |
117/1. | [1] | 146577-8000 | PLUG L4.8 |
117/1. | [1] | 146577-8100 | PLUG L5.0 |
117/1. | [1] | 146877-0000 | PLUG L5.2 |
117/1. | [1] | 146877-0100 | PLUG L5.3 |
117/1. | [1] | 146877-0200 | PLUG L5.4 |
117/1. | [1] | 146877-0300 | PLUG L5.5 |
117/1. | [1] | 146877-4700 | PLUG |
117/1. | [1] | 146877-4800 | PLUG |
117/1. | [1] | 146877-4900 | PLUG |
117/1. | [1] | 146877-5000 | PLUG |
123. | [3] | 139106-0200 | FLAT-HEAD SCREW |
124. | [1] | 146620-0500 | HEX-SOCKET-HEAD CAP SCREW |
130. | [1] | 146421-0320 | CAPSULE |
130/2. | [1] | 026508-1140 | GASKET D11.4&8.2T1 |
130/3. | [1] | 146422-0300 | BLEEDER SCREW |
130/4. | [1] | 146600-0500 | O-RING |
133. | [1] | 146600-0600 | O-RING |
134. | [1] | 146600-0700 | O-RING |
135. | [1] | 146110-0720 | CONTROL VALVE |
135/5. | [1] | 146114-0000 | SPRING WASHER |
136. | [1] | 146120-0020 | OVER FLOW VALVE |
137. | [2] | 139512-0500 | GASKET |
138. | [1] | 146666-8920 | INLET UNION |
158. | [1] | 020105-0940 | BLEEDER SCREW |
159. | [1] | 146625-8000 | PLATE |
163. | [1] | 020146-1270 | BLEEDER SCREW |
205. | [1] | 025804-1610 | WOODRUFF KEY |
220. | [1] | 146587-5000 | COILED SPRING |
240. | [1] | 146650-1220 | PULLING ELECTROMAGNET |
240/8. | [1] | 146600-1700 | O-RING |
242. | [1] | 146658-7320 | WIRE |
243. | [1] | 146621-1000 | UNION NUT |
245. | [2] | 139512-0500 | GASKET |
246. | [1] | 027412-2440 | EYE BOLT |
247. | [1] | 146609-4620 | INLET UNION |
280. | [1] | 146361-0523 | START ADVANCE ASSY |
281. | [1] | 146600-0800 | O-RING |
282. | [2] | 010206-1240 | HEX-SOCKET-HEAD CAP SCREW M6P1L12 |
287. | [1] | 020306-4040 | O-RING |
310. | [1] | 146684-5720 | POTENTCIOMETER |
310/1. | [1] | 146684-5700 | POTENTCIOMETER |
310/2. | [2] | 139104-0400 | FLAT-HEAD SCREW |
310/3. | [1] | 146621-0500 | UNION NUT |
310/4. | [1] | 146620-2900 | FLAT-HEAD SCREW |
310/5. | [1] | 146614-2300 | JOINT CONNECTION |
310/6. | [1] | 146661-0401 | BOOT |
311. | [1] | 010206-1440 | HEX-SOCKET-HEAD CAP SCREW M6P1L14 |
312. | [1] | 146934-4720 | PLATE |
800S. | [1] | 146018-6320 | PUMP HOUSING |
800S/1/6. | [1] | 146601-0700 | PACKING RING |
804S. | [1] | 146232-0720 | COMPRESSION SPRING |
805S. | [1] | 146574-0120 | PARTS SET |
810S. | [1] | 146600-1120 | REPAIR SET |
821S. | [1] | 146210-5720 | ROLLER SET |
835S. | [1] | 146598-1000 | CAP |
836S/1. | [1] | 146598-0600 | CAP L18 |
836S/1. | [1] | 146598-0700 | CAP L21 |
836S/1. | [1] | 146598-0800 | CAP L24 |
836S/1. | [1] | 146598-0900 | CAP L27 |
903. | [1] | 146672-1720 | PULSE GENERATOR |
903/2. | [1] | 146600-1300 | O-RING &13W1.9 |
905. | [1] | 146679-4720 | ADJUSTING DEVICE |
906. | [1] | 146968-7400 | NAMEPLATE |
912. | [1] | 139006-4700 | BLEEDER SCREW |
913. | [1] | 013020-6040 | UNION NUT M6P1H5 |
Include in #2:
104746-6500
as INJECTION-PUMP ASSEMBLY
Cross reference number
BOSCH
9 460 613 252
9460613252
ZEXEL
104746-6500
1047466500
Zexel num
Bosch num
Firm num
Name
Calibration Data:
Adjustment conditions
Test oil
1404 Test oil ISO4113orSAEJ967d
1404 Test oil ISO4113orSAEJ967d
Test oil temperature
degC
45
45
50
Nozzle
105780-0060
Bosch type code
NP-DN0SD1510
Nozzle holder
105780-2150
Opening pressure
MPa
13
12.7
13.3
Opening pressure
kgf/cm2
133
130
136
Injection pipe
157805-7320
Injection pipe
Inside diameter - outside diameter - length (mm) mm 2-6-450
Inside diameter - outside diameter - length (mm) mm 2-6-450
Joint assembly
157641-4720
Tube assembly
157641-4020
Transfer pump pressure
kPa
20
20
20
Transfer pump pressure
kgf/cm2
0.2
0.2
0.2
Direction of rotation (viewed from drive side)
Right R
Right R
Injection timing adjustment
Pump speed
r/min
1150
1150
1150
Average injection quantity
mm3/st.
61.9
61.4
62.4
Difference in delivery
mm3/st.
5
Basic
*
Oil temperature
degC
50
48
52
Injection timing adjustment_02
Pump speed
r/min
500
500
500
Average injection quantity
mm3/st.
30.2
26.7
35.7
Oil temperature
degC
48
46
50
Injection timing adjustment_03
Pump speed
r/min
750
750
750
Average injection quantity
mm3/st.
42.4
38.9
45.9
Oil temperature
degC
50
48
52
Injection timing adjustment_04
Pump speed
r/min
1150
1150
1150
Average injection quantity
mm3/st.
61.9
60.9
62.9
Difference in delivery
mm3/st.
5
Basic
*
Oil temperature
degC
50
48
52
Injection timing adjustment_05
Pump speed
r/min
1900
1900
1900
Average injection quantity
mm3/st.
71.9
67.9
75.9
Oil temperature
degC
50
48
52
Injection quantity adjustment
Pump speed
r/min
2350
2350
2350
Average injection quantity
mm3/st.
26.6
23.6
29.6
Difference in delivery
mm3/st.
4
Basic
*
Oil temperature
degC
52
50
54
Injection quantity adjustment_02
Pump speed
r/min
2350
2350
2350
Average injection quantity
mm3/st.
26.6
23.6
29.6
Difference in delivery
mm3/st.
4
Basic
*
Oil temperature
degC
52
50
54
Injection quantity adjustment_03
Pump speed
r/min
2700
2700
2700
Average injection quantity
mm3/st.
5
Oil temperature
degC
55
52
58
Governor adjustment
Pump speed
r/min
385
385
385
Average injection quantity
mm3/st.
6.7
4.7
8.7
Difference in delivery
mm3/st.
2
Basic
*
Oil temperature
degC
48
46
50
Governor adjustment_02
Pump speed
r/min
385
385
385
Average injection quantity
mm3/st.
6.7
4.7
8.7
Difference in delivery
mm3/st.
2
Basic
*
Oil temperature
degC
48
46
50
Timer adjustment
Pump speed
r/min
100
100
100
Average injection quantity
mm3/st.
60
60
100
Oil temperature
degC
48
46
50
Remarks
Full
Full
Timer adjustment_02
Pump speed
r/min
100
100
100
Average injection quantity
mm3/st.
60
60
100
Oil temperature
degC
48
46
50
Remarks
Full
Full
Speed control lever angle
Pump speed
r/min
385
385
385
Average injection quantity
mm3/st.
0
0
0
Oil temperature
degC
48
46
50
Remarks
Magnet OFF at idling position
Magnet OFF at idling position
Speed control lever angle_02
Pump speed
r/min
385
385
385
Average injection quantity
mm3/st.
0
0
0
Oil temperature
degC
48
46
50
Remarks
Magnet OFF at idling position
Magnet OFF at idling position
0000000901
Pump speed
r/min
1500
1500
1500
Overflow quantity
cm3/min
380
250
510
Oil temperature
degC
50
48
52
_02
Pump speed
r/min
1500
1500
1500
Overflow quantity
cm3/min
380
250
510
Oil temperature
degC
50
48
52
Stop lever angle
Pump speed
r/min
1500
1500
1500
Pressure
kPa
412
392
432
Pressure
kgf/cm2
4.2
4
4.4
Basic
*
Oil temperature
degC
50
48
52
Stop lever angle_02
Pump speed
r/min
1500
1500
1500
Pressure
kPa
412
392
432
Pressure
kgf/cm2
4.2
4
4.4
Basic
*
Oil temperature
degC
50
48
52
0000001101
Pump speed
r/min
1500
1500
1500
Timer stroke
mm
2.4
2.2
2.6
Basic
*
Oil temperature
degC
50
48
52
_02
Pump speed
r/min
1000
1000
1000
Timer stroke
mm
0.5
Oil temperature
degC
50
48
52
_03
Pump speed
r/min
1500
1500
1500
Timer stroke
mm
2.4
2.2
2.6
Basic
*
Oil temperature
degC
50
48
52
_04
Pump speed
r/min
1700
1700
1700
Timer stroke
mm
3.4
3
3.8
Oil temperature
degC
50
48
52
_05
Pump speed
r/min
2050
2050
2050
Timer stroke
mm
5.3
5
5.7
Oil temperature
degC
52
50
54
0000001201
Max. applied voltage
V
8
8
8
Test voltage
V
13
12
14
Timing setting
K dimension
mm
3.1
3
3.2
KF dimension
mm
5.5
5.4
5.6
MS dimension
mm
0.8
0.7
0.9
Pre-stroke
mm
0.45
0.43
0.47
Control lever angle alpha
deg.
18
14
22
Control lever angle beta
deg.
35
30
40
Test data Ex:
0000001801 POTENTIOMETER ADJUSTMENT

Adjusting method [applied voltage Vi, dummy bolt (C)]
1. Hold the dummy bolt (C) against the control lever at position N = N1, Q = Q1.
Fix using the lock nut.
2. When adjusting the potentiometer, position the control lever against the dummy bolt (C) and adjust the potentiometer so that the output voltage is V1 (V).
3. Remove the dummy bolt (C) after the completion of adjustment.
Confirm that the potentiometer output voltage is within the above mentioned standards between the control lever's adjusting point and the idling position.
N:Pump speed
V:Output voltage
Q:Injection quantity
P:Boost pressure
A:Adjusting point
B:Checking point
Q2:Idle
Q3:Full speed
(C): Dummy bolt
(D): Bracket for mounting the dummy bolt
(E): Part numbers of the dummy bolt and the nut
146526-3300 (bolt) 42L
013020-6040 (nut)
----------
N1=750r/min V1=4.1+-0.03V Q1=7.4+-1cm3/1,000st
----------
N1=750r/min N2=385r/min V1=4.1+-0.03V V2=(2.12+-0.45)V V3=(7.78+-0.45)V Q1=9.7+-1.0cm3/1,000st Q2=6.7+-2.0cm3/1,000st(Idle)
----------
N1=750r/min V1=4.1+-0.03V Q1=7.4+-1cm3/1,000st
----------
N1=750r/min N2=385r/min V1=4.1+-0.03V V2=(2.12+-0.45)V V3=(7.78+-0.45)V Q1=9.7+-1.0cm3/1,000st Q2=6.7+-2.0cm3/1,000st(Idle)
0000001901 W-CSD ADJUSTMENT

Adjustment of the W-CSD
1. Determine the timer advance angle using the graph.
2. Adjust with the screw (A) so that the timer advance angle determined in item 1 is obtained.
Y:Time lift TA (mm)
X:Temperature t (deg C)
(B): Timer stroke TA (mm)
----------
----------
----------
----------
0000002001 V-FICD ADJUSTMENT

Adjustment of the V-FICD
1. Mount the V-FICD after the completion of potentiometer adjustment.
2. Confirm that the clearance between the control lever (B) and the actuator rod (A) is at least L1.
3. Insert the L2 shim between the control lever (D) and the idle set screw (C).
4. Adjust the stroke adjusting screw (E) so that the actuator moves through its full stroke, then fix using nut (F).
Note
When adjustment is not possible using the stroke adjusting screw (E), move the actuator rod position using (G), (H) and (I).
Adjust again the stroke with (E) and (F).
5. Apply negative pressure P1 {P2} to the actuator and confirm that it moves through its full stroke.
6. After releasing negative pressure, re-confirm that the clearance between (A) and (B) is at least L1.
----------
L1=1mm L2=1.30+-0.1mm P1=-53.3kPa P2=-400mmHg
----------
L1=1mm L2=1.30+-0.1mm
----------
L1=1mm L2=1.30+-0.1mm P1=-53.3kPa P2=-400mmHg
----------
L1=1mm L2=1.30+-0.1mm
Information:
Maintenance Recommendations
Caterpillar Inc. truck engines are certified by the United States Environmental Protection Agency (EPA) to comply with smoke and gaseous emission standards prescribed by Federal laws at the time of manufacture.Efficiency of emission control and engine performance depends on adherence to proper operation and maintenance recommendations AND use of recommended fuels and lubricating oils. It is recommended that major adjustments and repair be made by your authorized Caterpillar dealer.Various chemical fuel additives claiming to reduce visible smoke are available commercially. Although additives have been used by individuals to solve some isolated smoke problems in the field, they are not recommended for general use. Federal smoke regulations require that engines be certified without smoke depressants.The corrective steps taken immediately on discovery of worn parts, which may affect emission levels, will help assure proper operation of emission control systems. The use of genuine Caterpillar parts is recommended. Suppliers of non-Caterpillar parts must assure the owner that the use of such parts will not adversely affect emission levels.Regular maintenance intervals, along with special emphasis on the following items, are necessary to keep exhaust emissions within acceptable limits for the useful life of the engine. Refer to the Maintenance Management Schedule and Maintenance Section of this manual for details. If the engine is operating under severe conditions, adjust the maintenance schedule accordingly. See your authorized Caterpillar dealer to help analyze your specific application, operating environment and maintenance schedule adjustments.The following is an explanation of maintenance for emission-related components. See the Maintenance Management Schedule for the specific interval for the following items. FUEL INJECTION NOZZLES - Damaged fuel nozzles will normally cause the engine to misfire, run rough and smoke. Test and replace if necessary as recommended in the Maintenance Management Schedule. Fuel nozzles can be tested by an authorized Caterpillar truck engine dealer. TURBOCHARGER - Check for any unusual sound or vibration in the turbocharger. Inspect inlet and exhaust piping and connections. Check bearing condition and perform maintenance as described in the Maintenance Management Schedule.Owner is encouraged to keep adequate maintenance records, but the absence of such, in and of itself, will not invalidate the warranty.The vehicle owner may perform routine maintenance, repairs and other non warranty work or have it done at any repair facility. Such non warranty work need not be performed at a designated warranty station in order for the warranty to remain in force.Customer Assistance
Caterpillar Inc. aims to ensure that the Emission Control Systems warranty is properly administered. In the event that you do not receive the warranty service to which you believe you are entitled under the Emission Control Systems Warranty, call or write:Caterpillar Inc.
Manager, Truck Engine Business
Peoria, Illinois 61629
Ph. (309) 578-6288
Authorized dealers are recommended for major maintenance and repair work as they are staffed with trained personnel, proper tools and are aware of the latest maintenance methods and procedures. Owners and others who desire to perform their own work should purchase a Service Manual and obtain current service information from their Caterpillar dealer.For information regarding
Caterpillar Inc. truck engines are certified by the United States Environmental Protection Agency (EPA) to comply with smoke and gaseous emission standards prescribed by Federal laws at the time of manufacture.Efficiency of emission control and engine performance depends on adherence to proper operation and maintenance recommendations AND use of recommended fuels and lubricating oils. It is recommended that major adjustments and repair be made by your authorized Caterpillar dealer.Various chemical fuel additives claiming to reduce visible smoke are available commercially. Although additives have been used by individuals to solve some isolated smoke problems in the field, they are not recommended for general use. Federal smoke regulations require that engines be certified without smoke depressants.The corrective steps taken immediately on discovery of worn parts, which may affect emission levels, will help assure proper operation of emission control systems. The use of genuine Caterpillar parts is recommended. Suppliers of non-Caterpillar parts must assure the owner that the use of such parts will not adversely affect emission levels.Regular maintenance intervals, along with special emphasis on the following items, are necessary to keep exhaust emissions within acceptable limits for the useful life of the engine. Refer to the Maintenance Management Schedule and Maintenance Section of this manual for details. If the engine is operating under severe conditions, adjust the maintenance schedule accordingly. See your authorized Caterpillar dealer to help analyze your specific application, operating environment and maintenance schedule adjustments.The following is an explanation of maintenance for emission-related components. See the Maintenance Management Schedule for the specific interval for the following items. FUEL INJECTION NOZZLES - Damaged fuel nozzles will normally cause the engine to misfire, run rough and smoke. Test and replace if necessary as recommended in the Maintenance Management Schedule. Fuel nozzles can be tested by an authorized Caterpillar truck engine dealer. TURBOCHARGER - Check for any unusual sound or vibration in the turbocharger. Inspect inlet and exhaust piping and connections. Check bearing condition and perform maintenance as described in the Maintenance Management Schedule.Owner is encouraged to keep adequate maintenance records, but the absence of such, in and of itself, will not invalidate the warranty.The vehicle owner may perform routine maintenance, repairs and other non warranty work or have it done at any repair facility. Such non warranty work need not be performed at a designated warranty station in order for the warranty to remain in force.Customer Assistance
Caterpillar Inc. aims to ensure that the Emission Control Systems warranty is properly administered. In the event that you do not receive the warranty service to which you believe you are entitled under the Emission Control Systems Warranty, call or write:Caterpillar Inc.
Manager, Truck Engine Business
Peoria, Illinois 61629
Ph. (309) 578-6288
Authorized dealers are recommended for major maintenance and repair work as they are staffed with trained personnel, proper tools and are aware of the latest maintenance methods and procedures. Owners and others who desire to perform their own work should purchase a Service Manual and obtain current service information from their Caterpillar dealer.For information regarding