Information injection-pump assembly
ZEXEL
104746-6280
1047466280
ISUZU
8971361051
8971361051
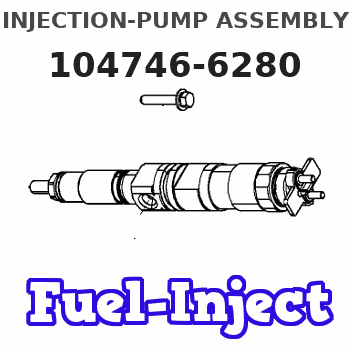
Rating:
Cross reference number
ZEXEL
104746-6280
1047466280
ISUZU
8971361051
8971361051
Zexel num
Bosch num
Firm num
Name
Calibration Data:
Adjustment conditions
Test oil
1404 Test oil ISO4113orSAEJ967d
1404 Test oil ISO4113orSAEJ967d
Test oil temperature
degC
45
45
50
Nozzle
105780-0060
Bosch type code
NP-DN0SD1510
Nozzle holder
105780-2150
Opening pressure
MPa
13
13
13.3
Opening pressure
kgf/cm2
133
133
136
Injection pipe
157805-7320
Injection pipe
Inside diameter - outside diameter - length (mm) mm 2-6-450
Inside diameter - outside diameter - length (mm) mm 2-6-450
Joint assembly
157641-4720
Tube assembly
157641-4020
Transfer pump pressure
kPa
20
20
20
Transfer pump pressure
kgf/cm2
0.2
0.2
0.2
Direction of rotation (viewed from drive side)
Left L
Left L
Injection timing adjustment
Pump speed
r/min
750
750
750
Boost pressure
kPa
40
38.7
41.3
Boost pressure
mmHg
300
290
310
Average injection quantity
mm3/st.
43.3
42.8
43.8
Difference in delivery
mm3/st.
3.5
Basic
*
Oil temperature
degC
50
48
52
Remarks
CBS
CBS
Injection timing adjustment_02
Pump speed
r/min
1250
1250
1250
Boost pressure
kPa
73.3
72
74.6
Boost pressure
mmHg
550
540
560
Average injection quantity
mm3/st.
66.7
66.2
67.2
Difference in delivery
mm3/st.
5.5
Basic
*
Oil temperature
degC
50
48
52
Remarks
Full
Full
Injection timing adjustment_03
Pump speed
r/min
500
500
500
Boost pressure
kPa
0
0
0
Boost pressure
mmHg
0
0
0
Average injection quantity
mm3/st.
28.8
24.8
32.8
Oil temperature
degC
48
46
50
Injection timing adjustment_04
Pump speed
r/min
750
750
750
Boost pressure
kPa
40
38.7
41.3
Boost pressure
mmHg
300
290
310
Average injection quantity
mm3/st.
43.3
42.3
44.3
Difference in delivery
mm3/st.
3.5
Basic
*
Oil temperature
degC
50
48
52
Remarks
CBS
CBS
Injection timing adjustment_05
Pump speed
r/min
1150
1150
1150
Boost pressure
kPa
73.3
72
74.6
Boost pressure
mmHg
550
540
560
Average injection quantity
mm3/st.
64.2
60.7
67.7
Oil temperature
degC
50
48
52
Injection timing adjustment_06
Pump speed
r/min
1250
1250
1250
Boost pressure
kPa
73.3
72
74.6
Boost pressure
mmHg
550
540
560
Average injection quantity
mm3/st.
66.7
65.7
67.7
Difference in delivery
mm3/st.
5.5
Basic
*
Oil temperature
degC
50
48
52
Remarks
Full
Full
Injection timing adjustment_07
Pump speed
r/min
1250
1250
1250
Boost pressure
kPa
0
0
0
Boost pressure
mmHg
0
0
0
Average injection quantity
mm3/st.
49.9
46.4
53.4
Oil temperature
degC
50
48
52
Injection timing adjustment_08
Pump speed
r/min
1900
1900
1900
Boost pressure
kPa
73.3
72
74.6
Boost pressure
mmHg
550
540
560
Average injection quantity
mm3/st.
73.1
69.1
77.1
Oil temperature
degC
50
48
52
Injection quantity adjustment
Pump speed
r/min
2300
2300
2300
Boost pressure
kPa
73.3
72
74.6
Boost pressure
mmHg
550
540
560
Average injection quantity
mm3/st.
28.7
25.7
31.7
Difference in delivery
mm3/st.
4.5
Basic
*
Oil temperature
degC
52
50
54
Injection quantity adjustment_02
Pump speed
r/min
2700
2700
2700
Boost pressure
kPa
73.3
72
74.6
Boost pressure
mmHg
550
540
560
Average injection quantity
mm3/st.
5
Oil temperature
degC
55
52
58
Injection quantity adjustment_03
Pump speed
r/min
2300
2300
2300
Boost pressure
kPa
73.3
72
74.6
Boost pressure
mmHg
550
540
560
Average injection quantity
mm3/st.
28.7
25.7
31.7
Difference in delivery
mm3/st.
4.5
Basic
*
Oil temperature
degC
52
50
54
Governor adjustment
Pump speed
r/min
425
425
425
Boost pressure
kPa
0
0
0
Boost pressure
mmHg
0
0
0
Average injection quantity
mm3/st.
8
6
10
Difference in delivery
mm3/st.
2
Basic
*
Oil temperature
degC
48
46
50
Governor adjustment_02
Pump speed
r/min
425
425
425
Boost pressure
kPa
0
0
0
Boost pressure
mmHg
0
0
0
Average injection quantity
mm3/st.
8
6
10
Difference in delivery
mm3/st.
2
Basic
*
Oil temperature
degC
48
46
50
Timer adjustment
Pump speed
r/min
100
100
100
Boost pressure
kPa
0
0
0
Boost pressure
mmHg
0
0
0
Average injection quantity
mm3/st.
60
60
100
Basic
*
Oil temperature
degC
48
46
50
Remarks
IDLE
IDLE
Timer adjustment_02
Pump speed
r/min
100
100
100
Boost pressure
kPa
0
0
0
Boost pressure
mmHg
0
0
0
Average injection quantity
mm3/st.
60
60
100
Oil temperature
degC
48
46
50
Remarks
IDLE
IDLE
Speed control lever angle
Pump speed
r/min
425
425
425
Boost pressure
kPa
0
0
0
Boost pressure
mmHg
0
0
0
Average injection quantity
mm3/st.
0
0
0
Oil temperature
degC
48
46
50
Remarks
Magnet OFF at idling position
Magnet OFF at idling position
0000000901
Pump speed
r/min
1900
1900
1900
Boost pressure
kPa
73.3
72
74.6
Boost pressure
mmHg
550
540
560
Overflow quantity
cm3/min
770
640
900
Oil temperature
degC
50
48
52
Stop lever angle
Pump speed
r/min
1900
1900
1900
Boost pressure
kPa
73.3
72
74.6
Boost pressure
mmHg
550
540
560
Pressure
kPa
618
598
638
Pressure
kgf/cm2
6.3
6.1
6.5
Basic
*
Oil temperature
degC
50
48
52
Stop lever angle_02
Pump speed
r/min
1900
1900
1900
Boost pressure
kPa
73.3
72
74.6
Boost pressure
mmHg
550
540
560
Pressure
kPa
618
598
638
Pressure
kgf/cm2
6.3
6.1
6.5
Basic
*
Oil temperature
degC
50
48
52
0000001101
Pump speed
r/min
1900
1900
1900
Boost pressure
kPa
73.3
72
74.6
Boost pressure
mmHg
550
540
560
Timer stroke
mm
4.5
4.3
4.7
Basic
*
Oil temperature
degC
50
48
52
_02
Pump speed
r/min
1300
1300
1300
Boost pressure
kPa
73.3
72
74.6
Boost pressure
mmHg
550
540
560
Timer stroke
mm
0.5
Oil temperature
degC
50
48
52
_03
Pump speed
r/min
1600
1600
1600
Boost pressure
kPa
73.3
72
74.6
Boost pressure
mmHg
550
540
560
Timer stroke
mm
2.2
1.8
2.6
Oil temperature
degC
50
48
52
_04
Pump speed
r/min
1900
1900
1900
Boost pressure
kPa
73.3
72
74.6
Boost pressure
mmHg
550
540
560
Timer stroke
mm
4.5
4.3
4.7
Basic
*
Oil temperature
degC
50
48
52
_05
Pump speed
r/min
2300
2300
2300
Boost pressure
kPa
73.3
72
74.6
Boost pressure
mmHg
550
540
560
Timer stroke
mm
7
6.7
7.4
Oil temperature
degC
52
50
54
0000001201
Max. applied voltage
V
8
8
8
Test voltage
V
13
12
14
Timing setting
K dimension
mm
3.1
3
3.2
KF dimension
mm
5.5
5.4
5.6
MS dimension
mm
0.7
0.6
0.8
BCS stroke
mm
3.3
3.2
3.4
Pre-stroke
mm
0.45
0.43
0.47
Control lever angle alpha
deg.
18
14
22
Control lever angle beta
deg.
37
32
42
Test data Ex:
0000001801 POTENTIOMETER ADJUSTMENT

A:Adjusting point
B:Confirmation point
C:Lever position
Vi:Applied voltage
V:Output voltage
C1:Idle
C2:Full speed
----------
----------
V1=1.2+-0.03V V2=(7.37+-0.86)V V3=10V V4=10V
----------
----------
V1=1.2+-0.03V V2=(7.37+-0.86)V V3=10V V4=10V
0000001901 A/T PLATE ADJUSTMENT
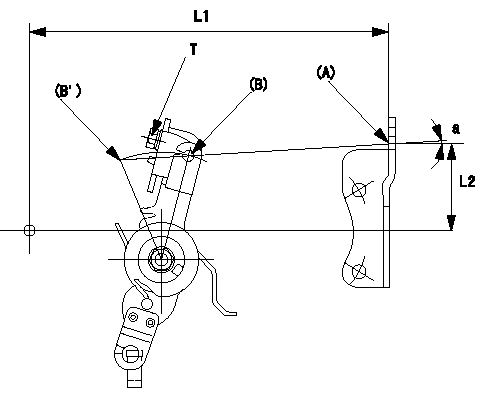
A/T plate adjustment
Rotate the control lever from the idle position (B) to the full-speed position (C).
Adjust the A/T plate (A) so that (A) (C) - (A) (B) = L3, and fix.
(B): B idle position
(C): B' full
----------
L3=32.9+-2mm
----------
L1=174mm L2=42mm T=3.4~4.9N-m{0.35~0.5kgf-m} a=2deg
----------
L3=32.9+-2mm
----------
L1=174mm L2=42mm T=3.4~4.9N-m{0.35~0.5kgf-m} a=2deg
Information:
Water Pump Seal
Over concentration of coolant additive (Conditioner), mineral deposits from hard water or cooling system contamination can accelerate the wear on the water pump coolant seal. The cooling system maintenance interval provides an opportunity to inspect and replace the water pump seal if necessary to reduce coolant leakage.Dispose of used engine coolant in an environmentally correct way or recycle. Various methods have been proposed to reclaim used coolant for reuse in engine cooling systems. The full distillation procedure is the only method acceptable by Caterpillar to reclaim the used coolant and for information regarding disposal and recycling of used coolant.4. Clean and install all drain plugs and/or close the cooling system drain valve(s).Replace Thermostat, Gaskets and Seal
Refer to the Service Manual for detailed instructions regarding Disassembly and Assembly of the Cooling System. Repeat procedure for both thermostat housing assemblies.Replacing the thermostats prior to failure is a recommended preventive maintenance practice because it reduces the chances for cooling system problems and unscheduled downtime.
Failure to replace your thermostats on a regularly scheduled basis could cause severe engine damage.
If replacing thermostats ONLY, drain the coolant from the cooling system to a level below the thermostat housing.5. Disconnect hose assemblies from radiator and each thermostat housing assembly.6. Remove bolts and thermostat housing assembly.7. Remove the gasket, thermostat and seal from each housing.
Former thermostats may be used, if they meet test specifications as described in the Service Manual (and are not damaged or have excessive buildup of deposits).
The thermostats can be reused if they are tested and meet the test specifications in the Service Manual.Flush
8. Refill the cooling system with clean water mixed with the proper concentration (six to ten percent) of Fast Acting-Type Caterpillar Cooling System Cleaner (4C4611). Tighten cooling system vent cap. For proper cooling system maintenance cleaning, refer to label directions for the type of Caterpillar Cooling System Cleaner used in your cooling system.9. Start and run (operate) the engine to circulate fluid in the cooling system.10. Stop the engine and allow to cool. Loosen cooling system vent cap and drain plugs.11. Drain the cleaning solution. Flush the cooling system with clean water and a neutralizing solution until draining water is clear. Clean and install all drain plugs and/or close the drain valve. Sodium Carbonate crystals at a rate of 250 grams per 40 liters of water (1/2 pound per 10 U.S. gallon of water) may be used as a neutralizer. Repeat Steps 8 thru 11 if necessary until the draining water is clear.Install Thermostat
Caterpillar engines incorporate a shunt design cooling system and require operating the engine with a thermostat installed.If the thermostat is installed wrong, it will cause the engine to overheat.
Inspect gaskets before assembly and replace if worn or damaged.12. Install a new seal in each thermostat housing and install new thermostats.13. Install a new gasket and the thermostat housing on the engine cylinder head.14. Install the cooling system connections and tighten the hose or piping clamps.Fill
All water is corrosive at engine operating temperature. The cooling system
Over concentration of coolant additive (Conditioner), mineral deposits from hard water or cooling system contamination can accelerate the wear on the water pump coolant seal. The cooling system maintenance interval provides an opportunity to inspect and replace the water pump seal if necessary to reduce coolant leakage.Dispose of used engine coolant in an environmentally correct way or recycle. Various methods have been proposed to reclaim used coolant for reuse in engine cooling systems. The full distillation procedure is the only method acceptable by Caterpillar to reclaim the used coolant and for information regarding disposal and recycling of used coolant.4. Clean and install all drain plugs and/or close the cooling system drain valve(s).Replace Thermostat, Gaskets and Seal
Refer to the Service Manual for detailed instructions regarding Disassembly and Assembly of the Cooling System. Repeat procedure for both thermostat housing assemblies.Replacing the thermostats prior to failure is a recommended preventive maintenance practice because it reduces the chances for cooling system problems and unscheduled downtime.
Failure to replace your thermostats on a regularly scheduled basis could cause severe engine damage.
If replacing thermostats ONLY, drain the coolant from the cooling system to a level below the thermostat housing.5. Disconnect hose assemblies from radiator and each thermostat housing assembly.6. Remove bolts and thermostat housing assembly.7. Remove the gasket, thermostat and seal from each housing.
Former thermostats may be used, if they meet test specifications as described in the Service Manual (and are not damaged or have excessive buildup of deposits).
The thermostats can be reused if they are tested and meet the test specifications in the Service Manual.Flush
8. Refill the cooling system with clean water mixed with the proper concentration (six to ten percent) of Fast Acting-Type Caterpillar Cooling System Cleaner (4C4611). Tighten cooling system vent cap. For proper cooling system maintenance cleaning, refer to label directions for the type of Caterpillar Cooling System Cleaner used in your cooling system.9. Start and run (operate) the engine to circulate fluid in the cooling system.10. Stop the engine and allow to cool. Loosen cooling system vent cap and drain plugs.11. Drain the cleaning solution. Flush the cooling system with clean water and a neutralizing solution until draining water is clear. Clean and install all drain plugs and/or close the drain valve. Sodium Carbonate crystals at a rate of 250 grams per 40 liters of water (1/2 pound per 10 U.S. gallon of water) may be used as a neutralizer. Repeat Steps 8 thru 11 if necessary until the draining water is clear.Install Thermostat
Caterpillar engines incorporate a shunt design cooling system and require operating the engine with a thermostat installed.If the thermostat is installed wrong, it will cause the engine to overheat.
Inspect gaskets before assembly and replace if worn or damaged.12. Install a new seal in each thermostat housing and install new thermostats.13. Install a new gasket and the thermostat housing on the engine cylinder head.14. Install the cooling system connections and tighten the hose or piping clamps.Fill
All water is corrosive at engine operating temperature. The cooling system