Information injection-pump assembly
ZEXEL
104746-1030
1047461030
ISUZU
8970802010
8970802010
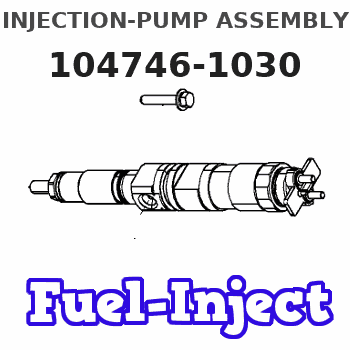
Rating:
Cross reference number
ZEXEL
104746-1030
1047461030
ISUZU
8970802010
8970802010
Zexel num
Bosch num
Firm num
Name
Calibration Data:
Adjustment conditions
Test oil
1404 Test oil ISO4113orSAEJ967d
1404 Test oil ISO4113orSAEJ967d
Test oil temperature
degC
45
45
50
Nozzle
105780-0060
Bosch type code
NP-DN0SD1510
Nozzle holder
105780-2150
Opening pressure
MPa
13
13
13.3
Opening pressure
kgf/cm2
133
133
136
Injection pipe
157805-7320
Injection pipe
Inside diameter - outside diameter - length (mm) mm 2-6-450
Inside diameter - outside diameter - length (mm) mm 2-6-450
Joint assembly
157641-4720
Tube assembly
157641-4020
Transfer pump pressure
kPa
20
20
20
Transfer pump pressure
kgf/cm2
0.2
0.2
0.2
Direction of rotation (viewed from drive side)
Right R
Right R
Injection timing adjustment
Pump speed
r/min
1000
1000
1000
Average injection quantity
mm3/st.
60.2
59.7
60.7
Difference in delivery
mm3/st.
3.5
Basic
*
Oil temperature
degC
50
48
52
Injection timing adjustment_02
Pump speed
r/min
500
500
500
Average injection quantity
mm3/st.
55.8
55.8
55.8
Oil temperature
degC
48
46
50
Injection timing adjustment_03
Pump speed
r/min
1000
1000
1000
Average injection quantity
mm3/st.
60.2
59.2
61.2
Difference in delivery
mm3/st.
3.5
Basic
*
Oil temperature
degC
50
48
52
Injection timing adjustment_04
Pump speed
r/min
1440
1440
1440
Average injection quantity
mm3/st.
57.3
57.3
57.3
Oil temperature
degC
50
48
52
Injection timing adjustment_05
Pump speed
r/min
1800
1800
1800
Average injection quantity
mm3/st.
60.1
60.1
60.1
Oil temperature
degC
50
48
52
Injection quantity adjustment
Pump speed
r/min
2100
2100
2100
Average injection quantity
mm3/st.
26.5
23.5
29.5
Difference in delivery
mm3/st.
5.5
Basic
*
Oil temperature
degC
52
50
54
Injection quantity adjustment_02
Pump speed
r/min
2300
2300
2300
Average injection quantity
mm3/st.
5
Oil temperature
degC
52
50
54
Injection quantity adjustment_03
Pump speed
r/min
2100
2100
2100
Average injection quantity
mm3/st.
26.5
23.5
29.5
Difference in delivery
mm3/st.
5.5
Basic
*
Oil temperature
degC
52
50
54
Governor adjustment
Pump speed
r/min
425
425
425
Average injection quantity
mm3/st.
16.4
14.4
18.4
Difference in delivery
mm3/st.
2
Basic
*
Oil temperature
degC
48
46
50
Governor adjustment_02
Pump speed
r/min
425
425
425
Average injection quantity
mm3/st.
16.4
14.4
18.4
Difference in delivery
mm3/st.
2
Basic
*
Oil temperature
degC
48
46
50
Timer adjustment
Pump speed
r/min
100
100
100
Average injection quantity
mm3/st.
80
80
120
Basic
*
Oil temperature
degC
48
46
50
Remarks
Full
Full
Timer adjustment_02
Pump speed
r/min
100
100
100
Average injection quantity
mm3/st.
80
80
120
Basic
*
Oil temperature
degC
48
46
50
Remarks
IDLE
IDLE
Timer adjustment_03
Pump speed
r/min
100
100
100
Average injection quantity
mm3/st.
80
80
120
Oil temperature
degC
48
46
50
Speed control lever angle
Pump speed
r/min
425
425
425
Average injection quantity
mm3/st.
0
0
0
Oil temperature
degC
48
46
50
Remarks
Magnet OFF
Magnet OFF
0000000901
Pump speed
r/min
1000
1000
1000
Overflow quantity
cm3/min
680
550
810
Oil temperature
degC
50
48
52
Stop lever angle
Pump speed
r/min
1000
1000
1000
Pressure
kPa
422
393
451
Pressure
kgf/cm2
4.3
4
4.6
Basic
*
Oil temperature
degC
50
48
52
Stop lever angle_02
Pump speed
r/min
1000
1000
1000
Pressure
kPa
402
373
431
Pressure
kgf/cm2
4.1
3.8
4.4
Basic
*
Oil temperature
degC
50
48
52
0000001101
Pump speed
r/min
1000
1000
1000
Timer stroke
mm
2.5
2.3
2.7
Basic
*
Oil temperature
degC
50
48
52
_02
Pump speed
r/min
1700
1700
1700
Timer stroke
mm
5.8
5.4
6.2
Basic
*
Oil temperature
degC
50
48
52
_03
Pump speed
r/min
520
520
520
Timer stroke
mm
0.5
0.1
1.3
Oil temperature
degC
50
48
52
_04
Pump speed
r/min
1000
1000
1000
Timer stroke
mm
2.5
2.3
2.7
Basic
*
Oil temperature
degC
50
48
52
_05
Pump speed
r/min
1440
1440
1440
Timer stroke
mm
3.9
3.6
4.2
Oil temperature
degC
50
48
52
_06
Pump speed
r/min
1700
1700
1700
Timer stroke
mm
5.8
5.4
6.2
Basic
*
Oil temperature
degC
50
48
52
_07
Pump speed
r/min
1950
1950
1950
Timer stroke
mm
7.8
7.5
8.2
Oil temperature
degC
50
48
52
0000001201
Max. applied voltage
V
8
8
8
Test voltage
V
13
12
14
0000001401
Pump speed
r/min
1000
1000
1000
Average injection quantity
mm3/st.
31.1
30.6
31.6
Timer stroke TA
mm
2.2
2.2
2.2
Timer stroke variation dT
mm
0.3
0.1
0.5
Basic
*
Oil temperature
degC
50
48
52
_02
Pump speed
r/min
1000
1000
1000
Average injection quantity
mm3/st.
28.7
27.7
29.7
Timer stroke variation dT
mm
0.5
0.1
0.9
Basic
*
Oil temperature
degC
50
48
52
_03
Pump speed
r/min
1000
1000
1000
Average injection quantity
mm3/st.
16
15
17
Timer stroke variation dT
mm
1
0.4
1.6
Oil temperature
degC
50
48
52
Timing setting
K dimension
mm
3.3
3.2
3.4
KF dimension
mm
5.8
5.7
5.9
MS dimension
mm
0.7
0.6
0.8
Control lever angle alpha
deg.
18
14
22
Control lever angle beta
deg.
31
26
36
Test data Ex:
0000001801 W-CSD ADJUSTMENT

Adjustment of the W-CSD
Adjustment of the timer advance angle
1. Determine the timer advance angle using the graph (graph TA).
2. Adjust with the screw (A) so that the timer advance angle determined in item 1 is obtained.
X:Temperature t (deg C)
Y:Timer stroke TA (mm)
(S) Cooling water temperature: increase direction
(R) Cooling water temperature (deg C)
(T) Timer piston stroke (mm)
(B) Standard point
N:Pump speed
----------
TA=-0.0345t+2.59
----------
N1=500(r/min) a=20(degC) b=-20(degC) c=1.9+-0.4(mm) d=3.3+-0.6(mm)
----------
TA=-0.0345t+2.59
----------
N1=500(r/min) a=20(degC) b=-20(degC) c=1.9+-0.4(mm) d=3.3+-0.6(mm)
0000001901 V-FICD ADJUSTMENT
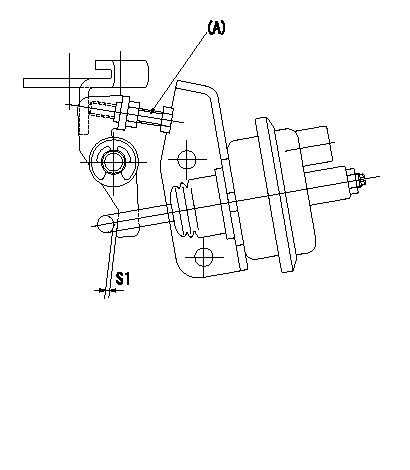
Adjustment of the V-FICD
1. Install the V-FICD and adjust using screw A so that the clearance between the intermediate link and the actuator is S1.
2. Apply negative pressure P1 to the actuator and confirm the full stroke.
----------
S1=1+1mm P1=-53.3kPa(-400mmHg)
----------
S1=1+1mm
----------
S1=1+1mm P1=-53.3kPa(-400mmHg)
----------
S1=1+1mm
0000002001 A/T PLATE ADJUSTMENT

A/T plate adjustment
Rotate the control lever from the idle position (B) to the full-speed position (C).
Adjust the A/T plate (A) so that (A) (C) - (A) (B) = L1, and fix.
When fixing, fix the A/T plate within the range L3 from the center of the control lever's wire hole (hole L2).
(B) Idle position
(C) Full position
----------
L1=32.9+-1mm L2=Dia.8.5mm L3=Dia.9.2mm
----------
L3=Dia.9.2mm L4=169.8mm L5=12.4mm a=18+-4deg
----------
L1=32.9+-1mm L2=Dia.8.5mm L3=Dia.9.2mm
----------
L3=Dia.9.2mm L4=169.8mm L5=12.4mm a=18+-4deg
0000002101 POTENTIOMETER ADJUSTMENT

A:Lever position
V:Output voltage
C:Lever angle
Vi:Applied voltage
D:Full speed
E:Idle
----------
----------
V1=8.2+-0.03(V) V2=3.94--(V) V3=10(V) V4=10(V) C1=31+-5(deg) C2=0(deg)
----------
----------
V1=8.2+-0.03(V) V2=3.94--(V) V3=10(V) V4=10(V) C1=31+-5(deg) C2=0(deg)
Information:
start by: a) remove flywheel When a replacement of the rear seal is made, a replacement of the wear sleeve is to be made also. 1. Remove the crankshaft rear seal from the flywheel housing with tooling (A).2. Install tool (C) in the rear seal bore. 3. Install tool (B) between tool (C) and the wear sleeve. Turn tool (B) until the edge of the tool makes a flat place (crease) in the wear sleeve. Do this in two or more places until the wear sleeve is loose.4. Remove tool (C) and the wear sleeve by hand.Install Crankshaft Rear Seal And Wear Sleeve
The crankshaft seal and wear sleeve come as a set and must not be separated from each other at any time. Carefully read Special Instruction, Form No. SMHS8508, that is included with each seal and wear sleeve before any handling of the seal group is made.
1. Install the crankshaft rear seal and wear sleeve with tooling (A) as follows: a) Clean and make a preparation of the crankshaft outside diameter with 6V1541 Quick Cure Primer. Make an application of 9S3265 Retaining Compound to crankshaft outside diameter.b) Install locator (3) and the bolts on the rear of the crankshaft (4).c) Put the wear sleeve (2) and seal (7) as a unit on locator (3) with the outside diameter bevel of the wear sleeve toward the outside.d) Put installer (5) in position on the locator (3).e) Put clean engine oil on the face of nut (6) and install it on the locator. Tighten the nut until installer (5) is at bottom.f) Remove tooling (A) and check the wear sleeve and seal for the correct position after installation.end by: a) install flywheel
The crankshaft seal and wear sleeve come as a set and must not be separated from each other at any time. Carefully read Special Instruction, Form No. SMHS8508, that is included with each seal and wear sleeve before any handling of the seal group is made.
1. Install the crankshaft rear seal and wear sleeve with tooling (A) as follows: a) Clean and make a preparation of the crankshaft outside diameter with 6V1541 Quick Cure Primer. Make an application of 9S3265 Retaining Compound to crankshaft outside diameter.b) Install locator (3) and the bolts on the rear of the crankshaft (4).c) Put the wear sleeve (2) and seal (7) as a unit on locator (3) with the outside diameter bevel of the wear sleeve toward the outside.d) Put installer (5) in position on the locator (3).e) Put clean engine oil on the face of nut (6) and install it on the locator. Tighten the nut until installer (5) is at bottom.f) Remove tooling (A) and check the wear sleeve and seal for the correct position after installation.end by: a) install flywheel