Information injection-pump assembly
BOSCH
9 460 614 563
9460614563
ZEXEL
104745-9351
1047459351
NISSAN
1670065N04
1670065n04
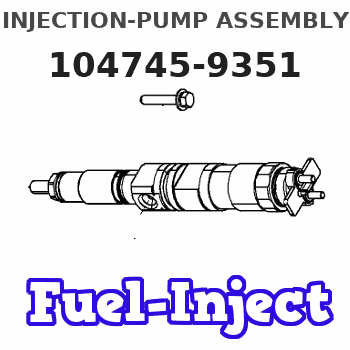
Rating:
Cross reference number
BOSCH
9 460 614 563
9460614563
ZEXEL
104745-9351
1047459351
NISSAN
1670065N04
1670065n04
Zexel num
Bosch num
Firm num
Name
Calibration Data:
Adjustment conditions
Test oil
1404 Test oil ISO4113orSAEJ967d
1404 Test oil ISO4113orSAEJ967d
Test oil temperature
degC
45
45
50
Nozzle
105780-0060
Bosch type code
NP-DN0SD1510
Nozzle holder
105780-2150
Opening pressure
MPa
13
13
13.3
Opening pressure
kgf/cm2
133
133
136
Injection pipe
157805-7320
Injection pipe
Inside diameter - outside diameter - length (mm) mm 2-6-450
Inside diameter - outside diameter - length (mm) mm 2-6-450
Joint assembly
157641-4720
Tube assembly
157641-4020
Transfer pump pressure
kPa
20
20
20
Transfer pump pressure
kgf/cm2
0.2
0.2
0.2
Direction of rotation (viewed from drive side)
Right R
Right R
Injection timing adjustment
Pump speed
r/min
1100
1100
1100
Average injection quantity
mm3/st.
49.9
49.4
50.4
Difference in delivery
mm3/st.
4
Basic
*
Oil temperature
degC
50
48
52
Injection timing adjustment_02
Pump speed
r/min
500
500
500
Average injection quantity
mm3/st.
41.3
38.8
43.8
Oil temperature
degC
48
46
50
Injection timing adjustment_03
Pump speed
r/min
1100
1100
1100
Average injection quantity
mm3/st.
49.9
48.9
50.9
Difference in delivery
mm3/st.
4.5
Basic
*
Oil temperature
degC
50
48
52
Injection timing adjustment_04
Pump speed
r/min
2150
2150
2150
Average injection quantity
mm3/st.
46.3
43.8
48.8
Oil temperature
degC
52
50
54
Injection quantity adjustment
Pump speed
r/min
2550
2550
2550
Average injection quantity
mm3/st.
10.9
8.9
12.9
Difference in delivery
mm3/st.
3
Basic
*
Oil temperature
degC
55
52
58
Injection quantity adjustment_02
Pump speed
r/min
2700
2700
2700
Average injection quantity
mm3/st.
5
Oil temperature
degC
55
52
58
Injection quantity adjustment_03
Pump speed
r/min
2350
2350
2350
Average injection quantity
mm3/st.
39.7
39.7
39.7
Oil temperature
degC
52
50
54
Injection quantity adjustment_04
Pump speed
r/min
2550
2550
2550
Average injection quantity
mm3/st.
10.9
8.4
13.4
Basic
*
Oil temperature
degC
55
52
58
Governor adjustment
Pump speed
r/min
350
350
350
Average injection quantity
mm3/st.
7.7
5.7
9.7
Difference in delivery
mm3/st.
2
Basic
*
Oil temperature
degC
48
46
50
Governor adjustment_02
Pump speed
r/min
350
350
350
Average injection quantity
mm3/st.
7.7
5.2
10.2
Difference in delivery
mm3/st.
2.5
Basic
*
Oil temperature
degC
48
46
50
Timer adjustment
Pump speed
r/min
100
100
100
Average injection quantity
mm3/st.
60
45
80
Basic
*
Oil temperature
degC
48
46
50
Remarks
Full
Full
Timer adjustment_02
Pump speed
r/min
100
100
100
Average injection quantity
mm3/st.
60
45
80
Oil temperature
degC
48
46
50
Remarks
Full
Full
Speed control lever angle
Pump speed
r/min
350
350
350
Average injection quantity
mm3/st.
0
0
0
Oil temperature
degC
48
46
50
Remarks
Magnet OFF at idling position
Magnet OFF at idling position
0000000901
Pump speed
r/min
1100
1100
1100
Overflow quantity with S/T ON
cm3/min
390
260
520
Oil temperature
degC
50
48
52
Remarks
With S/T O-ring; S/T ON.
With S/T O-ring; S/T ON.
_02
Pump speed
r/min
1100
1100
1100
Overflow quantity with S/T ON
cm3/min
600
470
730
Oil temperature
degC
50
48
52
Remarks
Without S/T O-ring; S/T ON.
Without S/T O-ring; S/T ON.
Stop lever angle
Pump speed
r/min
1100
1100
1100
Pressure with S/T ON
kPa
520
481
559
Pressure with S/T ON
kgf/cm2
5.3
4.9
5.7
Pressure with S/T OFF
kPa
431
402
460
Pressure with S/T OFF
kgf/cm2
4.4
4.1
4.7
Basic
*
Oil temperature
degC
50
48
52
Remarks
OFF
OFF
Stop lever angle_02
Pump speed
r/min
1100
1100
1100
Pressure with S/T OFF
kPa
431
392
470
Pressure with S/T OFF
kgf/cm2
4.4
4
4.8
Basic
*
Oil temperature
degC
50
48
52
Stop lever angle_03
Pump speed
r/min
1700
1700
1700
Pressure with S/T OFF
kPa
559
520
598
Pressure with S/T OFF
kgf/cm2
5.7
5.3
6.1
Oil temperature
degC
50
48
52
0000001101
Pump speed
r/min
1100
1100
1100
Timer stroke with S/T ON
mm
3.4
3
3.8
Timer stroke with S/T OFF
mm
1.9
1.7
2.1
Basic
*
Oil temperature
degC
50
48
52
Remarks
OFF
OFF
_02
Pump speed
r/min
850
850
850
Timer stroke with S/T OFF
mm
0.5
0
1
Oil temperature
degC
50
48
52
_03
Pump speed
r/min
1100
1100
1100
Timer stroke with S/T ON
mm
3.4
2.9
3.9
Timer stroke with S/T OFF
mm
1.9
1.6
2.2
Basic
*
Oil temperature
degC
50
48
52
_04
Pump speed
r/min
1700
1700
1700
Timer stroke with S/T OFF
mm
4.4
3.9
4.9
Oil temperature
degC
50
48
52
_05
Pump speed
r/min
2300
2300
2300
Timer stroke with S/T OFF
mm
6.1
5.6
6.5
Oil temperature
degC
52
50
54
0000001201
Max. applied voltage
V
8
8
8
Test voltage
V
13
12
14
0000001401
Pump speed
r/min
1100
1100
1100
Average injection quantity
mm3/st.
31
30.5
31.5
Timer stroke TA
mm
1.2
1
1.4
Timer stroke variation dT
mm
0.7
0.7
0.7
Basic
*
Oil temperature
degC
50
48
52
_02
Pump speed
r/min
1100
1100
1100
Average injection quantity
mm3/st.
31
30
32
Timer stroke TA
mm
1.2
0.9
1.5
Basic
*
Oil temperature
degC
50
48
52
_03
Pump speed
r/min
1100
1100
1100
Average injection quantity
mm3/st.
22
19.5
24.5
Timer stroke TA
mm
0.6
0.1
1.1
Oil temperature
degC
50
48
52
Timing setting
K dimension
mm
3.3
3.2
3.4
KF dimension
mm
5.8
5.7
5.9
MS dimension
mm
0.9
0.8
1
Pre-stroke
mm
0.1
0.08
0.12
Control lever angle alpha
deg.
25
23
27
Control lever angle beta
deg.
36
31
41
Test data Ex:
0000001801 POTENTIOMETER ADJUSTMENT
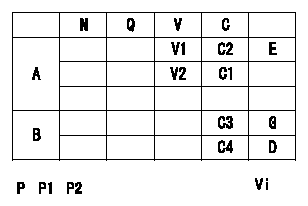
A:Potentiometer standards
B:ON, OFF switch standard
G:ON-->OFF
D:OFF-->ON
E:Adjusting point
F:Checking point
P:Boost pressure
Vi:Applied voltage
C1:Full-speed
C2:Idle
Q:Injection quantity
N:Pump speed
V:Output voltage
C:Control lever angle
----------
----------
V1=1.0+-0.03V V2=7.0+-1.1V C3=(8.5+-2.5)deg C4=(23+-4)deg Vi=10V P1=-kPa P2=-mmHg
----------
----------
V1=1.0+-0.03V V2=7.0+-1.1V C3=(8.5+-2.5)deg C4=(23+-4)deg Vi=10V P1=-kPa P2=-mmHg
0000001901 ACCELERATOR SWITCH ADJ
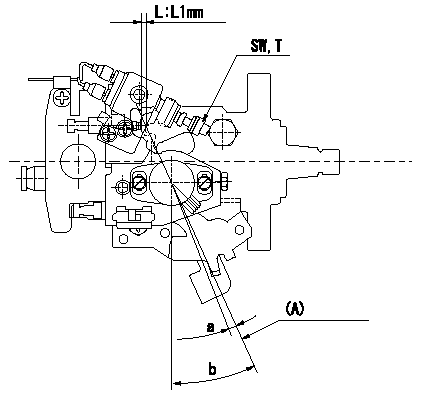
Adjustment of the accelerator switch
ON - OFF changeover point: from idle to c (shim thickness L = L1)
Idle-d: ON
e-full: OFF
L:Thickness of the shim
(A): Position of the idle lever
----------
c=7+-2deg d=7deg e=7deg L1=4.6+-0.13mm
----------
SW=SW10 T=6~9N-m(0.6~0.9Kgf-m) a=7+-2deg b=25+-2deg L1=4.6mm
----------
c=7+-2deg d=7deg e=7deg L1=4.6+-0.13mm
----------
SW=SW10 T=6~9N-m(0.6~0.9Kgf-m) a=7+-2deg b=25+-2deg L1=4.6mm
Information:
Crankshaft Gear Removal
Remove the gear using an 8B7548 Push Puller, 8B7551 Bearing Pulling Attachment, 8B7561 Step Plate, and 8H684 Ratchet Box Wrench.
PULLING CRANKSHAFT GEARThe 1P820 Hydraulic Puller Group can also be used to pull gear from crankshaft. Tools required are 1P820 Hydraulic Puller Group, 8B7551 Bearing Pulling Attachment, 8B7549 Puller legs (two), 8B7561 Step Plate, 3H465 Plate (four), 1B4207 Nut (two), and 9S5800 Pump Group.
USING HYDRAULIC PULLERCrankshaft Gear Installation
1. Install the key in keyway of crankshaft. Remove all burrs from key and keyway inside of crankshaft gear.2. Heat gear to 500° F. (260° C) maximum.3. Install gear on crankshaft with timing mark on gear facing front of crankshaft.Crankshaft Wear Sleeve Removal
REMOVING WEAR SLEEVEUse the 8S7164 Wear Sleeve Puller Group to remove the wear sleeve.Crankshaft Wear Sleeve Installation
WEAR SLEEVE INSTALLATION TOOLS
1. 5P290 Pilot. 2. 5P286 Ring. 3. 9S8858 Nut. 4. 1P5515 Bolts. 5. 9S8864 Pusher Plate.To install the wear sleeve, use the following procedure:1. Install 5P290 Pilot (1) on the end of the crankshaft. Install 1P5515 Bolts (4) and tighten just enough to hold pilot (1) yet allow some side movement. Put the wear sleeve on pilot (1) with the chamfer toward the rear of the engine. Push the wear sleeve on the crankshaft to put pilot (1) in the center, then tighten bolts (4).2. Put 5P286 Ring (2) on 9S8864 Pusher Plate (5) and place this assembly on the stud of pilot (1). Install 9S8858 Nut (3) and tighten nut to push wear sleeve on to the crankshaft.Crankshaft Rear Oil Seal Removal
Use the 1P3075 Puller Group to remove the crankshaft rear seal.
REMOVING REAR OIL SEAL (Typical Example)Crankshaft Rear Oil Seal Installation
REAR OIL SEAL INSTALLATION TOOLS
1. 5P290 Pilot. 2. 1P5515 Bolts. 3. 5P285 Ring. 4. 9S8858 Nut. 5. 5P288 Ring. 6. 9S8864 Pusher Plate.To install the crankshaft rear oil seal, use the following procedure:1. Install 5P290 Pilot (1) on the crankshaft with 1P5515 Bolts (2). Install 5P288 Ring (5) on pilot (1).2. Put 7F2770 Cement on the outer diameter of the seal metal shell. Put engine oil on the lip of the seal. Install the seal on the pilot with the lip of the seal toward the front of the engine.3. Install 9S8864 Pusher Plate (6) and 5P285 Ring (3) over pilot (1). Install 9S8858 Nut (4). Tighten nut (4) until ring (5) makes contact with the flywheel housing. To prevent possible oil leakage, install a new wear sleeve each time the rear oil seal is replaced.Crankshaft Front Oil Seal (1100, 3100, and 3208 Engines 79V1-79V1407)
The crankshaft front oil seal can be removed with the timing gear cover on or off the engine. To install the seal to the proper depth, the timing gear cover must be on the engine.A new timing gear cover permits the crankshaft front oil seal to be installed to two depths.Use the 9S6030 Installation Group which includes the 8S2276 Installer and 9S6012 Spacer to install the seal. To install seal to the original depth, use only the 8S2276 Installer. To obtain an additional wear
Remove the gear using an 8B7548 Push Puller, 8B7551 Bearing Pulling Attachment, 8B7561 Step Plate, and 8H684 Ratchet Box Wrench.
PULLING CRANKSHAFT GEARThe 1P820 Hydraulic Puller Group can also be used to pull gear from crankshaft. Tools required are 1P820 Hydraulic Puller Group, 8B7551 Bearing Pulling Attachment, 8B7549 Puller legs (two), 8B7561 Step Plate, 3H465 Plate (four), 1B4207 Nut (two), and 9S5800 Pump Group.
USING HYDRAULIC PULLERCrankshaft Gear Installation
1. Install the key in keyway of crankshaft. Remove all burrs from key and keyway inside of crankshaft gear.2. Heat gear to 500° F. (260° C) maximum.3. Install gear on crankshaft with timing mark on gear facing front of crankshaft.Crankshaft Wear Sleeve Removal
REMOVING WEAR SLEEVEUse the 8S7164 Wear Sleeve Puller Group to remove the wear sleeve.Crankshaft Wear Sleeve Installation
WEAR SLEEVE INSTALLATION TOOLS
1. 5P290 Pilot. 2. 5P286 Ring. 3. 9S8858 Nut. 4. 1P5515 Bolts. 5. 9S8864 Pusher Plate.To install the wear sleeve, use the following procedure:1. Install 5P290 Pilot (1) on the end of the crankshaft. Install 1P5515 Bolts (4) and tighten just enough to hold pilot (1) yet allow some side movement. Put the wear sleeve on pilot (1) with the chamfer toward the rear of the engine. Push the wear sleeve on the crankshaft to put pilot (1) in the center, then tighten bolts (4).2. Put 5P286 Ring (2) on 9S8864 Pusher Plate (5) and place this assembly on the stud of pilot (1). Install 9S8858 Nut (3) and tighten nut to push wear sleeve on to the crankshaft.Crankshaft Rear Oil Seal Removal
Use the 1P3075 Puller Group to remove the crankshaft rear seal.
REMOVING REAR OIL SEAL (Typical Example)Crankshaft Rear Oil Seal Installation
REAR OIL SEAL INSTALLATION TOOLS
1. 5P290 Pilot. 2. 1P5515 Bolts. 3. 5P285 Ring. 4. 9S8858 Nut. 5. 5P288 Ring. 6. 9S8864 Pusher Plate.To install the crankshaft rear oil seal, use the following procedure:1. Install 5P290 Pilot (1) on the crankshaft with 1P5515 Bolts (2). Install 5P288 Ring (5) on pilot (1).2. Put 7F2770 Cement on the outer diameter of the seal metal shell. Put engine oil on the lip of the seal. Install the seal on the pilot with the lip of the seal toward the front of the engine.3. Install 9S8864 Pusher Plate (6) and 5P285 Ring (3) over pilot (1). Install 9S8858 Nut (4). Tighten nut (4) until ring (5) makes contact with the flywheel housing. To prevent possible oil leakage, install a new wear sleeve each time the rear oil seal is replaced.Crankshaft Front Oil Seal (1100, 3100, and 3208 Engines 79V1-79V1407)
The crankshaft front oil seal can be removed with the timing gear cover on or off the engine. To install the seal to the proper depth, the timing gear cover must be on the engine.A new timing gear cover permits the crankshaft front oil seal to be installed to two depths.Use the 9S6030 Installation Group which includes the 8S2276 Installer and 9S6012 Spacer to install the seal. To install seal to the original depth, use only the 8S2276 Installer. To obtain an additional wear