Information injection-pump assembly
BOSCH
9 460 614 562
9460614562
ZEXEL
104745-9341
1047459341
NISSAN
1670065N03
1670065n03
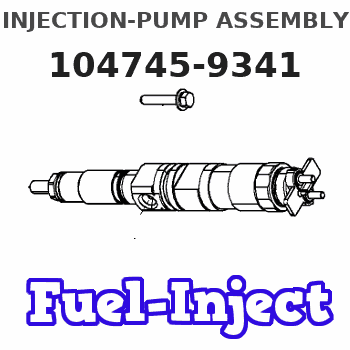
Rating:
Cross reference number
BOSCH
9 460 614 562
9460614562
ZEXEL
104745-9341
1047459341
NISSAN
1670065N03
1670065n03
Zexel num
Bosch num
Firm num
Name
Calibration Data:
Adjustment conditions
Test oil
1404 Test oil ISO4113orSAEJ967d
1404 Test oil ISO4113orSAEJ967d
Test oil temperature
degC
45
45
50
Nozzle
105780-0060
Bosch type code
NP-DN0SD1510
Nozzle holder
105780-2150
Opening pressure
MPa
13
13
13.3
Opening pressure
kgf/cm2
133
133
136
Injection pipe
157805-7320
Injection pipe
Inside diameter - outside diameter - length (mm) mm 2-6-450
Inside diameter - outside diameter - length (mm) mm 2-6-450
Joint assembly
157641-4720
Tube assembly
157641-4020
Transfer pump pressure
kPa
20
20
20
Transfer pump pressure
kgf/cm2
0.2
0.2
0.2
Direction of rotation (viewed from drive side)
Right R
Right R
Injection timing adjustment
Pump speed
r/min
1100
1100
1100
Average injection quantity
mm3/st.
49.9
49.4
50.4
Difference in delivery
mm3/st.
4
Basic
*
Oil temperature
degC
50
48
52
Injection timing adjustment_02
Pump speed
r/min
500
500
500
Average injection quantity
mm3/st.
41.3
38.8
43.8
Oil temperature
degC
48
46
50
Injection timing adjustment_03
Pump speed
r/min
1100
1100
1100
Average injection quantity
mm3/st.
49.9
48.9
50.9
Difference in delivery
mm3/st.
4.5
Basic
*
Oil temperature
degC
50
48
52
Injection timing adjustment_04
Pump speed
r/min
2150
2150
2150
Average injection quantity
mm3/st.
46.3
43.8
48.8
Oil temperature
degC
52
50
54
Injection quantity adjustment
Pump speed
r/min
2550
2550
2550
Average injection quantity
mm3/st.
10.9
8.9
12.9
Difference in delivery
mm3/st.
3
Basic
*
Oil temperature
degC
55
52
58
Injection quantity adjustment_02
Pump speed
r/min
2700
2700
2700
Average injection quantity
mm3/st.
5
Oil temperature
degC
55
52
58
Injection quantity adjustment_03
Pump speed
r/min
2350
2350
2350
Average injection quantity
mm3/st.
39.7
39.7
39.7
Oil temperature
degC
52
50
54
Injection quantity adjustment_04
Pump speed
r/min
2550
2550
2550
Average injection quantity
mm3/st.
10.9
8.4
13.4
Basic
*
Oil temperature
degC
55
52
58
Governor adjustment
Pump speed
r/min
350
350
350
Average injection quantity
mm3/st.
7.7
5.7
9.7
Difference in delivery
mm3/st.
2
Basic
*
Oil temperature
degC
48
46
50
Governor adjustment_02
Pump speed
r/min
350
350
350
Average injection quantity
mm3/st.
7.7
5.2
10.2
Difference in delivery
mm3/st.
2.5
Basic
*
Oil temperature
degC
48
46
50
Timer adjustment
Pump speed
r/min
100
100
100
Average injection quantity
mm3/st.
60
45
80
Basic
*
Oil temperature
degC
48
46
50
Remarks
Full
Full
Timer adjustment_02
Pump speed
r/min
100
100
100
Average injection quantity
mm3/st.
60
45
80
Oil temperature
degC
48
46
50
Remarks
Full
Full
Speed control lever angle
Pump speed
r/min
350
350
350
Average injection quantity
mm3/st.
0
0
0
Oil temperature
degC
48
46
50
Remarks
Magnet OFF at idling position
Magnet OFF at idling position
0000000901
Pump speed
r/min
1100
1100
1100
Overflow quantity
cm3/min
390
260
520
Oil temperature
degC
50
48
52
Stop lever angle
Pump speed
r/min
1100
1100
1100
Pressure
kPa
431
402
460
Pressure
kgf/cm2
4.4
4.1
4.7
Basic
*
Oil temperature
degC
50
48
52
Stop lever angle_02
Pump speed
r/min
1100
1100
1100
Pressure
kPa
431
392
470
Pressure
kgf/cm2
4.4
4
4.8
Basic
*
Oil temperature
degC
50
48
52
Stop lever angle_03
Pump speed
r/min
1700
1700
1700
Pressure
kPa
559
520
598
Pressure
kgf/cm2
5.7
5.3
6.1
Oil temperature
degC
50
48
52
0000001101
Pump speed
r/min
1100
1100
1100
Timer stroke
mm
1.9
1.7
2.1
Basic
*
Oil temperature
degC
50
48
52
_02
Pump speed
r/min
850
850
850
Timer stroke
mm
0.5
0
1
Oil temperature
degC
50
48
52
_03
Pump speed
r/min
1100
1100
1100
Timer stroke
mm
1.9
1.6
2.2
Basic
*
Oil temperature
degC
50
48
52
_04
Pump speed
r/min
1700
1700
1700
Timer stroke
mm
4.4
3.9
4.9
Oil temperature
degC
50
48
52
_05
Pump speed
r/min
2300
2300
2300
Timer stroke
mm
6.1
5.6
6.5
Oil temperature
degC
52
50
54
0000001201
Max. applied voltage
V
8
8
8
Test voltage
V
13
12
14
0000001401
Pump speed
r/min
1100
1100
1100
Average injection quantity
mm3/st.
31
30.5
31.5
Timer stroke TA
mm
1.2
1
1.4
Timer stroke variation dT
mm
0.7
0.7
0.7
Basic
*
Oil temperature
degC
50
48
52
_02
Pump speed
r/min
1100
1100
1100
Average injection quantity
mm3/st.
31
30
32
Timer stroke TA
mm
1.2
0.9
1.5
Basic
*
Oil temperature
degC
50
48
52
_03
Pump speed
r/min
1100
1100
1100
Average injection quantity
mm3/st.
22
19.5
24.5
Timer stroke TA
mm
0.6
0.1
1.1
Oil temperature
degC
50
48
52
Timing setting
K dimension
mm
3.3
3.2
3.4
KF dimension
mm
5.8
5.7
5.9
MS dimension
mm
0.9
0.8
1
Pre-stroke
mm
0.1
0.08
0.12
Control lever angle alpha
deg.
25
23
27
Control lever angle beta
deg.
36
31
41
Test data Ex:
0000001801 POTENTIOMETER ADJUSTMENT
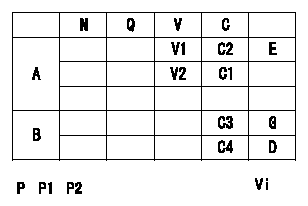
A:Potentiometer standards
B:ON, OFF switch standard
G:ON-->OFF
D:OFF-->ON
E:Adjusting point
F:Checking point
P:Boost pressure
Vi:Applied voltage
C1:Full-speed
C2:Idle
Q:Injection quantity
N:Pump speed
V:Output voltage
C:Control lever angle
----------
----------
V1=1.0+-0.03V V2=7.0+-1.1V C3=(8.5+-2.5)deg C4=(23+-4)deg Vi=10V P1=-kPa P2=-mmHg
----------
----------
V1=1.0+-0.03V V2=7.0+-1.1V C3=(8.5+-2.5)deg C4=(23+-4)deg Vi=10V P1=-kPa P2=-mmHg
Information:
FEED ENGAGED
21. Slot. 22. Pin. 23. Knob. To set the feed mechanism into feed on later units, turn lever (A) up (the direction of arrow).
LATER FEED MECHANISM
A. Lever.Place adapter (24) into boring bar and tighten setscrew (25).
ADAPTER INSTALLED
24. 1P2364 Adapter. 25. Setscrew.Apply layout bluing to the bearing cap and bearing bore. Oil the centering rings. Do not use lubricant on the cutter. Use a one-half inch electric drill with universal joint (26) to feed tool through the bore. Service main bearings with .010 in. (0.25 mm) oversize outside diameter are available to permit the bore to be bored oversize. Bore the bore to 3.7175 .0005 in. (94.425 0.013 mm).
BORING BEARING BORE
26. 1P2363 Universal. If you use the later feed mechanism, the tool can be driven from either the boring bar or the feed mechanism.
DRIVING THROUGH FEED MECHANISM (Typical Example)
26. 1P2363 Universal.The bluing applied to the bearing bore indicates the condition of the bore at the correct bore size. If bluing shows an out of round condition, check the largest diameter (indicated by remaining bluing) in relation to the smallest diameter (indicated by lack of bluing). The difference of the two must not exceed .0010 in. (0.025 mm).If bluing indicates a step in the joint face, measure the diameter at the step in relation to the smallest diameter. A step of .0005 in. (0.013 mm) on one or both sides is permissible. A maximum of .0010 in. (0.025 mm) over the nominal finish bore diameter is permissible if within the described limits.To check the bore diameter, set the 1P3535 Dial Bore Gauge to 3.7175 in. (94.425 mm).
CHECKING BORE (Typical Example)Line Boring Main Bearing Bores
Line bore all main bearing bores if bearing caps or saddles are distorted.Clean bearing caps and saddles. Remove all nicks from pan rail. Plug oil holes in block with grease to prevent chips from entering oil passages.Place 1P2344 Centering Rings (1), with oiler (2) up, at each end of block. If an end bore is distorted, use the next good bore. There must be two good bores for locating centering rings.
CENTERING RINGS IN BLOCK
1. 1P2344 Centering Rings. 2. Oiler.Place original bearing caps (4) over the centering rings (1). Tighten bolts (3) hand tight.
CENTERING RINGS INSTALLED
1. 1P2344 Centering Rings. 3. Bolts (four). 4. Bearing caps.
BORING BAR INSTALLED
1. 1P2344 Centering Rings. 3. Bolts (four). 5. 1P2352 Boring Bar.Oil boring bar (5) and insert it through centering rings (1). Tighten bolts (3) to a minimum of 20 lb. ft. (25 N m) and a maximum of 50 lb. ft. (70 N m) while spinning boring bar (5) to check for binding. Centering rings (1) must be seated in bearing saddles after tightening.Slide boring bar (5) out of one end of block and install bearing assemblies (6) on boring bar (5). Slide boring bar (5) back through centering ring. Adjust bearing by tightening bolt (7) until bar begins to bind, then back off until boring bar (5) spins easily.
INSTALLING BEARING ASSEMBLIES
5. 1P2352 Boring Bar. 6. 1P2373 Bearing assembly