Information injection-pump assembly
ZEXEL
104745-4980
1047454980
NISSAN-DIESEL
167006T000
167006t000
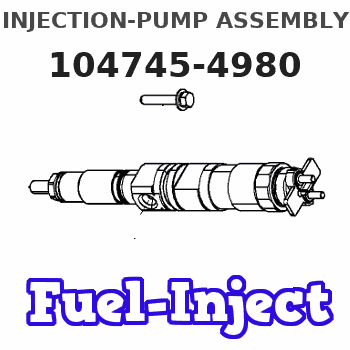
Rating:
Cross reference number
ZEXEL
104745-4980
1047454980
NISSAN-DIESEL
167006T000
167006t000
Zexel num
Bosch num
Firm num
Name
Calibration Data:
Adjustment conditions
Test oil
1404 Test oil ISO4113orSAEJ967d
1404 Test oil ISO4113orSAEJ967d
Test oil temperature
degC
45
45
50
Nozzle
105780-0060
Bosch type code
NP-DN0SD1510
Nozzle holder
105780-2150
Opening pressure
MPa
13
13
13.3
Opening pressure
kgf/cm2
133
133
136
Injection pipe
157805-7320
Injection pipe
Inside diameter - outside diameter - length (mm) mm 2-6-450
Inside diameter - outside diameter - length (mm) mm 2-6-450
Joint assembly
157641-4720
Tube assembly
157641-4020
Transfer pump pressure
kPa
20
20
20
Transfer pump pressure
kgf/cm2
0.2
0.2
0.2
Direction of rotation (viewed from drive side)
Right R
Right R
Injection timing adjustment
Pump speed
r/min
1100
1100
1100
Average injection quantity
mm3/st.
45.3
44.8
45.8
Difference in delivery
mm3/st.
3
Basic
*
Oil temperature
degC
50
48
52
Injection timing adjustment_02
Pump speed
r/min
500
500
500
Average injection quantity
mm3/st.
43
40.5
45.5
Oil temperature
degC
48
46
50
Injection timing adjustment_03
Pump speed
r/min
1100
1100
1100
Average injection quantity
mm3/st.
45.3
44.3
46.3
Difference in delivery
mm3/st.
3.5
Basic
*
Oil temperature
degC
50
48
52
Injection timing adjustment_04
Pump speed
r/min
2150
2150
2150
Average injection quantity
mm3/st.
43
40.5
45.5
Oil temperature
degC
52
50
54
Injection quantity adjustment
Pump speed
r/min
2350
2350
2350
Average injection quantity
mm3/st.
38
36
40
Basic
*
Oil temperature
degC
52
50
54
Injection quantity adjustment_02
Pump speed
r/min
2700
2700
2700
Average injection quantity
mm3/st.
5
Oil temperature
degC
55
52
58
Injection quantity adjustment_03
Pump speed
r/min
2350
2350
2350
Average injection quantity
mm3/st.
38
35.5
40.5
Basic
*
Oil temperature
degC
52
50
54
Injection quantity adjustment_04
Pump speed
r/min
2550
2550
2550
Average injection quantity
mm3/st.
11.5
7
16
Oil temperature
degC
55
52
58
Governor adjustment
Pump speed
r/min
350
350
350
Average injection quantity
mm3/st.
7.4
5.4
9.4
Difference in delivery
mm3/st.
2
Basic
*
Oil temperature
degC
48
46
50
Governor adjustment_02
Pump speed
r/min
350
350
350
Average injection quantity
mm3/st.
7.4
4.9
9.9
Difference in delivery
mm3/st.
2.5
Basic
*
Oil temperature
degC
48
46
50
Timer adjustment
Pump speed
r/min
100
100
100
Average injection quantity
mm3/st.
60
50
80
Basic
*
Oil temperature
degC
48
46
50
Remarks
Full
Full
Timer adjustment_02
Pump speed
r/min
100
100
100
Average injection quantity
mm3/st.
60
45
80
Oil temperature
degC
48
46
50
Remarks
Full
Full
Speed control lever angle
Pump speed
r/min
350
350
350
Average injection quantity
mm3/st.
0
0
0
Oil temperature
degC
48
46
50
Remarks
Magnet OFF at idling position
Magnet OFF at idling position
0000000901
Pump speed
r/min
1100
1100
1100
Overflow quantity
cm3/min
390
260
520
Oil temperature
degC
50
48
52
Stop lever angle
Pump speed
r/min
1100
1100
1100
Pressure
kPa
431
402
460
Pressure
kgf/cm2
4.4
4.1
4.7
Basic
*
Oil temperature
degC
50
48
52
Stop lever angle_02
Pump speed
r/min
1100
1100
1100
Pressure
kPa
431
392
470
Pressure
kgf/cm2
4.4
4
4.8
Basic
*
Oil temperature
degC
50
48
52
Stop lever angle_03
Pump speed
r/min
1700
1700
1700
Pressure
kPa
579
540
618
Pressure
kgf/cm2
5.9
5.5
6.3
Oil temperature
degC
50
48
52
0000001101
Pump speed
r/min
1100
1100
1100
Timer stroke
mm
2.6
2.4
2.8
Basic
*
Oil temperature
degC
50
48
52
_02
Pump speed
r/min
700
700
700
Timer stroke
mm
0.5
0.5
Oil temperature
degC
50
48
52
_03
Pump speed
r/min
1100
1100
1100
Timer stroke
mm
2.6
2.3
2.9
Basic
*
Oil temperature
degC
50
48
52
_04
Pump speed
r/min
1700
1700
1700
Timer stroke
mm
4.9
4.4
5.4
Oil temperature
degC
50
48
52
_05
Pump speed
r/min
2550
2550
2550
Timer stroke
mm
7.4
6.9
7.8
Oil temperature
degC
55
52
58
0000001201
Max. applied voltage
V
8
8
8
Test voltage
V
13
12
14
Timing setting
K dimension
mm
3.3
3.2
3.4
KF dimension
mm
5.8
5.7
5.9
MS dimension
mm
0.9
0.8
1
Pre-stroke
mm
0.1
0.08
0.12
Control lever angle alpha
deg.
25
23
27
Control lever angle beta
deg.
36
31
41
Information:
Parts Location
Illustration 2 g01631813
(A) Flywheel (B) Fender Group (C) Tank Group (1) 319-8929 Diesel Particulate Filter Gp (2) 329-1696 Tube (3) 329-1701 Tube As (4) 295-3044 Exhaust Support Gp (5) 8T-4223 Hard Washer (6) 8T-4183 Bolt (7) 270-0112 Bellows (8) 7E-3870 Muffler Clamp (9) 247-5011 Pipe Clamp (10) 9Y-8315 Pipe Clamp (11) 8S-5120 Extension Pipe (12) 7S-4994 Rain Cap As (13) 241-6170 Plug (14) 8T-6765 Pipe Plug Installation Procedure
Diesel Particulate Filter Installation
Illustration 3 g01630053
(4) 295-3044 Exhaust Support Gp (Lower half) (5) 8T-4223 Hard Washer (6) 8T-4183 Bolt
Install the lower half of each new 295-3044 Exhaust Support Gp (4) on top of the hood, towards the right side of the cab, by using four new 8T-4183 Bolts (6), and four new 8T-4223 Hard Washers (5). Refer to Illustration 3.
Illustration 4 g01630056
(1) 319-8929 Diesel Particulate Filter Gp
Install the new 319-8929 Diesel Particulate Filter Gp (1) onto the lower half of exhaust support group (4). Refer to Illustration 4.
Illustration 5 g01630074
(4a) Upper half (Exhaust support group) (4b) Bolt (4c) Hard washer (4d) Weld nut
Install the upper half (4a) of exhaust support group by using two bolts (4b), two hard washers (4c), and two weld nuts (4d). Repeat for the other exhaust support group. Refer to Illustration 5.
Illustration 6 g01630094
(2) 329-1696 Tube (3) 329-1701 Tube As (7) 270-0112 Bellows (8) 7E-3870 Muffler Clamp
Install the new 329-1696 Tube (2) to the inlet module tube of the diesel particulate filter group by using one new 7E-3870 Muffler Clamp (8). Refer to Illustration 6.
Install the new 270-0112 Bellows (7) to tube (2) by using one new 7E-3870 Muffler Clamp (8). Refer to Illustration 6.
Install the new 329-1701 Tube Assembly (3) to bellows (7) by using one new 7E-3870 Muffler Clamp (8). Refer to Illustration 6.
Illustration 7 g01630133
(9) 247-5011 Pipe Clamp (11) 8S-5120 Extension Pipe
Install 8S-5120 Extension Pipe (11) to the outlet module tube of the diesel particulate filter group by using a new 247-5011 Pipe Clamp (9). Refer to Illustration 7.
Illustration 8 g01630173
(12) 7S-4994 Rain Cap As
Install the new 7S-4994 Rain Cap Assembly (12) on extension pipe (11). Refer to Illustration 8.
Illustration 9 g01630234
(13) 241-6170 Plug (14) 8T-6765 Pipe Plug
Install a new 241-6170 Plug (13) and a new 8T-6765 Pipe Plug (14) on tube assembly (3) at the respective slots provided. Refer to Illustration 9.
Reconnect the drain lines.Exhaust Monitor Installation
Refer to Special Instruction, REHS5606, "Installation and Operation of the Caterpillar Diesel Particulate Filter (DPF) and the Diagnostic Module for Non-Road Machine Applications (Non-California Applications)" for information regarding the installation and the operation of the exhaust monitor.The exhaust monitor is a device designed to monitor the Caterpillar DPF system continuously. The exhaust monitor provides critical information to the vehicle operator and maintenance
Illustration 2 g01631813
(A) Flywheel (B) Fender Group (C) Tank Group (1) 319-8929 Diesel Particulate Filter Gp (2) 329-1696 Tube (3) 329-1701 Tube As (4) 295-3044 Exhaust Support Gp (5) 8T-4223 Hard Washer (6) 8T-4183 Bolt (7) 270-0112 Bellows (8) 7E-3870 Muffler Clamp (9) 247-5011 Pipe Clamp (10) 9Y-8315 Pipe Clamp (11) 8S-5120 Extension Pipe (12) 7S-4994 Rain Cap As (13) 241-6170 Plug (14) 8T-6765 Pipe Plug Installation Procedure
Diesel Particulate Filter Installation
Illustration 3 g01630053
(4) 295-3044 Exhaust Support Gp (Lower half) (5) 8T-4223 Hard Washer (6) 8T-4183 Bolt
Install the lower half of each new 295-3044 Exhaust Support Gp (4) on top of the hood, towards the right side of the cab, by using four new 8T-4183 Bolts (6), and four new 8T-4223 Hard Washers (5). Refer to Illustration 3.
Illustration 4 g01630056
(1) 319-8929 Diesel Particulate Filter Gp
Install the new 319-8929 Diesel Particulate Filter Gp (1) onto the lower half of exhaust support group (4). Refer to Illustration 4.
Illustration 5 g01630074
(4a) Upper half (Exhaust support group) (4b) Bolt (4c) Hard washer (4d) Weld nut
Install the upper half (4a) of exhaust support group by using two bolts (4b), two hard washers (4c), and two weld nuts (4d). Repeat for the other exhaust support group. Refer to Illustration 5.
Illustration 6 g01630094
(2) 329-1696 Tube (3) 329-1701 Tube As (7) 270-0112 Bellows (8) 7E-3870 Muffler Clamp
Install the new 329-1696 Tube (2) to the inlet module tube of the diesel particulate filter group by using one new 7E-3870 Muffler Clamp (8). Refer to Illustration 6.
Install the new 270-0112 Bellows (7) to tube (2) by using one new 7E-3870 Muffler Clamp (8). Refer to Illustration 6.
Install the new 329-1701 Tube Assembly (3) to bellows (7) by using one new 7E-3870 Muffler Clamp (8). Refer to Illustration 6.
Illustration 7 g01630133
(9) 247-5011 Pipe Clamp (11) 8S-5120 Extension Pipe
Install 8S-5120 Extension Pipe (11) to the outlet module tube of the diesel particulate filter group by using a new 247-5011 Pipe Clamp (9). Refer to Illustration 7.
Illustration 8 g01630173
(12) 7S-4994 Rain Cap As
Install the new 7S-4994 Rain Cap Assembly (12) on extension pipe (11). Refer to Illustration 8.
Illustration 9 g01630234
(13) 241-6170 Plug (14) 8T-6765 Pipe Plug
Install a new 241-6170 Plug (13) and a new 8T-6765 Pipe Plug (14) on tube assembly (3) at the respective slots provided. Refer to Illustration 9.
Reconnect the drain lines.Exhaust Monitor Installation
Refer to Special Instruction, REHS5606, "Installation and Operation of the Caterpillar Diesel Particulate Filter (DPF) and the Diagnostic Module for Non-Road Machine Applications (Non-California Applications)" for information regarding the installation and the operation of the exhaust monitor.The exhaust monitor is a device designed to monitor the Caterpillar DPF system continuously. The exhaust monitor provides critical information to the vehicle operator and maintenance