Information injection-pump assembly
BOSCH
9 460 614 977
9460614977
ZEXEL
104742-7232
1047427232
YANMAR
12969251951
12969251951
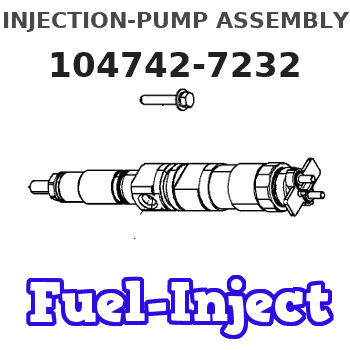
Rating:
Cross reference number
BOSCH
9 460 614 977
9460614977
ZEXEL
104742-7232
1047427232
YANMAR
12969251951
12969251951
Zexel num
Bosch num
Firm num
Name
104742-7232
9 460 614 977
12969251951 YANMAR
INJECTION-PUMP ASSEMBLY
4JH3 K 11CJ INJECTION PUMP ASSY VE4 VE
4JH3 K 11CJ INJECTION PUMP ASSY VE4 VE
Calibration Data:
Adjustment conditions
Test oil
1404 Test oil ISO4113orSAEJ967d
1404 Test oil ISO4113orSAEJ967d
Test oil temperature
degC
45
45
50
Nozzle
105780-0060
Bosch type code
NP-DN0SD1510
Nozzle holder
105780-2150
Opening pressure
MPa
13
13
13.3
Opening pressure
kgf/cm2
133
133
136
Injection pipe
157805-7320
Injection pipe
Inside diameter - outside diameter - length (mm) mm 2-6-450
Inside diameter - outside diameter - length (mm) mm 2-6-450
Joint assembly
157641-4720
Tube assembly
157641-4020
Transfer pump pressure
kPa
20
20
20
Transfer pump pressure
kgf/cm2
0.2
0.2
0.2
Direction of rotation (viewed from drive side)
Right R
Right R
Injection timing adjustment
Pump speed
r/min
1600
1600
1600
Average injection quantity
mm3/st.
74
73.5
74.5
Difference in delivery
mm3/st.
6
Basic
*
Oil temperature
degC
50
48
52
Injection timing adjustment_02
Pump speed
r/min
500
500
500
Average injection quantity
mm3/st.
46.4
40.4
52.4
Oil temperature
degC
48
46
50
Injection timing adjustment_03
Pump speed
r/min
600
600
600
Average injection quantity
mm3/st.
45.2
39.2
51.2
Oil temperature
degC
50
48
52
Injection timing adjustment_04
Pump speed
r/min
900
900
900
Average injection quantity
mm3/st.
60.3
55.8
64.8
Oil temperature
degC
50
48
52
Injection timing adjustment_05
Pump speed
r/min
1350
1350
1350
Average injection quantity
mm3/st.
77.4
73.4
81.4
Oil temperature
degC
50
48
52
Injection timing adjustment_06
Pump speed
r/min
1600
1600
1600
Average injection quantity
mm3/st.
74
73
75
Difference in delivery
mm3/st.
6
Basic
*
Oil temperature
degC
50
48
52
Injection timing adjustment_07
Pump speed
r/min
1800
1800
1800
Average injection quantity
mm3/st.
69.7
65.7
73.7
Oil temperature
degC
50
48
52
Injection quantity adjustment
Pump speed
r/min
2050
2050
2050
Average injection quantity
mm3/st.
6.2
3.2
9.2
Difference in delivery
mm3/st.
3
Basic
*
Oil temperature
degC
52
50
54
Injection quantity adjustment_02
Pump speed
r/min
2200
2200
2200
Average injection quantity
mm3/st.
3
Oil temperature
degC
52
50
54
Injection quantity adjustment_03
Pump speed
r/min
2050
2050
2050
Average injection quantity
mm3/st.
6.2
1.7
10.7
Difference in delivery
mm3/st.
3
Basic
*
Oil temperature
degC
52
50
54
Governor adjustment
Pump speed
r/min
325
325
325
Average injection quantity
mm3/st.
15.9
13.9
17.9
Difference in delivery
mm3/st.
3
Basic
*
Oil temperature
degC
48
46
50
Governor adjustment_02
Pump speed
r/min
325
325
325
Average injection quantity
mm3/st.
15.9
13.4
18.4
Difference in delivery
mm3/st.
3
Basic
*
Oil temperature
degC
48
46
50
Timer adjustment
Pump speed
r/min
100
100
100
Average injection quantity
mm3/st.
85
65
105
Basic
*
Oil temperature
degC
48
46
50
Remarks
Full
Full
Timer adjustment_02
Pump speed
r/min
150
150
150
Average injection quantity
mm3/st.
85
65
105
Basic
*
Oil temperature
degC
48
46
50
Remarks
Full
Full
Timer adjustment_03
Pump speed
r/min
100
100
100
Average injection quantity
mm3/st.
85
65
105
Oil temperature
degC
48
46
50
Remarks
Full
Full
Speed control lever angle
Pump speed
r/min
100
100
100
Average injection quantity
mm3/st.
0
0
0
Oil temperature
degC
48
46
50
Remarks
Magnet ON at idling position and reversed operate
Magnet ON at idling position and reversed operate
Speed control lever angle_02
Pump speed
r/min
325
325
325
Average injection quantity
mm3/st.
0
0
0
Oil temperature
degC
48
46
50
Remarks
Magnet ON at idling position and reversed operate
Magnet ON at idling position and reversed operate
Speed control lever angle_03
Pump speed
r/min
100
100
100
Average injection quantity
mm3/st.
0
0
0
Oil temperature
degC
48
46
50
Remarks
Magnet OFF at idling position and stop lever operate
Magnet OFF at idling position and stop lever operate
Speed control lever angle_04
Pump speed
r/min
325
325
325
Average injection quantity
mm3/st.
0
0
0
Oil temperature
degC
48
46
50
Remarks
Magnet OFF at idling position and stop lever operate
Magnet OFF at idling position and stop lever operate
0000000901
Pump speed
r/min
1050
1050
1050
Overflow quantity
cm3/min
1280
1050
1510
Oil temperature
degC
50
48
52
Stop lever angle
Pump speed
r/min
1050
1050
1050
Pressure
kPa
510
481
539
Pressure
kgf/cm2
5.2
4.9
5.5
Basic
*
Oil temperature
degC
50
48
52
Stop lever angle_02
Pump speed
r/min
950
950
950
Pressure
kPa
490
451
529
Pressure
kgf/cm2
5
4.6
5.4
Oil temperature
degC
50
48
52
Stop lever angle_03
Pump speed
r/min
1050
1050
1050
Pressure
kPa
510
471
549
Pressure
kgf/cm2
5.2
4.8
5.6
Basic
*
Oil temperature
degC
50
48
52
Stop lever angle_04
Pump speed
r/min
1800
1800
1800
Pressure
kPa
677
638
716
Pressure
kgf/cm2
6.9
6.5
7.3
Oil temperature
degC
50
48
52
0000001101
Pump speed
r/min
1050
1050
1050
Timer stroke
mm
0.8
0.6
1
Basic
*
Oil temperature
degC
50
48
52
_02
Pump speed
r/min
1050
1050
1050
Timer stroke
mm
0.8
0.4
1.2
Basic
*
Oil temperature
degC
50
48
52
_03
Pump speed
r/min
1800
1800
1800
Timer stroke
mm
1.7
1.2
2.1
Oil temperature
degC
50
48
52
0000001201
Max. applied voltage
V
16
16
16
Test voltage
Reverse operation (At Normal: OFF, At Stop: ON) V 25 24 26
Reverse operation (At Normal: OFF, At Stop: ON) V 25 24 26
Timing setting
K dimension
mm
3.6
3.5
3.7
KF dimension
mm
6.85
6.75
6.95
MS dimension
mm
0.9
0.8
1
Pre-stroke
mm
0.2
0.18
0.22
Control lever angle alpha
deg.
25
21
29
Control lever angle beta
deg.
45
40
50
Test data Ex:
0000001801 Temp. adjust full-load screw
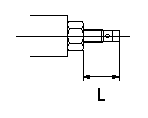
Temporary full load screw adjustment
Set the full load screw protrusion at L mm at assembly.
----------
L=14+-0.5mm
----------
L=14+-0.5mm
----------
L=14+-0.5mm
----------
L=14+-0.5mm
0000001901 STOP LEVER ADJUSTMENT
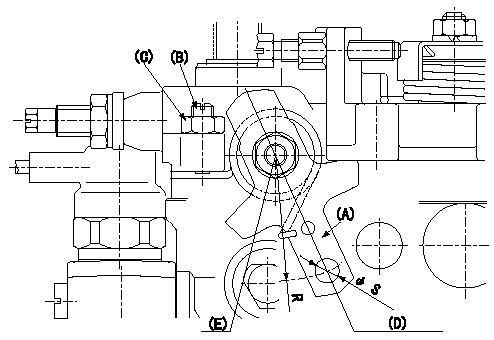
Adjustment of the stop lever
1. Confirm that the starting injection quantity is within standards at the normal position.
If below the specified lower limit, move the stop lever serrations one tooth and reconfirm.
2. Pull the stop lever (A) to the fuel cut direction at the standard idling speed of N and adjust the screw (B) to the position Q.
Fix nut (C) to the torque T at the position where the clearance between the stop lever and the end of the screw is L mm (the screw is returned 2 turns).
The head of the screw must protrude above the face of the nut. If the head of the screw is below the face of the nut, adjust the clearance between the stop lever A and the end of the screw at Q to L mm or more.
3. If adjustment in item 2 is not possible, move the stop lever installation position 1 tooth.
4. The stop lever's operating force is max. M kg (at R = 35). The stop lever must operate smoothly.
(D) Normal position
(E) Stop position
----------
N=325r/min Q=0mm3/st T=6~9N-m(0.6~0.9kgf-m) L=2mm M=4.0kg
----------
S=Dia6.5+0.09mm R=35mm
----------
N=325r/min Q=0mm3/st T=6~9N-m(0.6~0.9kgf-m) L=2mm M=4.0kg
----------
S=Dia6.5+0.09mm R=35mm
Information:
Start By:a. remove oil pumpb. remove timing gear coverc. remove flywheel housingd. remove pistons For more detail about removal of main bearings, see the topic "Remove & Install Crankshaft Main Bearings" in this module. 1. Check each bearing cap (1) for its location on the engine. Each cap has an arrow which is toward the front of the block and a number which gives the location of that cap. Keep each bearing with the correct cap.2. Remove bearing caps No. 2 through No. 6. Remove thrust plates from No. 4 upper bearing.3. Install one of the flywheel bolts in each end of the crankshaft. Fasten a hoist to the crankshaft as shown. Remove No. 1 and No. 7 main bearing caps. Remove the crankshaft. Weight of the crankshaft is 181 kg (400 lb).
Be careful not to damage the crankshaft journals when the crankshaft is removed.
4. Remove crankshaft gear (2) with Tooling (A).5. Remove dowel and pin from crankshaft with Tooling (B).Install Crankshaft
1. Install pin (1) in the crankshaft end until it is extended from the surface a distance of 6.4 0.5 mm (.25 .02 in).2. Install dowel (2) until it is extended from the surface a distance of 4.1 0.5 mm (.16 .02 in). 3. Heat crankshaft gear (3) to a maximum temperature of 232°C (450°F). Install gear (3) on the crankshaft with groove (4) in alignment with dowel (2).4. Make sure the upper main bearings are clean. Put clean oil on the upper main bearings and journals of the crankshaft. 5. Install one of the flywheel bolts in each end of the crankshaft. Fasten a hoist to the crankshaft and put it in position in the block.
Use care to prevent damage to the crankshaft journals. Make sure the "V" mark on the crankshaft gear is in alignment with the "V" mark on the idler gear.
For more detail about installation of main bearings, see Remove And Install Crankshaft Main Bearings.6. Check the bearing clearances with Plastigage.7. Put clean engine oil on the bolts for caps No. 1 and No. 7. Install No. 1 and No. 7 caps with the bolts finger tight. Make sure the arrows on the caps are toward the front of the block. 8. Install thrust plates (5) for the No. 4 upper main bearing. Install the thrust plates with the side that has identification "BLOCK SIDE" toward the cylinder block.9. Put clean oil on the bolts for caps No. 2 through No. 6. Install caps No. 2 through No. 6 with the bolts finger tight. Make sure the arrows are toward the front of the block.
Do not use an impact wrench to tighten the bolts the additional 120 degrees.
10. Tighten the cap bolts as follows:a. Tighten the bolts on the tab end of the caps first to a torque of 260 14 N m (190
Be careful not to damage the crankshaft journals when the crankshaft is removed.
4. Remove crankshaft gear (2) with Tooling (A).5. Remove dowel and pin from crankshaft with Tooling (B).Install Crankshaft
1. Install pin (1) in the crankshaft end until it is extended from the surface a distance of 6.4 0.5 mm (.25 .02 in).2. Install dowel (2) until it is extended from the surface a distance of 4.1 0.5 mm (.16 .02 in). 3. Heat crankshaft gear (3) to a maximum temperature of 232°C (450°F). Install gear (3) on the crankshaft with groove (4) in alignment with dowel (2).4. Make sure the upper main bearings are clean. Put clean oil on the upper main bearings and journals of the crankshaft. 5. Install one of the flywheel bolts in each end of the crankshaft. Fasten a hoist to the crankshaft and put it in position in the block.
Use care to prevent damage to the crankshaft journals. Make sure the "V" mark on the crankshaft gear is in alignment with the "V" mark on the idler gear.
For more detail about installation of main bearings, see Remove And Install Crankshaft Main Bearings.6. Check the bearing clearances with Plastigage.7. Put clean engine oil on the bolts for caps No. 1 and No. 7. Install No. 1 and No. 7 caps with the bolts finger tight. Make sure the arrows on the caps are toward the front of the block. 8. Install thrust plates (5) for the No. 4 upper main bearing. Install the thrust plates with the side that has identification "BLOCK SIDE" toward the cylinder block.9. Put clean oil on the bolts for caps No. 2 through No. 6. Install caps No. 2 through No. 6 with the bolts finger tight. Make sure the arrows are toward the front of the block.
Do not use an impact wrench to tighten the bolts the additional 120 degrees.
10. Tighten the cap bolts as follows:a. Tighten the bolts on the tab end of the caps first to a torque of 260 14 N m (190
Have questions with 104742-7232?
Group cross 104742-7232 ZEXEL
Dpico
Daewoo
Yanmar
Yanmar
Yanmar
104742-7232
9 460 614 977
12969251951
INJECTION-PUMP ASSEMBLY
4JH3
4JH3