Information injection-pump assembly
ZEXEL
104742-3022
1047423022
MITSUBISHI-HEAV
32A6537330
32a6537330

Rating:
Cross reference number
ZEXEL
104742-3022
1047423022
MITSUBISHI-HEAV
32A6537330
32a6537330
Zexel num
Bosch num
Firm num
Name
104742-3022
32A6537330 MITSUBISHI-HEAV
INJECTION-PUMP ASSEMBLY
S4S-DT
S4S-DT
Calibration Data:
Adjustment conditions
Test oil
1404 Test oil ISO4113orSAEJ967d
1404 Test oil ISO4113orSAEJ967d
Test oil temperature
degC
45
45
50
Nozzle
105780-0060
Bosch type code
NP-DN0SD1510
Nozzle holder
105780-2150
Opening pressure
MPa
13
13
13.3
Opening pressure
kgf/cm2
133
133
136
Injection pipe
157805-7320
Injection pipe
Inside diameter - outside diameter - length (mm) mm 2-6-450
Inside diameter - outside diameter - length (mm) mm 2-6-450
Joint assembly
157641-4720
Tube assembly
157641-4020
Transfer pump pressure
kPa
20
20
20
Transfer pump pressure
kgf/cm2
0.2
0.2
0.2
Direction of rotation (viewed from drive side)
Right R
Right R
(Solenoid timer adjustment condition)
With S/T O-ring; S/T OFF. OFF
With S/T O-ring; S/T OFF. OFF
Timer measuring device installation position
Low pressure side LOW PRESSURE SIDE
Low pressure side LOW PRESSURE SIDE
Injection timing adjustment
Pump speed
r/min
900
900
900
Boost pressure
kPa
37.3
36
38.6
Boost pressure
mmHg
280
270
290
Average injection quantity
mm3/st.
111.5
111
112
Basic
*
Oil temperature
degC
50
48
52
Remarks
CBS
CBS
Injection timing adjustment_02
Pump speed
r/min
900
900
900
Boost pressure
kPa
66.7
65.4
68
Boost pressure
mmHg
500
490
510
Average injection quantity
mm3/st.
116.2
115.7
116.7
Difference in delivery
mm3/st.
11
Basic
*
Oil temperature
degC
50
48
52
Remarks
Full
Full
Injection timing adjustment_03
Pump speed
r/min
500
500
500
Boost pressure
kPa
0
0
0
Boost pressure
mmHg
0
0
0
Average injection quantity
mm3/st.
77.8
70.8
84.8
Oil temperature
degC
48
46
50
Injection timing adjustment_04
Pump speed
r/min
900
900
900
Boost pressure
kPa
37.3
36
38.6
Boost pressure
mmHg
280
270
290
Average injection quantity
mm3/st.
111.5
109
114
Basic
*
Oil temperature
degC
50
48
52
Remarks
CBS
CBS
Injection timing adjustment_05
Pump speed
r/min
900
900
900
Boost pressure
kPa
66.7
65.4
68
Boost pressure
mmHg
500
490
510
Average injection quantity
mm3/st.
116.2
113.7
118.7
Difference in delivery
mm3/st.
11.5
Basic
*
Oil temperature
degC
50
48
52
Remarks
Full
Full
Injection timing adjustment_06
Pump speed
r/min
1100
1100
1100
Boost pressure
kPa
66.7
65.4
68
Boost pressure
mmHg
500
490
510
Average injection quantity
mm3/st.
125.3
119.8
130.8
Oil temperature
degC
50
48
52
Injection timing adjustment_07
Pump speed
r/min
1250
1250
1250
Boost pressure
kPa
66.7
65.4
68
Boost pressure
mmHg
500
490
510
Average injection quantity
mm3/st.
123.7
118.2
129.2
Oil temperature
degC
50
48
52
Injection quantity adjustment
Pump speed
r/min
1425
1425
1425
Boost pressure
kPa
66.7
65.4
68
Boost pressure
mmHg
500
490
510
Average injection quantity
mm3/st.
5
Basic
*
Oil temperature
degC
50
48
52
Injection quantity adjustment_02
Pump speed
r/min
1425
1425
1425
Boost pressure
kPa
66.7
65.4
68
Boost pressure
mmHg
500
490
510
Average injection quantity
mm3/st.
6.5
Basic
*
Oil temperature
degC
50
48
52
Injection quantity adjustment_03
Pump speed
r/min
1300
1300
1300
Boost pressure
kPa
66.7
65.4
68
Boost pressure
mmHg
500
490
510
Average injection quantity
mm3/st.
115.4
115.4
Oil temperature
degC
50
48
52
Remarks
(check)
(check)
Governor adjustment
Pump speed
r/min
595
595
595
Boost pressure
kPa
0
0
0
Boost pressure
mmHg
0
0
0
Average injection quantity
mm3/st.
7.2
5.2
9.2
Difference in delivery
mm3/st.
3
Basic
*
Oil temperature
degC
50
48
52
Governor adjustment_02
Pump speed
r/min
595
595
595
Boost pressure
kPa
0
0
0
Boost pressure
mmHg
0
0
0
Average injection quantity
mm3/st.
7.2
4.7
9.7
Difference in delivery
mm3/st.
3.5
Basic
*
Oil temperature
degC
50
48
52
Timer adjustment
Pump speed
r/min
100
100
100
Boost pressure
kPa
0
0
0
Boost pressure
mmHg
0
0
0
Average injection quantity
mm3/st.
103
78
128
Basic
*
Oil temperature
degC
48
46
50
Remarks
Full
Full
Timer adjustment_02
Pump speed
r/min
100
100
100
Boost pressure
kPa
0
0
0
Boost pressure
mmHg
0
0
0
Average injection quantity
mm3/st.
103
78
128
Oil temperature
degC
48
46
50
Remarks
Full
Full
Speed control lever angle
Pump speed
r/min
595
595
595
Boost pressure
kPa
0
0
0
Boost pressure
mmHg
0
0
0
Average injection quantity
mm3/st.
0
0
0
Oil temperature
degC
50
48
52
Remarks
Magnet OFF at idling position
Magnet OFF at idling position
Speed control lever angle_02
Pump speed
r/min
595
595
595
Boost pressure
kPa
0
0
0
Boost pressure
mmHg
0
0
0
Average injection quantity
mm3/st.
0
0
0
Oil temperature
degC
50
48
52
Remarks
Magnet ON at idling position and stop lever operate
Magnet ON at idling position and stop lever operate
0000000901
Pump speed
r/min
1250
1250
1250
Boost pressure
kPa
66.7
65.4
68
Boost pressure
mmHg
500
490
510
Overflow quantity with S/T ON
cm3/min
540
410
670
Oil temperature
degC
50
48
52
Stop lever angle
Pump speed
r/min
1250
1250
1250
Boost pressure
kPa
66.7
65.4
68
Boost pressure
mmHg
500
490
510
Pressure with S/T ON
kPa
736
687
785
Pressure with S/T ON
kgf/cm2
7.5
7
8
Pressure with S/T OFF
kPa
539
519
559
Pressure with S/T OFF
kgf/cm2
5.5
5.3
5.7
Basic
*
Oil temperature
degC
50
48
52
Remarks
OFF
OFF
Stop lever angle_02
Pump speed
r/min
900
900
900
Boost pressure
kPa
66.7
65.4
68
Boost pressure
mmHg
500
490
510
Pressure with S/T OFF
kPa
392
343
441
Pressure with S/T OFF
kgf/cm2
4
3.5
4.5
Oil temperature
degC
50
48
52
Stop lever angle_03
Pump speed
r/min
1100
1100
1100
Boost pressure
kPa
66.7
65.4
68
Boost pressure
mmHg
500
490
510
Pressure with S/T OFF
kPa
490
441
539
Pressure with S/T OFF
kgf/cm2
5
4.5
5.5
Oil temperature
degC
50
48
52
Stop lever angle_04
Pump speed
r/min
1250
1250
1250
Boost pressure
kPa
66.7
65.4
68
Boost pressure
mmHg
500
490
510
Pressure with S/T ON
kPa
736
677
795
Pressure with S/T ON
kgf/cm2
7.5
6.9
8.1
Pressure with S/T OFF
kPa
539
510
568
Pressure with S/T OFF
kgf/cm2
5.5
5.2
5.8
Basic
*
Oil temperature
degC
50
48
52
Remarks
OFF
OFF
0000001101
Pump speed
r/min
1250
1250
1250
Boost pressure
kPa
66.7
65.4
68
Boost pressure
mmHg
500
490
510
Timer stroke with S/T ON
mm
4.2
3.7
4.7
Timer stroke with S/T OFF
mm
2.5
2.3
2.7
Basic
*
Oil temperature
degC
50
48
52
Remarks
OFF
OFF
_02
Pump speed
r/min
900
900
900
Boost pressure
kPa
66.7
65.4
68
Boost pressure
mmHg
500
490
510
Timer stroke with S/T OFF
mm
0.9
0.2
1.6
Oil temperature
degC
50
48
52
_03
Pump speed
r/min
1100
1100
1100
Boost pressure
kPa
66.7
65.4
68
Boost pressure
mmHg
500
490
510
Timer stroke with S/T OFF
mm
2
1.4
2.6
Oil temperature
degC
50
48
52
_04
Pump speed
r/min
1250
1250
1250
Boost pressure
kPa
66.7
65.4
68
Boost pressure
mmHg
500
490
510
Timer stroke with S/T ON
mm
4.2
3.5
4.9
Timer stroke with S/T OFF
mm
2.5
2.1
2.9
Basic
*
Oil temperature
degC
50
48
52
Remarks
OFF
OFF
0000001201
Max. applied voltage
V
8
8
8
Test voltage
V
13
12
14
0000001401
Pump speed
r/min
1250
1250
1250
Boost pressure
kPa
66.7
65.4
68
Boost pressure
mmHg
500
490
510
Average injection quantity
mm3/st.
99
97
101
Timer stroke TA
mm
0
0
0.3
Timer stroke variation dT
mm
2.5
2.5
2.5
Basic
*
Oil temperature
degC
50
48
52
_02
Pump speed
r/min
1250
1250
1250
Boost pressure
kPa
66.7
65.4
68
Boost pressure
mmHg
500
490
510
Average injection quantity
mm3/st.
116
114
118
Timer stroke TA
mm
2.3
2.3
Timer stroke variation dT
mm
0.2
0.2
0.2
Oil temperature
degC
50
48
52
Remarks
(check)
(check)
_03
Pump speed
r/min
1250
1250
1250
Boost pressure
kPa
66.7
65.4
68
Boost pressure
mmHg
500
490
510
Average injection quantity
mm3/st.
99
96.5
101.5
Timer stroke TA
mm
0
0
0.5
Timer stroke variation dT
mm
2.5
2.5
2.5
Basic
*
Oil temperature
degC
50
48
52
_04
Pump speed
r/min
1250
1250
1250
Boost pressure
kPa
66.7
65.4
68
Boost pressure
mmHg
500
490
510
Average injection quantity
mm3/st.
15
12.5
17.5
Timer stroke TA
mm
3.1
2.3
3.9
Timer stroke variation dT
mm
1.1
1.1
1.1
Oil temperature
degC
50
48
52
Timing setting
K dimension
mm
3.1
3
3.2
KF dimension
mm
5.5
5.4
5.6
MS dimension
mm
0.6
0.5
0.7
BCS stroke
mm
1.6
1.5
1.7
Pre-stroke
mm
0.45
0.43
0.47
Control lever angle alpha
deg.
16
12
20
Control lever angle beta
deg.
30
25
35
Test data Ex:
0000001801 TAMPER PROOF
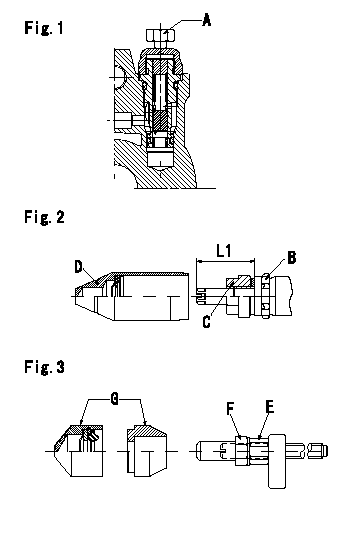
Tamperproof installation procedure
A:Position of break
B:Rubber vibration damper
C:Nut
D:Cap
E:Nut
F:Nut
G:Cap
L1:Inspection dimension
Fig. 1 Regulating valve seal
1) Target breaking torque T1
2) Maximum allowable breaking torque T2
3) Because the cap and the regulating valve are fixed using the MEC process, the bolt cannot be loosened after the bolt has been broken.
Fig.2 Full load adjusting screw
1) Confirm the position of the rubber vibration damper (B) and then tighten nut (C) to the torque T3.
Fig. 3 Maximum speed adjusting screw
1) Tighten nut (E) to the torque T4.
2) To prevent nut (E) from turning together, fix (E) using the tool, then tighten nut (F) to torque T4.
----------
L1=23~28mm T1=5~6.9N-m(0.5~0.69kgf-m) T2=9N-m(0.9kgf-m) T3=7~9N-m(0.7~0.9kgf-m) T4=6~9N-m(0.6~0.9kgf-m)
----------
L1=23~28mm
----------
L1=23~28mm T1=5~6.9N-m(0.5~0.69kgf-m) T2=9N-m(0.9kgf-m) T3=7~9N-m(0.7~0.9kgf-m) T4=6~9N-m(0.6~0.9kgf-m)
----------
L1=23~28mm
Information:
Solenoid Valve Replacement
Make reference to the at the beginning of the Testing And Adjusting section.
This procedure assumes that the ether cylinder mounted on the failed solenoid valve may still contain ether and is usable. If the ether cylinder is empty and needs replacement, complete this procedure and then follow the normal cylinder replacement procedure. See Ether Cylinder Replacement.
Solenoid Valve Assembly The solenoid valve itself is not serviceable. The complete solenoid valve assembly must be replaced. This includes the mounting bracket.1. Turn the disconnect switch to the OFF position. 2. Remove the ether cylinder from failed solenoid valve (1).3. Disconnect ether line (2) from the outlet of failed solenoid valve (1).4. Disconnect (unplug) solenoid valve harness connector (3). 5. Remove the reset switch bracket from the solenoid valve by removing two bolts (4). Leave the reset switch and wires intact on the bracket.6. Remove the solenoid valve assembly, which includes the mounting bracket, from the vehicle by removing two bolts (5).
Orifice Fitting And Filter7. Prepare the new solenoid valve for installation by installing a new orifice fitting and filter.
The orifice fitting has left-hand threads.
8. Attach the new solenoid valve and reset switch bracket to the vehicle. Tighten top two bolts (5) and leave lower two bolts (4) loose.
Gasket Filter9. Install a new gasket filter into the inlet of the solenoid valve.10. Install the same ether cylinder. See within Ether Cylinder Replacement. Hand tighten the ether cylinder to the solenoid valve. 11. Adjust the reset switch bracket such that reset switch button (6) depresses as much as possible while contacting the ether cylinder. Tighten lower two bolts (4) which fasten the reset switch bracket and solenoid valve to the vehicle. The reset switch must be adjusted correctly in order for the ether injection system to operate properly. The function of the reset switch is: to be OPEN (depressed switch button) when an ether cylinder is installed, and to be CLOSED (extended switch button) when the ether cylinder is removed. Ether injection is disabled when an ether cylinder is removed (reset switch closed).12. Verify that the reset switch is OPEN by continuity checking between the pin and socket in harness plug (7) of the reset switch. There should be no continuity.13. Reconnect the harnesses to the solenoid valve and the reset switch. Turn the disconnect switch to the ON position.Ether Cylinder Removal
Non-Empty Cylinders
During maintenance or servicing, the ether cylinders may need to be removed when they are not empty (for example, the cylinders may have to be removed to gain access to some other item requiring service). Under these conditions, it is desirable to remove and reinstall the ether cylinders without disturbing the "ether cylinder timers" within the ether injection control. This procedure allows the same ether cylinder to be reinstalled after it has been removed. Normal ether cylinder replacement is performed when the ether cylinder is empty. Normal removal of an empty ether cylinder resets the "ether cylinder timers" within the ether injection control. See Ether Cylinder Replacement. Failure to
Make reference to the at the beginning of the Testing And Adjusting section.
This procedure assumes that the ether cylinder mounted on the failed solenoid valve may still contain ether and is usable. If the ether cylinder is empty and needs replacement, complete this procedure and then follow the normal cylinder replacement procedure. See Ether Cylinder Replacement.
Solenoid Valve Assembly The solenoid valve itself is not serviceable. The complete solenoid valve assembly must be replaced. This includes the mounting bracket.1. Turn the disconnect switch to the OFF position. 2. Remove the ether cylinder from failed solenoid valve (1).3. Disconnect ether line (2) from the outlet of failed solenoid valve (1).4. Disconnect (unplug) solenoid valve harness connector (3). 5. Remove the reset switch bracket from the solenoid valve by removing two bolts (4). Leave the reset switch and wires intact on the bracket.6. Remove the solenoid valve assembly, which includes the mounting bracket, from the vehicle by removing two bolts (5).
Orifice Fitting And Filter7. Prepare the new solenoid valve for installation by installing a new orifice fitting and filter.
The orifice fitting has left-hand threads.
8. Attach the new solenoid valve and reset switch bracket to the vehicle. Tighten top two bolts (5) and leave lower two bolts (4) loose.
Gasket Filter9. Install a new gasket filter into the inlet of the solenoid valve.10. Install the same ether cylinder. See within Ether Cylinder Replacement. Hand tighten the ether cylinder to the solenoid valve. 11. Adjust the reset switch bracket such that reset switch button (6) depresses as much as possible while contacting the ether cylinder. Tighten lower two bolts (4) which fasten the reset switch bracket and solenoid valve to the vehicle. The reset switch must be adjusted correctly in order for the ether injection system to operate properly. The function of the reset switch is: to be OPEN (depressed switch button) when an ether cylinder is installed, and to be CLOSED (extended switch button) when the ether cylinder is removed. Ether injection is disabled when an ether cylinder is removed (reset switch closed).12. Verify that the reset switch is OPEN by continuity checking between the pin and socket in harness plug (7) of the reset switch. There should be no continuity.13. Reconnect the harnesses to the solenoid valve and the reset switch. Turn the disconnect switch to the ON position.Ether Cylinder Removal
Non-Empty Cylinders
During maintenance or servicing, the ether cylinders may need to be removed when they are not empty (for example, the cylinders may have to be removed to gain access to some other item requiring service). Under these conditions, it is desirable to remove and reinstall the ether cylinders without disturbing the "ether cylinder timers" within the ether injection control. This procedure allows the same ether cylinder to be reinstalled after it has been removed. Normal ether cylinder replacement is performed when the ether cylinder is empty. Normal removal of an empty ether cylinder resets the "ether cylinder timers" within the ether injection control. See Ether Cylinder Replacement. Failure to
Have questions with 104742-3022?
Group cross 104742-3022 ZEXEL
Mitsubishi-Heav
104742-3022
32A6537330
INJECTION-PUMP ASSEMBLY
S4S-DT
S4S-DT