Information injection-pump assembly
ZEXEL
104742-1010
1047421010
ISUZU
8944046530
8944046530
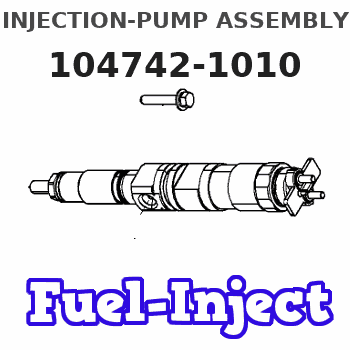
Rating:
Cross reference number
ZEXEL
104742-1010
1047421010
ISUZU
8944046530
8944046530
Zexel num
Bosch num
Firm num
Name
Calibration Data:
Adjustment conditions
Test oil
1404 Test oil ISO4113orSAEJ967d
1404 Test oil ISO4113orSAEJ967d
Test oil temperature
degC
45
45
50
Nozzle
105000-2010
Bosch type code
NP-DN12SD12TT
Nozzle holder
105780-2080
Opening pressure
MPa
14.7
14.7
15.19
Opening pressure
kgf/cm2
150
150
155
Injection pipe
Inside diameter - outside diameter - length (mm) mm 2-6-840
Inside diameter - outside diameter - length (mm) mm 2-6-840
Transfer pump pressure
kPa
20
20
20
Transfer pump pressure
kgf/cm2
0.2
0.2
0.2
Direction of rotation (viewed from drive side)
Right R
Right R
Injection timing adjustment
Pump speed
r/min
1050
1050
1050
Average injection quantity
mm3/st.
67.1
66.6
67.6
Difference in delivery
mm3/st.
4
Basic
*
Oil temperature
degC
50
48
52
Injection timing adjustment_02
Pump speed
r/min
500
500
500
Average injection quantity
mm3/st.
49.2
45.7
52.7
Difference in delivery
mm3/st.
6
Oil temperature
degC
48
46
50
Injection timing adjustment_03
Pump speed
r/min
700
700
700
Average injection quantity
mm3/st.
56.3
52.8
59.8
Difference in delivery
mm3/st.
6
Oil temperature
degC
50
48
52
Injection timing adjustment_04
Pump speed
r/min
1050
1050
1050
Average injection quantity
mm3/st.
67.1
66.1
68.1
Difference in delivery
mm3/st.
4
Basic
*
Oil temperature
degC
50
48
52
Injection timing adjustment_05
Pump speed
r/min
1400
1400
1400
Average injection quantity
mm3/st.
66.9
63.4
70.4
Difference in delivery
mm3/st.
6
Oil temperature
degC
50
48
52
Injection timing adjustment_06
Pump speed
r/min
1750
1750
1750
Average injection quantity
mm3/st.
65.5
62
69
Difference in delivery
mm3/st.
6
Oil temperature
degC
50
48
52
Injection quantity adjustment
Pump speed
r/min
2100
2100
2100
Average injection quantity
mm3/st.
18
15
21
Difference in delivery
mm3/st.
7
Basic
*
Oil temperature
degC
52
50
54
Injection quantity adjustment_02
Pump speed
r/min
2200
2200
2200
Average injection quantity
mm3/st.
10
Oil temperature
degC
52
50
54
Injection quantity adjustment_03
Pump speed
r/min
2100
2100
2100
Average injection quantity
mm3/st.
18
15
21
Difference in delivery
mm3/st.
7
Oil temperature
degC
52
50
54
Governor adjustment
Pump speed
r/min
350
350
350
Average injection quantity
mm3/st.
9.5
7.5
11.5
Difference in delivery
mm3/st.
2
Basic
*
Oil temperature
degC
48
46
50
Governor adjustment_02
Pump speed
r/min
350
350
350
Average injection quantity
mm3/st.
9.5
7.5
11.5
Difference in delivery
mm3/st.
3
Oil temperature
degC
48
46
50
Timer adjustment
Pump speed
r/min
100
100
100
Average injection quantity
mm3/st.
80
80
Basic
*
Oil temperature
degC
48
46
50
Remarks
Full
Full
Timer adjustment_02
Pump speed
r/min
100
100
100
Average injection quantity
mm3/st.
80
80
Oil temperature
degC
48
46
50
Speed control lever angle
Pump speed
r/min
350
350
350
Average injection quantity
mm3/st.
0
0
0
Oil temperature
degC
48
46
50
Remarks
Magnet OFF at idling position
Magnet OFF at idling position
Speed control lever angle_02
Pump speed
r/min
100
100
100
Average injection quantity
mm3/st.
0
0
0
Oil temperature
degC
48
46
50
Remarks
Magnet OFF at idling position
Magnet OFF at idling position
0000000901
Pump speed
r/min
1500
1500
1500
Overflow quantity
cm3/min
450
320
580
Oil temperature
degC
50
48
52
Stop lever angle
Pump speed
r/min
1500
1500
1500
Pressure
kPa
539
519
559
Pressure
kgf/cm2
5.5
5.3
5.7
Basic
*
Oil temperature
degC
50
48
52
Stop lever angle_02
Pump speed
r/min
1500
1500
1500
Pressure
kPa
539
519
559
Pressure
kgf/cm2
5.5
5.3
5.7
Oil temperature
degC
50
48
52
Stop lever angle_03
Pump speed
r/min
1750
1750
1750
Pressure
kPa
637
608
666
Pressure
kgf/cm2
6.5
6.2
6.8
Oil temperature
degC
50
48
52
0000001101
Pump speed
r/min
1600
1600
1600
Timer stroke
mm
3.5
3.3
3.7
Basic
*
Oil temperature
degC
50
48
52
_02
Pump speed
r/min
1450
1400
1500
Timer stroke
mm
0.5
0.5
0.5
Oil temperature
degC
50
48
52
_03
Pump speed
r/min
1500
1500
1500
Timer stroke
mm
1.2
0.9
1.5
Oil temperature
degC
50
48
52
_04
Pump speed
r/min
1600
1600
1600
Timer stroke
mm
3.5
3.3
3.7
Basic
*
Oil temperature
degC
50
48
52
_05
Pump speed
r/min
1700
1700
1700
Timer stroke
mm
5.7
5.5
6
Oil temperature
degC
50
48
52
0000001201
Max. applied voltage
V
16
16
16
Test voltage
V
25
24
26
Timing setting
K dimension
mm
3.1
3
3.2
KF dimension
mm
5.5
5.4
5.6
MS dimension
mm
1
0.9
1.1
Pre-stroke
mm
0.45
0.43
0.47
Control lever angle alpha
deg.
15
11
19
Control lever angle beta
deg.
41
36
46
Information:
1. External View
(Natural-aspirated engine)
* This photo shows the model 6D14.(Turbocharged engine)
* This photo shows the model 6D14-T.2. Major Specifications
2.1 Major Specifications
2.2 Engine Outputs Classified by Application
1. The output (SAE, gross) is corrected to standard ambient conditions based on SAE J1349.2. The continuous rated output allows 10% (one hour) overload operation.3. Engine Number And Nameplate
(1) Engine number The engine number is stamped on the position as illustrated.Example: The engine number is important in knowing the history of the engine.(2) Nameplate The nameplate is attached to the portion as illustrated.The nameplate bears the followings: 4. General Precautions For Servicing
Before starting the service procedures, check the vehicle for total time driven, use conditions, and user's complaints and requests to know exactly the engine conditions. Record information where necessary.To ensure you are doing correct and efficient service jobs, observe the following precautions: (1) Before performing the service procedures given in this manual, know the trouble spots and isolate the possible cause to determine whether the removal or disassembly procedure is required.(2) Select a flat surface for the service job.(3) When servicing the electrical system, be sure to disconnect the negative cable from the battery.(4) Carefully check parts for oil leaks before cleaning. After cleaning, it may become difficult to spot defective areas.(5) Ready and make the most of the special tools required for servicing. Use the right tools (specified special tools) in the right place to prevent damages to parts and personal injury.(6) Make alignment marks and keep disassembled parts neatly arranged to ensure that they are reassembled into the right positions.* Special care must be taken for assemblies involving a number of parts, similar parts, or parts identical at right- and left-hand sides to ensure correct reassembly.* For alignment and punching markings, select a position that would not mar the appearance and function.* Clearly distinguish parts to be replaced from those reused. (7) The oil seals, packings, O-rings, and other rubber parts, gaskets, and split pins must be replaced with a new one whenever they are removed. For replacement, use Mitsubishi Genuine parts. (8) Apply the specified grease to U-packings, oil seals, dust seals, and bearings before installation.(9) When work requires an assistant or two, always make sure of the safety each other. Never play with switches and levers.(10) Make sure that your shoes are free from grease and oil especially when working on a heavy item.(11) When checking or changing lubricants, wipe off grease and oil from parts immediately with a waste.(12) Special care must be taken in handling sensors and relays which are suspectible to shocks and heat.(13) Use care so that hands and fingers are not injured by sharp edges or corners of the parts.(14) Wear safety goggles whenever handling a grinder or welding machine. Wear gloves as required to ensure utmost safety.5. General Bolts And Nuts Tightening Torque Table
Unless otherwise specified, the parts and equipment of vehicle must be tightened by the following standard bolts and nuts. Tightening torques for these bolts and nuts are shown below.
(Natural-aspirated engine)
* This photo shows the model 6D14.(Turbocharged engine)
* This photo shows the model 6D14-T.2. Major Specifications
2.1 Major Specifications
2.2 Engine Outputs Classified by Application
1. The output (SAE, gross) is corrected to standard ambient conditions based on SAE J1349.2. The continuous rated output allows 10% (one hour) overload operation.3. Engine Number And Nameplate
(1) Engine number The engine number is stamped on the position as illustrated.Example: The engine number is important in knowing the history of the engine.(2) Nameplate The nameplate is attached to the portion as illustrated.The nameplate bears the followings: 4. General Precautions For Servicing
Before starting the service procedures, check the vehicle for total time driven, use conditions, and user's complaints and requests to know exactly the engine conditions. Record information where necessary.To ensure you are doing correct and efficient service jobs, observe the following precautions: (1) Before performing the service procedures given in this manual, know the trouble spots and isolate the possible cause to determine whether the removal or disassembly procedure is required.(2) Select a flat surface for the service job.(3) When servicing the electrical system, be sure to disconnect the negative cable from the battery.(4) Carefully check parts for oil leaks before cleaning. After cleaning, it may become difficult to spot defective areas.(5) Ready and make the most of the special tools required for servicing. Use the right tools (specified special tools) in the right place to prevent damages to parts and personal injury.(6) Make alignment marks and keep disassembled parts neatly arranged to ensure that they are reassembled into the right positions.* Special care must be taken for assemblies involving a number of parts, similar parts, or parts identical at right- and left-hand sides to ensure correct reassembly.* For alignment and punching markings, select a position that would not mar the appearance and function.* Clearly distinguish parts to be replaced from those reused. (7) The oil seals, packings, O-rings, and other rubber parts, gaskets, and split pins must be replaced with a new one whenever they are removed. For replacement, use Mitsubishi Genuine parts. (8) Apply the specified grease to U-packings, oil seals, dust seals, and bearings before installation.(9) When work requires an assistant or two, always make sure of the safety each other. Never play with switches and levers.(10) Make sure that your shoes are free from grease and oil especially when working on a heavy item.(11) When checking or changing lubricants, wipe off grease and oil from parts immediately with a waste.(12) Special care must be taken in handling sensors and relays which are suspectible to shocks and heat.(13) Use care so that hands and fingers are not injured by sharp edges or corners of the parts.(14) Wear safety goggles whenever handling a grinder or welding machine. Wear gloves as required to ensure utmost safety.5. General Bolts And Nuts Tightening Torque Table
Unless otherwise specified, the parts and equipment of vehicle must be tightened by the following standard bolts and nuts. Tightening torques for these bolts and nuts are shown below.