Information injection-pump assembly
ZEXEL
104741-7000
1047417000
YANMAR
12957451070
12957451070

Rating:
Cross reference number
ZEXEL
104741-7000
1047417000
YANMAR
12957451070
12957451070
Zexel num
Bosch num
Firm num
Name
Calibration Data:
Adjustment conditions
Test oil
1404 Test oil ISO4113orSAEJ967d
1404 Test oil ISO4113orSAEJ967d
Test oil temperature
degC
45
45
50
Nozzle
105780-0060
Bosch type code
NP-DN0SD1510
Nozzle holder
105780-2150
Opening pressure
MPa
13
13
13.3
Opening pressure
kgf/cm2
133
133
136
Injection pipe
157805-7320
Injection pipe
Inside diameter - outside diameter - length (mm) mm 2-6-450
Inside diameter - outside diameter - length (mm) mm 2-6-450
Joint assembly
157641-4720
Tube assembly
157641-4020
Transfer pump pressure
kPa
20
20
20
Transfer pump pressure
kgf/cm2
0.2
0.2
0.2
Direction of rotation (viewed from drive side)
Right R
Right R
Timer measuring device installation position
Low pressure side LOW PRESSURE SIDE
Low pressure side LOW PRESSURE SIDE
Injection timing adjustment
Pump speed
r/min
1700
1700
1700
Average injection quantity
mm3/st.
69
68.5
69.5
Difference in delivery
mm3/st.
4
Basic
*
Oil temperature
degC
50
48
52
Injection timing adjustment_02
Pump speed
r/min
500
500
500
Average injection quantity
mm3/st.
35.3
35.3
35.3
Oil temperature
degC
48
46
50
Injection timing adjustment_03
Pump speed
r/min
750
750
750
Average injection quantity
mm3/st.
37.4
37.4
37.4
Oil temperature
degC
50
48
52
Injection timing adjustment_04
Pump speed
r/min
1000
1000
1000
Average injection quantity
mm3/st.
46.1
46.1
46.1
Oil temperature
degC
50
48
52
Injection timing adjustment_05
Pump speed
r/min
1350
1350
1350
Average injection quantity
mm3/st.
58.9
58.9
58.9
Oil temperature
degC
50
48
52
Injection timing adjustment_06
Pump speed
r/min
1700
1700
1700
Average injection quantity
mm3/st.
69
68
70
Difference in delivery
mm3/st.
4
Basic
*
Oil temperature
degC
50
48
52
Injection quantity adjustment
Pump speed
r/min
1990
1990
1990
Average injection quantity
mm3/st.
12.5
8.5
16.5
Difference in delivery
mm3/st.
4
Basic
*
Oil temperature
degC
50
48
52
Injection quantity adjustment_02
Pump speed
r/min
1990
1990
1990
Average injection quantity
mm3/st.
12.5
8
17
Oil temperature
degC
50
48
52
Injection quantity adjustment_03
Pump speed
r/min
2200
2200
2200
Average injection quantity
mm3/st.
5
Oil temperature
degC
52
50
54
Governor adjustment
Pump speed
r/min
325
325
325
Average injection quantity
mm3/st.
13.1
11.1
15.1
Difference in delivery
mm3/st.
2
Basic
*
Oil temperature
degC
48
46
50
Governor adjustment_02
Pump speed
r/min
325
325
325
Average injection quantity
mm3/st.
13.1
10.6
15.6
Difference in delivery
mm3/st.
2
Oil temperature
degC
48
46
50
Timer adjustment
Pump speed
r/min
100
100
100
Average injection quantity
mm3/st.
77
57
97
Basic
*
Oil temperature
degC
48
46
50
Remarks
Full
Full
Timer adjustment_02
Pump speed
r/min
100
100
100
Average injection quantity
mm3/st.
77
57
97
Oil temperature
degC
48
46
50
Speed control lever angle
Pump speed
r/min
100
100
100
Average injection quantity
mm3/st.
0
0
0
Oil temperature
degC
48
46
50
Remarks
Magnet ON at idling position and reversed operate
Magnet ON at idling position and reversed operate
Speed control lever angle_02
Pump speed
r/min
325
325
325
Average injection quantity
mm3/st.
0
0
0
Oil temperature
degC
48
46
50
Remarks
Magnet ON at idling position and reversed operate
Magnet ON at idling position and reversed operate
Speed control lever angle_03
Pump speed
r/min
100
100
100
Average injection quantity
mm3/st.
0
0
0
Oil temperature
degC
48
46
50
Remarks
Magnet OFF at idling position and stop lever operate
Magnet OFF at idling position and stop lever operate
Speed control lever angle_04
Pump speed
r/min
325
325
325
Average injection quantity
mm3/st.
0
0
0
Oil temperature
degC
48
46
50
Remarks
Magnet OFF at idling position and stop lever operate
Magnet OFF at idling position and stop lever operate
0000000901
Pump speed
r/min
1350
1350
1350
Oil temperature
degC
50
48
52
Remarks
MEASURE
MEASURE
Stop lever angle
Pump speed
r/min
1350
1350
1350
Pressure
kPa
353
324
382
Pressure
kgf/cm2
3.6
3.3
3.9
Basic
*
Oil temperature
degC
50
48
52
Stop lever angle_02
Pump speed
r/min
1000
1000
1000
Pressure
kPa
245
206
284
Pressure
kgf/cm2
2.5
2.1
2.9
Oil temperature
degC
50
48
52
Stop lever angle_03
Pump speed
r/min
1350
1350
1350
Pressure
kPa
353
314
392
Pressure
kgf/cm2
3.6
3.2
4
Basic
*
Oil temperature
degC
50
48
52
Stop lever angle_04
Pump speed
r/min
1500
1500
1500
Pressure
kPa
402
363
441
Pressure
kgf/cm2
4.1
3.7
4.5
Oil temperature
degC
50
48
52
0000001101
Pump speed
r/min
2100
2100
2100
Timer stroke
mm
0
0
0
Oil temperature
degC
52
50
54
_02
Pump speed
r/min
2100
2100
2100
Timer stroke
mm
0
0
0
Oil temperature
degC
52
50
54
0000001201
Max. applied voltage
V
8
8
8
Test voltage
Reverse operation (At Normal: OFF, At Stop: ON) V 13 12 14
Reverse operation (At Normal: OFF, At Stop: ON) V 13 12 14
Timing setting
K dimension
mm
3.1
3
3.2
KF dimension
mm
5.5
5.4
5.6
MS dimension
mm
0.7
0.6
0.8
Pre-stroke
mm
0.45
0.43
0.47
Control lever angle alpha
deg.
25
21
29
Control lever angle beta
deg.
41
36
46
Test data Ex:
0000001801 Temp. adjust full-load screw
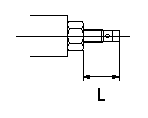
Temporary full load screw adjustment
Set the full load screw protrusion at L mm at assembly.
----------
L=14+-0.5mm
----------
L=14+-0.5mm
----------
L=14+-0.5mm
----------
L=14+-0.5mm
0000001901 STOP LEVER ADJUSTMENT
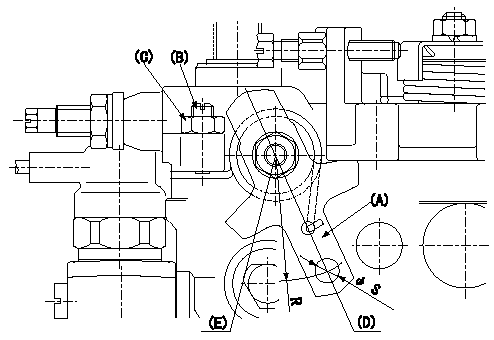
Adjustment of the stop lever
1. Confirm that the starting injection quantity is within standards at the normal position.
If below the specified lower limit, move the stop lever serrations one tooth and reconfirm.
2. Pull the stop lever (A) to the fuel cut direction at the standard idling speed of N and adjust the screw (B) to the position Q.
Fix nut (C) to the torque T at the position where the clearance between the stop lever and the end of the screw is L (the screw is returned n turns).
The head of the screw must protrude above the face of the nut. If the head of the screw is below the face of the nut, adjust the clearance between the stop lever A and the end of the screw at Q to L or more.
3. If adjustment in item 2 is not possible, move the stop lever installation position 1 tooth.
4. The stop lever's operating force is max. M (at R = 35). The stop lever must operate smoothly.
(D) Normal position
(E) Stop position
----------
N=325r/min Q=0mm3/st T=6~9N-m(0.6~0.9kgf-m) L=1mm M=4.0kg n=1
----------
S=Dia6.5+0.09mm R=35mm
----------
N=325r/min Q=0mm3/st T=6~9N-m(0.6~0.9kgf-m) L=1mm M=4.0kg n=1
----------
S=Dia6.5+0.09mm R=35mm
Information:
This instruction is written for electronic technicians only, and must not be used by service personnel with no training or knowledge of electronics. For repairs that can be done by the Caterpillar Dealer Serviceman, with no knowledge of electronics, see Special Instruction Form SMHS6964 "Using 1P3500 and 2P8280 Injection Timing Groups."As an aid to the technician for troubleshooting the inverter and timing light, the following information is given in this instruction:1. Circuit board illustrations showing the position of each of the components and the test points (T) for using a voltmeter or an oscilloscope.2. Schematics of the electrical circuit so the technician can easily follow the sequence of the circuit.3. Test point values.4. Electrical parts replacement information.5. Timing light calibration procedure.Timing Light
1P3500 And 2P8280 Timing Lights - Electrical Schematic, Test Points And Parts List
Inverter - Electrical Schematic, Test Points And Parts List
There is a two position switch that is marked ADV.-RPM on the side of the 1P3499 Timing Light. When the timing light is in use, operation of the ADV.-RPM switch is as follows:RPM Position
A fuel injection pulse opens the switch in the transducer and starts a positive pulse (TP9) of fixed duration, from the monostable composed of Q2 and Q3. This pulse turns on a transistor switch Q4, allowing current to pass through meter M1, which mechanically averages pulses from an operating engine, and is calibrated to read RPM. Switch S2 grounds the gate of SCR1 to prevent the flash tube from strobing.ADV. Position
A fuel injection pulse again starts a pulse from the monostable. Adjustment of R7, the TIME-ADVANCE control, now determines the pulse duration from the monostable. When R7 is adjusted so that TDC on the damper coincides with the pointer on the block of an operating engine, the monostable pulse duration is exactly the same as the fuel system advance measured in seconds. Transistor switch Q4 again turns on, allowing current to pass through meter M1, causing a meter indicator that is calibrated in degrees of advance instead of seconds.Electrical Calibration Procedure
Before the electrical calibration can be done, the following equipment must be obtained.1) Oscilloscope with triggered sweep. Heath Co. M/N SO-4530 or equivalent.2) Signal generator. Heath M/N SG-72A or equivalent.3) Electronic counter. Data Precision M/N 5740 or equivalent.4) Electronic switch (dealer built).Calibration Procedure
(1) Hold the 1P3499 Timing Light in the same position (about a 45° angle) as if measuring the timing advance on an engine, and check the mechanical meter zero. Make an adjustment to zero if necessary. (2) To remove the protective rubber boot from the flash tube, twist the rubber boot and pull it away from the timing light as shown. (3) Remove the right side (side that has the serial number tag) of the timing light case.(4) Connect the 1P3499 Timing Light to a circuit like the one that follows. This will simulate (be the same as) a fuel flow transducer on an engine that is operating at 2400 RPM. (5) Turn the TIME-ADV. control counterclockwise (CCW) to its minimum
1P3500 And 2P8280 Timing Lights - Electrical Schematic, Test Points And Parts List
Inverter - Electrical Schematic, Test Points And Parts List
There is a two position switch that is marked ADV.-RPM on the side of the 1P3499 Timing Light. When the timing light is in use, operation of the ADV.-RPM switch is as follows:RPM Position
A fuel injection pulse opens the switch in the transducer and starts a positive pulse (TP9) of fixed duration, from the monostable composed of Q2 and Q3. This pulse turns on a transistor switch Q4, allowing current to pass through meter M1, which mechanically averages pulses from an operating engine, and is calibrated to read RPM. Switch S2 grounds the gate of SCR1 to prevent the flash tube from strobing.ADV. Position
A fuel injection pulse again starts a pulse from the monostable. Adjustment of R7, the TIME-ADVANCE control, now determines the pulse duration from the monostable. When R7 is adjusted so that TDC on the damper coincides with the pointer on the block of an operating engine, the monostable pulse duration is exactly the same as the fuel system advance measured in seconds. Transistor switch Q4 again turns on, allowing current to pass through meter M1, causing a meter indicator that is calibrated in degrees of advance instead of seconds.Electrical Calibration Procedure
Before the electrical calibration can be done, the following equipment must be obtained.1) Oscilloscope with triggered sweep. Heath Co. M/N SO-4530 or equivalent.2) Signal generator. Heath M/N SG-72A or equivalent.3) Electronic counter. Data Precision M/N 5740 or equivalent.4) Electronic switch (dealer built).Calibration Procedure
(1) Hold the 1P3499 Timing Light in the same position (about a 45° angle) as if measuring the timing advance on an engine, and check the mechanical meter zero. Make an adjustment to zero if necessary. (2) To remove the protective rubber boot from the flash tube, twist the rubber boot and pull it away from the timing light as shown. (3) Remove the right side (side that has the serial number tag) of the timing light case.(4) Connect the 1P3499 Timing Light to a circuit like the one that follows. This will simulate (be the same as) a fuel flow transducer on an engine that is operating at 2400 RPM. (5) Turn the TIME-ADV. control counterclockwise (CCW) to its minimum