Information injection-pump assembly
ZEXEL
104741-6781
1047416781
ISUZU
8970134681
8970134681
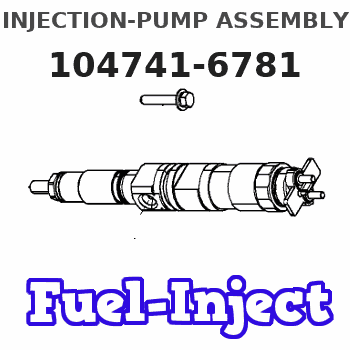
Rating:
Cross reference number
ZEXEL
104741-6781
1047416781
ISUZU
8970134681
8970134681
Zexel num
Bosch num
Firm num
Name
Calibration Data:
Adjustment conditions
Test oil
1404 Test oil ISO4113orSAEJ967d
1404 Test oil ISO4113orSAEJ967d
Test oil temperature
degC
45
45
50
Nozzle
105000-2010
Bosch type code
NP-DN12SD12TT
Nozzle holder
105780-2080
Opening pressure
MPa
14.7
14.7
15.19
Opening pressure
kgf/cm2
150
150
155
Injection pipe
Inside diameter - outside diameter - length (mm) mm 2-6-840
Inside diameter - outside diameter - length (mm) mm 2-6-840
Transfer pump pressure
kPa
20
20
20
Transfer pump pressure
kgf/cm2
0.2
0.2
0.2
Direction of rotation (viewed from drive side)
Right R
Right R
Injection timing adjustment
Pump speed
r/min
1000
1000
1000
Average injection quantity
mm3/st.
41.7
41.2
42.2
Difference in delivery
mm3/st.
3.5
Basic
*
Oil temperature
degC
50
48
52
Injection timing adjustment_02
Pump speed
r/min
500
500
500
Average injection quantity
mm3/st.
38.3
38.3
38.3
Oil temperature
degC
48
46
50
Injection timing adjustment_03
Pump speed
r/min
700
700
700
Average injection quantity
mm3/st.
34.4
34.4
34.4
Oil temperature
degC
50
48
52
Injection timing adjustment_04
Pump speed
r/min
1000
1000
1000
Average injection quantity
mm3/st.
41.7
40.7
42.7
Difference in delivery
mm3/st.
3.5
Basic
*
Oil temperature
degC
50
48
52
Injection timing adjustment_05
Pump speed
r/min
1450
1450
1450
Average injection quantity
mm3/st.
43.9
40.9
46.9
Oil temperature
degC
50
48
52
Injection timing adjustment_06
Pump speed
r/min
1800
1800
1800
Average injection quantity
mm3/st.
47.5
44
51
Difference in delivery
mm3/st.
5.5
Oil temperature
degC
50
48
52
Injection quantity adjustment
Pump speed
r/min
2100
2100
2100
Average injection quantity
mm3/st.
10.6
7.6
13.6
Difference in delivery
mm3/st.
4
Basic
*
Oil temperature
degC
52
50
54
Injection quantity adjustment_02
Pump speed
r/min
2300
2300
2300
Average injection quantity
mm3/st.
5
Oil temperature
degC
52
50
54
Injection quantity adjustment_03
Pump speed
r/min
2100
2100
2100
Average injection quantity
mm3/st.
10.6
7.6
13.6
Difference in delivery
mm3/st.
4
Oil temperature
degC
52
50
54
Governor adjustment
Pump speed
r/min
425
425
425
Average injection quantity
mm3/st.
5.5
3.5
7.5
Difference in delivery
mm3/st.
2
Basic
*
Oil temperature
degC
48
46
50
Governor adjustment_02
Pump speed
r/min
425
425
425
Average injection quantity
mm3/st.
5.5
3.5
7.5
Difference in delivery
mm3/st.
2
Oil temperature
degC
48
46
50
Timer adjustment
Pump speed
r/min
100
100
100
Average injection quantity
mm3/st.
60
60
100
Basic
*
Oil temperature
degC
48
46
50
Remarks
Full
Full
Timer adjustment_02
Pump speed
r/min
100
100
100
Average injection quantity
mm3/st.
80
60
100
Oil temperature
degC
48
46
50
Speed control lever angle
Pump speed
r/min
390
390
390
Average injection quantity
mm3/st.
0
0
0
Oil temperature
degC
48
46
50
Remarks
Magnet OFF at idling position
Magnet OFF at idling position
0000000901
Pump speed
r/min
1600
1600
1600
Overflow quantity with S/T ON
cm3/min
490
360
620
Overflow quantity with S/T OFF
cm3/min
580
450
710
Oil temperature
degC
50
48
52
Stop lever angle
Pump speed
r/min
1600
1600
1600
Pressure with S/T OFF
kPa
451
431
490
Pressure with S/T OFF
kgf/cm2
4.6
4.4
5
Basic
*
Oil temperature
degC
50
48
52
Stop lever angle_02
Pump speed
r/min
1600
1600
1600
Pressure with S/T OFF
kPa
451
431
490
Pressure with S/T OFF
kgf/cm2
4.6
4.4
5
Basic
*
Oil temperature
degC
50
48
52
0000001101
Pump speed
r/min
1600
1600
1600
Timer stroke with S/T OFF
mm
2.2
2
2.4
Basic
*
Oil temperature
degC
50
48
52
_02
Pump speed
r/min
900
900
900
Timer stroke with S/T ON
mm
0.5
0.5
Oil temperature
degC
50
48
52
_03
Pump speed
r/min
1500
1500
1500
Timer stroke with S/T OFF
mm
0.5
Oil temperature
degC
50
48
52
_04
Pump speed
r/min
1600
1600
1600
Timer stroke with S/T OFF
mm
2.2
2
2.4
Basic
*
Oil temperature
degC
50
48
52
_05
Pump speed
r/min
1800
1800
1800
Timer stroke with S/T OFF
mm
7
6.7
7.4
Oil temperature
degC
50
48
52
0000001201
Max. applied voltage
V
8
8
8
Test voltage
V
13
12
14
Timing setting
K dimension
mm
2.8
2.7
2.9
KF dimension
mm
5
4.9
5.1
MS dimension
mm
1
0.9
1.1
Pre-stroke
mm
0.45
0.43
0.47
Control lever angle alpha
deg.
18
14
22
Control lever angle beta
deg.
31
26
36
Test data Ex:
0000001801 V-FICD ADJUSTMENT
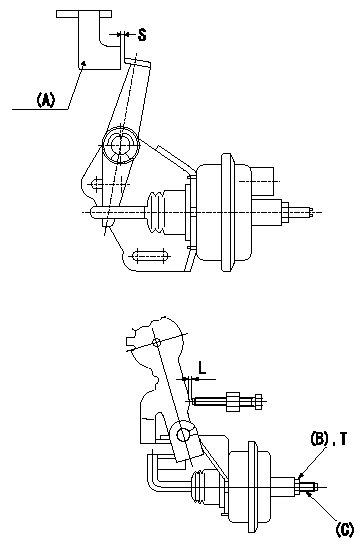
Adjustment of the V-FICD
1. Adjust to obtain S.
2. Confirm that L1 is obtained when negative pressure P1 (P2 ) is applied to the actuator.
To adjust the stroke adjust the actuator's stroke adjusting screw (C).
(A) Control lever
(B) Lock nut (Tightening torque T)
(C) Stroke adjusting screw
----------
S=2+1mm L=0.7+-0.2mm P1=-46.7kPa P2=-350mmHg
----------
S=2+1mm L=0.7+-0.2mm T=1.2~1.5N-m{0.12~0.15kgf-m}
----------
S=2+1mm L=0.7+-0.2mm P1=-46.7kPa P2=-350mmHg
----------
S=2+1mm L=0.7+-0.2mm T=1.2~1.5N-m{0.12~0.15kgf-m}
0000001901 A/T PLATE ADJUSTMENT
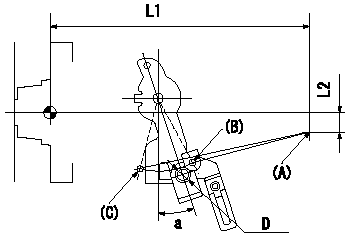
A/T plate adjustment
Rotate the control lever from the idle position (B) to the full-speed position (C).
Adjust the A/T plate (A) so that (A) (C) - (A) (B) = L3, and fix.
When fixing, fix the A/T plate outside the range diameter 9.2 mm from the center of the control lever's wire hole (hole dia. 8.5 mm).
(B): B idle position
(C): B' full
----------
L3=32.9+-1mm
----------
L1=169.8mm L2=12.4mm a=18+-4deg D=Dia.9.2mm
----------
L3=32.9+-1mm
----------
L1=169.8mm L2=12.4mm a=18+-4deg D=Dia.9.2mm
0000002001 POTENTIOMETER ADJUSTMENT
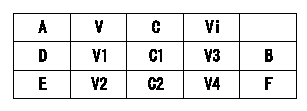
A = lever position
B = adjusting point
Vi = applied voltage
V = output voltage
C = lever angle
D = full speed
E = idle
F = confirmation point
----------
----------
V1=8.2+-0.03V V2=3.94 or less V C1=31+-5deg C2=0deg V3=10V V4=10V
----------
----------
V1=8.2+-0.03V V2=3.94 or less V C1=31+-5deg C2=0deg V3=10V V4=10V
Information:
Problem
The fuel lines on certain 3408 Generator Set, Industrial, and Marine engines may fail. New fuel line groups can be installed that have a longer service life.
Affected Product
Model & Identification Number
3408 (67U12405-15199; 78Z2829-4522; 99U5985-7229)
Parts Needed
1 - 6I0030 Fuel Line Group6 - 5M2894 Washer6 - 0S0509 BoltAdditional Parts Needed For DIT Engines (Non-Aftercooled)
5 - 5M2894 Washer1 - 4P8261 Bracket1 - 4P8385 Bracket2 - 5P0537 Washer5 - 0S1571 Bolt2 - 0S1615 Bolt3 - 8T1296 WasherAction Required
Parts Stock
Make sure that all 7C6931, 7C6932, 7C6933, 7C6934, 7C6935, 7C6936, 7C6937 and 7C6938 Fuel Lines were removed from parts stock while implementing Product Support Program PS4737.
Affected Product
Remove the existing fuel lines and install the new fuel injection line groups as a group. See the attached rework procedure.
Do not over tighten the screws of the metal-to- metal fuel line clamps. Use a 6V6069 Torgue Screwdriver or similar tool to tighten the screw to a torgue of 2.25 N m (20 lb in).
Service Claim Allowances
Parts Stock
Refer to the Product Support Program PS4737.
Affected Product
This is a 2.2-hour job.
Parts Disposition
Handle the parts in accordance with your Warranty Bulletin on warranty parts handling.
Attach. (1-Rework Procedure)Rework Procedure
Refer to the parts list and illustrations. Replace the existing fuel lines and their related parts with the new 6I0030 Fuel Line Group.
To insure that the clamp locations are correct, install fuel line group as assembled. In a case where it is necessary to remove the clamps, mark their locations to insure the correct position when assembling.
1. Clean and paint the new 6I0030 Fuel Line Group before proceeding to the job site.A) Install 5F2807 Plastic Caps and 2F2990 Plastic Plugs on the ends of the lines.B) Clean and paint the fuel line group.C) After drying, do not remove the plastic plugs and caps until the fuel line group is ready to be installed on the engine. Transport the fuel line group in it's original shipping box. If the engine to be reworked is non-aftercooled, also clean and pre-paint the new 4P8385 and 4P8261 Brackets.
2. Remove all the mounting bolts from the fuel line bracket at the aftercooler housing on DITA engines or at the 6N1671 Bracket on DIT engines. The 6N1671 Bracket in the vee of the DIT (non- aftercooled) engines is used to support the fuel line brackets. This bracket is part of the 6N1672 Fastener Group, Affected Product not having an aftercooler required a new two piece bracket.
3. Disconnect all the fuel line nuts at the fuel injection pump and at the adapters in the valve cover bases.4. a) Remove the old fuel line group.b) On DIT engines only, remove the 6N1671 Bracket from the vee of the engine and install the new brackets. Illustrations 2 and 3 show how the new brackets are installed. The 4P8385 Bracket and 4P8261 Bracket are the 2 main parts of this group. Five 0S1571 Bolts and five 5M2894 Washers attach the assembly to the block. To align the assembly correctly, three 8T1296 Washers are reguired to shim the brackets to the block (see Illustration
The fuel lines on certain 3408 Generator Set, Industrial, and Marine engines may fail. New fuel line groups can be installed that have a longer service life.
Affected Product
Model & Identification Number
3408 (67U12405-15199; 78Z2829-4522; 99U5985-7229)
Parts Needed
1 - 6I0030 Fuel Line Group6 - 5M2894 Washer6 - 0S0509 BoltAdditional Parts Needed For DIT Engines (Non-Aftercooled)
5 - 5M2894 Washer1 - 4P8261 Bracket1 - 4P8385 Bracket2 - 5P0537 Washer5 - 0S1571 Bolt2 - 0S1615 Bolt3 - 8T1296 WasherAction Required
Parts Stock
Make sure that all 7C6931, 7C6932, 7C6933, 7C6934, 7C6935, 7C6936, 7C6937 and 7C6938 Fuel Lines were removed from parts stock while implementing Product Support Program PS4737.
Affected Product
Remove the existing fuel lines and install the new fuel injection line groups as a group. See the attached rework procedure.
Do not over tighten the screws of the metal-to- metal fuel line clamps. Use a 6V6069 Torgue Screwdriver or similar tool to tighten the screw to a torgue of 2.25 N m (20 lb in).
Service Claim Allowances
Parts Stock
Refer to the Product Support Program PS4737.
Affected Product
This is a 2.2-hour job.
Parts Disposition
Handle the parts in accordance with your Warranty Bulletin on warranty parts handling.
Attach. (1-Rework Procedure)Rework Procedure
Refer to the parts list and illustrations. Replace the existing fuel lines and their related parts with the new 6I0030 Fuel Line Group.
To insure that the clamp locations are correct, install fuel line group as assembled. In a case where it is necessary to remove the clamps, mark their locations to insure the correct position when assembling.
1. Clean and paint the new 6I0030 Fuel Line Group before proceeding to the job site.A) Install 5F2807 Plastic Caps and 2F2990 Plastic Plugs on the ends of the lines.B) Clean and paint the fuel line group.C) After drying, do not remove the plastic plugs and caps until the fuel line group is ready to be installed on the engine. Transport the fuel line group in it's original shipping box. If the engine to be reworked is non-aftercooled, also clean and pre-paint the new 4P8385 and 4P8261 Brackets.
2. Remove all the mounting bolts from the fuel line bracket at the aftercooler housing on DITA engines or at the 6N1671 Bracket on DIT engines. The 6N1671 Bracket in the vee of the DIT (non- aftercooled) engines is used to support the fuel line brackets. This bracket is part of the 6N1672 Fastener Group, Affected Product not having an aftercooler required a new two piece bracket.
3. Disconnect all the fuel line nuts at the fuel injection pump and at the adapters in the valve cover bases.4. a) Remove the old fuel line group.b) On DIT engines only, remove the 6N1671 Bracket from the vee of the engine and install the new brackets. Illustrations 2 and 3 show how the new brackets are installed. The 4P8385 Bracket and 4P8261 Bracket are the 2 main parts of this group. Five 0S1571 Bolts and five 5M2894 Washers attach the assembly to the block. To align the assembly correctly, three 8T1296 Washers are reguired to shim the brackets to the block (see Illustration