Information injection-pump assembly
ZEXEL
104741-4422
1047414422
NISSAN
167002S615
167002s615
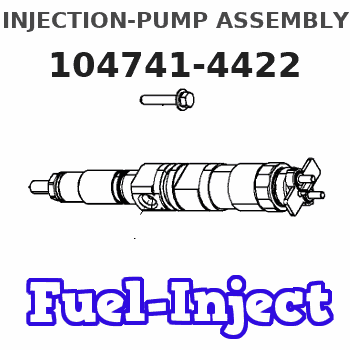
Rating:
Cross reference number
ZEXEL
104741-4422
1047414422
NISSAN
167002S615
167002s615
Zexel num
Bosch num
Firm num
Name
Calibration Data:
Adjustment conditions
Test oil
1404 Test oil ISO4113orSAEJ967d
1404 Test oil ISO4113orSAEJ967d
Test oil temperature
degC
45
45
50
Nozzle
105780-0060
Bosch type code
NP-DN0SD1510
Nozzle holder
105780-2150
Opening pressure
MPa
13
13
13.3
Opening pressure
kgf/cm2
133
133
136
Injection pipe
157805-7320
Injection pipe
Inside diameter - outside diameter - length (mm) mm 2-6-450
Inside diameter - outside diameter - length (mm) mm 2-6-450
Joint assembly
157641-4720
Tube assembly
157641-4020
Transfer pump pressure
kPa
20
20
20
Transfer pump pressure
kgf/cm2
0.2
0.2
0.2
Direction of rotation (viewed from drive side)
Right R
Right R
Injection timing adjustment
Pump speed
r/min
1000
1000
1000
Average injection quantity
mm3/st.
54.8
54.3
55.3
Difference in delivery
mm3/st.
4.5
Basic
*
Oil temperature
degC
50
48
52
Injection timing adjustment_02
Pump speed
r/min
500
500
500
Average injection quantity
mm3/st.
48.2
44.7
51.7
Oil temperature
degC
48
46
50
Injection timing adjustment_03
Pump speed
r/min
800
800
800
Average injection quantity
mm3/st.
54.1
50.6
57.6
Oil temperature
degC
50
48
52
Injection timing adjustment_04
Pump speed
r/min
1000
1000
1000
Average injection quantity
mm3/st.
54.8
53.8
55.8
Difference in delivery
mm3/st.
5
Basic
*
Oil temperature
degC
50
48
52
Injection timing adjustment_05
Pump speed
r/min
1500
1500
1500
Average injection quantity
mm3/st.
55.6
52.6
58.6
Oil temperature
degC
50
48
52
Injection timing adjustment_06
Pump speed
r/min
1800
1800
1800
Average injection quantity
mm3/st.
57.2
54.2
60.2
Oil temperature
degC
50
48
52
Injection quantity adjustment
Pump speed
r/min
2350
2350
2350
Average injection quantity
mm3/st.
17.8
15.8
19.8
Basic
*
Oil temperature
degC
52
50
54
Injection quantity adjustment_02
Pump speed
r/min
2600
2600
2600
Average injection quantity
mm3/st.
5
Oil temperature
degC
55
52
58
Injection quantity adjustment_03
Pump speed
r/min
2350
2350
2350
Average injection quantity
mm3/st.
17.8
15.3
20.3
Basic
*
Oil temperature
degC
52
50
54
Governor adjustment
Pump speed
r/min
375
375
375
Average injection quantity
mm3/st.
12.9
10.9
14.9
Difference in delivery
mm3/st.
2
Basic
*
Oil temperature
degC
48
46
50
Governor adjustment_02
Pump speed
r/min
375
375
375
Average injection quantity
mm3/st.
12.9
10.4
15.4
Difference in delivery
mm3/st.
2.5
Basic
*
Oil temperature
degC
48
46
50
Timer adjustment
Pump speed
r/min
100
100
100
Average injection quantity
mm3/st.
90
75
110
Basic
*
Oil temperature
degC
48
46
50
Remarks
Full
Full
Timer adjustment_02
Pump speed
r/min
100
100
100
Average injection quantity
mm3/st.
90
75
110
Oil temperature
degC
48
46
50
Remarks
Full
Full
Speed control lever angle
Pump speed
r/min
375
375
375
Average injection quantity
mm3/st.
0
0
0
Oil temperature
degC
48
46
50
Remarks
Magnet OFF at idling position
Magnet OFF at idling position
0000000901
Pump speed
r/min
1000
1000
1000
Overflow quantity with S/T ON
cm3/min
500
370
630
Oil temperature
degC
50
48
52
Stop lever angle
Pump speed
r/min
1000
1000
1000
Pressure with S/T ON
kPa
618
579
657
Pressure with S/T ON
kgf/cm2
6.3
5.9
6.7
Pressure with S/T OFF
kPa
539
519
559
Pressure with S/T OFF
kgf/cm2
5.5
5.3
5.7
Basic
*
Oil temperature
degC
50
48
52
Stop lever angle_02
Pump speed
r/min
1000
1000
1000
Pressure with S/T OFF
kPa
539
500
578
Pressure with S/T OFF
kgf/cm2
5.5
5.1
5.9
Basic
*
Oil temperature
degC
50
48
52
Stop lever angle_03
Pump speed
r/min
1800
1800
1800
Pressure with S/T OFF
kPa
736
677
795
Pressure with S/T OFF
kgf/cm2
7.5
6.9
8.1
Oil temperature
degC
50
48
52
0000001101
Pump speed
r/min
1000
1000
1000
Timer stroke with S/T ON
mm
5.1
4.7
5.5
Timer stroke with S/T OFF
mm
3.6
3.4
3.8
Basic
*
Oil temperature
degC
50
48
52
_02
Pump speed
r/min
750
750
750
Timer stroke with S/T OFF
mm
1.7
1.1
2.3
Oil temperature
degC
50
48
52
_03
Pump speed
r/min
1000
1000
1000
Timer stroke with S/T ON
mm
5.1
4.6
5.6
Timer stroke with S/T OFF
mm
3.6
3.3
3.9
Basic
*
Oil temperature
degC
50
48
52
_04
Pump speed
r/min
1800
1800
1800
Timer stroke with S/T OFF
mm
7.5
7
8
Oil temperature
degC
50
48
52
_05
Pump speed
r/min
2100
2100
2100
Timer stroke with S/T OFF
mm
8.2
7.7
8.6
Oil temperature
degC
52
50
54
0000001201
Max. applied voltage
V
8
8
8
Test voltage
V
13
12
14
Timing setting
K dimension
mm
3.3
3.2
3.4
KF dimension
mm
5.62
5.52
5.72
MS dimension
mm
0.9
0.8
1
Pre-stroke
mm
0.1
0.08
0.12
Control lever angle alpha
deg.
55.5
51.5
59.5
Control lever angle beta
deg.
32.5
27.5
37.5
Information:
Installing main bearings(b) Fit the flanged main bearing in the No. 3 journal position.(c) Smear a little engine oil on the inner surface of each bearing.
Installing flanged main bearingInstalling Crankshaft
(a) Wash the crankshaft thoroughly in cleaning solvent, then dry it with compressed air.(b) Keeping the crankshaft horizontal, gently lower it into the cylinder block.(c) Smear a little engine oil on each crankshaft journal.
Installing crankshaftInstalling Main Bearing Caps
(a) Before installing the main bearing caps, apply sealant to the mating surfaces of the frontmost and rearmost caps and to the corresponding surfaces in the cylinder block.
Installing main bearing caps(b) Referring to the cap numbers, fit the main bearing caps sequentially starting at the front of the engine. The arrow on each cap must point toward the front of the engine.
Front marks and cap numbers
Make sure the frontmost and rearmost caps fit flush against the cylinder block.
(4) Tightening Bearing Cap Bolts
Tighten the bearing cap bolts alternately a little at a time, then torque each bolt to specification.
Tightening bearing cap bolts(5) Checking Crankshaft Rotation
Confirm that the crankshaft turns smoothly.
Checking crankshaft rotation(6) Measuring End Plan of Crankshaft
Apply a dial gauge to the end of the crankshaft and measure the end play. If the measurement exceeds the specified limit, replace the No. 3 flanged bearing.
Measuring end play of crankshaft(7) Inserting Side Seals
(a) Apply sealant to the mating surfaces of each side seal. (b) With the radius of each side seal facing the outside, push the side seals part-way into the frontmost and rearmost caps by hand.
Alignment of side seals for installation(c) Press each side seal completely into position using a flat implement. Be careful not to bend the side seals.
Inserting side seals(8) Preparation for Installation of Piston and Connecting Rod Assemblies
(a) Clean each cylinder's inner surface with a rag, then smear each with engine oil.(b) Press the connecting rod bearings (upper and lower) into the connecting rods and caps such that the bearings' lugs fir into the grooves.(c) Smear the connecting rod bearings with engine oil.(d) Turn the cylinder block onto its side.
Preparation for installation of piston and connecting rod assemblies(9) Installing Piston and Connecting Rod Assemblies
(a) Smear the pistons' sliding surfaces and piston rings with engine oil(b) Position the piston ring gaps as shown in the illustration. Do not align any ring gap with the piston pin or at 90° to the piston pin.
Piston ring positions(c) Turn the crankshaft until the crank pin onto which the connecting rod is to be fitted reaches its TDC position.(d) Align the piston such that its front mark (this is stamped on the piston crown) points toward the timing gear case mounting surface (the front of the engine).(e) Using a piston guide (commercially available), insert the piston and connecting rod assembly into the cylinder from the top of the cylinder block.
Inserting piston and connecting rod assembly
If the piston is tapped hard while being inserted, the piston rings may break and the crank pin may become damaged.
(10) Installing Connecting Rod Caps
(a) When the connecting rod's big end is