Information injection-pump assembly
ZEXEL
104741-1910
1047411910
ISUZU
8944752200
8944752200
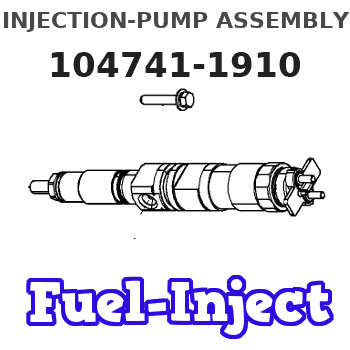
Rating:
Cross reference number
ZEXEL
104741-1910
1047411910
ISUZU
8944752200
8944752200
Zexel num
Bosch num
Firm num
Name
Calibration Data:
Adjustment conditions
Test oil
1404 Test oil ISO4113orSAEJ967d
1404 Test oil ISO4113orSAEJ967d
Test oil temperature
degC
45
45
50
Nozzle
105000-2010
Bosch type code
NP-DN12SD12TT
Nozzle holder
105780-2080
Opening pressure
MPa
14.7
14.7
15.19
Opening pressure
kgf/cm2
150
150
155
Injection pipe
Inside diameter - outside diameter - length (mm) mm 2-6-840
Inside diameter - outside diameter - length (mm) mm 2-6-840
Transfer pump pressure
kPa
20
20
20
Transfer pump pressure
kgf/cm2
0.2
0.2
0.2
Direction of rotation (viewed from drive side)
Left L
Left L
Injection timing adjustment
Pump speed
r/min
1000
1000
1000
Average injection quantity
mm3/st.
40.9
40.4
41.4
Difference in delivery
mm3/st.
3.5
Basic
*
Oil temperature
degC
50
48
52
Injection timing adjustment_02
Pump speed
r/min
500
500
500
Average injection quantity
mm3/st.
30.5
27
34
Oil temperature
degC
48
46
50
Injection timing adjustment_03
Pump speed
r/min
700
700
700
Average injection quantity
mm3/st.
34.2
31.7
36.7
Oil temperature
degC
50
48
52
Injection timing adjustment_04
Pump speed
r/min
1000
1000
1000
Average injection quantity
mm3/st.
40.9
39.9
41.9
Difference in delivery
mm3/st.
3.5
Basic
*
Oil temperature
degC
50
48
52
Injection timing adjustment_05
Pump speed
r/min
1150
1150
1150
Average injection quantity
mm3/st.
44.1
44.1
44.1
Oil temperature
degC
50
48
52
Injection timing adjustment_06
Pump speed
r/min
2000
2000
2000
Average injection quantity
mm3/st.
42.6
42.6
42.6
Oil temperature
degC
50
48
52
Injection timing adjustment_07
Pump speed
r/min
2100
2100
2100
Average injection quantity
mm3/st.
39.9
39.9
39.9
Oil temperature
degC
52
50
54
Injection quantity adjustment
Pump speed
r/min
2400
2400
2400
Average injection quantity
mm3/st.
16
13
19
Difference in delivery
mm3/st.
4.5
Basic
*
Oil temperature
degC
52
50
54
Injection quantity adjustment_02
Pump speed
r/min
2500
2500
2500
Average injection quantity
mm3/st.
12
Oil temperature
degC
55
52
58
Injection quantity adjustment_03
Pump speed
r/min
2400
2400
2400
Average injection quantity
mm3/st.
16
13
19
Difference in delivery
mm3/st.
4.5
Oil temperature
degC
52
50
54
Governor adjustment
Pump speed
r/min
375
375
375
Average injection quantity
mm3/st.
6
4
8
Difference in delivery
mm3/st.
2
Basic
*
Oil temperature
degC
48
46
50
Governor adjustment_02
Pump speed
r/min
375
375
375
Average injection quantity
mm3/st.
6
4
8
Difference in delivery
mm3/st.
2
Oil temperature
degC
48
46
50
Timer adjustment
Pump speed
r/min
100
100
100
Average injection quantity
mm3/st.
60
60
100
Basic
*
Oil temperature
degC
48
46
50
Remarks
Full
Full
Timer adjustment_02
Pump speed
r/min
100
100
100
Average injection quantity
mm3/st.
80
60
100
Oil temperature
degC
48
46
50
Speed control lever angle
Pump speed
r/min
375
375
375
Average injection quantity
mm3/st.
0
0
0
Oil temperature
degC
48
46
50
Remarks
Magnet OFF at idling position
Magnet OFF at idling position
0000000901
Pump speed
r/min
1600
1600
1600
Overflow quantity with S/T OFF
cm3/min
530
400
660
Oil temperature
degC
50
48
52
Remarks
MEASURE
MEASURE
Stop lever angle
Pump speed
r/min
1600
1600
1600
Pressure with S/T OFF
kPa
490
470
510
Pressure with S/T OFF
kgf/cm2
5
4.8
5.2
Basic
*
Oil temperature
degC
50
48
52
Stop lever angle_02
Pump speed
r/min
1600
1600
1600
Pressure with S/T OFF
kPa
490
470
510
Pressure with S/T OFF
kgf/cm2
5
4.8
5.2
Basic
*
Oil temperature
degC
50
48
52
Stop lever angle_03
Pump speed
r/min
2000
2000
2000
Pressure with S/T OFF
kPa
608
579
637
Pressure with S/T OFF
kgf/cm2
6.2
5.9
6.5
Oil temperature
degC
50
48
52
0000001101
Pump speed
r/min
1600
1600
1600
Timer stroke with S/T OFF
mm
5
4.8
5.2
Basic
*
Oil temperature
degC
50
48
52
_02
Pump speed
r/min
670
670
670
Timer stroke with S/T ON
mm
0.5
0.5
Oil temperature
degC
50
48
52
_03
Pump speed
r/min
1020
1020
1020
Timer stroke with S/T OFF
mm
0.5
0.1
0.9
Oil temperature
degC
50
48
52
_04
Pump speed
r/min
1600
1600
1600
Timer stroke with S/T OFF
mm
5
4.8
5.2
Basic
*
Oil temperature
degC
50
48
52
_05
Pump speed
r/min
2000
2000
2000
Timer stroke with S/T OFF
mm
7.8
7.5
8.2
Oil temperature
degC
50
48
52
0000001201
Max. applied voltage
V
8
8
8
Test voltage
V
13
12
14
0000001501
Pump speed
r/min
1000
1000
1000
Height
m
2000
2000
2000
Atmospheric pressure difference
kPa
-21.9
-22.6
-21.2
Atmospheric pressure difference
mmHg
-164
-169
-159
Average injection quantity
mm3/st.
33.5
33.5
33.5
Decrease qty
mm3/st.
7.4
6.4
8.4
Decrease rate
%
18
15
21
Basic
*
Oil temperature
degC
50
48
52
_02
Pump speed
r/min
1000
1000
1000
Height
m
0
0
0
Atmospheric pressure difference
kPa
0
0
0
Atmospheric pressure difference
mmHg
0
0
0
Decrease qty
mm3/st.
0
0
0
Decrease rate
%
0
0
0
Oil temperature
degC
50
48
52
_03
Pump speed
r/min
1000
1000
1000
Height
m
500
500
500
Atmospheric pressure difference
kPa
-5.9
-9.2
-2.6
Atmospheric pressure difference
mmHg
-44
-69
-19
Oil temperature
degC
50
48
52
Remarks
Point of inflection
Point of inflection
_04
Pump speed
r/min
1000
1000
1000
Height
m
2000
2000
2000
Atmospheric pressure difference
kPa
-21.9
-22.6
-21.2
Atmospheric pressure difference
mmHg
-164
-169
-159
Decrease qty
mm3/st.
7.4
6.4
8.4
Decrease rate
%
18
15
21
Oil temperature
degC
50
48
52
Timing setting
K dimension
mm
2.8
2.7
2.9
KF dimension
mm
5.5
5.4
5.6
MS dimension
mm
1
0.9
1.1
Pre-stroke
mm
0.45
0.43
0.47
Control lever angle alpha
deg.
18
14
22
Control lever angle beta
deg.
37
32
42
Test data Ex:
0000001801 V-FICD ADJUSTMENT
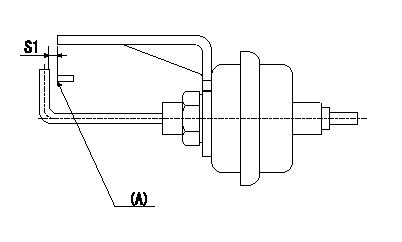
Adjustment of the V-FICD
1. Adjust the actuator rod to obtain S1.
2. Apply negative pressure P1 to the actuator and confirm the full stroke.
(A) Control lever (Idling position)
----------
S1=1+1mm P1=-53.3kPa(-400mmHg)
----------
S1=1+1mm
----------
S1=1+1mm P1=-53.3kPa(-400mmHg)
----------
S1=1+1mm
Information:
Introduction
The problem that is identified below does not have a known permanent solution. Until a permanent solution is known, use the solution that is identified below.Problem
If the engine is stored for 6 months or more, the fuel injection pump linkage needs to be lubricated.Solution
Follow the procedure in this article to lubricate the fuel injection pump linkage.
Remove the fuel shutoff solenoid. Refer to Disassembly and Assembly, "Fuel Shutoff Solenoid - Remove and Install" for the correct procedure.
Spray the fuel control rack with a suitable lubricant spray.
Use a suitable magnet to operate the fuel control rack. The operation of the fuel control rack will disperse the lubricant.Note: If the fuel control rack does not move freely, then the fuel injection pump should be replaced. Refer to Disassembly and Assembly, "Fuel Injection Pump - Remove and Install" for the correct procedure.
Install the fuel shutoff solenoid. Refer to Disassembly and Assembly, "Fuel Shutoff Solenoid - Remove and Install" for the correct procedure.
Record the repair in the Service Information Management System (SIMSi), including the engine/machine serial number and the date of the repair.
The problem that is identified below does not have a known permanent solution. Until a permanent solution is known, use the solution that is identified below.Problem
If the engine is stored for 6 months or more, the fuel injection pump linkage needs to be lubricated.Solution
Follow the procedure in this article to lubricate the fuel injection pump linkage.
Remove the fuel shutoff solenoid. Refer to Disassembly and Assembly, "Fuel Shutoff Solenoid - Remove and Install" for the correct procedure.
Spray the fuel control rack with a suitable lubricant spray.
Use a suitable magnet to operate the fuel control rack. The operation of the fuel control rack will disperse the lubricant.Note: If the fuel control rack does not move freely, then the fuel injection pump should be replaced. Refer to Disassembly and Assembly, "Fuel Injection Pump - Remove and Install" for the correct procedure.
Install the fuel shutoff solenoid. Refer to Disassembly and Assembly, "Fuel Shutoff Solenoid - Remove and Install" for the correct procedure.
Record the repair in the Service Information Management System (SIMSi), including the engine/machine serial number and the date of the repair.