Information injection-pump assembly
ZEXEL
104741-1082
1047411082
ISUZU
8941397411
8941397411
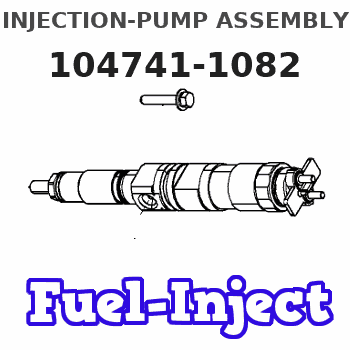
Rating:
Cross reference number
ZEXEL
104741-1082
1047411082
ISUZU
8941397411
8941397411
Zexel num
Bosch num
Firm num
Name
Calibration Data:
Adjustment conditions
Test oil
1404 Test oil ISO4113orSAEJ967d
1404 Test oil ISO4113orSAEJ967d
Test oil temperature
degC
45
45
50
Nozzle
105000-2010
Bosch type code
NP-DN12SD12TT
Nozzle holder
105780-2080
Opening pressure
MPa
14.7
14.7
15.19
Opening pressure
kgf/cm2
150
150
155
Injection pipe
Inside diameter - outside diameter - length (mm) mm 2-6-840
Inside diameter - outside diameter - length (mm) mm 2-6-840
Transfer pump pressure
kPa
20
20
20
Transfer pump pressure
kgf/cm2
0.2
0.2
0.2
Direction of rotation (viewed from drive side)
Left L
Left L
(Solenoid timer adjustment condition)
OFF
Injection timing adjustment
Pump speed
r/min
1000
1000
1000
Average injection quantity
mm3/st.
39.5
39
40
Difference in delivery
mm3/st.
3
Basic
*
Injection timing adjustment_02
Pump speed
r/min
2100
2100
2100
Average injection quantity
mm3/st.
16.1
12.6
19.6
Injection timing adjustment_03
Pump speed
r/min
2000
2000
2000
Average injection quantity
mm3/st.
32.7
28.2
37.2
Injection timing adjustment_04
Pump speed
r/min
1800
1800
1800
Average injection quantity
mm3/st.
38.9
35.9
41.9
Injection timing adjustment_05
Pump speed
r/min
1350
1350
1350
Average injection quantity
mm3/st.
42.2
39.2
45.2
Injection timing adjustment_06
Pump speed
r/min
1000
1000
1000
Average injection quantity
mm3/st.
39.5
38.5
40.5
Injection timing adjustment_07
Pump speed
r/min
700
700
700
Average injection quantity
mm3/st.
35.1
32.6
37.6
Injection timing adjustment_08
Pump speed
r/min
500
500
500
Average injection quantity
mm3/st.
36.1
32.1
40.1
Injection quantity adjustment
Pump speed
r/min
2100
2100
2100
Average injection quantity
mm3/st.
16.1
13.1
19.1
Difference in delivery
mm3/st.
4.5
Basic
*
Injection quantity adjustment_02
Pump speed
r/min
2300
2300
2300
Average injection quantity
mm3/st.
5
Governor adjustment
Pump speed
r/min
390
390
390
Average injection quantity
mm3/st.
7.5
5.5
9.5
Difference in delivery
mm3/st.
2
Basic
*
Governor adjustment_02
Pump speed
r/min
390
390
390
Average injection quantity
mm3/st.
7.5
5.5
9.5
Governor adjustment_03
Pump speed
r/min
550
550
550
Average injection quantity
mm3/st.
3
Timer adjustment
Pump speed
r/min
100
100
100
Average injection quantity
mm3/st.
90
75
105
Basic
*
Speed control lever angle
Pump speed
r/min
390
390
390
Average injection quantity
mm3/st.
0
0
0
Remarks
Magnet OFF
Magnet OFF
0000000901
Pump speed
r/min
1500
1500
1500
Overflow quantity
cm3/min
519
390
648
Stop lever angle
Pump speed
r/min
1500
1500
1500
Pressure
kPa
519.5
500
539
Pressure
kgf/cm2
5.3
5.1
5.5
Basic
*
Stop lever angle_02
Pump speed
r/min
1000
1000
1000
Pressure
kPa
323.5
294
353
Pressure
kgf/cm2
3.3
3
3.6
Stop lever angle_03
Pump speed
r/min
1500
1500
1500
Pressure
kPa
519.5
500
539
Pressure
kgf/cm2
5.3
5.1
5.5
Stop lever angle_04
Pump speed
r/min
1950
1950
1950
Pressure
kPa
666.5
637
696
Pressure
kgf/cm2
6.8
6.5
7.1
0000001101
Pump speed
r/min
1500
1500
1500
Timer stroke
mm
2.3
2.1
2.5
Basic
*
_02
Pump speed
r/min
550
450
650
Timer stroke with S/T ON
mm
0.5
0.5
0.5
_03
Pump speed
r/min
1250
1200
1300
Timer stroke with S/T OFF
mm
0.5
0.5
0.5
_04
Pump speed
r/min
1500
1500
1500
Timer stroke with S/T OFF
mm
2.3
2
2.6
_05
Pump speed
r/min
1950
1950
1950
Timer stroke with S/T OFF
mm
5.7
5.3
6.1
0000001201
Max. applied voltage
V
8
8
8
Test voltage
V
13
12
14
Timing setting
K dimension
mm
2.8
2.7
2.9
KF dimension
mm
5
4.9
5.1
MS dimension
mm
1
0.9
1.1
Pre-stroke
mm
0.45
0.43
0.47
Control lever angle alpha
deg.
18
14
22
Control lever angle beta
deg.
37
32
42
Information:
Illustration 4 g06005614
(A) Hydraulic tank drain
Drain the hydraulic tank. Refer to Illustration 4.Note: After draining, if a significant number of metal particles are visible in the tank, contact BCP STTT support through the DSN for guidance before proceeding further.
Drain the hydraulic cylinders.
Disconnect and drain the lines at all cylinders.
Retract and extend the cylinder rods to evacuate cylinders.
Illustration 5 g06005620
(B) Inlet lines
(C) Outlet lines
Drain the hydraulic oil cooler. Refer to Illustration 5.
Remove inlet and outlet lines at cooler.
Drain the cooler and the lines.Note: Ensure that the cooler has been drained.
Illustration 6 g06005623
(D) Case plug
Drain the hystat pumps. Refer to Illustration 6.
Remove case plug (D) on the rear right side of the pump.
Drain pumps and suction remaining oil from pump housing.Note: Ensure that the pump case has been drained.
Illustration 7 g06005628
(E) Parking brake lines
Drain the parking brake lines. Refer to Illustration 7.
Disconnect and drain the parking brake line (E) at the bottom of the pumps.
Disconnect and drain the right-hand brake line (E) connection.
Illustration 8 g06005631
(F) Case drain lines and hystat motors
Drain the drive motors. Refer to Illustration 8.
Disconnect the case drain lines at the hystat motors.Note: Ensure that the motor cases have been drained.
Illustration 9 g06005637
Standard Machine
(G) Hydraulic filter
Illustration 10 g06005640
Winch Machine
(G) Hydraulic filter
(H) Winch hydraulic filter
Drain the hydraulic filters. Refer to Illustrations 9 and 10.
Replace the standard and winch (if equipped) filters with each drain cycle.
Check filters for metal particles.
Refill the hydraulic system, repeat Steps 2 through 8, running and warming the hydraulic oil between drain, fill, and filter change cycles. Cycle all cylinders and travel circuits after every fill cycle to achieve full circulation throughout the hydraulic and power train systems with the new oil. Perform SOS check after each run cycle and follow standard SOS guidelines, specifically checking for DEF.Note: Typically takes 5 to 6 drain/refill cycles to clean the hydraulic system and get a clean SOS sample. Clean oil will be red and transparent or clear / light yellow and transparent. If there is any milky appearance to the color, repeat Steps 2 through 9.
Confirm that charge pressure can be set and maintained to specification, especially at pump stall.
Recalibrate the hystat pumps and drive motors, ensuring that calibration is successfully completed. Confirm that the hystat pump pressure can be adjusted to the correct specificationNote: Refer to Testing and Adjusting, UENR4089, "D3K2, D4K2, and D5K2 Track-Type Tractor Systems" for the correct procedure and specification.
Illustration 11 g06005642
(1) 484-5902 Diesel Exhaust Fluid (DEF) film(U.S.)(Shown)
(1A) 393-2614 Diesel Exhaust Fluid (DEF) film(International)
(2) 484-5903 Hydraulic oil film
(3) 430-3036 Diesel Exhaust Fluid (DEF) Gauge (Inst) film(Inside Door)
Illustration 12 g06237577
(1) 484-5902 Diesel Exhaust Fluid (DEF) film
(1A) 393-2614 Diesel Exhaust Fluid (DEF) film (International)
(2) 484-5903 Hydraulic oil film
Illustration 13 g06166475
(3) 430-3036 Diesel Exhaust Fluid (DEF) Gauge (Inst) film
New extra DEF (1), hydraulic oil (2), and DEF gauge instruction (3) films will be used in production. Refer to Table 2 for the affected machines that require the new films. For the film locations, refer to Illustrations 11, 12, and 13.Note: Adding these stickers to reduce chances of a recurrence of this issue is recommended.Note: Refer