Information injection-pump assembly
ZEXEL
104741-1061
1047411061
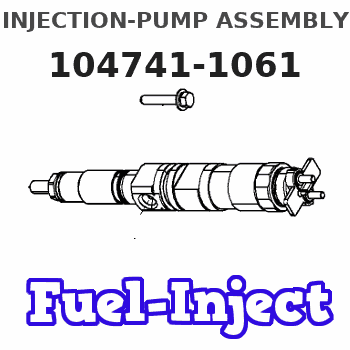
Rating:
Cross reference number
ZEXEL
104741-1061
1047411061
Zexel num
Bosch num
Firm num
Name
Calibration Data:
Adjustment conditions
Test oil
1404 Test oil ISO4113orSAEJ967d
1404 Test oil ISO4113orSAEJ967d
Test oil temperature
degC
45
45
50
Nozzle
105000-2010
Bosch type code
NP-DN12SD12TT
Nozzle holder
105780-2080
Opening pressure
MPa
14.7
14.7
15.19
Opening pressure
kgf/cm2
150
150
155
Injection pipe
Inside diameter - outside diameter - length (mm) mm 2-6-840
Inside diameter - outside diameter - length (mm) mm 2-6-840
Transfer pump pressure
kPa
20
20
20
Transfer pump pressure
kgf/cm2
0.2
0.2
0.2
Direction of rotation (viewed from drive side)
Left L
Left L
Injection timing adjustment
Pump speed
r/min
1000
1000
1000
Average injection quantity
mm3/st.
47.2
46.7
47.7
Difference in delivery
mm3/st.
4
Basic
*
Oil temperature
degC
50
48
52
Injection timing adjustment_02
Pump speed
r/min
500
500
500
Average injection quantity
mm3/st.
41.1
37.6
44.6
Difference in delivery
mm3/st.
5
Oil temperature
degC
48
46
50
Injection timing adjustment_03
Pump speed
r/min
700
700
700
Average injection quantity
mm3/st.
42.1
40.1
44.1
Difference in delivery
mm3/st.
5
Oil temperature
degC
50
48
52
Injection timing adjustment_04
Pump speed
r/min
1000
1000
1000
Average injection quantity
mm3/st.
47.2
46.2
48.2
Difference in delivery
mm3/st.
4
Basic
*
Oil temperature
degC
50
48
52
Injection timing adjustment_05
Pump speed
r/min
1450
1450
1450
Average injection quantity
mm3/st.
48.1
46.1
50.1
Difference in delivery
mm3/st.
6
Oil temperature
degC
50
48
52
Injection timing adjustment_06
Pump speed
r/min
1800
1800
1800
Average injection quantity
mm3/st.
47.1
44.6
49.6
Difference in delivery
mm3/st.
5.5
Oil temperature
degC
50
48
52
Injection quantity adjustment
Pump speed
r/min
2100
2100
2100
Average injection quantity
mm3/st.
13
10
16
Difference in delivery
mm3/st.
4
Basic
*
Oil temperature
degC
52
50
54
Injection quantity adjustment_02
Pump speed
r/min
2300
2300
2300
Average injection quantity
mm3/st.
5
Oil temperature
degC
52
50
54
Injection quantity adjustment_03
Pump speed
r/min
2100
2100
2100
Average injection quantity
mm3/st.
13
10
16
Difference in delivery
mm3/st.
4
Oil temperature
degC
52
50
54
Governor adjustment
Pump speed
r/min
390
390
390
Average injection quantity
mm3/st.
8
6
10
Difference in delivery
mm3/st.
2
Basic
*
Oil temperature
degC
48
46
50
Governor adjustment_02
Pump speed
r/min
390
390
390
Average injection quantity
mm3/st.
8
6
10
Difference in delivery
mm3/st.
2
Oil temperature
degC
48
46
50
Timer adjustment
Pump speed
r/min
100
100
100
Average injection quantity
mm3/st.
95
75
115
Basic
*
Oil temperature
degC
48
46
50
Remarks
Full
Full
Timer adjustment_02
Pump speed
r/min
100
100
100
Average injection quantity
mm3/st.
95
75
115
Oil temperature
degC
48
46
50
Speed control lever angle
Pump speed
r/min
390
390
390
Average injection quantity
mm3/st.
0
0
0
Oil temperature
degC
48
46
50
Remarks
Magnet OFF at idling position
Magnet OFF at idling position
0000000901
Pump speed
r/min
1500
1500
1500
Overflow quantity
cm3/min
530
400
660
Oil temperature
degC
50
48
52
Stop lever angle
Pump speed
r/min
1500
1500
1500
Pressure with S/T OFF
kPa
510
490
530
Pressure with S/T OFF
kgf/cm2
5.2
5
5.4
Basic
*
Oil temperature
degC
50
48
52
Remarks
OFF
OFF
Stop lever angle_02
Pump speed
r/min
1500
1500
1500
Pressure with S/T OFF
kPa
510
490
530
Pressure with S/T OFF
kgf/cm2
5.2
5
5.4
Basic
*
Oil temperature
degC
50
48
52
0000001101
Pump speed
r/min
1500
1500
1500
Timer stroke with S/T OFF
mm
2.3
2.1
2.5
Basic
*
Oil temperature
degC
50
48
52
Remarks
OFF
OFF
_02
Pump speed
r/min
600
500
700
Timer stroke with S/T ON
mm
0.5
0.5
0.5
Oil temperature
degC
50
48
52
_03
Pump speed
r/min
1270
1220
1320
Timer stroke with S/T OFF
mm
0.5
0.5
0.5
Oil temperature
degC
50
48
52
_04
Pump speed
r/min
1500
1500
1500
Timer stroke with S/T OFF
mm
2.3
2.1
2.5
Basic
*
Oil temperature
degC
50
48
52
_05
Pump speed
r/min
1950
1950
1950
Timer stroke with S/T OFF
mm
5.7
5.4
6.1
Oil temperature
degC
50
48
52
0000001201
Max. applied voltage
V
8
8
8
Test voltage
V
13
12
14
Timing setting
K dimension
mm
2.8
2.7
2.9
KF dimension
mm
5
4.9
5.1
MS dimension
mm
1
0.9
1.1
Pre-stroke
mm
0.45
0.43
0.47
Control lever angle alpha
deg.
18
14
22
Control lever angle beta
deg.
35
30
40
Information:
When using Cat ELC, do not use conventional SCAs, or, if equipped, SCA maintenance elements. In order to avoid SCA contamination of an ELC system, remove the SCA element base and plug off or bypass the coolant lines.
Cat ELC Cooling System Cleaning
Note: If the cooling system is already using Cat ELC, cleaning agents are not required at the specified coolant change interval. Cleaning agents are only required if the system has been contaminated by the addition of some other type of coolant or by cooling system damage.Clean water is the only cleaning agent that is required when Cat ELC is drained from a properly maintained cooling system.After the cooling system is drained and then refilled, operate the engine while the cooling system filler cap is removed. Operate the engine until the coolant level reaches the normal operating temperature and until the coolant level stabilizes. As needed, add the coolant mixture in order to fill the system to the proper level.Recycling Cat ELC
Cat ELC can be recycled into conventional coolants. The drained coolant mixture can be distilled in order to remove the ethylene glycol and the water. The ethylene glycol and the water can be reused. The distilled material does not contain the additives that are required as either Cat ELC or Cat DEAC. Consult your Cat dealer for more information. Recycled coolants should meet the most current revision level of "ASTM D6210".Changing to Cat ELC
To change from heavy-duty coolant/antifreeze to the Cat ELC, perform the following steps:
Care must be taken to ensure that fluids are contained during performance of inspection, maintenance, testing, adjusting and repair of the product. Be prepared to collect the fluid with suitable containers before opening any compartment or disassembling any component containing fluids.Refer to Special Publication, NENG2500, "Caterpillar Dealer Service Tool Catalog" and to Special Publication, PECJ0003, "Cat Shop Supplies and Tools" for tools and supplies suitable to collect and contain fluids on Cat products.Dispose of all fluids according to applicable regulations and mandates.
Drain the coolant into a suitable container.
Dispose of the coolant according to local regulations.
If equipped, remove the empty SCA maintenance element and remove the element base. Plug the coolant lines or bypass the coolant lines.
Do not leave an empty SCA maintenance element on a system that is filled with Cat ELC.The element housing may corrode and leak causing an engine failure.Remove the SCA element base and plug off or by-pass the coolant lines.
Flush the system with clean water in order to remove any debris.
Use Cat Quick Flush Cooling System Cleaner for cooling systems in order to clean the system. Cat Quick Flush Cooling System Cleaner is available in various sizes. Part numbers are 4C-4609 ( 0.5 L (0.125 US gal)) through 4C-4613 ( 208.2 L (55 US gal)). Follow the instructions on the label using a 6-10% concentration of cleaner in water.
Drain the cleaner into a suitable container. Flush the cooling system with clean water. Note: Deposits that remain in the system may be loosened and removed by the Cat ELC.
In