Information injection-pump assembly
ZEXEL
104741-1001
1047411001
ISUZU
8941337571
8941337571
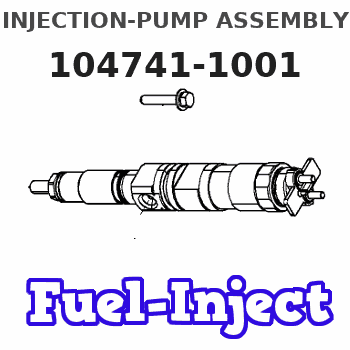
Rating:
Cross reference number
ZEXEL
104741-1001
1047411001
ISUZU
8941337571
8941337571
Zexel num
Bosch num
Firm num
Name
Calibration Data:
Adjustment conditions
Test oil
1404 Test oil ISO4113orSAEJ967d
1404 Test oil ISO4113orSAEJ967d
Test oil temperature
degC
45
45
50
Nozzle
105000-2010
Bosch type code
NP-DN12SD12TT
Nozzle holder
105780-2080
Opening pressure
MPa
14.7
14.7
15.19
Opening pressure
kgf/cm2
150
150
155
Injection pipe
Inside diameter - outside diameter - length (mm) mm 2-6-840
Inside diameter - outside diameter - length (mm) mm 2-6-840
Transfer pump pressure
kPa
20
20
20
Transfer pump pressure
kgf/cm2
0.2
0.2
0.2
Direction of rotation (viewed from drive side)
Right R
Right R
(Solenoid timer adjustment condition)
OFF OFF
OFF OFF
Timer measuring device installation position
Low pressure side LOW PRESSURE SIDE
Low pressure side LOW PRESSURE SIDE
Injection timing adjustment
Pump speed
r/min
1000
1000
1000
Average injection quantity
mm3/st.
47.5
47
48
Difference in delivery
mm3/st.
4
Basic
*
Injection timing adjustment_02
Pump speed
r/min
2100
2100
2100
Average injection quantity
mm3/st.
13.1
9.6
16.6
Injection timing adjustment_03
Pump speed
r/min
1800
1800
1800
Average injection quantity
mm3/st.
47.4
44.9
49.9
Injection timing adjustment_04
Pump speed
r/min
1450
1450
1450
Average injection quantity
mm3/st.
48.4
46.4
50.4
Injection timing adjustment_05
Pump speed
r/min
1000
1000
1000
Average injection quantity
mm3/st.
47.5
46.5
48.5
Injection timing adjustment_06
Pump speed
r/min
700
700
700
Average injection quantity
mm3/st.
42.35
40.3
44.4
Injection quantity adjustment
Pump speed
r/min
2100
2100
2100
Average injection quantity
mm3/st.
13.1
10.1
16.1
Difference in delivery
mm3/st.
4
Basic
*
Injection quantity adjustment_02
Pump speed
r/min
2300
2300
2300
Average injection quantity
mm3/st.
5
Governor adjustment
Pump speed
r/min
390
390
390
Average injection quantity
mm3/st.
8
6
10
Difference in delivery
mm3/st.
2
Basic
*
Governor adjustment_02
Pump speed
r/min
390
390
390
Average injection quantity
mm3/st.
8
6
10
Governor adjustment_03
Pump speed
r/min
550
550
550
Average injection quantity
mm3/st.
3
Timer adjustment
Pump speed
r/min
100
100
100
Average injection quantity
mm3/st.
95
75
115
Basic
*
Speed control lever angle
Pump speed
r/min
390
390
390
Average injection quantity
mm3/st.
0
0
0
Remarks
Magnet OFF
Magnet OFF
0000000901
Pump speed
r/min
1600
1600
1600
Overflow quantity with S/T OFF
cm3/min
531
402
660
Remarks
OFF
OFF
Stop lever angle
Pump speed
r/min
1600
1600
1600
Pressure
kPa
539.5
520
559
Pressure
kgf/cm2
5.5
5.3
5.7
Basic
*
Stop lever angle_02
Pump speed
r/min
1000
1000
1000
Pressure
kPa
313.5
284
343
Pressure
kgf/cm2
3.2
2.9
3.5
Stop lever angle_03
Pump speed
r/min
1600
1600
1600
Pressure
kPa
539.5
520
559
Pressure
kgf/cm2
5.5
5.3
5.7
Stop lever angle_04
Pump speed
r/min
1900
1900
1900
Pressure
kPa
627.5
598
657
Pressure
kgf/cm2
6.4
6.1
6.7
0000001101
Pump speed
r/min
1600
1600
1600
Timer stroke
mm
1.9
1.7
2.1
Basic
*
_02
Pump speed
r/min
790
690
890
Timer stroke with S/T ON
mm
0.5
0.5
0.5
_03
Pump speed
r/min
1490
1440
1540
Timer stroke with S/T OFF
mm
0.5
0.5
0.5
_04
Pump speed
r/min
1600
1600
1600
Timer stroke with S/T OFF
mm
1.9
1.6
2.2
_05
Pump speed
r/min
1900
1900
1900
Timer stroke with S/T OFF
mm
5.7
5.3
6.1
0000001201
Max. applied voltage
V
8
8
8
Test voltage
V
13
12
14
Timing setting
K dimension
mm
2.8
2.7
2.9
KF dimension
mm
5
4.9
5.1
MS dimension
mm
1
0.9
1.1
Pre-stroke
mm
0.45
0.43
0.47
Control lever angle alpha
deg.
18
14
22
Control lever angle beta
deg.
35
30
40
Information:
Care must be taken to ensure that fluids are contained during performance of inspection, maintenance, testing, adjusting and repair of the product. Be prepared to collect the fluid with suitable containers before opening any compartment or disassembling any component containing fluids.Refer to Special Publication, NENG2500, "Caterpillar Tools and Shop Products Guide" for tools and supplies suitable to collect and contain fluids on Caterpillar products.Dispose of all fluids according to local regulations and mandates.
Remove any coolant lines that may interfere with the installation. Remove any air inlet lines that may interfere with the installation.
Illustration 1 g01006397
Typical example (1) Bolt (2) Washer (3) Air inlet cover
Remove bolt (1) and the washer (2) from the air inlet cover (3). Discard the bolt (1) and the washer (2) .
Disconnect the electrical connector of the injection actuation pressure control valve (7). Remove the injection actuation pressure control valve (7) from the pump. Retain the injection actuation pressure control valve (7) for the reinstallation.Note: Modifications to the tools may need to be made in order to reduce interference with engine components.
Illustration 2 g01007381
Modified 2P-5494 crowfoot wrench
Remove the hose assembly (5), the connector (8), and the elbow (6). Discard these parts.
Illustration 3 g01006381
(4) HEUI pump (5) Flexible oil line (6) Elbow (7) Injection actuation pressure control valve (8) ConnectorInstallation of the 240-0716 Tube Kit
Illustration 4 g01006407
(4) HEUI pump (7) Injection actuation pressure control valve (9) Connector (10) Clip (11) Washer (12) Bolt (13) Spacer (14) Tube assembly (15) O-ring (16) O-ring (17) Elbow
Illustration 5 g01006437
(7) Injection actuation pressure control valve (9) Connector (15) O-ring (16) O-ring (17) Elbow
Apply a light coat of oil to the O-rings (15) and (16) during installation. Install the O-ring (15) on the connector (9). Install the O-ring (16) on the connector (9). Thread the connector (9) into the port on the cylinder head by hand. Tighten to 48 + 5 N m (35 + 4 lb ft).
Apply a light coat of oil to the O-rings (15) and (16) during installation. Install the O-ring (15) on the elbow (17). Install the O-ring (16) on the elbow (17).
Back off the jam nut on the elbow (17) to the top of the threads on the elbow assembly (17). Push the washer tightly against the jam nut. Check that the washer is as tight as possible. Thread the elbow assembly (17) into the port of the HEUI pump (4). Hand tighten the elbow (17) into the port of the HEUI pump until the washer is tight against the HEUI pump (4). Unscrew the elbow assembly (17) no more than one complete turn to 40 degrees.
Align the tube assembly (14) with the connector (9) and the elbow (17). Loosely thread each end of the tube assembly (14) onto the connector (9) and the elbow (17). Position the elbow (17) in order to not create stress in the tube assembly (14) .
Attach the clip (10) to the tube assembly (14). The flat side of the clip (10) must be toward the air inlet cover. Place the washer (11) onto the bolt