Information injection-pump assembly
ZEXEL
104740-9740
1047409740
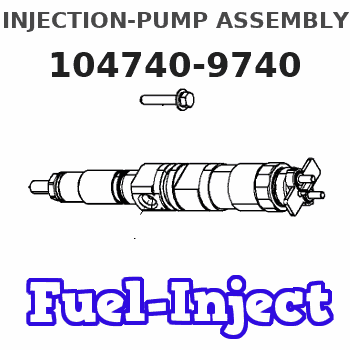
Rating:
Cross reference number
ZEXEL
104740-9740
1047409740
Zexel num
Bosch num
Firm num
Name
Calibration Data:
Adjustment conditions
Test oil
1404 Test oil ISO4113orSAEJ967d
1404 Test oil ISO4113orSAEJ967d
Test oil temperature
degC
45
45
50
Nozzle
105000-2010
Bosch type code
NP-DN12SD12TT
Nozzle holder
105780-2080
Opening pressure
MPa
14.7
14.7
15.19
Opening pressure
kgf/cm2
150
150
155
Injection pipe
Inside diameter - outside diameter - length (mm) mm 2-6-840
Inside diameter - outside diameter - length (mm) mm 2-6-840
Transfer pump pressure
kPa
20
20
20
Transfer pump pressure
kgf/cm2
0.2
0.2
0.2
Direction of rotation (viewed from drive side)
Right R
Right R
Injection timing adjustment
Pump speed
r/min
1100
1100
1100
Average injection quantity
mm3/st.
43.3
42.8
43.8
Difference in delivery
mm3/st.
3
Basic
*
Oil temperature
degC
50
48
52
Injection timing adjustment_02
Pump speed
r/min
600
600
600
Average injection quantity
mm3/st.
41.8
39.8
43.8
Oil temperature
degC
50
48
52
Injection timing adjustment_03
Pump speed
r/min
1100
1100
1100
Average injection quantity
mm3/st.
43.3
42.3
44.3
Difference in delivery
mm3/st.
3.5
Basic
*
Oil temperature
degC
50
48
52
Injection timing adjustment_04
Pump speed
r/min
2150
2150
2150
Average injection quantity
mm3/st.
36.8
34.7
38.9
Oil temperature
degC
52
50
54
Injection quantity adjustment
Pump speed
r/min
2500
2500
2500
Average injection quantity
mm3/st.
8.8
6.8
10.8
Basic
*
Oil temperature
degC
55
52
58
Injection quantity adjustment_02
Pump speed
r/min
2700
2700
2700
Average injection quantity
mm3/st.
5
Oil temperature
degC
55
52
58
Injection quantity adjustment_03
Pump speed
r/min
2500
2500
2500
Average injection quantity
mm3/st.
8.8
5.3
12.3
Basic
*
Oil temperature
degC
55
52
58
Governor adjustment
Pump speed
r/min
350
350
350
Average injection quantity
mm3/st.
6.5
4.5
8.5
Difference in delivery
mm3/st.
2
Basic
*
Oil temperature
degC
48
46
50
Governor adjustment_02
Pump speed
r/min
350
350
350
Average injection quantity
mm3/st.
6.5
4
9
Difference in delivery
mm3/st.
2.5
Basic
*
Oil temperature
degC
48
46
50
Timer adjustment
Pump speed
r/min
100
100
100
Average injection quantity
mm3/st.
53
48
58
Basic
*
Oil temperature
degC
48
46
50
Remarks
Full
Full
Timer adjustment_02
Pump speed
r/min
100
100
100
Average injection quantity
mm3/st.
53
47
59
Oil temperature
degC
48
46
50
Speed control lever angle
Pump speed
r/min
350
350
350
Average injection quantity
mm3/st.
0
0
0
Oil temperature
degC
48
46
50
Remarks
Magnet OFF at idling position
Magnet OFF at idling position
0000000901
Pump speed
r/min
1100
1100
1100
Overflow quantity
cm3/min
390
260
520
Oil temperature
degC
50
48
52
Stop lever angle
Pump speed
r/min
1700
1700
1700
Pressure
kPa
579
550
608
Pressure
kgf/cm2
5.9
5.6
6.2
Basic
*
Oil temperature
degC
50
48
52
Stop lever angle_02
Pump speed
r/min
1700
1700
1700
Pressure
kPa
579
540
618
Pressure
kgf/cm2
5.9
5.5
6.3
Basic
*
Oil temperature
degC
50
48
52
Stop lever angle_03
Pump speed
r/min
2150
2150
2150
Pressure
kPa
677
638
716
Pressure
kgf/cm2
6.9
6.5
7.3
Oil temperature
degC
52
50
54
0000001101
Pump speed
r/min
1700
1700
1700
Timer stroke
mm
4.6
4.4
4.8
Basic
*
Oil temperature
degC
50
48
52
_02
Pump speed
r/min
700
700
700
Timer stroke
mm
0.5
0.5
Oil temperature
degC
50
48
52
_03
Pump speed
r/min
1100
1100
1100
Timer stroke
mm
2.5
1.9
3.1
Oil temperature
degC
50
48
52
_04
Pump speed
r/min
1700
1700
1700
Timer stroke
mm
4.6
4.2
5
Basic
*
Oil temperature
degC
50
48
52
_05
Pump speed
r/min
2500
2500
2500
Timer stroke
mm
7
6.5
7.4
Oil temperature
degC
55
52
58
0000001201
Max. applied voltage
V
8
8
8
Test voltage
V
13
12
14
Timing setting
K dimension
mm
3.3
3.2
3.4
KF dimension
mm
5.75
5.65
5.85
MS dimension
mm
1
0.9
1.1
Control lever angle alpha
deg.
25
23
27
Control lever angle beta
deg.
36
31
41
Test data Ex:
0000001801 STOP LEVER ADJUSTMENT
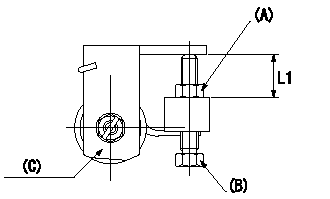
Adjustment of the stop lever
Adjust adjusting bolt (B) so that the starting injection quantity is within the standard. Fix using nut (A)
(A) Adjusting nut
(B) Adjusting bolt
(C) Starting injection quantity adjusting lever
----------
----------
L1=15.0~18.5mm
----------
----------
L1=15.0~18.5mm
Information:
Table 1
Required Tools    
Tool     Part Number     Part Description     Qty    
A     380-5200     Tool Kit     1    
B     366-7782     Attenuator     1    Testing Procedure
Perform a "Manual Diesel Particulate Filter Regeneration" using the electronic service tool. If the "Manual Diesel Particulate Filter Regeneration" procedure follows the removal of excess oil from the exhaust system, proceed to Step 2.
Follow the procedure that is detailed by Step 1.b through to Step 1.m to clean oil from the exhaust system.
Remove excess oil from all pipes with a clean cloth.
Remove the DPF from the bracket for the clean emission module. Refer to Disassembly and Assembly, "Diesel Particulate Filter - Remove" for the correct procedure.
Use a suitable supporting device, position the DPF in a vertical position. Ensure that the inlet side of the DPF faces in a DOWNWARDS position.
Let the DPF drain overnight. The oil will collect inside the inlet face of the DPF. Position a suitable container under the inlet face of the DPF. Incline the inlet face of the DPF to drain the oil into the container.
If amount drained from DPF equals less than 1 L (0.26 US gal), proceed to Step 1.g. If amount is greater than 1 L (0.26 US gal), then the DPF should be replaced.
Remove excess oil from the inlet and outlet of the DPF with a clean cloth.
Install the DPF from the bracket for the clean emission module. Refer to Disassembly and Assembly, "Diesel Particulate Filter - Install" for the correct procedure.
Start the engine. Operate the engine a 100 percent throttle for a MINIMUM of 20 minutes. Do not operate the application under load at this time period.
After 20 minutes, use the electronic service tool to perform the "DPF Desulphation Procedure". The "DPF Desulphation Procedure" will last 60 minutes.
Once the "DPF Desulphation Procedure" has been completed, observe the soot load. If the soot load is at a value less than 80 percent, then the application can be returned to service.
Check the application for any signs of visible black smoke coming from the exhaust stack after the cleaning procedure has been completed. This could indicate a cracked DPF that will need to be replaced.Note: Black soot residue on the surface of the inside of the exhaust stack does not necessarily indicate a cracked DPF therefore should not be used in determining a problem with the DPF.
If white smoke does not dissipate, contact the Technical Communicator at a Caterpillar dealer. For further assistance, the Technical Communicator can confer with the Dealer Solutions Network.
After the manual DPF regeneration is complete, operate the engine at 1800 rpm for a MINIMUM of 20 minutes to stabilize the DPF temperatures.Note: The engine must maintain a steady speed for the entire duration of the test.
Hot engine components can cause injury from burns. Before performing maintenance on the engine, allow the engine and the components to cool.
Illustration 1 g02597531
Typical example (1) DPF Outlet Cap (2) Filter Paper (3) Hose Assembly (4) Air Pump
Illustration