Information injection-pump assembly
ZEXEL
104740-9700
1047409700
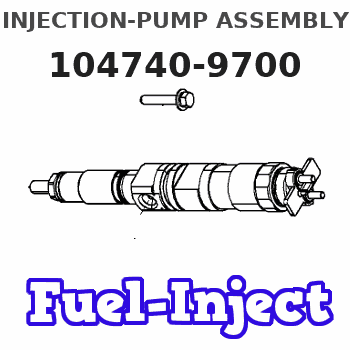
Rating:
Cross reference number
ZEXEL
104740-9700
1047409700
Zexel num
Bosch num
Firm num
Name
Calibration Data:
Adjustment conditions
Test oil
1404 Test oil ISO4113orSAEJ967d
1404 Test oil ISO4113orSAEJ967d
Test oil temperature
degC
45
45
50
Nozzle
105000-2010
Bosch type code
NP-DN12SD12TT
Nozzle holder
105780-2080
Opening pressure
MPa
14.7
14.7
15.19
Opening pressure
kgf/cm2
150
150
155
Injection pipe
Inside diameter - outside diameter - length (mm) mm 2-6-840
Inside diameter - outside diameter - length (mm) mm 2-6-840
Transfer pump pressure
kPa
20
20
20
Transfer pump pressure
kgf/cm2
0.2
0.2
0.2
Direction of rotation (viewed from drive side)
Right R
Right R
(Solenoid timer adjustment condition)
OFF
Injection timing adjustment
Pump speed
r/min
1100
1100
1100
Average injection quantity
mm3/st.
52
51.5
52.5
Difference in delivery
mm3/st.
3
Basic
*
Oil temperature
degC
50
48
52
Injection timing adjustment_02
Pump speed
r/min
600
600
600
Average injection quantity
mm3/st.
51.1
49.1
53.1
Oil temperature
degC
50
48
52
Injection timing adjustment_03
Pump speed
r/min
1100
1100
1100
Average injection quantity
mm3/st.
52
51
53
Difference in delivery
mm3/st.
3.5
Basic
*
Oil temperature
degC
50
48
52
Injection timing adjustment_04
Pump speed
r/min
2150
2150
2150
Average injection quantity
mm3/st.
44.2
42.1
46.3
Oil temperature
degC
52
50
54
Injection timing adjustment_05
Pump speed
r/min
2350
2350
2350
Average injection quantity
mm3/st.
33.6
30.6
36.6
Basic
*
Oil temperature
degC
52
50
54
Injection quantity adjustment
Pump speed
r/min
2350
2350
2350
Average injection quantity
mm3/st.
33.6
31.6
35.6
Basic
*
Oil temperature
degC
52
50
54
Injection quantity adjustment_02
Pump speed
r/min
2550
2550
2550
Average injection quantity
mm3/st.
10.8
7.3
14.3
Oil temperature
degC
55
52
58
Injection quantity adjustment_03
Pump speed
r/min
2700
2700
2700
Average injection quantity
mm3/st.
5
Oil temperature
degC
55
52
58
Governor adjustment
Pump speed
r/min
350
350
350
Average injection quantity
mm3/st.
6.5
4.5
8.5
Difference in delivery
mm3/st.
2
Basic
*
Oil temperature
degC
48
46
50
Governor adjustment_02
Pump speed
r/min
350
350
350
Average injection quantity
mm3/st.
6.5
4
9
Difference in delivery
mm3/st.
2.5
Basic
*
Oil temperature
degC
48
46
50
Timer adjustment
Pump speed
r/min
100
100
100
Average injection quantity
mm3/st.
60
45
80
Basic
*
Oil temperature
degC
48
46
50
Remarks
Full
Full
Timer adjustment_02
Pump speed
r/min
100
100
100
Average injection quantity
mm3/st.
60
45
80
Oil temperature
degC
48
46
50
Speed control lever angle
Pump speed
r/min
350
350
350
Average injection quantity
mm3/st.
0
0
0
Oil temperature
degC
48
46
50
Remarks
Magnet OFF at idling position
Magnet OFF at idling position
0000000901
Pump speed
r/min
1100
1100
1100
Overflow quantity with S/T ON
cm3/min
390
260
520
Oil temperature
degC
50
48
52
_02
Pump speed
r/min
1100
1100
1100
Overflow quantity with S/T ON
cm3/min
490
360
620
Oil temperature
degC
50
48
52
Remarks
Without an O-ring
Without an O-ring
Stop lever angle
Pump speed
r/min
1100
1100
1100
Pressure with S/T ON
kPa
481
442
520
Pressure with S/T ON
kgf/cm2
4.9
4.5
5.3
Pressure with S/T OFF
kPa
373
344
402
Pressure with S/T OFF
kgf/cm2
3.8
3.5
4.1
Basic
*
Oil temperature
degC
50
48
52
Stop lever angle_02
Pump speed
r/min
1100
1100
1100
Pressure with S/T OFF
kPa
373
334
412
Pressure with S/T OFF
kgf/cm2
3.8
3.4
4.2
Basic
*
Oil temperature
degC
50
48
52
Stop lever angle_03
Pump speed
r/min
1700
1700
1700
Pressure with S/T OFF
kPa
510
471
549
Pressure with S/T OFF
kgf/cm2
5.2
4.8
5.6
Oil temperature
degC
50
48
52
0000001101
Pump speed
r/min
1100
1100
1100
Timer stroke with S/T ON
mm
4.2
3.8
4.6
Timer stroke with S/T OFF
mm
2.5
2.3
2.7
Basic
*
Oil temperature
degC
50
48
52
_02
Pump speed
r/min
700
700
700
Timer stroke with S/T OFF
mm
0.5
0.5
Oil temperature
degC
50
48
52
_03
Pump speed
r/min
1100
1100
1100
Timer stroke with S/T ON
mm
4.2
3.7
4.7
Timer stroke with S/T OFF
mm
2.5
2.2
2.8
Basic
*
Oil temperature
degC
50
48
52
_04
Pump speed
r/min
1700
1700
1700
Timer stroke with S/T OFF
mm
4.6
4.1
5.1
Oil temperature
degC
50
48
52
_05
Pump speed
r/min
2550
2550
2550
Timer stroke with S/T OFF
mm
7.4
6.9
7.8
Oil temperature
degC
55
52
58
0000001201
Max. applied voltage
V
8
8
8
Test voltage
V
13
12
14
Timing setting
K dimension
mm
3.3
3.2
3.4
KF dimension
mm
5.8
5.7
5.9
MS dimension
mm
1
0.9
1.1
Control lever angle alpha
deg.
25
23
27
Control lever angle beta
deg.
36
31
41
Test data Ex:
0000001801 POTENTIOMETER ADJUSTMENT
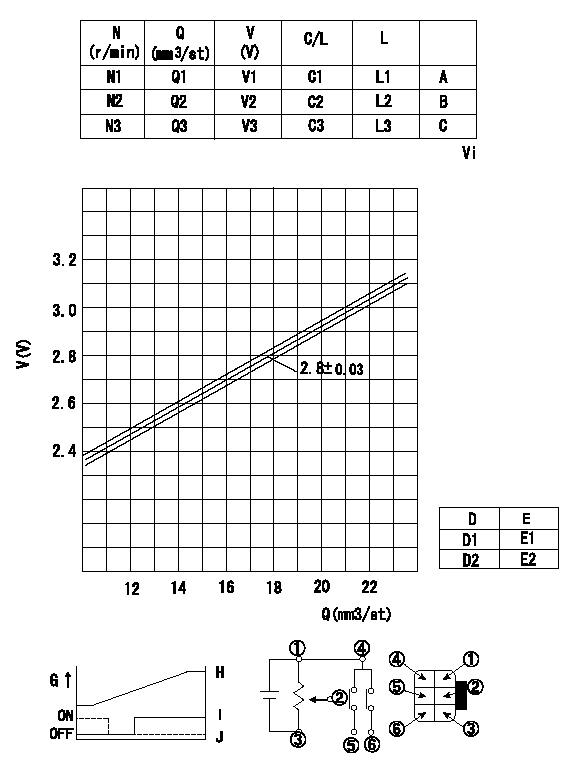
Adjustment of the potentiometer
1. Measure the injection quantity at pump speed N2 and with the control lever C2 from idle (gap L2). Then determine the voltage from the formula and adjust the potentiometer.
Voltage conversion formula: V+-0.03 = 0.068Q+1.59
2. At the full lever position, confirm at least V4.
N:Pump speed
Q:Injection quantity
V:Output voltage
C/L: control lever position
L:Thickness of the shim
A:-
B:Adjusting point
C:-
Vi:Applied voltage
D:Conversion point
D1:ON-->OFF
D2:OFF-->ON
E:Lever opening (from idle)
F:Connecting diagram for the potentiometer
G:Output
H:Output when (2) and (3) connected.
I:When (4) or (6) connected: switch OFF to ON.
J:When (4) or (5) connected: switch ON to OFF.
----------
N2=750r/min C2=11.5deg L2=7.6mm V4=6V
----------
N1=500r/min N2=750r/min N3=1100r/min V1=2.13V V2=2.8V V3=3.13V Q1=(11.0+-2.7mm3/st) Q2=17.8+-1.0mm3/st Q3=(17.2+-4.7mm3/st) C1=(7.5deg) C2=(11.5deg) C3=(13.5deg) L1=(5.0mm) L2=(7.6mm) L3=(9.0mm) E1=4.7+-3.5deg E2=23.7+-3.5deg Vi=10V
----------
N2=750r/min C2=11.5deg L2=7.6mm V4=6V
----------
N1=500r/min N2=750r/min N3=1100r/min V1=2.13V V2=2.8V V3=3.13V Q1=(11.0+-2.7mm3/st) Q2=17.8+-1.0mm3/st Q3=(17.2+-4.7mm3/st) C1=(7.5deg) C2=(11.5deg) C3=(13.5deg) L1=(5.0mm) L2=(7.6mm) L3=(9.0mm) E1=4.7+-3.5deg E2=23.7+-3.5deg Vi=10V
Information:
Illustration 1 g00669441
CCM to Host Equipment Direct Connection (1) CCM (2) CCM RS-232C port (3) Computer RS-232C port (4) Host equipmentMake sure that the following equipment is available:
A personal computer. Refer to "Caterpillar CCM PC For Windows: Getting Started Manual" for specifications on the PC.
The proper RS-232C cables are required for the particular installation. Refer to the Operation and Maintenance Manual, "RS-232C Cable Requirements".
The CCM PC Software for Windows. This software is available from Caterpillar.ProcedurePerform the following procedure to initialize communication with the host equipment that is connected directly to the CCM.Note: The host equipment and the CCM should be turned OFF before you change the cables to the serial ports.
The CCM should be installed with all of the wiring. Refer to Operations and Maintenance Manual, "General Wiring Diagram" and "RS-232C Cable Requirements".
Determine the parameters for communication for the installation. The default rate of communication (bits per second or bps) is 9600. The remaining default settings from the factory are no parity, 8 data bits, and 1 stop bit. These parameters will work well in most installations. Use the Operations and Maintenance Manual, "Communication Parameters - Identify" to determine the parameters of communication that are stored in the CCM.
Load the CCM PC For Windows software into the PC. Refer to the "Caterpillar CCM PC For Windows: Getting Started Manual". Start the CCM PC program and connect to the CCM.
Go to the Data Link pull-down menu. Select ECM, CCM. Go to the CCM configuration screen in the Utilities menu. Set the parameters for communication to match the values that were chosen in step 2.
Use the CCM configuration screen to set the Connection Type to Direct Connection. The CCM is now set at the determined communication configuration.Note: If the PC is required to communicate with the CCM, go to the Phone Book pull-down menu and select Add or Edit. Set the communication parameters of the PC to the values that were chosen in Step 2.Note: The electronic controller of each engine must be programmed with the correct engine number for identification on the CCM. The electronic controller is programmed to Engine Number 1 at the factory. Refer to Operation and Maintenance Manual, SEBU6874, "Engine Number - Program".Note: After the CCM has been connected to the PC, refer to the "CCM PC Software Users Manual". This manual contains instructions on monitoring and on controlling the engine remotely.Note: Two conditions must be met before the electronic engine controller will allow control by the CCM. The Engine Control Switch must be in the AUTO position, and the remote initiate contacts must be open. The engine may be monitored with the ECS in any position.Note: For an EMCP II application, the CCM cannot control the generator set if the GSC is in Service Mode. The generator set can only be monitored.