Information injection-pump assembly
BOSCH
9 460 610 241
9460610241
ZEXEL
104740-9351
1047409351
NISSAN-DIESEL
1670002N19
1670002n19
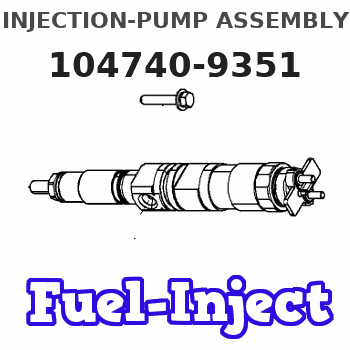
Rating:
Cross reference number
BOSCH
9 460 610 241
9460610241
ZEXEL
104740-9351
1047409351
NISSAN-DIESEL
1670002N19
1670002n19
Zexel num
Bosch num
Firm num
Name
Calibration Data:
Adjustment conditions
Test oil
1404 Test oil ISO4113orSAEJ967d
1404 Test oil ISO4113orSAEJ967d
Test oil temperature
degC
45
45
50
Nozzle
105000-2010
Bosch type code
NP-DN12SD12TT
Nozzle holder
105780-2080
Opening pressure
MPa
14.7
14.7
15.19
Opening pressure
kgf/cm2
150
150
155
Injection pipe
Inside diameter - outside diameter - length (mm) mm 2-6-840
Inside diameter - outside diameter - length (mm) mm 2-6-840
Transfer pump pressure
kPa
20
20
20
Transfer pump pressure
kgf/cm2
0.2
0.2
0.2
Direction of rotation (viewed from drive side)
Right R
Right R
(Solenoid timer adjustment condition)
OFF
Injection timing adjustment
Pump speed
r/min
1100
1100
1100
Average injection quantity
mm3/st.
44.6
44.1
45.1
Difference in delivery
mm3/st.
3
Basic
*
Injection timing adjustment_02
Pump speed
r/min
2550
2550
2550
Average injection quantity
mm3/st.
8.85
5.3
12.4
Injection timing adjustment_03
Pump speed
r/min
2350
2350
2350
Average injection quantity
mm3/st.
30.3
27.8
32.8
Injection timing adjustment_04
Pump speed
r/min
2150
2150
2150
Average injection quantity
mm3/st.
38
35.9
40.1
Injection timing adjustment_05
Pump speed
r/min
1100
1100
1100
Average injection quantity
mm3/st.
44.6
43.6
45.6
Injection timing adjustment_06
Pump speed
r/min
600
600
600
Average injection quantity
mm3/st.
43.5
41.5
45.5
Injection quantity adjustment
Pump speed
r/min
2350
2350
2350
Average injection quantity
mm3/st.
30.3
28.3
32.3
Basic
*
Injection quantity adjustment_02
Pump speed
r/min
2700
2700
2700
Average injection quantity
mm3/st.
5
Governor adjustment
Pump speed
r/min
350
350
350
Average injection quantity
mm3/st.
6.5
4.5
8.5
Difference in delivery
mm3/st.
2
Basic
*
Governor adjustment_02
Pump speed
r/min
350
350
350
Average injection quantity
mm3/st.
6.5
4.5
8.5
Governor adjustment_03
Pump speed
r/min
450
450
450
Average injection quantity
mm3/st.
2
Timer adjustment
Pump speed
r/min
100
100
100
Average injection quantity
mm3/st.
62.5
45
80
Basic
*
Speed control lever angle
Pump speed
r/min
350
350
350
Average injection quantity
mm3/st.
0
0
0
Remarks
Magnet OFF
Magnet OFF
0000000901
Pump speed
r/min
1100
1100
1100
Overflow quantity with S/T ON
cm3/min
390
258
522
Stop lever angle
Pump speed
r/min
1100
1100
1100
Pressure with S/T OFF
kPa
372.5
343
402
Pressure with S/T OFF
kgf/cm2
3.8
3.5
4.1
Basic
*
Stop lever angle_02
Pump speed
r/min
1100
1100
1100
Pressure with S/T OFF
kPa
372.5
343
402
Pressure with S/T OFF
kgf/cm2
3.8
3.5
4.1
Stop lever angle_03
Pump speed
r/min
1700
1700
1700
Pressure with S/T OFF
kPa
510
481
539
Pressure with S/T OFF
kgf/cm2
5.2
4.9
5.5
Stop lever angle_04
Pump speed
r/min
2150
2150
2150
Pressure with S/T OFF
kPa
598.5
569
628
Pressure with S/T OFF
kgf/cm2
6.1
5.8
6.4
0000001101
Pump speed
r/min
1100
1100
1100
Timer stroke with S/T OFF
mm
2.5
2.3
2.7
Basic
*
_02
Pump speed
r/min
1100
1100
1100
Timer stroke with S/T ON
mm
4.2
3.7
4.7
Timer stroke with S/T OFF
mm
2.5
2.2
2.8
_03
Pump speed
r/min
1700
1700
1700
Timer stroke with S/T OFF
mm
4.6
4.1
5.1
_04
Pump speed
r/min
2550
2550
2550
Timer stroke with S/T OFF
mm
6.9
6.4
7.4
0000001201
Max. applied voltage
V
8
8
8
Test voltage
V
13
12
14
Timing setting
K dimension
mm
3.3
3.2
3.4
KF dimension
mm
5.8
5.7
5.9
MS dimension
mm
1
0.9
1.1
Control lever angle alpha
deg.
54
50
58
Control lever angle beta
deg.
42
37
47
Test data Ex:
0000001801 CONTROL LEVER ANGLE
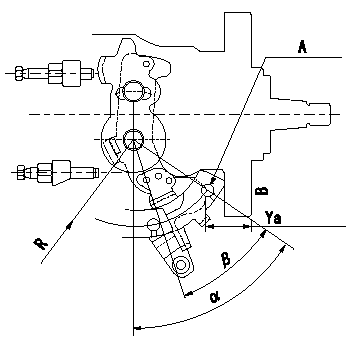
Control lever angle measurement
1. Measure dimension Ya between the end of the lever and the flange face.
2. Measure the lever angle from the pin hole R (plate).
A = lever angle measuring position
B = flange face
----------
Ya=23.7~28.3mm R=49mm
----------
Ya=23.7~28.3mm R=49mm
----------
Ya=23.7~28.3mm R=49mm
----------
Ya=23.7~28.3mm R=49mm
Information:
Illustration 8 g00778880
This is an illustration of the 154-8016 Fuel Injector Seals . (14) Metal Seal (15) 133-3715 Backup Ring (16) 150-4105 Backup Ring (17) 9X-7557 O-Ring Seal (18) 148-2903 O-Ring Seal (19) 149-5240 Backup Ring (20) 109-3207 O-Ring Seal
Illustration 9 g00638512
(A) 149-2955 Seal Protector
Illustration 10 g00638506
(B) 149-2956 Seal Installer
The correct procedures and tooling specifications must always be used. Failure to follow any of the procedures may result in damage, malfunction, or possible engine failure.
Note: Install the upper seal pack first. Then install the middle seal pack. Finally, install the bottom O-Ring Seal.
Both the 149-2955 Seal Protector (A) and the 149-2956 Seal Installer (B) should be used when you are installing the upper high pressure seals.Note: New seals should be installed after each removal of the injector from the engine.
Lubricate the O-Ring seals and the sleeve bore of the injector sparingly with clean engine oil.Note: Proper installation of the injector is very important. Damage to the upper high pressure seals can cause excessive oil leakage under the valve cover. This may cause the engine not to start due to a low actuation pressure. Damage to the lower high pressure seals may allow high pressure oil to leak into the fuel supply passage. This will result in excessive oil consumption.
Illustration 11 g00621566
(X) 8T-2396 Bolts . (Y) 159-0288 Deflector . Note: Some of these engines were built without the 159-0288 Deflector . During the installation of the unit injectors, the deflectors should be installed. Six 159-0288 Deflectors and six 8T-2396 Bolts are required for each engine. These new deflectors and bolts replace the former 6V-8653 Bolts .
Illustration 12 g00294210
Illustration 13 g00312124
(C) 152-1057 Fuel Injector Installer
Carefully install the injector into the injector bore. If access permits you to seat the injector, push the injector straight down on top of the injector's solenoid by hand until the injector is firmly seated in the injector bore. Pushing hard enough to compress the injector's seals may be difficult. If the injector can not be seated by hand, use a 152-1057 Fuel Injector Installer (C). Note: Do NOT pry on the top of the injector with another tool. Do NOT strike the injector with a hammer. Damage to the injector will result. Damage to the injector that is due to improper installation is not a warrantable failure.
Illustration 14 g00778888
(2) Wiring Harness Connection (3) Clamp (10) Shoulder Bolt (11) Socket Head BoltNote: Do not use the shoulder bolt and the socket head bolt in order to seat the injector. If a side load is placed on the bolts, the bolts may fail.
After the injector is seated, position the clamp (2) and tighten the Shoulder Bolt (10) to a torque of 6 N m (50 lb in). Then tighten the Socket Head Bolt (11) to a torque of 12 N m (9 lb ft).
Insert the harness connectors (2) back into the injectors' solenoids. Ensure that the clips are snapped back into