Information injection-pump assembly
ZEXEL
104740-4230
1047404230
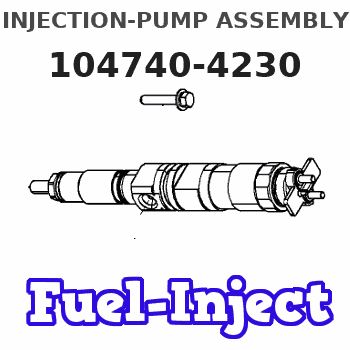
Rating:
Cross reference number
ZEXEL
104740-4230
1047404230
Zexel num
Bosch num
Firm num
Name
Calibration Data:
Adjustment conditions
Test oil
1404 Test oil ISO4113orSAEJ967d
1404 Test oil ISO4113orSAEJ967d
Test oil temperature
degC
45
45
50
Nozzle
105000-2010
Bosch type code
NP-DN12SD12TT
Nozzle holder
105780-2080
Opening pressure
MPa
14.7
14.7
15.19
Opening pressure
kgf/cm2
150
150
155
Injection pipe
Inside diameter - outside diameter - length (mm) mm 2-6-840
Inside diameter - outside diameter - length (mm) mm 2-6-840
Transfer pump pressure
kPa
20
20
20
Transfer pump pressure
kgf/cm2
0.2
0.2
0.2
Direction of rotation (viewed from drive side)
Right R
Right R
Injection timing adjustment
Pump speed
r/min
1000
1000
1000
Average injection quantity
mm3/st.
37
36.5
37.5
Difference in delivery
mm3/st.
3
Basic
*
Injection timing adjustment_02
Pump speed
r/min
2300
2300
2300
Average injection quantity
mm3/st.
18.1
14.6
21.6
Injection timing adjustment_03
Pump speed
r/min
2150
2150
2150
Average injection quantity
mm3/st.
33.2
31.1
35.3
Injection timing adjustment_04
Pump speed
r/min
1000
1000
1000
Average injection quantity
mm3/st.
37
36
38
Injection timing adjustment_05
Pump speed
r/min
600
600
600
Average injection quantity
mm3/st.
31.9
29.9
33.9
Injection timing adjustment_06
Pump speed
r/min
1000
1000
1000
Average injection quantity
mm3/st.
36.1
35.6
36.6
Difference in delivery
mm3/st.
3
Basic
*
Remarks
For Japan
For Japan
Injection timing adjustment_07
Pump speed
r/min
2300
2300
2300
Average injection quantity
mm3/st.
17.7
14.2
21.2
Remarks
For Japan
For Japan
Injection timing adjustment_08
Pump speed
r/min
2150
2150
2150
Average injection quantity
mm3/st.
32.6
30.5
34.7
Remarks
For Japan
For Japan
Injection timing adjustment_09
Pump speed
r/min
1000
1000
1000
Average injection quantity
mm3/st.
36.1
35.1
37.1
Remarks
For Japan
For Japan
Injection timing adjustment_10
Pump speed
r/min
600
600
600
Average injection quantity
mm3/st.
31.3
29.3
33.3
Remarks
For Japan
For Japan
Injection quantity adjustment
Pump speed
r/min
2300
2300
2300
Average injection quantity
mm3/st.
18.1
15.1
21.1
Basic
*
Injection quantity adjustment_02
Pump speed
r/min
2450
2450
2450
Average injection quantity
mm3/st.
5
Injection quantity adjustment_03
Pump speed
r/min
2300
2300
2300
Average injection quantity
mm3/st.
17.7
14.7
20.7
Basic
*
Remarks
For Japan
For Japan
Injection quantity adjustment_04
Pump speed
r/min
2450
2450
2450
Average injection quantity
mm3/st.
5
Remarks
For Japan
For Japan
Governor adjustment
Pump speed
r/min
300
300
300
Average injection quantity
mm3/st.
6.5
4.5
8.5
Difference in delivery
mm3/st.
2
Basic
*
Governor adjustment_02
Pump speed
r/min
300
300
300
Average injection quantity
mm3/st.
6.5
4.5
8.5
Governor adjustment_03
Pump speed
r/min
350
350
350
Average injection quantity
mm3/st.
3
Governor adjustment_04
Pump speed
r/min
300
300
300
Average injection quantity
mm3/st.
6.3
4.3
8.3
Difference in delivery
mm3/st.
2
Basic
*
Remarks
For Japan
For Japan
Governor adjustment_05
Pump speed
r/min
300
300
300
Average injection quantity
mm3/st.
6.3
4.3
8.3
Remarks
For Japan
For Japan
Governor adjustment_06
Pump speed
r/min
350
350
350
Average injection quantity
mm3/st.
3
Remarks
For Japan
For Japan
Timer adjustment
Pump speed
r/min
100
100
100
Average injection quantity
mm3/st.
74.5
57
92
Basic
*
Timer adjustment_02
Pump speed
r/min
100
100
100
Average injection quantity
mm3/st.
72.5
55
90
Basic
*
Remarks
For Japan
For Japan
Speed control lever angle
Pump speed
r/min
300
300
300
Average injection quantity
mm3/st.
0
0
0
Remarks
Magnet OFF
Magnet OFF
Speed control lever angle_02
Pump speed
r/min
300
300
300
Average injection quantity
mm3/st.
0
0
0
Remarks
For Japan: Magnet OFF
For Japan: Magnet OFF
0000000901
Pump speed
r/min
1000
1000
1000
Overflow quantity
cm3/min
360
234
486
_02
Pump speed
r/min
1000
1000
1000
Overflow quantity
cm3/min
378
246
510
Remarks
For Japan
For Japan
Stop lever angle
Pump speed
r/min
1700
1700
1700
Pressure
kPa
588.5
559
618
Pressure
kgf/cm2
6
5.7
6.3
Basic
*
Stop lever angle_02
Pump speed
r/min
600
600
600
Pressure
kPa
333.5
304
363
Pressure
kgf/cm2
3.4
3.1
3.7
Stop lever angle_03
Pump speed
r/min
1700
1700
1700
Pressure
kPa
588.5
559
618
Pressure
kgf/cm2
6
5.7
6.3
Stop lever angle_04
Pump speed
r/min
2150
2150
2150
Pressure
kPa
706
677
735
Pressure
kgf/cm2
7.2
6.9
7.5
Stop lever angle_05
Pump speed
r/min
1700
1700
1700
Pressure
kPa
578.5
549
608
Pressure
kgf/cm2
5.9
5.6
6.2
Basic
*
Remarks
For Japan
For Japan
Stop lever angle_06
Pump speed
r/min
600
600
600
Pressure
kPa
323.5
294
353
Pressure
kgf/cm2
3.3
3
3.6
Remarks
For Japan
For Japan
Stop lever angle_07
Pump speed
r/min
1700
1700
1700
Pressure
kPa
578.5
549
608
Pressure
kgf/cm2
5.9
5.6
6.2
Remarks
For Japan
For Japan
Stop lever angle_08
Pump speed
r/min
2150
2150
2150
Pressure
kPa
696.5
667
726
Pressure
kgf/cm2
7.1
6.8
7.4
Remarks
For Japan
For Japan
0000001101
Pump speed
r/min
1700
1700
1700
Timer stroke
mm
4.8
4.6
5
Basic
*
_02
Pump speed
r/min
1000
1000
1000
Timer stroke
mm
2.1
1.5
2.7
_03
Pump speed
r/min
1700
1700
1700
Timer stroke
mm
4.8
4.5
5.1
_04
Pump speed
r/min
2150
2150
2150
Timer stroke
mm
6.7
6.3
7.1
_05
Pump speed
r/min
1700
1700
1700
Timer stroke
mm
4.7
4.5
4.9
Basic
*
Remarks
For Japan
For Japan
_06
Pump speed
r/min
1000
1000
1000
Timer stroke
mm
2
1.4
2.6
Remarks
For Japan
For Japan
_07
Pump speed
r/min
1700
1700
1700
Timer stroke
mm
4.7
4.4
5
Remarks
For Japan
For Japan
_08
Pump speed
r/min
2150
2150
2150
Timer stroke
mm
6.6
6.1
7.1
Remarks
For Japan
For Japan
0000001201
Max. applied voltage
V
8
8
8
Test voltage
V
13
12
14
Timing setting
K dimension
mm
3.3
3.2
3.4
KF dimension
mm
5.8
5.7
5.9
MS dimension
mm
1.5
1.4
1.6
Control lever angle alpha
deg.
25
21
29
Control lever angle beta
deg.
46
41
51
Information:
Crankcase Breather
Clean
This maintenance is to be performed every other oil change or 600 hours. 1. Loosen breather retaining clamp (1) on breather.2. Loosen hose clamp (2) and remove breather assembly.3. Wash breather in clean, nonflammable solvent and allow to dry.4. Install new seal.5. Assemble breather and install in reverse order of removal.6. Tighten all hose clamps (2) to 27 4.5 lb in (3.0 0.5 N m). If the crankcase breather is not maintained on a regular basis, it will become plugged. A plugged crankcase breather would result in excessive crankcase pressure that may cause crankshaft seal leakage.Refer to the Torque Specifications section of this manual for Torque for Standard Hose Clamps-Worm Drive Band Type hose clamps if your engine is equipped.Alternator, Fan and Accessory Drive Belts
Inspect/Replace
Inspect the condition and adjustment of alternator belts and fan drive belts.Inspect all drive belts for wear and replace if they show any signs of wear.If one belt in a set requires replacement, always install a new matched set of belts. Never replace just the worn belt. If only the worn belt is replaced, the new belt will carry all the load, as it will not be stretched as much as the older belts. All the belts will fail in rapid succession.Belt Adjustment
If belts are too loose, they vibrate enough to cause unnecessary wear on the belts and pulleys.If belts are too tight, unnecessary stresses are placed upon the pulley bearings and belts which might shorten the life of both.1. Inspect the condition and adjustment of alternator belts and fan drive belts.2. To check the belt tension, apply 25 lbs (110 N) of force midway between the pulleys. Correctly adjusted belts will deflect 1/2 to 3/4 inch (13 to 19 mm).Adjust Alternator Belts
3. To adjust the alternator drive belts, loosen mounting bolt(s) (1) and adjusting bracket nut(s) (2).4. Adjust the alternator in or out by either tightening or loosening adjusting nut(s) (2), as required, to obtain the correct adjustment.5. Tighten bolts (1) and nuts (2).6. If new belts are installed, check belt adjustment again after 30 minutes of engine operation. Replace belts in matched sets only. If only one belt of a matched set is replaced, it will carry more of a load than the belts not replaced since the older belts are stretched. The additional load on the new belt could cause it to break.Adjust Fan Drive Belts
7. To adjust the fan drive belts, loosen mounting bolts and adjust with adjusting bolt.8. Move the fan drive up or down as required to obtain the correct adjustment. Tighten mounting bolts.9. If new belts are installed, check belt adjustment again after 30 minutes of engine operation.Refer to the Service Manual for 3406 Truck Engines for more information or see your Caterpillar dealer.Hoses and Clamps
Inspect
* Inspect all hoses for leaks due to cracking, softness and loose clamps.* Replace hoses that are cracked or soft and tighten loose clamps.Before Replacing Hoses
1. After engine is cool, loosen the radiator filler cap slowly to relieve any
Clean
This maintenance is to be performed every other oil change or 600 hours. 1. Loosen breather retaining clamp (1) on breather.2. Loosen hose clamp (2) and remove breather assembly.3. Wash breather in clean, nonflammable solvent and allow to dry.4. Install new seal.5. Assemble breather and install in reverse order of removal.6. Tighten all hose clamps (2) to 27 4.5 lb in (3.0 0.5 N m). If the crankcase breather is not maintained on a regular basis, it will become plugged. A plugged crankcase breather would result in excessive crankcase pressure that may cause crankshaft seal leakage.Refer to the Torque Specifications section of this manual for Torque for Standard Hose Clamps-Worm Drive Band Type hose clamps if your engine is equipped.Alternator, Fan and Accessory Drive Belts
Inspect/Replace
Inspect the condition and adjustment of alternator belts and fan drive belts.Inspect all drive belts for wear and replace if they show any signs of wear.If one belt in a set requires replacement, always install a new matched set of belts. Never replace just the worn belt. If only the worn belt is replaced, the new belt will carry all the load, as it will not be stretched as much as the older belts. All the belts will fail in rapid succession.Belt Adjustment
If belts are too loose, they vibrate enough to cause unnecessary wear on the belts and pulleys.If belts are too tight, unnecessary stresses are placed upon the pulley bearings and belts which might shorten the life of both.1. Inspect the condition and adjustment of alternator belts and fan drive belts.2. To check the belt tension, apply 25 lbs (110 N) of force midway between the pulleys. Correctly adjusted belts will deflect 1/2 to 3/4 inch (13 to 19 mm).Adjust Alternator Belts
3. To adjust the alternator drive belts, loosen mounting bolt(s) (1) and adjusting bracket nut(s) (2).4. Adjust the alternator in or out by either tightening or loosening adjusting nut(s) (2), as required, to obtain the correct adjustment.5. Tighten bolts (1) and nuts (2).6. If new belts are installed, check belt adjustment again after 30 minutes of engine operation. Replace belts in matched sets only. If only one belt of a matched set is replaced, it will carry more of a load than the belts not replaced since the older belts are stretched. The additional load on the new belt could cause it to break.Adjust Fan Drive Belts
7. To adjust the fan drive belts, loosen mounting bolts and adjust with adjusting bolt.8. Move the fan drive up or down as required to obtain the correct adjustment. Tighten mounting bolts.9. If new belts are installed, check belt adjustment again after 30 minutes of engine operation.Refer to the Service Manual for 3406 Truck Engines for more information or see your Caterpillar dealer.Hoses and Clamps
Inspect
* Inspect all hoses for leaks due to cracking, softness and loose clamps.* Replace hoses that are cracked or soft and tighten loose clamps.Before Replacing Hoses
1. After engine is cool, loosen the radiator filler cap slowly to relieve any