Information injection-pump assembly
BOSCH
9 460 610 239
9460610239
ZEXEL
104740-3760
1047403760
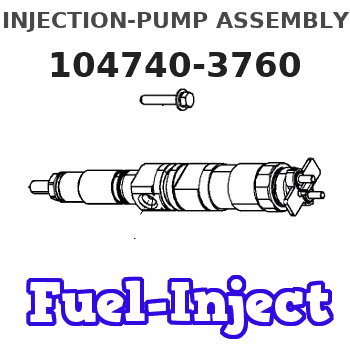
Rating:
Cross reference number
BOSCH
9 460 610 239
9460610239
ZEXEL
104740-3760
1047403760
Zexel num
Bosch num
Firm num
Name
Calibration Data:
Adjustment conditions
Test oil
1404 Test oil ISO4113orSAEJ967d
1404 Test oil ISO4113orSAEJ967d
Test oil temperature
degC
45
45
50
Nozzle
105000-2010
Bosch type code
NP-DN12SD12TT
Nozzle holder
105780-2080
Opening pressure
MPa
14.7
14.7
15.19
Opening pressure
kgf/cm2
150
150
155
Injection pipe
Inside diameter - outside diameter - length (mm) mm 2-6-840
Inside diameter - outside diameter - length (mm) mm 2-6-840
Transfer pump pressure
kPa
20
20
20
Transfer pump pressure
kgf/cm2
0.2
0.2
0.2
Direction of rotation (viewed from drive side)
Right R
Right R
Injection timing adjustment
Pump speed
r/min
1250
1250
1250
Average injection quantity
mm3/st.
45.8
45.3
46.3
Difference in delivery
mm3/st.
3
Basic
*
Injection timing adjustment_02
Pump speed
r/min
2150
2150
2150
Average injection quantity
mm3/st.
18.1
13.1
23.1
Injection timing adjustment_03
Pump speed
r/min
2000
2000
2000
Average injection quantity
mm3/st.
39.2
37.2
41.2
Injection timing adjustment_04
Pump speed
r/min
1250
1250
1250
Average injection quantity
mm3/st.
45.8
44.8
46.8
Injection timing adjustment_05
Pump speed
r/min
600
600
600
Average injection quantity
mm3/st.
44.3
42.3
46.3
Injection quantity adjustment
Pump speed
r/min
2150
2150
2150
Average injection quantity
mm3/st.
18.1
15.1
21.1
Difference in delivery
mm3/st.
4
Basic
*
Injection quantity adjustment_02
Pump speed
r/min
2500
2500
2500
Average injection quantity
mm3/st.
5
Governor adjustment
Pump speed
r/min
375
375
375
Average injection quantity
mm3/st.
8
6.5
9.5
Difference in delivery
mm3/st.
2
Basic
*
Governor adjustment_02
Pump speed
r/min
375
375
375
Average injection quantity
mm3/st.
8
6
10
Governor adjustment_03
Pump speed
r/min
600
600
600
Average injection quantity
mm3/st.
3
Timer adjustment
Pump speed
r/min
100
100
100
Average injection quantity
mm3/st.
73
63
83
Basic
*
Speed control lever angle
Pump speed
r/min
375
375
375
Average injection quantity
mm3/st.
0
0
0
Remarks
Magnet OFF
Magnet OFF
0000000901
Pump speed
r/min
1250
1250
1250
Overflow quantity
cm3/min
420
288
552
Stop lever angle
Pump speed
r/min
1250
1250
1250
Pressure
kPa
470.5
441
500
Pressure
kgf/cm2
4.8
4.5
5.1
Basic
*
Stop lever angle_02
Pump speed
r/min
600
600
600
Pressure
kPa
313.5
284
343
Pressure
kgf/cm2
3.2
2.9
3.5
Stop lever angle_03
Pump speed
r/min
1250
1250
1250
Pressure
kPa
470.5
441
500
Pressure
kgf/cm2
4.8
4.5
5.1
Stop lever angle_04
Pump speed
r/min
2000
2000
2000
Pressure
kPa
647.5
618
677
Pressure
kgf/cm2
6.6
6.3
6.9
0000001101
Pump speed
r/min
1250
1250
1250
Timer stroke
mm
3.7
3.5
3.9
Basic
*
_02
Pump speed
r/min
500
500
500
Timer stroke
mm
1.2
0.6
1.8
_03
Pump speed
r/min
750
750
750
Timer stroke
mm
2
1.4
2.6
_04
Pump speed
r/min
1250
1250
1250
Timer stroke
mm
3.7
3.3
4.1
_05
Pump speed
r/min
2000
2000
2000
Timer stroke
mm
6.8
6.2
7.4
0000001201
Max. applied voltage
V
8
8
8
Test voltage
V
13
12
14
0000001401
Pump speed
r/min
1250
1250
1250
Average injection quantity
mm3/st.
35.7
35.2
36.2
Timer stroke variation dT
mm
0.6
0.4
0.8
Basic
*
_02
Pump speed
r/min
1250
1250
1250
Average injection quantity
mm3/st.
35.7
34.7
36.7
Timer stroke TA
mm
3.1
3.1
3.1
Timer stroke variation dT
mm
0.6
0.2
1
_03
Pump speed
r/min
1250
1250
1250
Average injection quantity
mm3/st.
28.2
26.7
29.7
Timer stroke TA
mm
2.3
2.3
2.3
Timer stroke variation dT
mm
1.4
0.8
2
Timing setting
K dimension
mm
3.3
3.2
3.4
KF dimension
mm
5.8
5.7
5.9
MS dimension
mm
1.2
1.1
1.3
Pre-stroke
mm
0
0
0
Control lever angle alpha
deg.
59
55
63
Control lever angle beta
deg.
45
40
50
Information:
Fuel System Information
Use only fuel as recommended in this section.
Fill the fuel tank at the end of each day of operation to drive out moist air and to prevent condensation. Do not fill the tank to the top. Fuel expands as it gets warm and may overflow. Do not fill the fuel filters with fuel before installing them. Contaminated fuel will cause accelerated wear to the fuel system parts.
Fuel Tanks
Drain the water and sediment from any fuel storage tank weekly, at the oil change period, and before it is refilled. This will help prevent water and/or sediment from being pumped from the fuel storage tank into the engine fuel tank.Fuel tanks should contain some provision for draining water and sediment from the bottom of the fuel tanks. Some fuel tanks use supply pipes that allow water and sediment to settle below the end of the fuel supply pipe. This water and sediment should be drained at each oil change. Do not use fuel tanks with supply lines that take fuel directly from the bottom of the tank.Fuel Lines
The fuel return line should deposit fuel at the top of the tank opposite the supply connection. This allows the engine to get warm (not hot) fuel from the tank. It also allows air to escape from the return fuel without being pulled back into the engine. If hot fuel must return to the tank, a fuel cooler is required.Avoid sharp angles and use as few fittings and connections as possible. Moisture in the fuel will tend to collect and freeze at low points in the fuel lines. Fuel lines should travel the most direct route to the engine compartment.Do not use galvanized fittings in the fuel lines. Size fuel lines so they do not exceed maximum fuel transfer pump inlet restriction and fuel return line restriction specifications.Fuel Filters
A primary fuel filter and/or water separator is recommended and should be installed between the fuel tank and the engine fuel inlet.After changing the fuel filter(s), always prime the fuel system (if equipped with a priming pump) to remove air bubbles from the system.Fuel Recommendations
Caterpillar Diesel Engines are capable of burning a wide range of distillate fuels. The use of clean, stable blends of distillate fuel which meet the following requirements will provide quality engine service life. The fuels recommended for use in Caterpillar engines are normally No.2-D diesel fuel and No.2 fuel oil, although No. 1 grades are acceptable. The following fuel specifications are some of the worldwide fuels which also meet the requirements. The following fuel characteristics should be considered when procuring fuel for use in Caterpillar diesel engines.Cetane Number
The minimum cetane number required for average starting conditions for the direct injection engine is 40. A higher cetane value may be required for high altitude operation or cold weather starting.Filterability
Clean fuels should have no more than 0.1% of sediment and water. Storage of fuel for extended periods of time can cause fuel oxidation with solids forming, causing filtering problems.Pour Point
The pour
Use only fuel as recommended in this section.
Fill the fuel tank at the end of each day of operation to drive out moist air and to prevent condensation. Do not fill the tank to the top. Fuel expands as it gets warm and may overflow. Do not fill the fuel filters with fuel before installing them. Contaminated fuel will cause accelerated wear to the fuel system parts.
Fuel Tanks
Drain the water and sediment from any fuel storage tank weekly, at the oil change period, and before it is refilled. This will help prevent water and/or sediment from being pumped from the fuel storage tank into the engine fuel tank.Fuel tanks should contain some provision for draining water and sediment from the bottom of the fuel tanks. Some fuel tanks use supply pipes that allow water and sediment to settle below the end of the fuel supply pipe. This water and sediment should be drained at each oil change. Do not use fuel tanks with supply lines that take fuel directly from the bottom of the tank.Fuel Lines
The fuel return line should deposit fuel at the top of the tank opposite the supply connection. This allows the engine to get warm (not hot) fuel from the tank. It also allows air to escape from the return fuel without being pulled back into the engine. If hot fuel must return to the tank, a fuel cooler is required.Avoid sharp angles and use as few fittings and connections as possible. Moisture in the fuel will tend to collect and freeze at low points in the fuel lines. Fuel lines should travel the most direct route to the engine compartment.Do not use galvanized fittings in the fuel lines. Size fuel lines so they do not exceed maximum fuel transfer pump inlet restriction and fuel return line restriction specifications.Fuel Filters
A primary fuel filter and/or water separator is recommended and should be installed between the fuel tank and the engine fuel inlet.After changing the fuel filter(s), always prime the fuel system (if equipped with a priming pump) to remove air bubbles from the system.Fuel Recommendations
Caterpillar Diesel Engines are capable of burning a wide range of distillate fuels. The use of clean, stable blends of distillate fuel which meet the following requirements will provide quality engine service life. The fuels recommended for use in Caterpillar engines are normally No.2-D diesel fuel and No.2 fuel oil, although No. 1 grades are acceptable. The following fuel specifications are some of the worldwide fuels which also meet the requirements. The following fuel characteristics should be considered when procuring fuel for use in Caterpillar diesel engines.Cetane Number
The minimum cetane number required for average starting conditions for the direct injection engine is 40. A higher cetane value may be required for high altitude operation or cold weather starting.Filterability
Clean fuels should have no more than 0.1% of sediment and water. Storage of fuel for extended periods of time can cause fuel oxidation with solids forming, causing filtering problems.Pour Point
The pour