Information injection-pump assembly
BOSCH
9 400 616 468
9400616468
ZEXEL
104303-3360
1043033360
ISEKI
62156000130
62156000130

Rating:
Service parts 104303-3360 INJECTION-PUMP ASSEMBLY:
1.
_
3.
GOVERNOR
5.
AUTOM. ADVANCE MECHANIS
6.
COUPLING PLATE
7.
COUPLING PLATE
8.
_
9.
_
11.
Nozzle and Holder
6215300-0010E
12.
Open Pre:MPa(Kqf/cm2)
11.8{120}
15.
NOZZLE SET
Include in #1:
104303-3360
as INJECTION-PUMP ASSEMBLY
Cross reference number
BOSCH
9 400 616 468
9400616468
ZEXEL
104303-3360
1043033360
ISEKI
62156000130
62156000130
Zexel num
Bosch num
Firm num
Name
104303-3360
9 400 616 468
62156000130 ISEKI
INJECTION-PUMP ASSEMBLY
E3AD1 * K 14BV PES3K PE
E3AD1 * K 14BV PES3K PE
Calibration Data:
Adjustment conditions
Test oil
1404 Test oil ISO4113 or {SAEJ967d}
1404 Test oil ISO4113 or {SAEJ967d}
Test oil temperature
degC
40
40
45
Nozzle and nozzle holder
105780-8140
Bosch type code
EF8511/9A
Nozzle
105780-0000
Bosch type code
DN12SD12T
Nozzle holder
105780-2080
Bosch type code
EF8511/9
Opening pressure
MPa
17.2
Opening pressure
kgf/cm2
175
Injection pipe
Outer diameter - inner diameter - length (mm) mm 6-2-600
Outer diameter - inner diameter - length (mm) mm 6-2-600
Tester oil delivery pressure
kPa
157
157
157
Tester oil delivery pressure
kgf/cm2
1.6
1.6
1.6
Direction of rotation (viewed from drive side)
Right R
Right R
Injection timing adjustment
Direction of rotation (viewed from drive side)
Right R
Right R
Injection order
1-3-2
Pre-stroke
mm
2.1
2.05
2.15
Beginning of injection position
Drive side NO.1
Drive side NO.1
Difference between angles 1
Cal 1-3 deg. 120 119.5 120.5
Cal 1-3 deg. 120 119.5 120.5
Difference between angles 2
Cyl.1-2 deg. 240 239.5 240.5
Cyl.1-2 deg. 240 239.5 240.5
Injection quantity adjustment
Adjusting point
-
Rack position
9.4
Pump speed
r/min
800
800
800
Average injection quantity
mm3/st.
34.8
33.8
35.8
Max. variation between cylinders
%
0
-2.5
2.5
Basic
*
Fixing the lever
*
Standard for adjustment of the maximum variation between cylinders
*
Injection quantity adjustment_02
Adjusting point
-
Rack position
5.6+-0.5
Pump speed
r/min
425
425
425
Average injection quantity
mm3/st.
6.5
5.5
7.5
Max. variation between cylinders
%
0
-14
14
Fixing the lever
*
Standard for adjustment of the maximum variation between cylinders
*
Remarks
Adjust only variation between cylinders; adjust governor according to governor specifications.
Adjust only variation between cylinders; adjust governor according to governor specifications.
Injection quantity adjustment_03
Adjusting point
C
Rack position
8.5+-0.5
Pump speed
r/min
1300
1300
1300
Average injection quantity
mm3/st.
34.8
33.8
35.8
Basic
*
Fixing the lever
*
Remarks
Set full load.
Set full load.
Injection quantity adjustment_04
Adjusting point
D
Rack position
13+1
Pump speed
r/min
100
100
100
Average injection quantity
mm3/st.
40
40
Fixing the lever
*
Test data Ex:
Governor adjustment
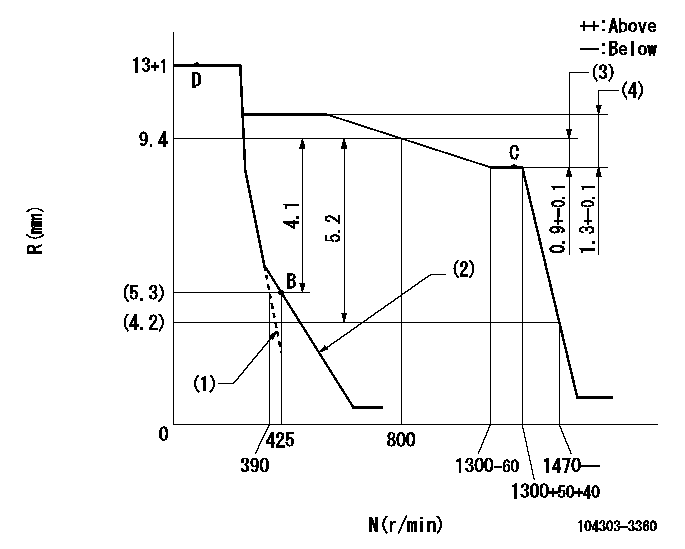
N:Pump speed
R:Rack position (mm)
(1)Set the idle spring.
(2)Main spring setting
(3)Rack difference between N = N1 and N = N2
(4)Rack difference between N = N3 and N = N4
----------
N1=1300r/min N2=800r/min N3=1300r/min N4=500r/min
----------
----------
N1=1300r/min N2=800r/min N3=1300r/min N4=500r/min
----------
Speed control lever angle
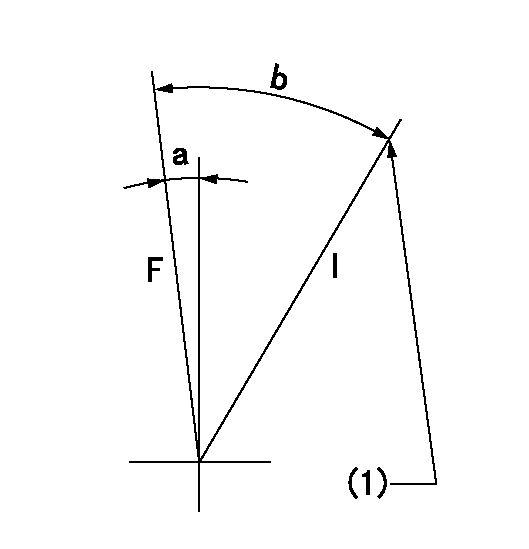
F:Full speed
I:Idle
(1)Stopper bolt setting
----------
----------
a=7deg+-3deg b=31deg+-6deg
----------
----------
a=7deg+-3deg b=31deg+-6deg
Timing setting

(1)Pump vertical direction
(2)Position of gear mark '00' at No 1 cylinder's beginning of injection
(3)B.T.D.C.: aa
(4)-
----------
aa=18deg
----------
a=(110deg)
----------
aa=18deg
----------
a=(110deg)
Information:
If fuel line clamps are not installed in their exact location, vibration can cause the fuel lines to break and cause possible personal injury, or damage to the machine.
1. Disconnect front fuel injection lines (1), disconnect middle fuel injection lines (2) and rear fuel injection lines (3) from the fuel injection pump and the cylinder head assembly.2. Remove fuel injection lines (1), (2) and (3). Put caps or plugs on all fuel line connections to keep foreign material out of the fuel system.3. If a separation of the fuel lines has to be made, make sure the exact location of the clamps are marked for assembly purposes. Remove the clamps and make a separation of the fuel lines. The following steps are for the installation of the fuel injection lines.4. Remove the caps or plugs for the fuel injection line connections.5. If removed, connect the fuel lines with the clamps. Make sure the clamps are installed back in their correct location. Use Tool (A) to tighten the clamp bolts to a torque of 2.3 N m (20 lb in). For more information, see Specifications Manual SENR6470, of Testing & Adjusting Manual SENR6471.6. Install front fuel injection lines (1) on the fuel injection pump and cylinder head assembly.7 Install middle fuel injection lines (2) on the fuel injection pump and the cylinder head assembly.8. Install rear fuel injection lines (3) on the fuel injection pump and the cylinder head assembly.9. Tighten the fuel injection line nuts to a torque of 40 7 N m (30 5 lb ft).
Have questions with 104303-3360?
Group cross 104303-3360 ZEXEL
Toyo-Sha
Ishikawajima-S
Iseki
104303-3360
9 400 616 468
62156000130
INJECTION-PUMP ASSEMBLY
E3AD1
E3AD1