Information injection-pump assembly
ZEXEL
104302-5060
1043025060
KOMATSU
6140711042
6140711042
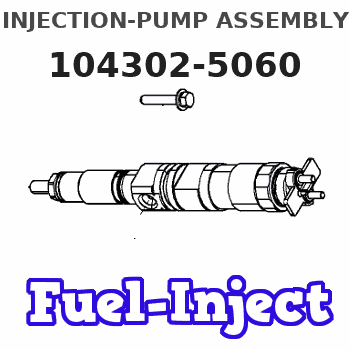
Rating:
Service parts 104302-5060 INJECTION-PUMP ASSEMBLY:
1.
_
3.
GOVERNOR
5.
AUTOM. ADVANCE MECHANIS
6.
COUPLING PLATE
7.
COUPLING PLATE
8.
_
9.
_
11.
Nozzle and Holder
6140-11-3103
12.
Open Pre:MPa(Kqf/cm2)
22.1{225}
15.
NOZZLE SET
Include in #1:
104302-5060
as INJECTION-PUMP ASSEMBLY
Cross reference number
ZEXEL
104302-5060
1043025060
KOMATSU
6140711042
6140711042
Zexel num
Bosch num
Firm num
Name
104302-5060
6140711042 KOMATSU
INJECTION-PUMP ASSEMBLY
2D92 * K
2D92 * K
Calibration Data:
Adjustment conditions
Test oil
1404 Test oil ISO4113 or {SAEJ967d}
1404 Test oil ISO4113 or {SAEJ967d}
Test oil temperature
degC
40
40
45
Nozzle and nozzle holder
105780-8140
Bosch type code
EF8511/9A
Nozzle
105780-0000
Bosch type code
DN12SD12T
Nozzle holder
105780-2080
Bosch type code
EF8511/9
Opening pressure
MPa
17.2
Opening pressure
kgf/cm2
175
Injection pipe
Outer diameter - inner diameter - length (mm) mm 6-2-600
Outer diameter - inner diameter - length (mm) mm 6-2-600
Tester oil delivery pressure
kPa
157
157
157
Tester oil delivery pressure
kgf/cm2
1.6
1.6
1.6
Direction of rotation (viewed from drive side)
Right R
Right R
Injection timing adjustment
Direction of rotation (viewed from drive side)
Right R
Right R
Injection order
1-2
Pre-stroke
mm
2.1
2.05
2.15
Beginning of injection position
Drive side NO.1
Drive side NO.1
Difference between angles 1
Cyl.1-2 deg. 90 89.5 90.5
Cyl.1-2 deg. 90 89.5 90.5
Injection quantity adjustment
Adjusting point
A
Rack position
7.4
Pump speed
r/min
600
600
600
Average injection quantity
mm3/st.
36
35
37
Max. variation between cylinders
%
0
-2
2
Basic
*
Fixing the lever
*
Injection quantity adjustment_02
Adjusting point
B
Rack position
7.1
Pump speed
r/min
900
900
900
Average injection quantity
mm3/st.
38.5
37
40
Max. variation between cylinders
%
0
-4
4
Fixing the lever
*
Injection quantity adjustment_03
Adjusting point
C
Rack position
6.5
Pump speed
r/min
1100
1100
1100
Average injection quantity
mm3/st.
34.5
33
36
Max. variation between cylinders
%
0
-4
4
Fixing the lever
*
Injection quantity adjustment_04
Adjusting point
D
Rack position
5+-0.5
Pump speed
r/min
350
350
350
Average injection quantity
mm3/st.
9
7.9
10.1
Max. variation between cylinders
%
0
-1.3
1.3
Fixing the rack
*
Test data Ex:
Governor adjustment
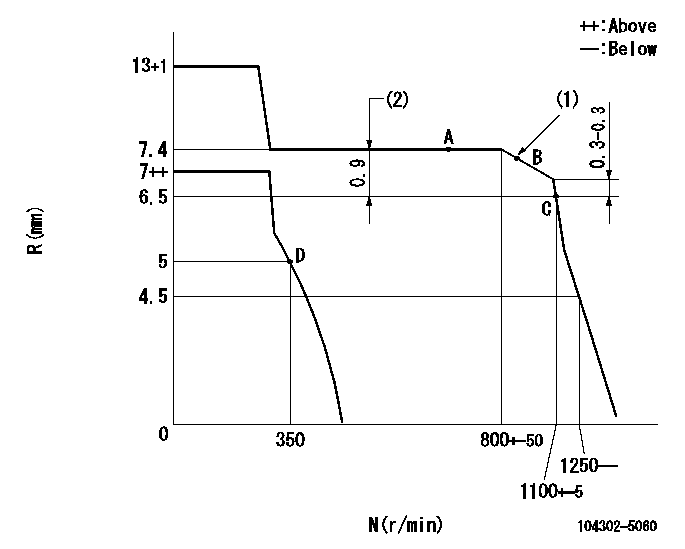
N:Pump speed
R:Rack position (mm)
(1)Set the torque control spring so that the injection quantity passes through point B.
(2)Torque control stroke
----------
----------
----------
----------
Speed control lever angle
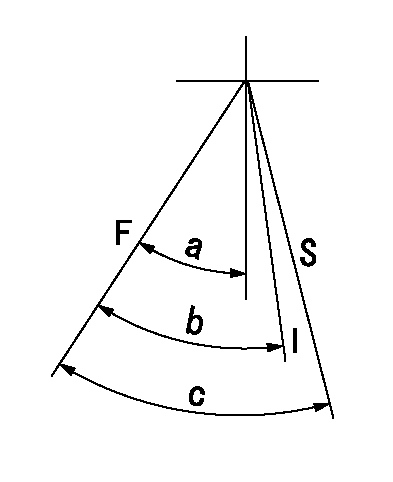
F:Full speed
I:Idle
S:Stop
----------
----------
a=30deg+-5deg b=32deg+-3deg c=38deg+-6deg
----------
----------
a=30deg+-5deg b=32deg+-3deg c=38deg+-6deg
Information:
ELC Cooling System Contamination
Mixing ELC with other products reduces the effectiveness of the ELC and shortens the ELC service life. Use only Caterpillar products or commercial products that have passed the Caterpillar EC-1 specification for premixed or concentrate coolants. Use only Caterpillar Extender with Caterpillar ELC. Failure to follow these recommendations can result in shortened cooling system component life.
ELC cooling systems can withstand contamination of up to ten percent of conventional HD coolant/antifreeze. If the contamination exceeds ten percent of the total system capacity, perform either one of the following two procedures: * Drain the cooling system. Flush the system with clean water. Refill the system with ELC.* Maintain the cooling system as if the system is filled with conventional HD coolant/antifreeze.Commercial ELC
If Caterpillar extended life coolant is not used, select a commercial extended life coolant that meets the Caterpillar EC-1 specification. Do not use a product that is labeled as an extended life coolant but does not meet the Caterpillar EC-1 specification. Follow the coolant maintenance guidelines of the commercial ELC supplier. In all cases, use distilled or deionized water or use water that has the properties listed in the Caterpillar Water Quality Limits chart.Caterpillar Diesel Engine Antifreeze/Coolant (DEAC)
Caterpillar recommends the use of Caterpillar Diesel Engine Antifreeze/Coolant (DEAC) in conventional HD cooling systems. DEAC is an alkaline type, single-phase, ethylene glycol-based antifreeze/coolant. DEAC contains inorganic corrosion inhibitors and antifoaming agents.Contact your Caterpillar dealer for part numbers and available container sizes.Caterpillar DEAC is available premixed with distilled water in a 50/50 concentration. If DEAC concentrate is used, Caterpillar recommends mixing the concentrate with distilled or deionized water. If distilled or deionized water is not available, use water that has the properties listed in the Caterpillar Water Quality Limits chart.Caterpillar Supplemental Coolant Additive (SCA)
Caterpillar Supplemental Coolant Additive (SCA) is effective in preventing corrosion on all metals. Caterpillar SCA also prevents the formation of mineral deposits, prevents liner cavitation, and eliminates coolant foaming.Caterpillar DEAC is formulated with the correct level of Caterpillar SCA. Additional SCA is NOT needed when the cooling system is initially filled with DEAC.Contact your Caterpillar dealer for part numbers and available container sizes.Commercial Heavy Duty (HD) Coolant/Antifreeze and SCA
If Caterpillar DEAC is not used, select a low silicate commercial HD coolant/antifreeze that meets ASTM D5345 or D4985 specifications.When a commercial HD coolant/antifreeze is used, the cooling system should be treated with three to six percent Caterpillar SCA by volume. Refer to the Caterpillar SCA Requirements for Heavy Duty Coolant/Antifreeze chart. If Caterpillar SCA is not used, select a commercial SCA. The commercial SCA must provide a minimum of 1200 mg/L or 1200 ppm (70 grains/US gal) nitrites in the final coolant mixture. Follow the coolant maintenance guidelines of the commercial SCA supplier.HD coolant/antifreezes that meet ASTM D5345 or D4985 specifications DO require SCA treatment at initial fill, and on a maintenance basis.When mixing concentrated coolants, use distilled or deionized water or use water that has the properties listed in the Caterpillar Water Quality Limits chart.Heavy Duty
Mixing ELC with other products reduces the effectiveness of the ELC and shortens the ELC service life. Use only Caterpillar products or commercial products that have passed the Caterpillar EC-1 specification for premixed or concentrate coolants. Use only Caterpillar Extender with Caterpillar ELC. Failure to follow these recommendations can result in shortened cooling system component life.
ELC cooling systems can withstand contamination of up to ten percent of conventional HD coolant/antifreeze. If the contamination exceeds ten percent of the total system capacity, perform either one of the following two procedures: * Drain the cooling system. Flush the system with clean water. Refill the system with ELC.* Maintain the cooling system as if the system is filled with conventional HD coolant/antifreeze.Commercial ELC
If Caterpillar extended life coolant is not used, select a commercial extended life coolant that meets the Caterpillar EC-1 specification. Do not use a product that is labeled as an extended life coolant but does not meet the Caterpillar EC-1 specification. Follow the coolant maintenance guidelines of the commercial ELC supplier. In all cases, use distilled or deionized water or use water that has the properties listed in the Caterpillar Water Quality Limits chart.Caterpillar Diesel Engine Antifreeze/Coolant (DEAC)
Caterpillar recommends the use of Caterpillar Diesel Engine Antifreeze/Coolant (DEAC) in conventional HD cooling systems. DEAC is an alkaline type, single-phase, ethylene glycol-based antifreeze/coolant. DEAC contains inorganic corrosion inhibitors and antifoaming agents.Contact your Caterpillar dealer for part numbers and available container sizes.Caterpillar DEAC is available premixed with distilled water in a 50/50 concentration. If DEAC concentrate is used, Caterpillar recommends mixing the concentrate with distilled or deionized water. If distilled or deionized water is not available, use water that has the properties listed in the Caterpillar Water Quality Limits chart.Caterpillar Supplemental Coolant Additive (SCA)
Caterpillar Supplemental Coolant Additive (SCA) is effective in preventing corrosion on all metals. Caterpillar SCA also prevents the formation of mineral deposits, prevents liner cavitation, and eliminates coolant foaming.Caterpillar DEAC is formulated with the correct level of Caterpillar SCA. Additional SCA is NOT needed when the cooling system is initially filled with DEAC.Contact your Caterpillar dealer for part numbers and available container sizes.Commercial Heavy Duty (HD) Coolant/Antifreeze and SCA
If Caterpillar DEAC is not used, select a low silicate commercial HD coolant/antifreeze that meets ASTM D5345 or D4985 specifications.When a commercial HD coolant/antifreeze is used, the cooling system should be treated with three to six percent Caterpillar SCA by volume. Refer to the Caterpillar SCA Requirements for Heavy Duty Coolant/Antifreeze chart. If Caterpillar SCA is not used, select a commercial SCA. The commercial SCA must provide a minimum of 1200 mg/L or 1200 ppm (70 grains/US gal) nitrites in the final coolant mixture. Follow the coolant maintenance guidelines of the commercial SCA supplier.HD coolant/antifreezes that meet ASTM D5345 or D4985 specifications DO require SCA treatment at initial fill, and on a maintenance basis.When mixing concentrated coolants, use distilled or deionized water or use water that has the properties listed in the Caterpillar Water Quality Limits chart.Heavy Duty
Have questions with 104302-5060?
Group cross 104302-5060 ZEXEL
Komatsu
104302-5060
6140711042
INJECTION-PUMP ASSEMBLY
2D92
2D92