Information injection-pump assembly
BOSCH
F 019 Z10 394
f019z10394
ZEXEL
103672-0380
1036720380
NIIGATA-URAWA
74V47060A
74v47060a
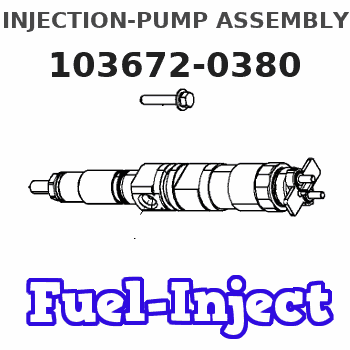
Rating:
Service parts 103672-0380 INJECTION-PUMP ASSEMBLY:
1.
_
5.
AUTOM. ADVANCE MECHANIS
6.
COUPLING PLATE
7.
COUPLING PLATE
8.
_
9.
_
10.
NOZZLE AND HOLDER ASSY
11.
Nozzle and Holder
12.
Open Pre:MPa(Kqf/cm2)
12.7{130}
15.
NOZZLE SET
Cross reference number
BOSCH
F 019 Z10 394
f019z10394
ZEXEL
103672-0380
1036720380
NIIGATA-URAWA
74V47060A
74v47060a
Zexel num
Bosch num
Firm num
Name
Calibration Data:
Adjustment conditions
Test oil
1404 Test oil ISO4113 or {SAEJ967d}
1404 Test oil ISO4113 or {SAEJ967d}
Test oil temperature
degC
40
40
45
Nozzle and nozzle holder
105780-8130
Bosch type code
EFEP215A
Nozzle
105780-0050
Bosch type code
DN6TD119NP1T
Nozzle holder
105780-2090
Bosch type code
EFEP215
Opening pressure
MPa
17.2
Opening pressure
kgf/cm2
175
Injection pipe
Outer diameter - inner diameter - length (mm) mm 8-4-1500
Outer diameter - inner diameter - length (mm) mm 8-4-1500
Overflow valve
131425-0120
Overflow valve opening pressure
kPa
157
123
191
Overflow valve opening pressure
kgf/cm2
1.6
1.25
1.95
Tester oil delivery pressure
kPa
157
157
157
Tester oil delivery pressure
kgf/cm2
1.6
1.6
1.6
Direction of rotation (viewed from drive side)
Left L
Left L
Injection timing adjustment
Direction of rotation (viewed from drive side)
Left L
Left L
Injection order
6-3-5-1-
4-2
Pre-stroke
mm
3
2.95
3.05
Beginning of injection position
Drive side NO.1
Drive side NO.1
Difference between angles 1
Cal 6-3 deg. 60 59.5 60.5
Cal 6-3 deg. 60 59.5 60.5
Difference between angles 2
Cal 6-5 deg. 120 119.5 120.5
Cal 6-5 deg. 120 119.5 120.5
Difference between angles 3
Cal 6-1 deg. 180 179.5 180.5
Cal 6-1 deg. 180 179.5 180.5
Difference between angles 4
Cal 6-4 deg. 240 239.5 240.5
Cal 6-4 deg. 240 239.5 240.5
Difference between angles 5
Cal 6-2 deg. 300 299.5 300.5
Cal 6-2 deg. 300 299.5 300.5
Injection quantity adjustment
Adjusting point
A
Rack position
14.5
Pump speed
r/min
500
500
500
Average injection quantity
mm3/st.
495
480
510
Max. variation between cylinders
%
0
-2
2
Basic
*
Fixing the rack
*
Injection quantity adjustment_02
Adjusting point
B
Rack position
6.7+-0.5
Pump speed
r/min
250
250
250
Average injection quantity
mm3/st.
41.5
38
45
Max. variation between cylinders
%
0
-10
10
Fixing the rack
*
Injection quantity adjustment_03
Adjusting point
C
Rack position
5.6+-0.5
Pump speed
r/min
500
500
500
Average injection quantity
mm3/st.
28
24.5
31.5
Max. variation between cylinders
%
0
-10
10
Fixing the rack
*
Test data Ex:
Governor adjustment
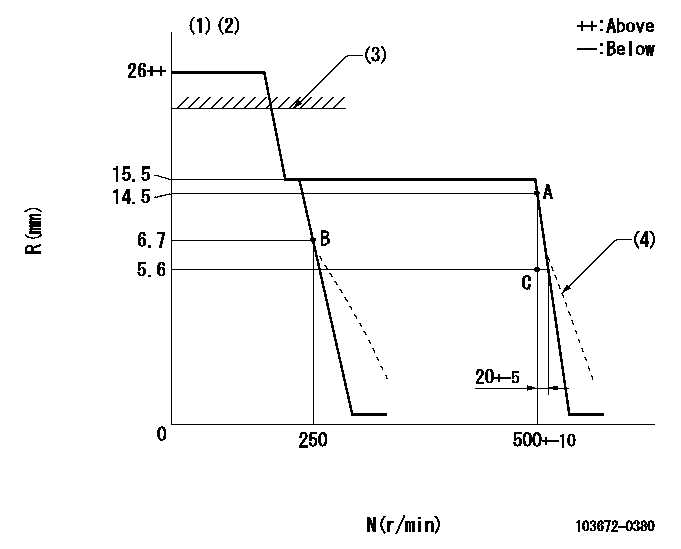
N:Pump speed
R:Rack position (mm)
(1)Target notch: K
(2)Delivered with idle spring not operating.
(3)RACK LIMIT: RAL
(4)Idle sub spring setting: L1.
----------
K=14 RAL=16.5+0.5mm L1=6.2-0.5mm
----------
----------
K=14 RAL=16.5+0.5mm L1=6.2-0.5mm
----------
Speed control lever angle
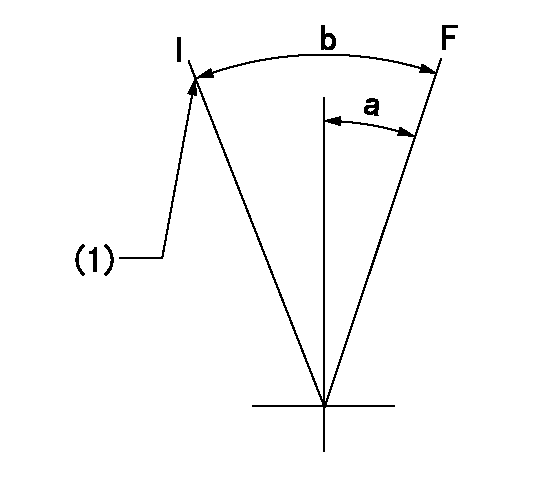
F:Full speed
I:Idle
(1)Stopper bolt setting
----------
----------
a=(12deg)+-5deg b=(25deg)+-5deg
----------
----------
a=(12deg)+-5deg b=(25deg)+-5deg
Stop lever angle
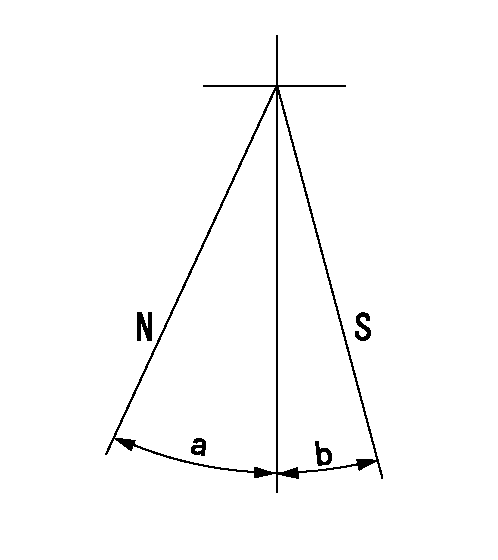
N:Pump normal
S:Stop the pump.
----------
----------
a=35deg+-5deg b=10deg+-5deg
----------
----------
a=35deg+-5deg b=10deg+-5deg
Timing setting
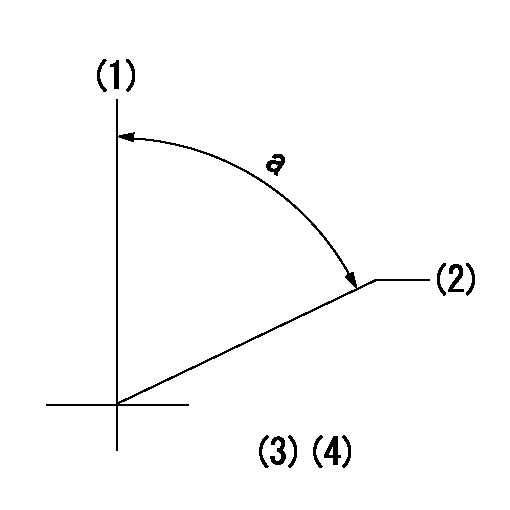
(1)Pump vertical direction
(2)Center of pump side coupling's elongated hole at No. 6 cylinder's beginning of injection.
(3)-
(4)-
----------
----------
a=(50deg)
----------
----------
a=(50deg)
Information:
TECHNICAL INFORMATION BULLETIN JAN. 15th, 2003
EXCAVATORS
WHEEL LOADERS
ENGINES 322C: (EMR, MAR);
325C: (CRB, CSJ, JLC, JLD, DTF)
950G II: (AYL, AYB);
962G II: (AYE, BAB)
3126B: (BMA)
Component Code(s) 1408SUBJECT: A NEW INJECTION ACTUATION PRESSURE CONTROL VALVE CONNECTOR INCREASES ENGINE OPERATION
PROBLEM:
The injection actuation pressure (IAP) control valve connector may have been assembled incorrectly on some 3126B engine harnesses. This can lead to intermittent engine operation or can cause the engine to stop.
SOLUTION:
If your machine exhibits symptoms of intermittent engine operation or abruptly stopping, the IAP control valve connector should be disconnected from the machine, examined for solenoid contact problems and re-installed using a correct procedure.
Procedure for installing the IAP control valve connector
This procedure will describe how to properly install the 232-4367 Harness.
Required Parts
Qty Part Number Description
1 232-4367 Harness
Procure the part that is listed in the table.
Illustration 1. Left Side of a 3126B Engine on a D6N.
(1) IAP Control Valve
(2) IAP Control Valve Connector
Note: Illustration 1 is from a D6N that is equipped with a 3126B for photographical purposes. The location of the IAP Control Valve is the same for your machine.
Disconnect the IAP control valve connector (2) from the IAP Control Valve (1). See Illustration 1.
Cut the two wires directly behind the connector.
Using wire strippers, strip the ends of the two wires.
Install the 232-4367 Harness, by crimping the stripped wires inside the splice.
Note: Take care to connect the pink wire to the pink wire on one hand and the purple wire to the purple wire on the other hand.
Heat both heat shrinkable tubes in order to insulate both the splices.
Reconnect the repaired harness to the IAP Control Valve (1).
COPYRIGHT 2003 CATERPILLAR
ALL RIGHTS RESERVED