Information injection-pump assembly
ZEXEL
102700-0150
1027000150
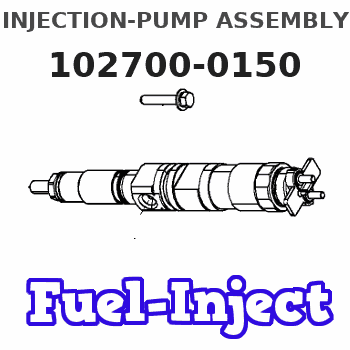
Rating:
Service parts 102700-0150 INJECTION-PUMP ASSEMBLY:
1.
_
6.
COUPLING PLATE
7.
COUPLING PLATE
8.
_
9.
_
11.
Nozzle and Holder
12.
Open Pre:MPa(Kqf/cm2)
21.6{220}
15.
NOZZLE SET
Cross reference number
ZEXEL
102700-0150
1027000150
Zexel num
Bosch num
Firm num
Name
102700-0150
DPICO
INJECTION-PUMP ASSEMBLY
K-1 * Q
K-1 * Q
Calibration Data:
Adjustment conditions
Test oil
1404 Test oil ISO4113 or {SAEJ967d}
1404 Test oil ISO4113 or {SAEJ967d}
Test oil temperature
degC
40
40
45
Nozzle and nozzle holder
105780-8140
Bosch type code
EF8511/9A
Nozzle
105780-0000
Bosch type code
DN12SD12T
Nozzle holder
105780-2080
Bosch type code
EF8511/9
Opening pressure
MPa
17.2
Opening pressure
kgf/cm2
175
Injection pipe
Outer diameter - inner diameter - length (mm) mm 6-2-600
Outer diameter - inner diameter - length (mm) mm 6-2-600
Overflow valve
131424-6220
Overflow valve opening pressure
kPa
255
221
289
Overflow valve opening pressure
kgf/cm2
2.6
2.25
2.95
Tester oil delivery pressure
kPa
157
157
157
Tester oil delivery pressure
kgf/cm2
1.6
1.6
1.6
Direction of rotation (viewed from drive side)
Right R
Right R
Injection timing adjustment
Direction of rotation (viewed from drive side)
Right R
Right R
Injection order
1-3-4-2
Pre-stroke
mm
3.6
3.55
3.65
Beginning of injection position
Drive side NO.1
Drive side NO.1
Difference between angles 1
Cal 1-3 deg. 90 89.5 90.5
Cal 1-3 deg. 90 89.5 90.5
Difference between angles 2
Cal 1-4 deg. 180 179.5 180.5
Cal 1-4 deg. 180 179.5 180.5
Difference between angles 3
Cyl.1-2 deg. 270 269.5 270.5
Cyl.1-2 deg. 270 269.5 270.5
Injection quantity adjustment
Adjusting point
-
Rack position
10.7
Pump speed
r/min
1000
1000
1000
Each cylinder's injection qty
mm3/st.
53.5
52.1
54.9
Basic
*
Fixing the rack
*
Standard for adjustment of the maximum variation between cylinders
*
Injection quantity adjustment_02
Adjusting point
H
Rack position
9.5+-0.5
Pump speed
r/min
300
300
300
Each cylinder's injection qty
mm3/st.
8
6.7
9.3
Fixing the rack
*
Standard for adjustment of the maximum variation between cylinders
*
Injection quantity adjustment_03
Adjusting point
A
Rack position
R1(10.7)
Pump speed
r/min
1000
1000
1000
Average injection quantity
mm3/st.
53.5
52.5
54.5
Basic
*
Fixing the lever
*
Injection quantity adjustment_04
Adjusting point
B
Rack position
R1(10.7)
Pump speed
r/min
1700
1700
1700
Average injection quantity
mm3/st.
57
53
61
Fixing the lever
*
Injection quantity adjustment_05
Adjusting point
C
Rack position
R1-0.1
Pump speed
r/min
680
680
680
Average injection quantity
mm3/st.
44.5
42.5
46.5
Fixing the lever
*
Injection quantity adjustment_06
Adjusting point
I
Rack position
-
Pump speed
r/min
100
100
100
Average injection quantity
mm3/st.
67
67
72
Fixing the lever
*
Rack limit
*
Timer adjustment
Pump speed
r/min
1400
Advance angle
deg.
0.5
Load
3/4
Timer adjustment_02
Pump speed
r/min
1750
Advance angle
deg.
6
5.5
6.5
Load
4/4
Remarks
Finish
Finish
Test data Ex:
Governor adjustment
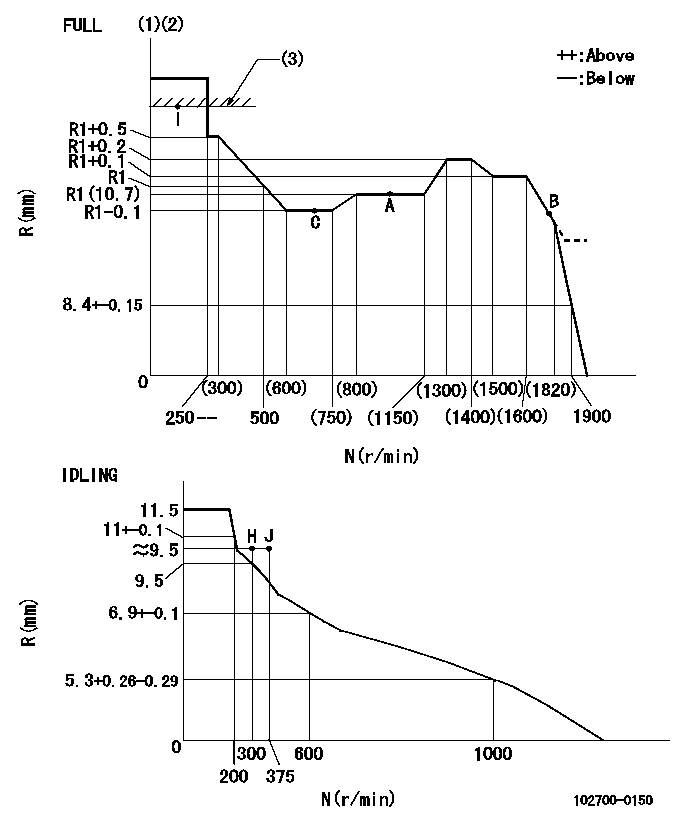
N:Pump speed
R:Rack position (mm)
(1)Torque cam stamping: T1
(2)Tolerance for racks not indicated: +-0.05mm.
(3)RACK LIMIT
----------
T1=G93
----------
----------
T1=G93
----------
Speed control lever angle

F:Full speed
I:Idle
(1)Use the hole at R = aa
(2)Stopper bolt set position 'H'
----------
aa=40mm
----------
a=26deg+-5deg b=(44deg)+-3deg
----------
aa=40mm
----------
a=26deg+-5deg b=(44deg)+-3deg
Stop lever angle
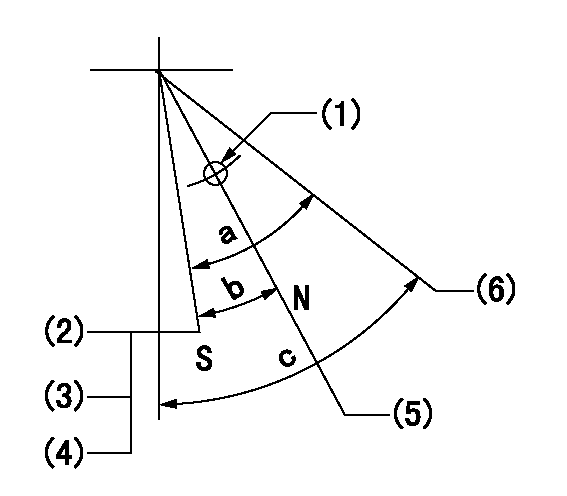
N:Engine manufacturer's normal use
S:Stop the pump.
(1)Use the hole at R = aa
(2)Set the stopper bolt at speed = bb and rack position = cc (non-injection rack position). Confirm non-injection.
(3)After setting the stopper bolt, confirm non-injection at speed = dd and rack position = not exceeding ee.
(4)-
(5)Rack position corresponding to ff
(6)Free (at delivery)
----------
aa=40mm bb=1750r/min cc=(6.2)-0.5mm dd=300r/min ee=(8)mm ff=16mm
----------
a=25deg+-5deg b=20deg+-5deg c=35deg+-5deg
----------
aa=40mm bb=1750r/min cc=(6.2)-0.5mm dd=300r/min ee=(8)mm ff=16mm
----------
a=25deg+-5deg b=20deg+-5deg c=35deg+-5deg
Timing setting

(1)Pump vertical direction
(2)Position of gear mark '3' at No 1 cylinder's beginning of injection
(3)B.T.D.C.: aa
(4)-
----------
aa=10deg
----------
a=(130deg)
----------
aa=10deg
----------
a=(130deg)
Information:
Termination Date
January 31, 1993Problem
The fuel injection pumps used on certain Remanufactured 1160 and 3208 Engines need to be inspected for gummy deposits.
Affected Product
Model & Identification Number
1160 (57V1-34325)
3208 (9WC1-730; 5CD1-5868; 62W1-68596; 93Z1-8374)
Remanufactured Fuel Pump Part Numbers
0R07660R09030R23840R23860R09020R23740R23850R2877 The above list of remanufactured pumps are affected only if they are stamped with a date code of 12/91 (UMDU) or earlier.
Parts Needed
Not Applicable
Action Required
Before installing or delivering any of the affected product, perform the following steps to ensure the internal fuel injection pump components are not stuck due to fuel pump gumming:
1. Remove the top cover of the fuel injection pump and check to ensure that all sleeves and levers are free and there are no gummy deposits on any of these components.2. If inspection performed in Step 1 indicates everything is clean, install top cover and return to parts stock.3. If inspection reveals components have gummy deposits, remove 12 ounces of fuel from the fuel pump housing and replace it with: - Fuel Injector Cleaner or
- Carburetor/Choke Cleaner
4. Allow the components to soak in cleaning solution for 45 minutes, then rotate the engine crankshaft to rotate the fuel injection pump (on pumps only, rotate the fuel pump camshaft). This will ensure the components have the gummy deposits removed. If the engine or fuel pump will be used immediately, install the cover on the fuel injection pump, and install or deliver the engine or pump.5. If the engine or fuel pump will be returned to stock, DO NOT leave the fuel injection pump full of cleaning solution because it may not contain any rust inhibitors. Remove the cleaning solution, fill the fuel injector pump with clean diesel fuel, and install the cover on the pump.Service Claim Allowances
It is a .5-hr. job to inspect the pump. An additional .5-hr. may be claimed if cleaning is required.
Parts Disposition
Handle the parts in accordance with your Warranty Bulletin on warranty parts handling.
January 31, 1993Problem
The fuel injection pumps used on certain Remanufactured 1160 and 3208 Engines need to be inspected for gummy deposits.
Affected Product
Model & Identification Number
1160 (57V1-34325)
3208 (9WC1-730; 5CD1-5868; 62W1-68596; 93Z1-8374)
Remanufactured Fuel Pump Part Numbers
0R07660R09030R23840R23860R09020R23740R23850R2877 The above list of remanufactured pumps are affected only if they are stamped with a date code of 12/91 (UMDU) or earlier.
Parts Needed
Not Applicable
Action Required
Before installing or delivering any of the affected product, perform the following steps to ensure the internal fuel injection pump components are not stuck due to fuel pump gumming:
1. Remove the top cover of the fuel injection pump and check to ensure that all sleeves and levers are free and there are no gummy deposits on any of these components.2. If inspection performed in Step 1 indicates everything is clean, install top cover and return to parts stock.3. If inspection reveals components have gummy deposits, remove 12 ounces of fuel from the fuel pump housing and replace it with: - Fuel Injector Cleaner or
- Carburetor/Choke Cleaner
4. Allow the components to soak in cleaning solution for 45 minutes, then rotate the engine crankshaft to rotate the fuel injection pump (on pumps only, rotate the fuel pump camshaft). This will ensure the components have the gummy deposits removed. If the engine or fuel pump will be used immediately, install the cover on the fuel injection pump, and install or deliver the engine or pump.5. If the engine or fuel pump will be returned to stock, DO NOT leave the fuel injection pump full of cleaning solution because it may not contain any rust inhibitors. Remove the cleaning solution, fill the fuel injector pump with clean diesel fuel, and install the cover on the pump.Service Claim Allowances
It is a .5-hr. job to inspect the pump. An additional .5-hr. may be claimed if cleaning is required.
Parts Disposition
Handle the parts in accordance with your Warranty Bulletin on warranty parts handling.
Have questions with 102700-0150?
Group cross 102700-0150 ZEXEL
Dpico
Dpico
Hyundai
Dpico
Hyundai
Dpico
102700-0150
INJECTION-PUMP ASSEMBLY
K-1
K-1