Information injection-pump assembly
BOSCH
9 400 616 215
9400616215
ZEXEL
101803-1750
1018031750
MITSUBISHI
ME060671
me060671
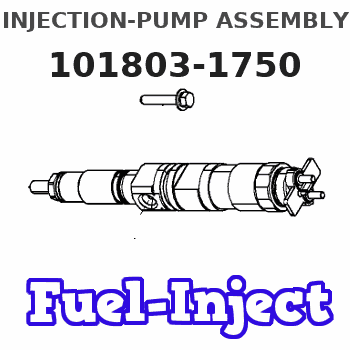
Rating:
Service parts 101803-1750 INJECTION-PUMP ASSEMBLY:
1.
_
7.
COUPLING PLATE
8.
_
9.
_
11.
Nozzle and Holder
12.
Open Pre:MPa(Kqf/cm2)
21.6(220)
13.
NOZZLE-HOLDER
15.
NOZZLE SET
Cross reference number
BOSCH
9 400 616 215
9400616215
ZEXEL
101803-1750
1018031750
MITSUBISHI
ME060671
me060671
Zexel num
Bosch num
Firm num
Name
9 400 616 215
ME060671 MITSUBISHI
INJECTION-PUMP ASSEMBLY
8DC82 K 14BH INJECTION PUMP ASSY PE8AD PE
8DC82 K 14BH INJECTION PUMP ASSY PE8AD PE
Calibration Data:
Adjustment conditions
Test oil
1404 Test oil ISO4113 or {SAEJ967d}
1404 Test oil ISO4113 or {SAEJ967d}
Test oil temperature
degC
40
40
45
Nozzle and nozzle holder
105780-8140
Bosch type code
EF8511/9A
Nozzle
105780-0000
Bosch type code
DN12SD12T
Nozzle holder
105780-2080
Bosch type code
EF8511/9
Opening pressure
MPa
17.2
Opening pressure
kgf/cm2
175
Injection pipe
Outer diameter - inner diameter - length (mm) mm 6-2-600
Outer diameter - inner diameter - length (mm) mm 6-2-600
Overflow valve opening pressure
kPa
157
123
191
Overflow valve opening pressure
kgf/cm2
1.6
1.25
1.95
Tester oil delivery pressure
kPa
157
157
157
Tester oil delivery pressure
kgf/cm2
1.6
1.6
1.6
Direction of rotation (viewed from drive side)
Right R
Right R
Injection timing adjustment
Direction of rotation (viewed from drive side)
Right R
Right R
Injection order
1-2-7-3-
4-5-6-8
Pre-stroke
mm
4.5
4.45
4.55
Beginning of injection position
Governor side NO.1
Governor side NO.1
Difference between angles 1
Cyl.1-2 deg. 45 44.5 45.5
Cyl.1-2 deg. 45 44.5 45.5
Difference between angles 2
Cal 1-7 deg. 90 89.5 90.5
Cal 1-7 deg. 90 89.5 90.5
Difference between angles 3
Cal 1-3 deg. 135 134.5 135.5
Cal 1-3 deg. 135 134.5 135.5
Difference between angles 4
Cal 1-4 deg. 180 179.5 180.5
Cal 1-4 deg. 180 179.5 180.5
Difference between angles 5
Cal 1-5 deg. 225 224.5 225.5
Cal 1-5 deg. 225 224.5 225.5
Difference between angles 6
Cal 1-6 deg. 270 269.5 270.5
Cal 1-6 deg. 270 269.5 270.5
Difference between angles 7
Cal 1-8 deg. 315 314.5 315.5
Cal 1-8 deg. 315 314.5 315.5
Injection quantity adjustment
Adjusting point
A
Rack position
7.6
Pump speed
r/min
900
900
900
Average injection quantity
mm3/st.
97.2
93.7
100.7
Max. variation between cylinders
%
0
-3
3
Basic
*
Fixing the lever
*
Injection quantity adjustment_02
Adjusting point
B
Rack position
6.3+-0.5
Pump speed
r/min
275
275
275
Average injection quantity
mm3/st.
18
15.4
20.6
Max. variation between cylinders
%
0
-15
15
Fixing the rack
*
Timer adjustment
Pump speed
r/min
550--
Advance angle
deg.
0
0
0
Remarks
Start
Start
Timer adjustment_02
Pump speed
r/min
500
Advance angle
deg.
0.5
Timer adjustment_03
Pump speed
r/min
800
Advance angle
deg.
1.6
1.1
2.1
Timer adjustment_04
Pump speed
r/min
1100
Advance angle
deg.
4
3.5
4.5
Timer adjustment_05
Pump speed
r/min
-
Advance angle
deg.
6.5
6.5
6.5
Remarks
Measure the actual speed, stop
Measure the actual speed, stop
Test data Ex:
Governor adjustment
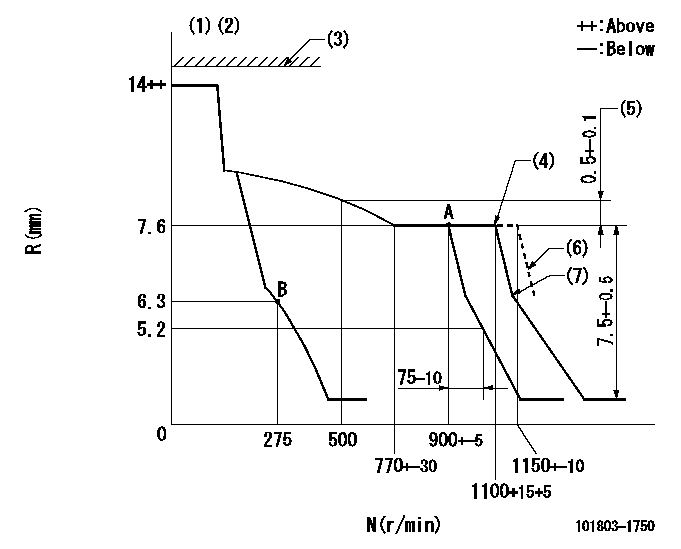
N:Pump speed
R:Rack position (mm)
(1)Target notch: K
(2)The torque control spring must does not have a set force.
(3)RACK LIMIT not operating.
(4)Torque spring does not operate.
(5)Rack difference between N = N1 and N = N2
(6)At shipping
(7)Idle sub spring setting: L1.
----------
K=18 N1=900r/min N2=500r/min L1=6+-0.1mm
----------
----------
K=18 N1=900r/min N2=500r/min L1=6+-0.1mm
----------
Speed control lever angle
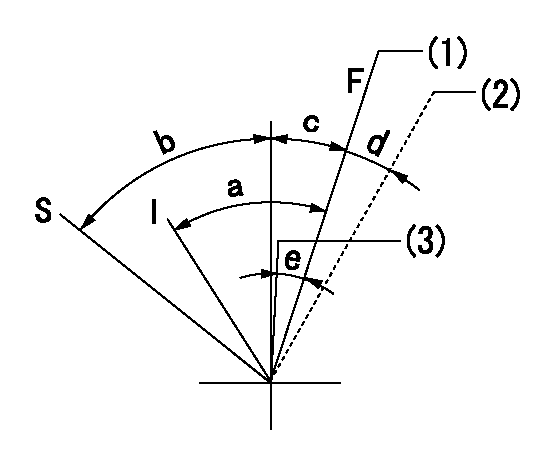
F:Full speed
I:Idle
S:Stop
(1)-
(2)At shipping
(3)Pump speed = aa
----------
aa=900r/min
----------
a=28deg+-5deg b=32deg+-3deg c=16deg+-5deg d=(2deg) e=7deg+-5deg
----------
aa=900r/min
----------
a=28deg+-5deg b=32deg+-3deg c=16deg+-5deg d=(2deg) e=7deg+-5deg
Stop lever angle

N:Pump normal
S:Stop the pump.
----------
----------
a=19deg+-5deg b=46deg+-5deg
----------
----------
a=19deg+-5deg b=46deg+-5deg
Timing setting

(1)Pump vertical direction
(2)Coupling's key groove position at No 1 cylinder's beginning of injection
(3)-
(4)-
----------
----------
a=(40deg)
----------
----------
a=(40deg)
Information:
Do not operate or work on this machine unless you have read and understand the instructions and warnings in the Operation and Maintenance Manual. Failure to follow the instructions or heed the warnings could result in injury or death. Contact your Caterpillar dealer for replacement manuals. Proper care is your responsibility.
Personal injury or death can result from improper assembly procedures.Do not attempt any assembly until you have read and understand the assembly instructions.
Accidental engine starting can cause injury or death to personnel working on the equipment.To avoid accidental engine starting, disconnect the battery cable from the negative (−) battery terminal. Completely tape all metal surfaces of the disconnected battery cable end in order to prevent contact with other metal surfaces which could activate the engine electrical system.Place a Do Not Operate tag at the Start/Stop switch location to inform personnel that the equipment is being worked on.
Required Parts
Table 1
Required Tools
Tool Part Number Part Name Qty
A 9S-9150 Terminal Crimp Tool As 1
B 9U-6070 Heat Gun Gp 1 Removal of a Connector from the Wire Harness
The following steps can be used to remove a connector for an injector on the wire harness.
Identify the connectors that need to be replaced. Wiring for the injector solenoid is not sensitive to polarity.
Illustration 1 g06093848
Connectors that are cut from the wire harness
Each injector will have two connectors. The wire on one connector will be longer than the other. Wire (A) is identified as the longer wire and wire (B) is identified as the shorter wire.
Cut wire (2) at a distance of 50 mm (1.9 inch) from the rear surface of the connector.
Cut wire (1) at a distance of 5 mm (0.2 inch) from the cut made on wire (2).
Illustration 2 g01111314
Wire from the harness for side (B) on the connector.
Wire from the harness for side (A) on the connector.Note: The wires on the old connector are cut to length so that the wires on the wire harness will match up to the new connector. Cutting the wires to the proper length will aid in matching the harness wires to the wires on the new connector.
Discard the old connectors.Installation of a New Connector
The following steps can be used to install a new connector for an injector on the wire harness that is located under the valve mechanism cover.
Use Tool (A) to remove 5 mm (0.2 inch) of the plastic from wires (3) and (4).
Illustration 3 g06125254
Connecting the connector to the wire harness
(A) Side (A) of the new connector
(B) Side (B) of the new connector
(3) Wire from the harness for side (B) on the new connector
(4) Wire from the harness for side (A) on the new connector
(5) Heat shrink tubes
(6) Butt splice on the wire that is on side (A) of the new connector
(7) Butt splice on the wire that is on side (B) of the new connector
Use heat shrink tubes (5) from the 257-4183 Injector Wiring Harness Kit. Slide the heat shrink tubes toward the connector to expose the butt splices.
Insert wire (4) into