Information injection-pump assembly
BOSCH
9 400 616 199
9400616199
ZEXEL
101701-9530
1017019530
NISSAN-DIESEL
16714Z6070
16714z6070
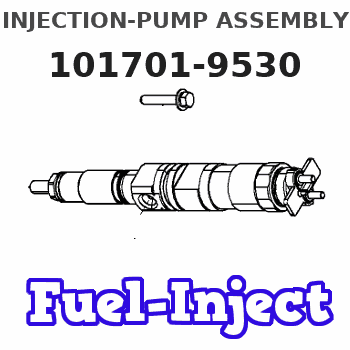
Rating:
Include in #1:
106871-2700
as _
Cross reference number
BOSCH
9 400 616 199
9400616199
ZEXEL
101701-9530
1017019530
NISSAN-DIESEL
16714Z6070
16714z6070
Zexel num
Bosch num
Firm num
Name
101701-9530
9 400 616 199
16714Z6070 NISSAN-DIESEL
INJECTION-PUMP ASSEMBLY
MD92 K
MD92 K
Calibration Data:
Adjustment conditions
Test oil
1404 Test oil ISO4113 or {SAEJ967d}
1404 Test oil ISO4113 or {SAEJ967d}
Test oil temperature
degC
40
40
45
Nozzle and nozzle holder
105780-8310
Nozzle
105780-0120
Bosch type code
1 688 901 990
Nozzle holder
105780-2240
Opening pressure
MPa
18
Opening pressure
kgf/cm2
184
Injection pipe
Outer diameter - inner diameter - length (mm) mm 6-2-600
Outer diameter - inner diameter - length (mm) mm 6-2-600
Overflow valve
134424-4120
Overflow valve opening pressure
kPa
255
221
289
Overflow valve opening pressure
kgf/cm2
2.6
2.25
2.95
Tester oil delivery pressure
kPa
255
255
255
Tester oil delivery pressure
kgf/cm2
2.6
2.6
2.6
Direction of rotation (viewed from drive side)
Left L
Left L
Injection timing adjustment
Direction of rotation (viewed from drive side)
Left L
Left L
Injection order
1-4-2-6-
3-5
Pre-stroke
mm
3.5
3.47
3.53
Beginning of injection position
Governor side NO.1
Governor side NO.1
Difference between angles 1
Cal 1-4 deg. 60 59.75 60.25
Cal 1-4 deg. 60 59.75 60.25
Difference between angles 2
Cyl.1-2 deg. 120 119.75 120.25
Cyl.1-2 deg. 120 119.75 120.25
Difference between angles 3
Cal 1-6 deg. 180 179.75 180.25
Cal 1-6 deg. 180 179.75 180.25
Difference between angles 4
Cal 1-3 deg. 240 239.75 240.25
Cal 1-3 deg. 240 239.75 240.25
Difference between angles 5
Cal 1-5 deg. 300 299.75 300.25
Cal 1-5 deg. 300 299.75 300.25
Injection quantity adjustment
Adjusting point
-
Rack position
12.6
Pump speed
r/min
700
700
700
Average injection quantity
mm3/st.
56
54
58
Max. variation between cylinders
%
0
-3.5
3.5
Basic
*
Fixing the rack
*
Standard for adjustment of the maximum variation between cylinders
*
Injection quantity adjustment_02
Adjusting point
Z
Rack position
9.7+-0.5
Pump speed
r/min
325
325
325
Average injection quantity
mm3/st.
13
12
14
Max. variation between cylinders
%
0
-8
8
Fixing the rack
*
Standard for adjustment of the maximum variation between cylinders
*
Injection quantity adjustment_03
Adjusting point
A
Rack position
R1(12.6)
Pump speed
r/min
700
700
700
Average injection quantity
mm3/st.
56
55
57
Basic
*
Fixing the lever
*
Injection quantity adjustment_04
Adjusting point
B
Rack position
R1+1.3
Pump speed
r/min
1300
1300
1300
Average injection quantity
mm3/st.
61.5
57.5
65.5
Fixing the lever
*
Timer adjustment
Pump speed
r/min
(N1+50)-
-
Advance angle
deg.
0
0
0
Remarks
Start
Start
Timer adjustment_02
Pump speed
r/min
N1
Advance angle
deg.
0.3
Remarks
Measure the actual speed.
Measure the actual speed.
Timer adjustment_03
Pump speed
r/min
-
Advance angle
deg.
4
3.7
4.3
Remarks
Measure the actual speed, stop
Measure the actual speed, stop
Test data Ex:
Governor adjustment
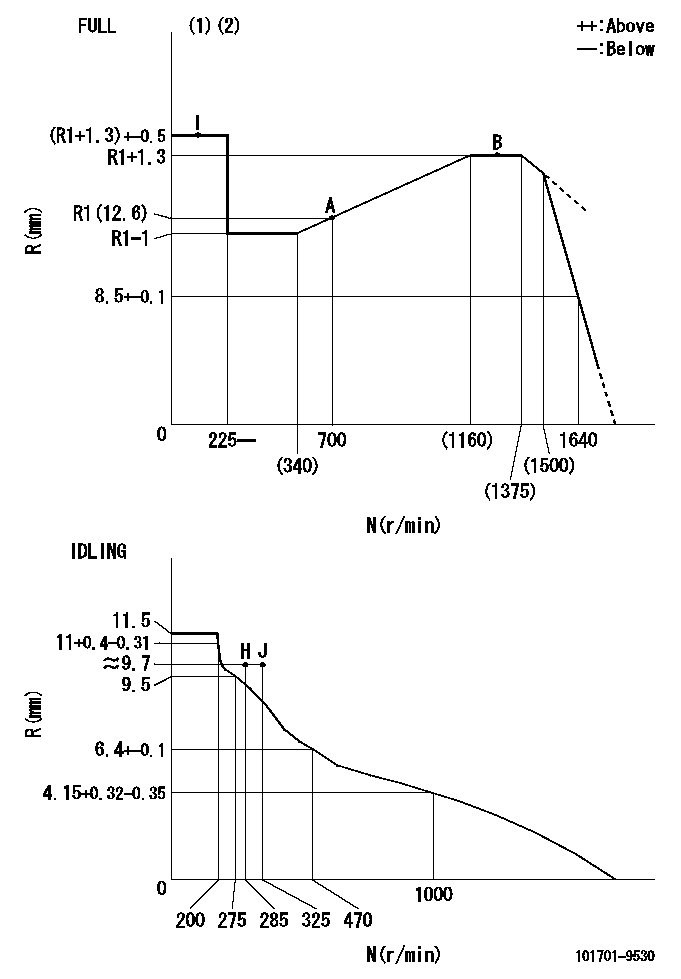
N:Pump speed
R:Rack position (mm)
(1)Torque cam stamping: T1
(2)Tolerance for racks not indicated: +-0.05mm.
----------
T1=N94
----------
----------
T1=N94
----------
Speed control lever angle
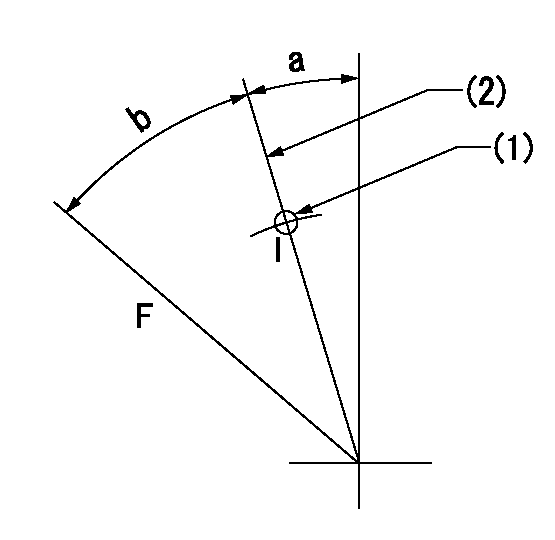
F:Full speed
I:Idle
(1)Use the hole at R = aa
(2)Stopper bolt set position 'H'
----------
aa=36mm
----------
a=8deg+-5deg b=43deg+-3deg
----------
aa=36mm
----------
a=8deg+-5deg b=43deg+-3deg
Stop lever angle
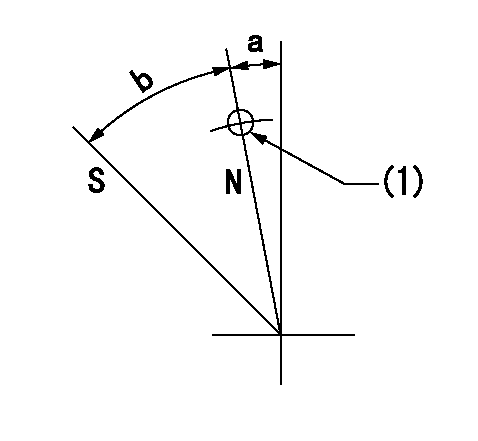
N:Pump normal
S:Stop the pump.
(1)Use the pin at R = aa
----------
aa=42mm
----------
a=5deg+-5deg b=40deg+-5deg
----------
aa=42mm
----------
a=5deg+-5deg b=40deg+-5deg
0000001501 RACK SENSOR

G:Red paint
H:Pump end face
P/N: part number of suitable shim
(1)Threaded type rack block
(2)Welded type rack block
Rack sensor adjustment
1. Threaded type rack sensor (-5*20, P type, no TICS rack limit).
(1)Screw in the bobbin (A) until it contacts the joint (B).
(2)Fix the pump lever.
(3)At speed N1 and rack position Ra, adjust the amount that the bobbin is screwed in so that the amp's output voltage is V1.
(4)Fix using the nut (F).
(5)Affix the caution plate to the upper part of the joint (B).
(6)Apply (G) at two places.
Connecting part between the joint (B) and the nut (F)
Connecting part between the end surface of the pump (H) and the joint (B)
2. Range for screw-in adjustment between the bobbin (A) and the joint (B) is 9 threads.
Screw in to the end from (the position where the bobbin (A) is rotated 9 turns).
Speed N1, rack position Ra, output voltage V1, rack sensor supply voltage 5+-0.01 (V)
----------
Ra=R1(12.6)mm N1=700r/min V1=2.6+-0.01V
----------
----------
Ra=R1(12.6)mm N1=700r/min V1=2.6+-0.01V
----------
Timing setting

(1)Pump vertical direction
(2)Coupling's key groove position at No 1 cylinder's beginning of injection
(3)-
(4)-
----------
----------
a=(10deg)
----------
----------
a=(10deg)
Information:
Failure to follow these oil recommendations can cause shortened engine service life due to deposits and/or excessive wear.
Total Base Number (TBN) and Fuel Sulfur Levels for Direct Injection (DI) Diesel Engines
The Total Base Number (TBN) for an oil depends on the fuel sulfur level. For direct injection engines that use distillate fuel, the minimum TBN must be 10 times the fuel sulfur level. The TBN is determined by the "ASTM D2896" procedure. The minimum TBN of the oil is 5 regardless of a low fuel sulfur level. Illustration 1 demonstrates the TBN.
Illustration 1 g00104890
(Y) TBN by "ASTM D2896"
(X) Percentage of fuel sulfur by weight
(1) TBN of new oil
(2) Change the used oil when the TBN reaches this level. Use the following guidelines for fuel sulfur levels that exceed 1.5 percent:
Choose an oil with the highest TBN that meets one of these classifications:
API CG-4
API CH-4
API CI-4Note: API CH-4 oils and API CI-4 oils are acceptable if the requirements of Caterpillar's ECF-1 (Engine Crankcase Fluid specification-1) are met. CH-4 oils and CI-4 oils that have not met the requirements of Caterpillar's ECF-1 Specification may cause reduced engine life.
Reduce the oil change interval. Base the oil change interval on the oil analysis. Ensure that the oil analysis includes the condition of the oil and a wear metal analysis. Excessive piston deposits can be produced by an oil with a high TBN. These deposits can lead to a loss of control of the oil consumption and to the polishing of the cylinder bore.
Operating Direct Injection (DI) diesel engines with fuel sulfur levels over 1.0 percent may require shortened oil change intervals in order to help maintain adequate wear protection.
Lubricant Viscosity Recommendations for Direct Injection (DI) Diesel Engines
The proper SAE viscosity grade of oil is determined by the minimum ambient temperature during cold engine start-up, and the maximum ambient temperature during engine operation. Refer to Table 1 (minimum temperature) in order to determine the required oil viscosity for starting a cold engine.Refer to Table 1 (maximum temperature) in order to select the oil viscosity for engine operation at the highest ambient temperature that is anticipated.Note: Generally, use the highest oil viscosity that is available to meet the requirement for the temperature at start-up.If ambient temperature conditions at engine start-up require the use of multigrade SAE 0W oil, SAE 0W-40 viscosity grade is generally preferred over SAE 0W-20 or SAE 0W-30.Note: SAE 10W-30 is the preferred viscosity grade for the following diesel engines when the ambient temperature is above −18 °C (0 °F), and below 40 °C (104 °F).
C7
C-9
C9
3116
3126When an engine is started and an engine is operated in ambient temperatures below −20 °C (−4 °F), use multigrade oils that are capable of flowing in low temperatures.These oils have lubricant viscosity grades of SAE 0W or SAE 5W.When an engine is started and operated in ambient temperatures below −30 °C (−22 °F), use a synthetic base stock multigrade oil with a 0W viscosity grade or with a 5W viscosity grade. Use an oil with a
Have questions with 101701-9530?
Group cross 101701-9530 ZEXEL
Nissan-Diesel
101701-9530
9 400 616 199
16714Z6070
INJECTION-PUMP ASSEMBLY
MD92
MD92