Information injection-pump assembly
BOSCH
9 400 616 190
9400616190
ZEXEL
101701-9351
1017019351
NISSAN-DIESEL
16714Z5666
16714z5666
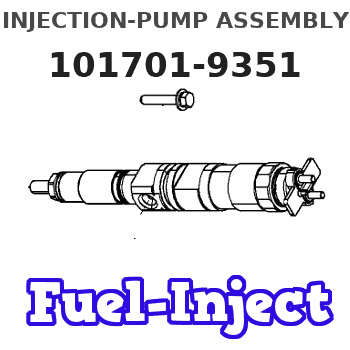
Rating:
Include in #1:
106871-2630
as _
Cross reference number
BOSCH
9 400 616 190
9400616190
ZEXEL
101701-9351
1017019351
NISSAN-DIESEL
16714Z5666
16714z5666
Zexel num
Bosch num
Firm num
Name
101701-9351
9 400 616 190
16714Z5666 NISSAN-DIESEL
INJECTION-PUMP ASSEMBLY
FE6A K
FE6A K
Calibration Data:
Adjustment conditions
Test oil
1404 Test oil ISO4113 or {SAEJ967d}
1404 Test oil ISO4113 or {SAEJ967d}
Test oil temperature
degC
40
40
45
Nozzle and nozzle holder
105780-8310
Nozzle
105780-0120
Bosch type code
1 688 901 990
Nozzle holder
105780-2240
Opening pressure
MPa
18
Opening pressure
kgf/cm2
184
Injection pipe
Outer diameter - inner diameter - length (mm) mm 6-2-600
Outer diameter - inner diameter - length (mm) mm 6-2-600
Overflow valve
131424-8120
Overflow valve opening pressure
kPa
255
255
255
Overflow valve opening pressure
kgf/cm2
2.6
2.6
2.6
Tester oil delivery pressure
kPa
255
255
255
Tester oil delivery pressure
kgf/cm2
2.6
2.6
2.6
Direction of rotation (viewed from drive side)
Right R
Right R
Injection timing adjustment
Direction of rotation (viewed from drive side)
Right R
Right R
Injection order
1-4-2-6-
3-5
Pre-stroke
mm
3.5
3.47
3.53
Beginning of injection position
Drive side NO.1
Drive side NO.1
Difference between angles 1
Cal 1-4 deg. 60 59.75 60.25
Cal 1-4 deg. 60 59.75 60.25
Difference between angles 2
Cyl.1-2 deg. 120 119.75 120.25
Cyl.1-2 deg. 120 119.75 120.25
Difference between angles 3
Cal 1-6 deg. 180 179.75 180.25
Cal 1-6 deg. 180 179.75 180.25
Difference between angles 4
Cal 1-3 deg. 240 239.75 240.25
Cal 1-3 deg. 240 239.75 240.25
Difference between angles 5
Cal 1-5 deg. 300 299.75 300.25
Cal 1-5 deg. 300 299.75 300.25
Injection quantity adjustment
Adjusting point
-
Rack position
12.8
Pump speed
r/min
600
600
600
Average injection quantity
mm3/st.
59.5
57.5
61.5
Max. variation between cylinders
%
0
-3.5
3.5
Basic
*
Fixing the rack
*
Standard for adjustment of the maximum variation between cylinders
*
Injection quantity adjustment_02
Adjusting point
Z
Rack position
9.8+-0.5
Pump speed
r/min
265
265
265
Average injection quantity
mm3/st.
13
11.2
14.8
Max. variation between cylinders
%
0
-10
10
Fixing the rack
*
Standard for adjustment of the maximum variation between cylinders
*
Injection quantity adjustment_03
Adjusting point
A
Rack position
R1(12.8)
Pump speed
r/min
600
600
600
Average injection quantity
mm3/st.
59.5
58.5
60.5
Basic
*
Fixing the lever
*
Injection quantity adjustment_04
Adjusting point
B
Rack position
R1+1.75
Pump speed
r/min
1400
1400
1400
Average injection quantity
mm3/st.
63.5
59.5
67.5
Fixing the lever
*
Timer adjustment
Pump speed
r/min
-
Advance angle
deg.
0
0
0
Remarks
Measure speed (beginning of operation).
Measure speed (beginning of operation).
Timer adjustment_02
Pump speed
r/min
1470
Advance angle
deg.
6
5.7
6.3
Remarks
Finish
Finish
Test data Ex:
Governor adjustment
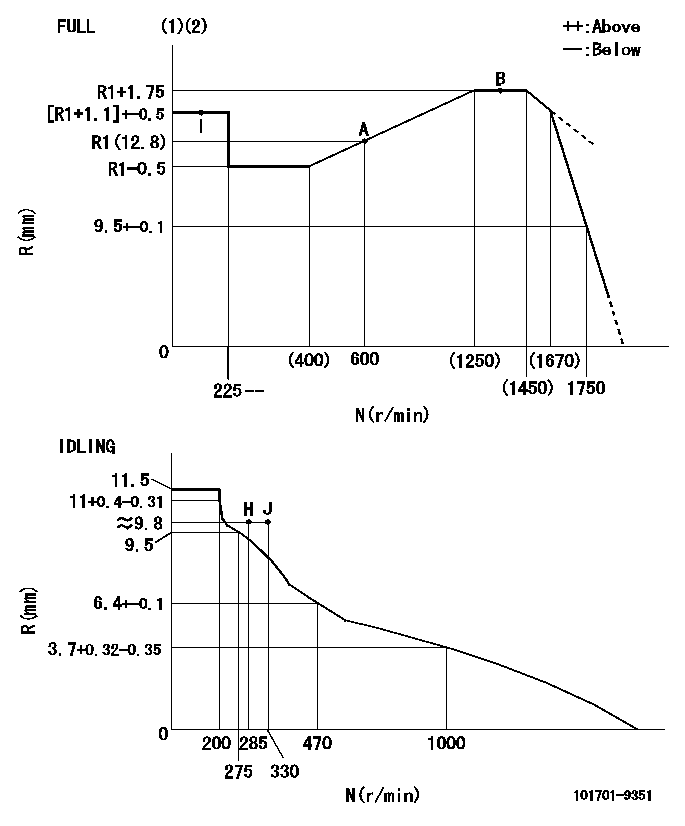
N:Pump speed
R:Rack position (mm)
(1)Torque cam stamping: T1
(2)Tolerance for racks not indicated: +-0.05mm.
----------
T1=P20
----------
----------
T1=P20
----------
Speed control lever angle

F:Full speed
I:Idle
(1)Use the hole at R = aa
(2)Stopper bolt setting
----------
aa=100mm
----------
a=22deg+-5deg b=(46.5deg)+-3deg
----------
aa=100mm
----------
a=22deg+-5deg b=(46.5deg)+-3deg
Stop lever angle

N:Pump normal
S:Stop the pump.
(1)Use the pin at R = aa
----------
aa=42mm
----------
a=25deg+-5deg b=40deg+-5deg
----------
aa=42mm
----------
a=25deg+-5deg b=40deg+-5deg
0000001501 RACK SENSOR

G:Red paint
H:Pump end face
P/N: part number of suitable shim
(1)Threaded type rack block
(2)Welded type rack block
Rack sensor adjustment
1. Threaded type rack sensor (-5*20, P type, no TICS rack limit).
(1)Screw in the bobbin (A) until it contacts the joint (B).
(2)Fix the pump lever.
(3)At speed N1 and rack position Ra, adjust the amount that the bobbin is screwed in so that the amp's output voltage is V1.
(4)Fix using the nut (F).
(5)Affix the caution plate to the upper part of the joint (B).
(6)Apply (G) at two places.
Connecting part between the joint (B) and the nut (F)
Connecting part between the end surface of the pump (H) and the joint (B)
2. Range for screw-in adjustment between the bobbin (A) and the joint (B) is 9 threads.
Screw in to the end from (the position where the bobbin (A) is rotated 9 turns).
Speed N1, rack position Ra, output voltage V1, rack sensor supply voltage 5+-0.01 (V)
----------
Ra=R1(12.8)mm N1=600r/min V1=2.6+-0.01V
----------
----------
Ra=R1(12.8)mm N1=600r/min V1=2.6+-0.01V
----------
Timing setting

(1)Pump vertical direction
(2)Coupling's key groove position at No 1 cylinder's beginning of injection
(3)-
(4)-
----------
----------
a=(20deg)
----------
----------
a=(20deg)
Information:
Disconnect all electrical power from the monitor before removing components. Failure to disconnect the power could result in severe electrical shock or damage to the monitor. An electrical shock can cause severe personal injury or death.
Choose the appropriate drive for your monitor from the table below. The 203-7811 Engine Monitoring Control Group uses Wonderware as the "Graphic Display Application". The 203-7810 Engine Monitoring Control Group uses RSView as the "Graphic Display Application".
Table 1
Drive    "Graphic Display Application"    
203-7816 Storage Drive     RSView    
204-8792 Storage Drive     Wonderware    In order to install the drive, perform the procedure that follows:
Connect the ribbon cable connector and power cables to the hard drive and the floppy disk drive.Note: Make sure that the ribbon cable is correctly installed. The connector must be positioned so that the red wire of the cable is closest to the back of the unit. If you are using the new cables, also connect the other end of the cables to the Central Processing Unit (CPU) card.
Illustration 1 g00858453
(1) Drive Bay Mounting Studs
Position the drive bay into the chassis so that the studs (1) on the chassis fit into the grommets on the drive bay.Note: Be careful not to push the vibration dampers (grommets) on the drive bay out of the sheet metal.
Install the back cover.
Apply power and verify the operation of the drive. Refer to any additional instructions that are provided with the drive.
Have questions with 101701-9351?
Group cross 101701-9351 ZEXEL
Nissan-Diesel
Nissan-Diesel
Nissan-Diesel
101701-9351
9 400 616 190
16714Z5666
INJECTION-PUMP ASSEMBLY
FE6A
FE6A